How farm-scale AD can offer sustainability and savings
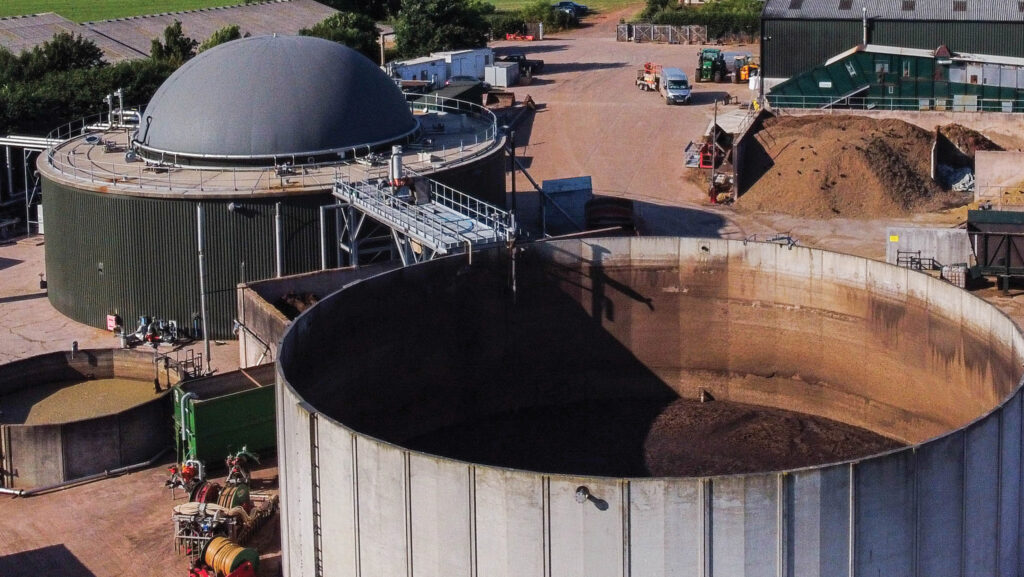
Of the 427 on-farm anaerobic digester (AD) plants operating at present in the UK, there are 79 running solely on livestock waste.
They vary in size from 4kWe to more than 3,000kWe generation capacity.
Many of these were built during the heyday of renewables, when the government’s Feed-in Tariff (FiT) and Renewable Heat Incentive (RHI) schemes offered payments for energy generated, greatly improving their financial viability.
New installations slumped when those schemes closed a few years ago, but there are signs that small-scale (sub-100kW) AD utilising animal waste produced on-farm is gaining traction again.
Dairy or other livestock farms with a ready supply of slurry or manure are at the forefront of this.
Especially given the wider political pressure to reduce greenhouse gas emissions and improve the carbon footprint of milk and meat production, says the National Non Food Crops Centre’s (NNFCC) Lucy Hopwood.
See also: Could agrivoltaics address the food vs fuel debate
Of the 90m tonnes of livestock waste produce annually in the UK, just 3% is used in AD.
“There’s a huge opportunity to put more of this waste through AD to help reduce emissions and deliver sustainability goals, while still allowing nutrients to be spread on land in a better, more available form [as digestate],” says Lucy.
Sustainability and the need to reduce emissions is an increasingly hot topic for milk buyers, and the biggest contributors are farms at the start of the supply chain, she says.
“Ten per cent of the country’s emissions come from agriculture; within that, farming contributes only 1% of carbon dioxide, whereas the big concerns are methane and nitrous oxide, of which agriculture accounts for 50% and 70% respectively.”
Capturing these gases and extracting value through biogas generation is potentially a win-win.
However, she acknowledges there are hurdles to overcome, not least grid availability and financing without support.
