Practical advice on health and safety: farm policy and finance
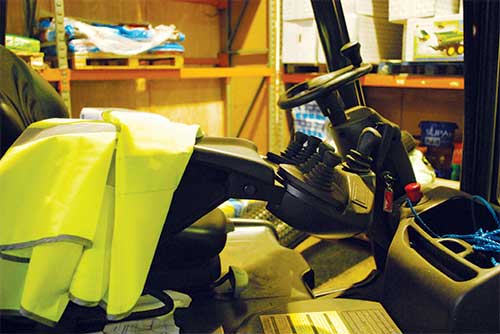
Investing in health and safety and in motivating staff is a key requirement for any progressive and professional farming business. Farmers Weekly discovers how a range of benefits and returns can come from that investment.
Fewer accidents, fewer claims, lower insurance costs and better staff motivation are just some of the consequences of introducing a health and safety culture to one farming business (see case study one).
Record-keeping and investment are also crucial areas to address in farm health and safety (see case study two).
The benefits of a proactive health and safety policy are:
- Fewer accidents
- Better staff motivation
- Fewer insurance claims
- Lower insurance costs
- Less down time – more efficient working
Robert Barnes of L E Barnes & Sons farms about 2,024ha (5,000 acres) in Bedfordshire and runs a contracting business alongside grain storage and haulage operations.
Nine years ago Mr Barnes set out to instil a safety culture in his team, raising awareness of risk and encouraging consistent good practice to reduce the likelihood of accidents. He was concerned about welfare following a couple of serious incidents on the farm, including injury caused by machinery and near-misses such as a runaway tractor.
The results have been dramatic, he says. Over that period the number of accidents and claims has dropped and insurance premiums on a like-for-like basis have followed them down.
Financial savings
The accident book now proves the progress, says Mr Barnes, with no accidents recorded and no claims have been made.
“In cash terms I’m saving about £5,000 a year on employer’s and public liability insurance,” he says. “Over the past five years our workforce has more than doubled from six to 16, while our employer’s liability insurance premium has only increased by 60%.
“More importantly, my claims history is improving dramatically – I’m investing in avoiding a situation where premiums rise because of an expectation of future claims.”
The way claims inflation has risen means that the costs of incidents on farm today is likely to be triple the figure of 10 years ago, says Douglas Brown of Arable Insurance Brokers.
Consultancy process and costs
Mr Barnes brought consultant Safety Revolution in to advise on how to manage the change in culture. Being in regular contact with Mr Barnes and, just as importantly, with his team are key, says managing director Oliver Dale.
Visits to the business are made two or three times a year and during these visits staff are encouraged to provide the ideas and raw material for developing health and safety systems. The typical annual cost for this type of service is £1,800 a year.
Benefit of involving staff
Staff are now fully engaged in the process, with quarterly staff health and safety meetings co-ordinated by Safety Revolution. Issues raised recently by staff included reducing speed in the yard, providing a mirror on the blind corner of the red diesel tank and poor lighting in some of the grain stores. Action has now been taken on all of these points.
“Issues such as personal protective clothing and training needs are often raised,” says Mr Dale. “Also, staff will often raise a concern with us that they won’t raise with the employer, or they may have a question that they want answered. We can do that without them feeling uncomfortable.
Looking ahead
“Issues are often seasonal – we try to flag common problems that might be encountered in the next quarter, for example long hours going into harvest or dust in dryers, an issue which is often overlooked.”
Mr Barnes sums up the way staff have engaged with the process as moving from a ‘what do we need to know that for?’ to a more enthusiastic ‘this is something we need to know about’ attitude.
“In order for a proactive approach to health and safety to deliver value, particularly when an accident occurs, it’s absolutely vital that the key components are in place,” says Mr Dale.
Risk assessments
“That means regular review of the health and safety policy and risk assessments and keeping these short, simple and to the point. There doesn’t have to be masses of paper but what is there must be really good and based on exactly what is happening on the ground.
“For example, taking an issue raised at a staff meeting and dealing with it through a combination of agreeing training, changes to equipment such as buying a wheel changer and writing a risk assessment.
