2013 Farmers Weekly Pig Farmer finalists revealed
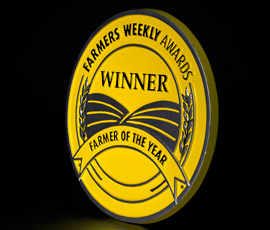
All three of this year’s Pig Farmer of the Year finalists are striving to increase output from the farm and maximise profits by investing in their units. Sarah Alderton and Caroline Stocks report
Jeremy and Jenny Brown
Vinnicombes Farm, Poltimore, Devon
A positive and focused outlook for the future of pig farming has lead Devon farmer Richard Knox to invest heavily in his farm and as a result boost output.
Despite the pig industry experiencing rocky times over the past three years, Richard has remained passionate and has increased herd size to 280 sows as well as improving performance.
The former outdoor unit on the edge of Dartmoor with 50 sows was moved fully indoors by Richard in 1996. Then in 2008 he invested heavily in the finishing accommodation, increasing pig places to 1,200.
He has since expanded further, most recently putting an additional 16 places into the farrowing room as well as erecting an 80-place gilt shed, something Richard felt was necessary for the business to be able to survive.
“Two years ago we needed to increase output from the farm to cover costs so we started farrowing extra numbers. The expansion to the farrowing shed has enabled us to farrow three more sows a week and the new gilt shed will give us further control of gilt management and allow us to bring a plentiful supply of gilts into the herd, thus enabling us to cull sows after five litters,” explains Richard.
FARM FACTS
- 105ha, owned land
- Target 150 pigs a weeks to sell with 40 smaller streamed pigs going to Cornish abattoir and the rest to Karro
- 280 sows, 1,700 finished pigs, 1,400 weaners, plus 120 ewes and 50 Simmental suckler cows
- Run by husband-and-wife team, one part-time worker plus help from eldest son, Alex
He says gilt management was once an area of weakness, but the extra gilt places now drive overall performance by allowing him to maintain a young and healthy herd.
Investment was also made last year into a new handling and loading bay, part-funded by BPEX under the Barometer Farm scheme. Now Richard measures growth rate at each stage, allowing areas of weaknesses to be addressed and rectified early.
All pigs that are not performing are streamed off and placed in newly renovated specialised accommodation. This means the other rooms can run at full capacity (110 pigs a week) with the best, fastest growing pigs. This, in turn, has given tighter weight bands within the room and allows Richard to clear finisher rooms in a tighter timeframe so the pigs have a higher, average daily liveweight gain and achieve a higher sale weight faster.
The streamed pigs are fed a higher specification diet allowing them to catch up and, by taking them out of the large groups, there is less stress, which helps growth rates and reduces mortality rates.
Richard has even sourced a dedicated market for these streamed pigs, selling them direct to a Cornish abattoir, where 40 pigs a week go at pork weight. The rest are marketed on a direct contract to Karro at Wiveliscombe, with last year’s pigs averaging 76.6kg at a P2 fat level of 10.3.
Richard’s attention to detail and monitoring at each of the stages is paying off with good production figures. An average of 11.5 pigs are weaned a litter, with growth rates of 350g a day in the nursery, 700g a day at the grower stage and 850g at the finisher stage. At all stages mortality is less than 2%.
The health of the pigs is maintained with quarterly vet visits. Richard also operates a strict biosecurity and disinfection policy and has invested in a Green-Line disinfecting and foaming system.
Always determined to try and streamline the pig operation further, Richard is now looking at renewable energy options.
Richard is confident about the future, and by attending workshops, running a Barometer Farm and hosting visits, he is always picking up ideas on how he can move the business forward.
Ian Davidson
Mosside Farm, Inverurie, Aberdeenshire
There are few people who would find a use for old chocolate factory parts on a pig farm, but Ian Davidson isn’t afraid to think differently to get the best results.
Faced with rocketing input prices and falling pig prices, he began looking for ways to cut costs and fell upon the idea of using liquid fish instead of fishmeal in his pig feed.
Taking advantage of the location of his 300-sow pig unit in Inverurie, Aberdeenshire, he started shipping in liquid fish direct from the coast, slashing his feed costs considerably.
“I get it from Shetland, it comes in a tanker and goes straight into the farm’s feed mill where it’s blended and processed,” he says.
“Because I need to get the fish to a certain temperature to process it I had to look around for the right equipment and came across this old tanker from a chocolate factory. It cost me £4,000, but I save £28,000 a year in feed costs.”
Ian took over the 180ha mixed farm from his father when he was 18, starting initially with cattle and a few pigs, but swiftly moving to add crops to the farm’s portfolio so he could produce his own feed and avoid the volatility of the grain markets.
Pig numbers steadily grew, as Ian realised he could make use of the slurry to produce average crop yields of 4t/acre.
FARM FACTS
- Mixed farm comprising of 180ha of arable land and 300 sows
- Benefits from expert consultant advice
- Nutrition tailored to maximize lean growth
“The whole business is structured as a fully integrated system,” he says. “Slurry is big on this farm and it’s important we look after it.
“By managing it on the crop we save £25,000 a year on fertiliser. When you have pigs that aren’t very profitable, it’s using the slurry on crops that makes you the profit.”
While coming up with inventive, cost-reducing ideas is Ian’s forte, he recognises the importance of having a strong team behind him to help advise and manage his operations.