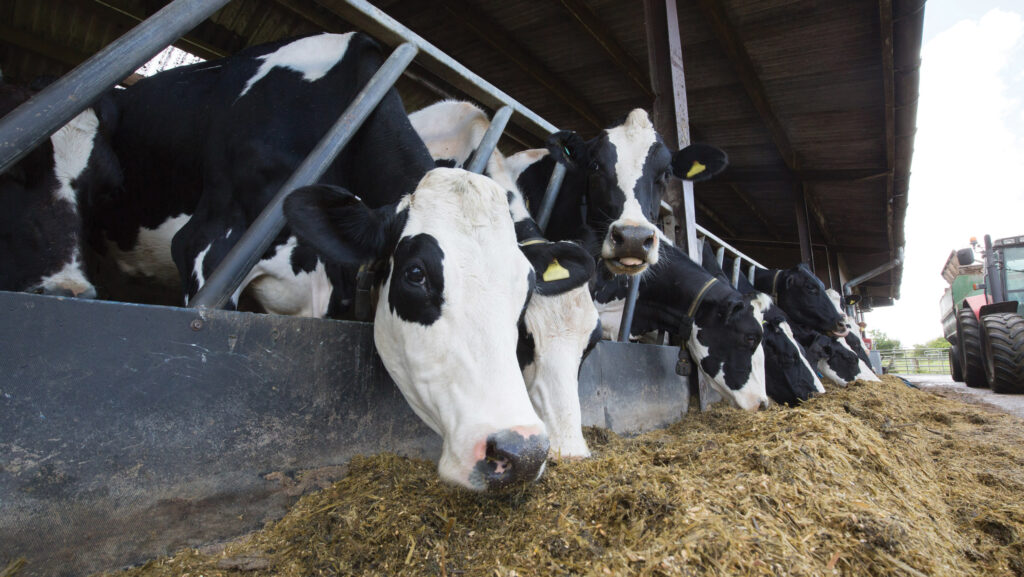
© Tim Scrivener
Many farmers believe AD is not financially viable without incentives such as FiTs and the RHI, says Lucy.
However, she insists this is not necessarily the case, especially when large proportions of energy can be used on-site and the value of wider benefits is included.
Main benefits of AD
Lucy summarises the main benefits as:
- Capturing additional value (energy) from farm waste
- Less exposure to volatile energy markets – energy security on-farm
- Reduced fugitive methane emissions from livestock waste
- Aligns with regenerative farming principles
- Reduces carbon footprint
- Improves utilisation of slurries and manures, turning them into a more useable form
- Wider soil, water and air quality improvements
- Improved soil carbon content and contribution to net-zero targets.
Valuing these wider benefits is difficult and there remain big questions over who should pay for or reward them. Some are trying, though.
Arla’s FarmAhead scheme, for example, offers a small premium on the farmgate milk price for farmers taking steps to reduce the carbon footprint of milk produced, and AD qualifies within this.
Others are expected to follow, as lowering the carbon footprint of meat and dairy products becomes increasingly important, says Lucy.
“It is also hoped there will be mechanisms in place to reward wider benefits in due course, making AD a more compelling case for those who cannot make it stack up on electricity displacement alone.”
North Yorkshire County Council is taking a lead on supporting small-scale farm AD, given its potential for renewable energy generation, carbon reduction and other environmental benefits.
It has recently awarded capital grant funding through its Shared Prosperity Fund, and Lucy hopes this will act as a catalyst for other local authorities to recognise the benefits of farm AD and do more to support new small-scale schemes.
Which farmers is AD suitable for?
Once operational, AD plants are designed to run 24/7, so need a consistent feedstock supply (slurry or manure).
This means they generally suit farms where sufficient cattle are housed year-round – typically at least 120 cows or more – and where there is a steady on-site demand for the energy generated.
Displacing bought-in electricity at 30p/kWh is more profitable than exporting it to the grid for 5p/kWh.
Allaster Dallas of the Farm Consultancy Group (FCG) says farm-scale AD units are often modular designs with an electrical generation capacity, typically varying from 22 to 74kW and costing anything from £200,000 to £500,000.