“I don’t say ‘let’s write a risk assessment’ I say ‘what could go wrong, what could hurt you?’ The staff then talk it through. I ask what they’re doing about it and what more they could do.
“We agree, say, two or three things and I say ‘you’ve just done a risk assessment’. They feel two things; first a risk assessment is not difficult and second it delivers a practical benefit. I make sure that what’s agreed gets done and that builds trust and credibility.
“If we get done what they feel is important they usually help us. It’s like building any relationship, it takes time and consistent application. The adviser has to know the business and the team well and the documents will reflect that.
Lower insurance costs
“I should be able to walk on to the farm and the guys recognise me and feel comfortable to chat to me.”
Mr Barnes sees Safety Revolution as part of the team. “This for me is a business decision. We need to see a return in excess of what we spend and we’ve achieved that. Our insurance costs have effectively dropped by 40% as a result of what we’ve achieved, we’ve saved money and that’s been achieved at the same time as keeping people safe.
“The costs of getting it wrong are rocketing; the costs of claims on a like-for-like basis have increased dramatically based on my broker’s estimates. We want to keep claims down as part of containing costs, but we also want our team fit and in the field where we need them on kit that is in good condition and not in the workshop being repaired.”
Former Farmers Weekly arable farmer of the year Colin McGregor farms more than 3,000ha in the Scottish Borders on different soils and across a range of family-owned, rented and contract-farmed land.
Investment
“We’ve been working steadily on improving safety across our business and for our farming clients,” says Mr McGregor. “It’s an investment that we’ve made as part of running a professional business and on behalf of our clients.
“We recently invested in a new chemical store and sprayer-filling area that provides a safer working environment for our staff and reduces the risk of contaminating local water courses.
“On both counts I feel that we are reducing the likelihood we will have an incident that could cost us millions – whether that’s related to an injury or to environmental damage. The return is not always immediately apparent but I’m confident it’s very substantial.”
Record-keeping
The key to good health and safety working is the quality of relationships, of the documentation produced and the practical application of policies on farm. “If you are tested by an incident, it’s no good having a shiny file on the shelf full of generic paperwork,” says Mr Dale.
“Your documents, which form your body of evidence and which will be closely scrutinised by HSE, should be regularly used, annotated and obviously be a living, used, set of guidance.
“Getting into the detail is critical, and showing over a sustained period that you really do invest not just money but time and thought too is the key to success. If it’s done well then it is perfectly possible to prove you have done as much as you could and that you have adequately discharged your duty of care, avoiding enforcement action and the costs that arise from it.
The most common failing by farm businesses is where an audit is carried out and recommendations are given with the documents often stating that certain procedures are being followed, but in fact they are not, says Mr Dale.
“This leaves them exposed. Farmers often comment that staff have not been involved or don’t understand something. This is key, the farmer has to be able to prove that information and instruction have been provided.
“Often there is no record. There has to be evidence that staff have read and signed documents. Often you’ll find that risk assessments are generic; they talk about general risks associated with that type of unit, they are not specific to the farm and therefore weaker.
“They must be gone through line by line and modified to that business so that the farmer can say hand on heart that he understands them.
“In a nutshell, the process is a quality, in-depth audit, an action plan based on that business, time spent ensuring everyone understands it and that it’s communicated effectively, and then regular, friendly and informal monitoring to help get it done.
“The result is that health and safety is no longer a scary subject. Most of our clients are driven by a desire to protect staff, to have a strong, healthy team and to show care for their welfare and then to gain cost savings by so doing.”
10 top health and safety tips
- Promote a safety culture
- Encourage staff to be risk aware
- Involve staff in planning and executing health and safety policy
- Hold regular safety meetings and encourage contributions
- Tailor health and safety to your business – do not use generic documents
- Actions and practice must demonstrate that policy is being followed
- Third-party advice can help staff to be open about issues they may not wish to raise directly with the employer
- Documents and risk assessments should be regularly reviewed – risks change seasonally
- Make sure any recommendations or changes are followed up immediately
- Take account of developments in the business and their impact on health and safety