Excessive vet checks and paperwork hit meat exports to EU
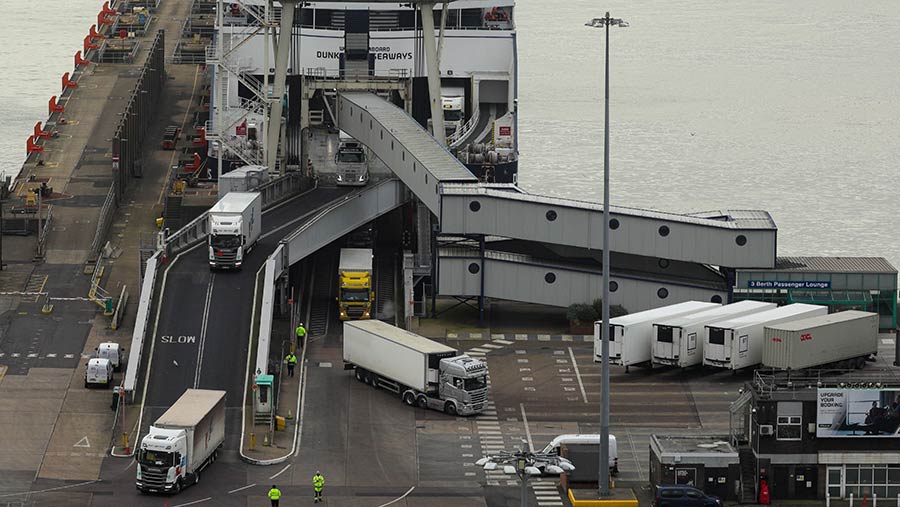
Excessive stock checks and stringent paperwork requirements are causing huge costs and disastrous delays for UK meat exporters.
The Food Standards Agency has been criticised by one lamb export business for its approach to supplying vets to carry out the necessary animal health and certification checks (see “Vet availability, costs and delays causing headache for lamb exports”).
Meanwhile, the National Pig Association (NPA) has blamed EU officials for their role at UK ports.
See also: Lamb prices likely to stay high amid tight supply
It said delays caused by excessive checks and paperwork were making UK shipments unattractive to buyers in the EU, forcing processors to reject shipments and cancel future orders.
One load was held at Calais for 20 hours while inspectors carried out checks. The pigmeat was then rejected on finally reaching its destination in Germany because its quality had deteriorated.
The NPA warned that the full overall impact of the new rules is yet to be felt, as UK export volumes remain lower than normal for the time of year.
Processors have reported a number of issues, including:
- Officials at ports in the UK, France, Ireland and the Netherlands taking an excessively stringent approach to assessing paperwork.
- Additional bureaucracy is causing major delays for processors – one took nine hours to prepare paperwork for a single shipment to the EU last week.
- Paperwork for a 15t shipment bound for the Netherlands required 12 stamps in three languages, in duplicate, or 72 stamps in all.
- Brexit rules require inspectors to check labels on each box in a consignment of pork products, meaning the whole pallet has to be offloaded and broken apart.
- Eurotunnel needs to process 500 lorries an hour but has the veterinary capacity for only 150 an hour, causing further delays.
- The administrative burden of health certificates means that vets are struggling to meet the demand.
Bureaucracy overload
“We are seeing a bureaucracy overload and it is already having a big impact on the pig sector,” NPA chief executive Zoe Davies said.
“This is partly an inevitable consequence of Brexit – we always knew it would mean more red tape, checks and delays. But there is a political element, too.”
Dr Davies said about 30% of all UK consignments to the EU were being checked. This was far more than for many other third country exporters to the EU – for New Zealand, for example, the figure was 1%.
“It is clear that the EU Commission wishes to make Brexit as painful and as messy as possible to prevent any other country from following suit, so we have very little hope of improving things,” she said.
While UK products heading to the EU are subject to additional checks, the same rules for products coming the other way won’t be applied for some time, as the UK is phasing in its checks.
Dr Davies called on the government to act.
“The government does not appear to think there is a problem,” she said. “The clear message we are receiving from our processors is that there is.
“We want to see some concerted action and political will to speed the processes up on both sides, with greater priority given to perishable products, such as pork.”
Dr Davies added: “While this delay is convenient for a government that wants to ensure there are no empty shelves in supermarkets, UK producers are being placed at a huge disadvantage and we have absolutely no leverage to convince the EU to change their position.”
Vet availability, costs and delays causing headache for lamb exports
Rizvan Khalid, managing director of exporter Euro Quality Lambs, said increased paperwork and veterinary checks on both sides of the border had resulted in higher costs and significant delays for many businesses.
“What was taking 15 minutes once the load was complete is now taking three hours, and the same checks at the Calais border have taken a further six hours before the product can go on to the customer,” he said.
“We’re still refining our processes and don’t yet know what the new normal will look like, but we are having to build in independent checks at every stage because one wrong digit on the paperwork can result in the load being rejected or delayed.”
An export vet has to check the load and complete an export health certificate for every customer in the load.
The biggest problem was that the Food Standards Agency, which has vets on-site, was not helping provide this service, Mr Khalid said.
“The vet we are using is travelling an hour and a half every day and there’s a cost involved with that, and issues with regard to the availability of vets,” he said.
“I’m flabbergasted the FSA aren’t doing more to help businesses. This seems to be a top-down approach because the vets are happy to do it and are on site anyway, but they are saying commercial businesses have to source their own vets. Personally, I don’t think that’s good enough.”
Another difficulty is a new customs requirement to send an invoice with the load in advance, meaning any weight changes over time cannot be taken into account.
Although Mr Khalid’s business has not had any loads rejected during the new process, he knows of several that have, and others that have faced two-day delays caused by problems with paperwork.
“Once you have narrowed down what you need to know for your specific business and gone through the process a few times it’s not as complex, though that will be more difficult for people who export less frequently,” he said.
“Also the costs and issues will be the same if you’re sending one or two pallets or sending a full load because the vet still needs to come.”
FSA response
An FSA spokesman said: “The FSA’s primary role in abattoirs is to verify food safety standards.
“We carry out food safety audits and inspections of all carcases as part of Official Controls. These are mandatory for businesses and the application of a health mark signifies the meat has passed inspection.
“The export of meat is a commercial business decision which requires additional documentation and is a service offered by commercial providers. However, we are working with industry to provide support for this where we have capacity and it will not impact on the delivery of our food safety work.”