Some feature the traditional round reactor where slurry is fermented and gas captured, while others can capture gases coming off existing slurry stores, which is then upgraded to a useable form of biomethane.
“Crucially, AD has to be scale-appropriate for the business,” Lucy stresses.
“In the days of FiTs and RHI, some projects were built too big in an attempt to chase incentives, only to find operational performance suffered because of insufficient feedstock.”
The example costings table is for a mid-sized 44kW plant, which Allaster says should supply enough electricity for a 300-cow indoor dairy unit and a farmhouse.
The figures only consider electricity sales, so other benefits from digestate and/or heat use should be considered, too.
It also shows how net income and return on investment would change should electricity prices rise.
Example costings for a mid-sized 44kW farm AD plant |
|
Slurry produced by 320 cows |
16.96cu m/day |
Potential biogas yield |
424cu m/day (assumes 1cu m of slurry produces 25cu m biogas) |
Gas requirement for a 44kW engine |
17.5cu m/hour or 420cu m/day |
Farm electricity requirement (dairy and house) |
400kWh/day |
Electricity cost at 32p/kWh |
£128/day or £46,720/year |
Total cost of AD plant and connections |
£300,000 |
Depreciation (flat line over 20 years) |
£1,250/month (£15,000/year) |
Cost of borrowing over 20 years at 5% |
£1,753/month (£21,036/year) |
Repairs and any additional costs |
£700/month (£8,400/year) |
Total annual cost |
£44,436 |
Value of electricity generated |
£46,720/year |
Net income (and return on investment) |
£2,284 (1% ROI) |
Net income at 45p/kWh electric price |
£21,264 (7%) |
Net income at 62p/kWh electric price |
£46,084 (15%) |
Source: FCG |
Grid connection is a potential issue for any new energy generation, even if most electricity is to be used on-site, so speak to your network operator at the outset to check local availability, Allaster advises.
Siting of any proposed AD plant and associated storage tanks needs careful planning, considering the logistics of where slurry/digestate has to be moved from/to, cabling/pipework routes, and any environmental constraints.
The Environment Agency should be consulted, as there are restrictions governing proximity to watercourses and areas of environmental protection.
“Generally, small AD plants can get through under an EA exemption rather than requiring a full permit, providing operating conditions are right,” says Lucy.
“It’s still a closely monitored and regulated activity, but doesn’t carry the permitting cost and administrative burden of larger AD plants.”
Farmers should also check with their local planning department whether planning permission is required, or whether installations qualify under permitted development.
Allaster notes AD does not generally suit systems where cows are bedded on sand, given its abrasiveness to equipment (especially pumps) and risk of sediment build-up in fermenters.
Ways of addressing this, such as slurry pre-treatment, are under investigation.
AD plant helps farm move towards energy self-sufficiency
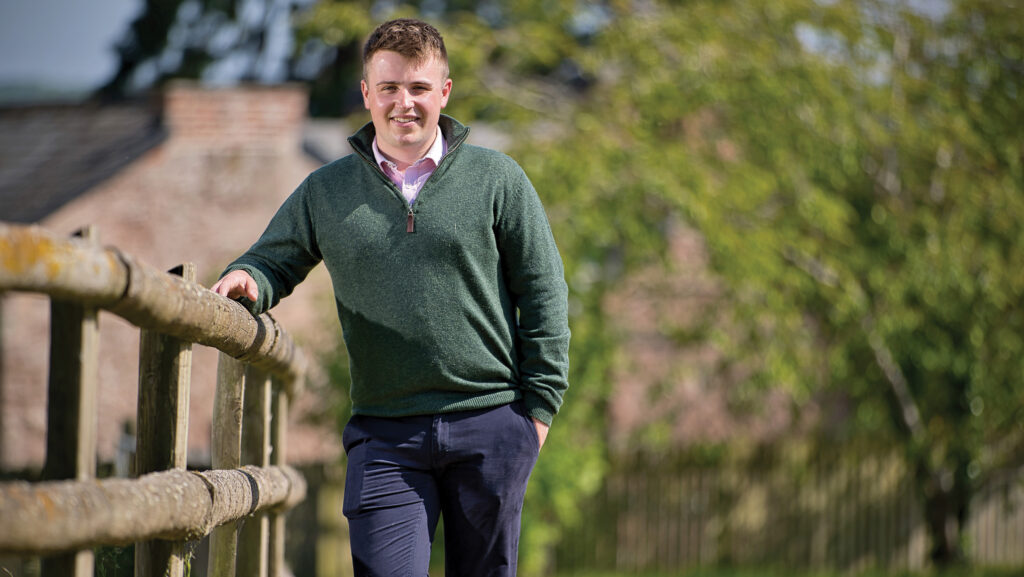
Harry Davies © Richard Stanton
Hopes Ash Farms in Herefordshire installed a 22kW slurry-only AD plant last autumn in a bid to become more energy self-sufficient and better utilise waste from its 130-cow dairy herd.
