Small-scale AD has a place on UK farms
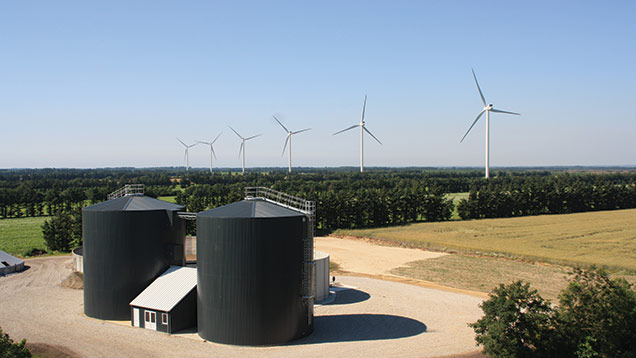
Small-scale anaerobic digestion (AD) plants can help livestock units become more efficient and self-sufficient.
The technology can provide a safe route for slurry and waste disposal, as well as generating energy and income earning potential, while the digestate by-product provides a fertiliser.
See also: Farm energy case-study- small scale AD
The small-scale AD sector is generally defined as plants of 500kW and smaller. Like the larger installations, the main challenges are finance and grid connection. Economies of scale also play a part, as generally the larger the plant, the lower the total cost of installation a kW.
However, smaller plants also offer some advantages, says Claus Jacobsen, managing director of Hallmark Power, better known to many farmers through its parent company Hallmark Tractors.
One such advantage is that smaller plants may go through the planning process under farming’s permitted development rules (PDR) – a shorter and cheaper alternative to the full planning approvals process.
The whole process – depending of the size of the system – from planning to installation should take between six and 10 months, he says.
Planning can take just a few weeks under the PDR system, or three to four months for full planning. From achieving permission, plants of this scale take four to five months to build and then 35 to 40 days to bring to full capacity.
Mr Jacobsen says that while those considering a small AD installation should take account of the important planning, finance and grid issues, it is also crucial to understand and evaluate the different types of AD technology correctly:
- Ease of operation and maintenance – thermophilic (higher temperature) digestion or mesophilic (lower temperature) – each has different space/time demands and considerations
- Skills needed – think of it as a husbandry challenge as with any other agricultural enterprise
- The experience of others using the same kit over at least 10 years
- Understand and ensure the technology and plant can support changing feedstock types:
- Annual running, maintenance and service costs – include around £20,000 for combined heat and power (CHP) unit service and one full day of time a week to run the unit
- Maintenance implications – how does regular maintenance work or a system fault affect productivity – what is the likely downtime?
Most pig farms are AD candidates as they have expanded into larger units to gain core efficiencies,” says Mr Jacobsen.
“Dairy farms generally need to be a minimum 200 to 300 cows. However, it depends on what other waste feedstock streams can be accessed or whether energy crops are grown. A co-operative approach, joining with other farmers, can also be beneficial.
“An AD system is aimed at producing max-rated power (for example 250kW) for 8,000 hours/year. Most power will be exported but a farm needing less power an hour than the rated power will effectively be self-sufficient. However, even if the AD system does not offset all of the needed power, it will offer an alternative income stream.”
As slurry storage regulations tightens, AD can be incorporated into a farm’s slurry management regime, says Mr Jacobsen.
“Because it’s an enclosed unit, it eliminates odour and therefore there are no restrictions on where it has to be placed. Most farms with open lagoons will be forced to cover them up through new regulations and this can be negated through an AD plant.”
Hallmark Power’s AD plants include 100kW, 250kW and 500kW models, with overall costs from £600,000 to £1.6m, plus grid costs. These are supplied by Danish company CombiGaS, which was itself founded by a pig farmer.
While these can operate at larger scales, the three sizes are designed to be self-sufficient on larger pig and dairy farms, fed exclusively by the slurry and other waste produced. The more consistent the feedstock, the better, says Mr Jacobsen.
These units are supported by Danish government export credit finance, making finance more easily available to UK farmers than for some other AD units, says Mr Jacobsen. “As long as the farmers can demonstrate two to three years of healthy accounts, they will be considered for this finance,” says Mr Jacobsen. This currrently offers 85% loans at 3.5% over five to seven years. The loans are secured not by the farmer, but by the Danish Government.
How does AD work?
AD converts plant and animal material (feedstock) into useful products through the action of micro-organisms in the absence of oxygen. Biomass can include a mixture of slurry, animal feed and energy crops. These are put in sealed tanks where the micro-organisms digest them, releasing methane (biogas) that can be used to provide renewable energy.
Primary elements of an installation are an in-feed system, primary and/or secondary digester tanks, gas storage (often built into the tanks), a combined heat and power (CHP) unit and a control building.
Energy generated earns Feed-in Tariffs (Fits), energy exported to the grid also earns a Fits export tariff, while AD can also earn Renewable Heat Incentive (RHI) payments.