Slurry holds the key to a green future
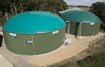
If you were looking for proof of the massive changes that farming businesses large and small are undergoing, then Bedfordia Farms’ new biogas project is a telling example.
This family-owned farming business, with 2200ha (5400 acres) of land, 1800ha (4500 acres) of arable crops, 1100 sows and a grain storage facility based at Milton Ernest near Bedford, is no stranger to diversification. It is part of a group that already has interests in the automotive and property sectors.
But from this spring it has had a new sideline – electricity production. Instead of being spread on to the land, slurry from the farm’s pigs races along a 250m underground pipe to a sparkling new biogas plant.
It’s by no means the first biogas plant on a farm in the UK, says managing director Andrew Needham. There are seven small on-farm plants in south-west Scotland and a new, bigger one coming on-stream in Aberdeenshire, plus a large off-farm centralised anaerobic digestion unit in Devon and a demo plant at Ludlow.
But what’s interesting about the Bedfordia plant is that it was conceived at the same time as the farm’s pig finishing unit, which was built on a greenfield site. So the two have been designed to dovetail together in a way that hasn’t been done elsewhere in the UK.
For the design and equipment, Andrew Needham and his team had to turn to Germany, a country that is home to an astonishing 3000 on-farm biogas plants and is Europe’s leader in turning farm wastes into electricity. The project went to planning in April 2003, but building didn’t start until April 2005 and the plant became operational in March 2006.
It’s been a protracted process, admits Mr Needham. Although biogas technology has been around in Germany for six or seven years, it has still had to be adapted to UK conditions, not to mention rules and regulations. Plus Bedfordia carried out lots of feasibility studies and made numerous on-the-go design changes to get this state-of-the-art plant exactly right.
The plant will also be licensed to process animal by-product, so bio-security had to be taken very seriously.
The multi-million-pound plant is now taking in 200cu m of pig slurry and 100t of food chain waste each week, but weekly capacity will rise to 575t. Slurry from the pigs forms the basis of the intake and is essential for achieving the porridge-like consistency ideal for the anaerobic digestion that produces the methane. But it’s the food waste, with its higher energy content, that really generates good amounts of methane.
In fact the food waste is an essential part of the economics of the project too. Some 30m tonnes of the stuff is produced in the UK every year, a third of it from the food that we all chuck into the dustbin, a third from out-of-date food discarded by supermarkets and a third from food manufacturers.
Tipped into holes Bedfordia Biogass- 01234 827 207 or andrew.needham@bedfordia.co.uk
All that used to be tipped into holes in the ground, but with landfill tax now at £21/t (and rising) the food industry is looking for cheaper and more eco-friendly ways of disposing of it. And the gate fees received by plants like the Milton Ernest one are an essential plank of their income.
The other plank, of course, is selling the electricity produced from all the methane that bubbles up from the fermenting slurry and food waste (see box for quick guide to the process). The Milton Ernest plant is expected to produce between 0.75 and 1MW a year, enough to power 600-800 houses.
In fact, says Mr Needham, biogas plants score very highly on several green fronts.
- They extract electricity and heat from two types of waste product that you wouldn’t normally think of as a power source, so that means less use of fossil fuels. In Germany and Sweden they also use the methane to directly power cars, buses and even trains.
- They cut the amount of food waste going into increasingly-scarce landfill.
- The process is carbon-neutral.
- Since landfilled food produces a lot of methane (22 times more damaging to the atmosphere than carbon dioxide), they cut greenhouse gas production.
- Slurry (121m tonnes of which is reckoned to be produced on UK farms each year) also produces methane so that’s reduced too.
- The slurry comes in by pipe so there are no tankers trundling around the roads. It provides a local solution for local waste. All of which saves fuel.
- The bio-fertiliser left at the end of the process helps conserve increasingly scarce fossil fertiliser sources and cuts the energy use in producing and transporting artificial fertiliser to UK farms.
Is smell an issue? Well, you don’t ferment pig slurry and food without producing a bit of a pong, but while there’s a distinct whiff inside the reception building, all the exiting air passes though a biofilter system, so the smell outside is no more than you’d get on any stock farm.
In Germany some of these plants are even sited on industrial estates, presumably without complaint from neighbouring businesses.
Sounds like a blueprint for a green future? Andrew Needham certainly thinks so. In fact, with the first plant up and running, Bedfordia sees a lot of potential for other such plants on UK farms. It wants other farmers to get involved on a joint venture basis and aims to have 10 biogas plants in five years’ time.
And it’s the expertise gained from building the Milton Ernest plant, says Andrew Needham, that gives Bedfordia the confidence to want to expand like this. “Our biggest selling point is that we’ve been there, done it and have an experienced team of people in place.”
HERE’S HOW THE JOINT VENTURE WOULD WORK: |
Bedfordia would:
The farmer would:
And would need to:
Every plant will need 18 months/two years to get up and runnning |