As well as his pig manager, Phil Adam, who has been with the farm for 19 years, Ian employs farrowing unit supervisor Helen Cruickshank and tractorman Stewart Lee.
Eight years ago he also brought in consultant Paul Wright who helped improve pig nutrition and implement a series of enhanced sow management strategies.
“I think two heads are better than one,” Ian says. “A lot of pig farmers asked why I was taking on a consultant, but I wanted to get the feed sorted and I wanted the system to be simple.”
The simplified rearing system involves 14 servings a week through AI with the aim of weaning up to 160 pigs each week.
Weaning pigs are put in batches of 40 and to reduce stress they stay in those groups until they are sold through Scottish Pig Producers at 75kg.
“Early indications show the reduction in stress has led to a significant increase in growth rate, plus it’s decreased the workload for Phil and Helen,” Ian says.
Increases in antibiotic use made them reassess their herd type, and in 2011 they brought in Hampshire genetics to boost hybrid vigour, which has enabled them to remove antibiotic use, saving them £3.70/pig.
Growth rate has improved by about 10% by bringing in new genetics.
Nutrition has been adapted to maximise lean growth time so the pigs receive a specific diet at every stage of growth.
It has had an impressive impact, with feed conversion ratios hitting 2.75:1, making the unit in the top 5% of the UK.
Meat sold a sow has also reached 2.1t, while litter sizes have increased by 1.5 pigs a sow to 27.44 pigs a sow each year.
Ian’s next aim is to add value to the pigs through the farm’s Mossies Pork catering brand.
He is also in the final planning stages for a 225kW wind turbine, which will be used to power the pig units, and will replace older buildings with porta-units to further streamline operations.
“Pigs haven’t been profitable for a long time, so looking at efficiencies has been key to getting our prices up,” Ian says. “If we continue to make improvements and work as a team to get those improvements in place there’s no reason why we won’t be here for generations to come.”
Richard Knox
Tor Pigs, Okehampton, Devon
A positive and focused outlook for the future of pig farming has lead Devon farmer Richard Knox to invest heavily in his farm and as a result boost output.
Despite the pig industry experiencing rocky times over the past three years, Richard has remained passionate and has increased herd size to 280 sows as well as improving performance.
The former outdoor unit on the edge of Dartmoor with 50 sows was moved fully indoors by Richard in 1996. Then in 2008 he invested heavily in the finishing accommodation, increasing pig places to 1,200.
He has since expanded further, most recently putting an additional 16 places into the farrowing room as well as erecting an 80-place gilt shed, something Richard felt was necessary for the business to be able to survive.
“Two years ago we needed to increase output from the farm to cover costs so we started farrowing extra numbers. The expansion to the farrowing shed has enabled us to farrow three more sows a week and the new gilt shed will give us further control of gilt management and allow us to bring a plentiful supply of gilts into the herd, thus enabling us to cull sows after five litters,” explains Richard.
He says gilt management was once an area of weakness, but the extra gilt places now drive overall performance by allowing him to maintain a young and healthy herd.
Investment was also made last year into a new handling and loading bay, part-funded by BPEX under the Barometer Farm scheme. Now Richard measures growth rate at each stage, allowing areas of weaknesses to be addressed and rectified early.
FARM FACTS
- 280 Large White cross Landrace sows
- Target 150 pigs a weeks to sell with 40 smaller streamed pigs going to Cornish abattoir and the rest to Karro
- BPEX Barometer Farm
- Invested heavily in new finishing and gilt accommodation as well as
extra farrowing spaces
- Has experienced pig unit manager to help drive the business forward
All pigs that are not performing are streamed off and placed in newly renovated specialised accommodation. This means the other rooms can run at full capacity (110 pigs a week) with the best, fastest growing pigs. This, in turn, has given tighter weight bands within the room and allows Richard to clear finisher rooms in a tighter timeframe so the pigs have a higher, average daily liveweight gain and achieve a higher sale weight faster.
The streamed pigs are fed a higher specification diet allowing them to catch up and, by taking them out of the large groups, there is less stress, which helps growth rates and reduces mortality rates.
Richard has even sourced a dedicated market for these streamed pigs, selling them direct to a Cornish abattoir, where 40 pigs a week go at pork weight. The rest are marketed on a direct contract to Karro at Wiveliscombe, with last year’s pigs averaging 76.6kg at a P2 fat level of 10.3.
Richard’s attention to detail and monitoring at each of the stages is paying off with good production figures. An average of 11.5 pigs are weaned a litter, with growth rates of 350g a day in the nursery, 700g a day at the grower stage and 850g at the finisher stage. At all stages mortality is less than 2%.
The health of the pigs is maintained with quarterly vet visits. Richard also operates a strict biosecurity and disinfection policy and has invested in a Green-Line disinfecting and foaming system.
Always determined to try and streamline the pig operation further, Richard is now looking at renewable energy options.
Richard is confident about the future, and by attending workshops, running a Barometer Farm and hosting visits, he is always picking up ideas on how he can move the business forward.
Sponsor’s message
“This year’s finalists have all dedicated a great deal of time and money involving their businesses, showing a huge commitment to the UK pig industry”
Oliver Dale
Safety Revolution
Find out more about the 2013 Farmers Weekly Awards