How to make the most of wool in a depressed market
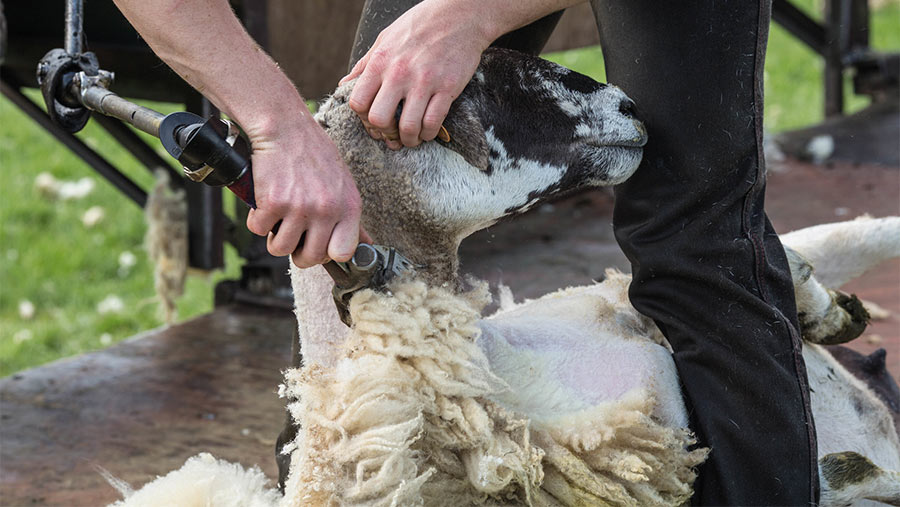
The wool market has taken a dramatic downturn since 2014, with the continued growth of synthetic fibres, supply chain consolidation, US tariffs on Chinese products and Covid-19 all having an effect.
This year, the pandemic has resulted in British Wool almost halving the price paid for the 2019 clip to 32p/kg, with no advance payments being made against the 2020 clip.
This means the price will not go near covering the cost of shearing in most cases. Therefore, getting the most value from wool may require tapping into new markets and buyers.
See also: More on alternative and new markets and uses for wool
1. British Wool
Farmers can maximise their returns through the traditional route by ensuring each fleece is presented correctly and is as clean as possible.
There are penalties for incorrectly rolled fleeces, and any unrolled wool is valued as “broken wool” and earns a much lower rate.
Maximising returns from the British Wool
- Remove all claggs and daggings – there is a price penalty for claggy and undocked fleeces.
- Pack different breeds and types of wool into separately labelled sheets.
- Pack oddments separately.
- Don’t mix hill wool with lowland wool. Kemp wool (brittle, weak fibres, residual traces of secondary coat in some species) from hill breeds can cause cross-fibre contamination and spoil lowland fleeces.
- Keep coloured and white wool separate. Mixing them can also cause cross-fibre contamination.
- Don’t mix hogg wool with wool from ewes and wethers.
- Don’t mix oddments with fleece wool.
Source: British Wool
2. Independent merchants
Laurence Pierce is one of the largest independent buyers of wool in the UK, purchasing about 15% its requirements direct from producers. It is owned by Curtis Wool Direct, which in turn buys 50% of its wool supply from British Wool auctions.
Direct purchases from farmers across the UK are paid for at an average price of 15p/kg for main white wool and 5p/kg for lesser wool, such as Swaledale.
Farmers are not required to roll the wool, but it must be presented clean and dry, with colours bagged separately. There is no discount for overly marked fleeces and farmers selling wool to the company are paid within 24 hours of delivery to the depot.
John Wood of Laurence Pierce says: “We offer a different avenue for farmers to sell their wool, and pay within 24 hours, which can help farmers pay shearing costs.
“We are offering a price that is realistic to the market at the moment.”
Other examples of independent wool merchants buying direct include Texacloth and DB Wool.
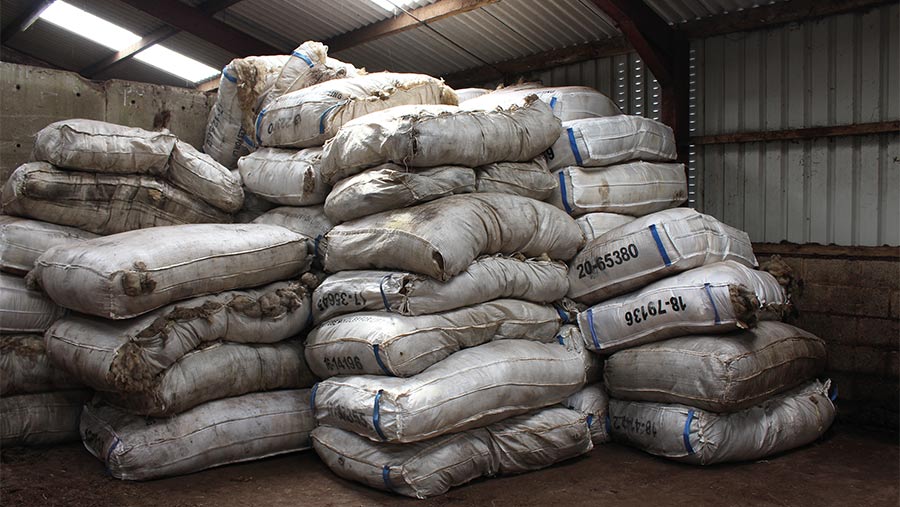
This stored wool is destined for composting through Dalesfoot Composts © Sarah Alderton
3. Storing the wool until next year
This option depends on having adequate storage and being willing to accept further price risk.
