Moy Park raises welfare standards of conventional chicken
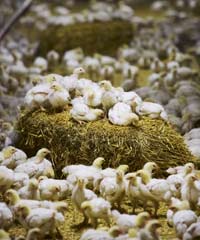
Moy Park is raising the welfare standards for its conventional chicken, as Richard Allison found out on a recent visit
Moy Park has invested £50m in British chicken production over the past three years and bird welfare is at the heart of its vision at its Anwick plant, Lincolnshire.
Back in 2004, Moy Park acquired Padleys including the processing plant at Anwick. And since then, the company has spent £30m at the plant, making it one of the largest investments in food manufacturing in Europe.
So why is the company investing so heavily in the British poultry sector? The reason is that it believes in the British fresh chicken industry and sees a great future.
Commercial director Seamus Rooney said at a recent press visit: “I want this industry to thrive as well as those who work for us, those who consume our food and the birds themselves.”
The company has a long history of innovation being a pioneer of windows in poultry sheds and was one of the first to rear free-range and organic chickens. In fact, it helped draw up the EU organic standards when the organic sector was in its infancy.
But now the company has set its sights on standard chicken, which accounts for about 80% of its production.
General manager Andy Ballantyne started by highlighting that “there is nothing wrong with Assured Chicken Production, it is a very welfare friendly chicken.”
However, the company is not intent with standing still and has a vision of moving the British industry forward.
“I’ve been in developing chicken production for some 26 years, and we still continue to search for more opportunities to enhance and improve our growing systems. There will be lots of research carried out and many prototypes tested,” he said.
As part of this vision, Moy Park has invested £30m in its poultry units supplying the Anwick plant through a combination of converting existing sites by fitting windows as well as embarking on a programme of new builds.
Mr Rooney explained: “In 2008 alone, we invested £750,000 converting existing poultry sheds by retro fitting windows.
“In addition, we are currently building a new site consisting of five sheds, each housing 30,000 birds. It is a significant investment as new builds are now costing between £18 and £20/sq ft; this depending on certain planning constraints, but also includes on site dwellings.”
But it is not just on its farms, welfare was also a key focus during its recent redevelopment of the Anwick processing plant. This has resulted in a doubling in the area to 25,000sq m with the addition of a new packing hall complete with the latest in robotics on the packing lines.
The plant employs 11,000 workers and operates six days a week for 17 hours a day processing 1.4m birds a week.
As soon as birds arrive, blue lighting coupled with a novel hydraulic jack system for removing modules from the lorries ensures birds are calm. “The hydraulic jack system eliminates the need for forklift trucks roaring around making noise and bouncing birds about,” said general site manager Philip Biddle.
Coupled with a specially designed ventilation system in the lairage area, it is a more pleasant environment for both birds and workers, he added.
Other welfare measures highlighted during the visit include the very short length of time from birds being shackled to being stunned. And at this stage, birds brush against a white plastic board as they move along, specifically designed to calm birds.
“Stroking birds has a calming effect and this plastic board mimics that,” he said.
One development that Moy Park is particularly proud of is its maturation process, which the company jointly developed with Queens University, Belfast. This patented system means it only takes about 3.5 hours for each bird to go through the plant from arrival to being packaged and ready to go to one of Moy Park’s customers.
It involves passing a small current through birds after they have been killed to stimulate birds. This reduces the pH of the meat, therefore tenderising it.
“In the past, it took 8-10 hours for birds to mature, which meant we had to remove birds from the line, store them in crates and then re-hang them once matured on the line for cutting and portioning. Now it is a more efficient process, said Mr Biddle.
Case study: Terry and Judith Saunby, Poolham Farm
Poolham Farm was originally built by Brandons for rearing turkeys, but it is now home to 300,000 broilers in 10 buildings.
Terry and Judith now manage a farm that has been completely renovated. In particular the houses have been converted to Moy Parks unique windowed system with windows running the length of both sides of the house.
Windows are double-glazed and the glass has been treated on the outside to reflect heat, says Moy Park general manager Andy Ballantyne. “We also tested them [windows] for light transmission and we found that 85% of the lux level outside is realised inside.”
Buildings are designed to make full use of light with a photosensitive cell in the shed maintaining consistent lighting levels by switching lights on and off. “If levels fall to 20 lux or less, the lights then come on,” said Mr Ballantyne.
The area of windows equates to about 5% of the floor area, which is well above the minimum standard of 3% set by Freedom Food for its own indoor system.
Window shutters are first opened seven days after chicks arrive and the natural light floods in.
“On this unit, we leave window shutters open at night, depending on lighting programme. However, on another unit which is near a main road, we have to close shutters along one side as the car lights were upsetting birds,” he says.
Straw bales, one under every light which works out at more than one per 1000 birds, are used on this site, says Mr Ballantyne.
Training
A key part to Moy Park’s focus on bird welfare is its highly trained farm managers, who undergo rigorous training and development throughout their career.
Recruiting farm managers is an increasing challenge across the industry as fewer school leavers choose poultry farming as a career. However, as commercial director Seamus Rooney said, this has not been a problem for Moy Park.
Back in 1984, the company developed its training academies, which are effectively modified poultry units.
“We take in raw recruits and they are then allocated to one of our special training sites. Instead of having the standard one bungalow for the manager, these sites have an extra bungalow to house the trainee,” he explained.
After a year, they can be promoted to look after their own site as they progress. Currently, the firm has eight breeder academy sites , five rearing sites and 10 broiler sites.
The result of this is that the academy has produced a continual supply of high quality managers without having to recruit staff from other poultry companies, said Mr Ballantyne.