Harry Davies, who runs the 200ha mixed arable, poultry and dairy farm with father Robert, is pleased with the system’s performance over the past year.
He estimates it meets 90-95% of the dairy unit’s electricity requirements, equivalent to around 530kWh a day.
“There were a few teething issues, but generally, the technology’s working really well so far.
“The automated system is fairly hands-off in terms of management. I monitor everything via my phone app and only need to step in if something goes wrong.”
Cows are housed year-round on mattresses and a recycled paper product, with milking operations occurring 24/7 through two Lely A3 robots.
So there is a consistent supply of slurry for the AD plant and a fairly steady energy demand year-round.
Slurry is collected in a reception pit, from which 4cu m is automatically taken out four times a day straight into the digester.
Material leaving the digester goes through a separator, splitting it into phosphate-rich solids (exported to neighbouring farms) and a nitrogen-rich liquid (stored and used on-farm).
A new slurry store was built to hold the liquid proportion, and doing so highlighted a major issue Harry and his father want other farmers to be aware of.
“We initially applied for a Slurry Infrastructure Grant (SIG) towards the new store, but only discovered during the application process that this specifically excludes digestate storage,” Harry explains.
“So, even though we’re only putting 100% slurry into the AD plant, because it goes through a fermentation process, Defra classifies the product coming out as digestate, not slurry, so the store is ineligible for SIG grant funding. In our case, the grant would’ve been worth £50,000-£80,000, so that’s a huge funding gap we had to cover.”
Rules also state that where a slurry store has been built under the SIG scheme, farmers must wait five years before using it to store digestate.
“The NFU has lobbied to change the stance on this, but sadly to no avail.”
In total, the Davies’s AD plant cost around £200,000, with an extra £50,000 for groundworks, concrete and pipework.
Once additional storage, slurry separator, and all associated infrastructure was included, costs were nearing £500,000.
Harry says the extra costs were higher than others might expect due to the topography and layout of the site.
Based on an electricity price of 30p/kWh if the farm had to buy in the electricity it produces, he estimates the AD plant will pay back in 10 years through electricity savings.
This could be longer or shorter depending on future prices.
“Currently, we’re only using waste heat to maintain the reactor temperature at 43C, but we’re considering how else it could be used.”
Even though most electricity is used on-site, the plant still required a grid connection, which can be an issue in areas with limited capacity for new connections.
It also needed planning permission and specialist insurance.
“Our insurer needed quite a few extra documents from the technology provider, but once they got those, it was fairly straightforward to sort out.”
The farm is a member of Arla’s FarmAhead incentive, so the AD plant contributes towards their score for this.
However, Harry admits that was not a major factor in the decision to go ahead with the project.
“AD is something we as a family have always been interested in, and as we are fully committed to milking cows and needed to update our slurry infrastructure, it made sense to try and extract additional value from it.”