Make energy go further on arable farms
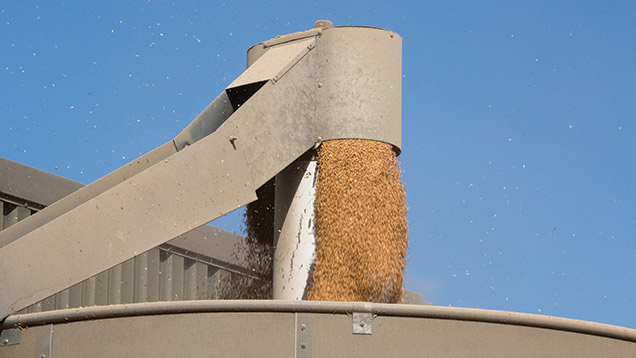
From farm assurance standards to end-user grower protocols, there is increasing pressure on arable farmers to improve energy efficiency.
While these may feel like regulatory hoops, there are considerable financial savings from energy efficiency, says Andrew Kneeshaw of the Farm Energy Centre.
“Energy efficiency has always been a harder sell than renewable technology, but the returns can be just as good, with many projects paying back in two to five years. The difficulty is that energy efficiency is harder to measure and requires accurate monitoring and recording.”
Keeping a record of fuel use over time allows growers to clearly identify where most fuel is used and see how consumption can be cut by doing things more efficiently, he says.
See also: Farmers should put energy saving ahead of energy generationÂ
Electricity use on most combinable crop farms is generally fairly minimal, so the greatest scope for saving energy (disregarding “embedded” energy in fertiliser) lies in the fuel needed during crop drying, storage and for field cultivations.
Energy use in each operation varies wildly depending on the business, says Mr Kneeshaw. “If you’re not drying anything, 90% of energy use might be in the field, whereas if you are drying grain it may be closer to a 50:50 split.”
Grain drying
ADAS figures published by the Farm Carbon Toolkit show conventional, high-temperature dryers require 55 litres of oil/ha of crop dried, yet simple measures such as ensuring all controls (especially humidity) are set correctly can cut energy use by a quarter.
It also outlines a number of other tips:
- Cooling crops rather than drying could save 10% energy costs
- Ensure equipment is well maintained, ventilation fans are the appropriate size and moisture measurements are accurate
- Adding recirculation to existing cross-flow driers can save up to 30% of energy usage
- Ensure the dryer is operating at the right capacity and avoid a second pass through
- Vary harvesting to reduce drying time needed.
There have been big advances in grain drying technology over recent years and energy efficiency is a key driver, says Chris Budd, commercial manager at Alvan Blanch.
He estimates the average thermal power needed to dry grain from 20% to 15% is approximately 60kW/wet tonne of grain processed each hour. For example, 20t/ hour will require approximately 1,200kW.
This needs around six litres of diesel for every tonne of grain, which at a red diesel price of 70p/litre, costs around ÂŁ4.20/wet tonne processed, he says.
Modern driers include features such as precise control of grain flow and temperature, insulated walls to retain heat, air recycling and efficient burner technology, he notes.
Cultivating energy gains
In terms of cultivations, the biggest single step for reducing energy use is to switch to a minimum or no-tillage system to reduce the amount of soil moved.
This will not suit every farm and there are sound agronomic reasons for sticking with more fuel-intensive systems. Nevertheless, there are still some key steps to consider, says Mr Kneeshaw.
Match gear and engine speed
Operate tractor engines at the lowest speed for the power requirement, but do not overload the engine. One European Efficient 20 study found reducing engine speed from 1,800-2,200rpm to 1,600-1,000rpm gave the following fuel savings:
- Cultivator – 7%
- Disc harrow – 12.5%
- Fertiliser spreading – 25.9%
- Plough – 6.4%
- Roller – 16.9%
- Drilling – 15.8%
- Transport – 17.6%
Multi-implement farming
Using equipment that allows multiple jobs to be done with each pass, such as ploughing and harrowing or seedbed preparation and drilling, can cut energy use by 25-40%. It may require compromises in set-up and speed, but generally saves time and fuel.
Scale down tractor size
Using smaller engine tractors where possible can save up to 50% of fuel, depending on the job. Also consider more efficient models when buying, or use a machinery ring/contractor instead of buying a bigger tractor.
Maintain machines
Key tasks include:
- Tyre pressures – take into account: implement, ballast, task and ground conditions
- Keep fluids and filters clean (air, oil, and fuel)
- Keep cooling coils clean and unblocked to avoid engine overheating and losing efficiency
- Lubricate engine and gears to reduce friction losses
- Tune the engine to optimise fuel-air-mixture
- Lubricate joints and linkages
- Sharpen blades on items like balers – 10% power losses have been found on balers with blunt blades.
Optimise tyre pressures
Tyre pressure is a balance between wheel slip and rolling resistance. Follow manufacturer guidelines on optimum tyre pressures for different tasks/ conditions. As a general example, 20% over or under inflation of tyres can lead to a 25% performance loss.
Efficient 20 ploughing trials in Shropshire showed a 5% saving by dropping pressures from 23psi all round to 14/17 psi (front/rear). Larger tyres with a wider footprint gave a 30% fuel decrease, saving 3.5 litres diesel/ha.