Storing the wool could mean a better price in 2021, but if this is something too many consider, there could be an oversupply next year, creating price pressure.
Wool should be stored off the ground, ideally on wooden pallets and in a dry shed.
Wool market factors
The market has been in decline since 2014, mainly due to:
- Substitution of cross-bred wool by oil-based synthetic fibres which have become cheaper.
- US tariffs on Chinese origin imports of wool products.
- Covid-19. February to May is normally the busiest wool-selling period. Last year, British Wool sold 44% of the annual clip during this time. However, the pandemic shut the cross-bred wool market in March, and it remains closed. As a result, British Wool has 7m kilograms of unsold stock from a total 27m kilograms from last year.
- Half of the 27m kilograms taken by British Wool annually remains in the UK, with most being made into carpets (50%), clothing (42%) and bedding (6%), as well as other uses (2%). Prices have dropped significantly because the carpet industry has pretty much been shut during this period, with shops closed and no need for contract carpets (for example, hotels and cruise ships).
- The decline in wool prices is a global trend, and British wool has been making better prices than New Zealand wool for the past two years.
4. Processing wool yourself
There is nothing to stop producers adding value to wool by having it processed into a range of materials for onward sale. There are several mills that deal directly with farmers.
For example, the Natural Fibre Company will take any fleece, with a minimum of 10kg required for scouring and carding (washing and combing). To produce a finished yarn, a minimum of 20kg is required.
It costs £45-£65/kg for undyed knitting yarn, including VAT and carriage. So, a minimum order of 20kg, yielding on average 12-15kg finished yarn, is likely to cost £500-£1,000 to process.
There is currently a seven-month waiting list with the Natural Fibre Company, with no intakes of Herdwick or organic fleeces until 2021, as these are only processed once a year. Sheep cannot have been dipped or treated with a pour-on within four months before shearing.
Sheep producers Maria Benjamin and John Atkinson, Nibthwaite Grange Farm, Cumbria, process and market about 20% of their wool themselves, with the rest sold to British Wool.
Last year, Ms Benjamin sold 200kg (150kg of their own wool and 50kg from local producers) to a buyer in Japan for spinning and handcrafting. She is paid between £6-£15/kg for the raw fleece, depending on the quality and rarity of the breed.
If she does not have the specific wool the Japanese buyers are looking for, she sources it from farming friends. These farmers receive the same price a kilogram as Ms Benjamin, and she receives an extra £1/kg handling charge for sourcing the fleece.
They are also paying about £45/kg to get their wool processed into spinning wool, which they then sell for £100-£180/kg. Ms Benjamin says: “After the costs of transport, packaging and labelling, you can still make a good markup if you sell it direct.
“The processing costs are high, but if you can invest the money, it can be worth it. Last year our turnover from wool was £20,000. It is also more stable, as you are taking charge of the market yourself.”
Disposing of wool
Disposal is a further option. While burning wool openly is illegal, it can be incinerated, or rendered followed by incineration.
Anaerobic digestion is a very unlikely option without any pre-treatment, as wool can take months or even years to degrade.
Legitimate disposal options include:
- Composting on farm with no need for Animal and Plant Health Agency (Apha) approval or registration
- Send it to a separate and registered wool-composting site
- Use any disposal method for category 3 animal by-products. Examples include:
a. Incineration or co-incineration in an approved plant
b. Landfill after fleeces have been processed
c. Processing fleeces and using them to make organic fertilisers and soil improvers
d. Sale for composting
e. Applying wool to land as a fertiliser, in some cases
The legality of disposal method can be checked with your local Apha office.
5. Local buyers
There is a host of smaller manufacturing companies buying fleeces direct, among them a growing number of wool duvet makers. For example, Baavet Duvets in Wales buys Texel and Lleyn fleeces from eight to 10 farmers a year and is using about 20t of wool for duvets.
It pays farmers about twice the current market price – based on British Wool prices – and has kept its rate consistent for 10 years. Baavet sells about 7,000 duvets a year through its online shop and at shows.
6. Composting wool
A hill farm in Cumbria, which has diversified into making compost from bracken and wool, is looking to purchase about 100t of wool from farmers across the country. Dalesfoot Composts is looking specifically for farmers that can supply them with both bracken and hill breed wool.
Farmers will be paid 40p/kg for their wool, with wool already being received from as far away as Dartmoor. For the bracken, farmers can expect about £22 a round bale.