Tips to help keep biomass boilers running trouble-free
Burning timber from your own woodland in boilers to provide heat for houses and offices seems like a bit of a no-brainer, especially when Theresa May will pay you for doing so through the Renewable Heat Incentive.
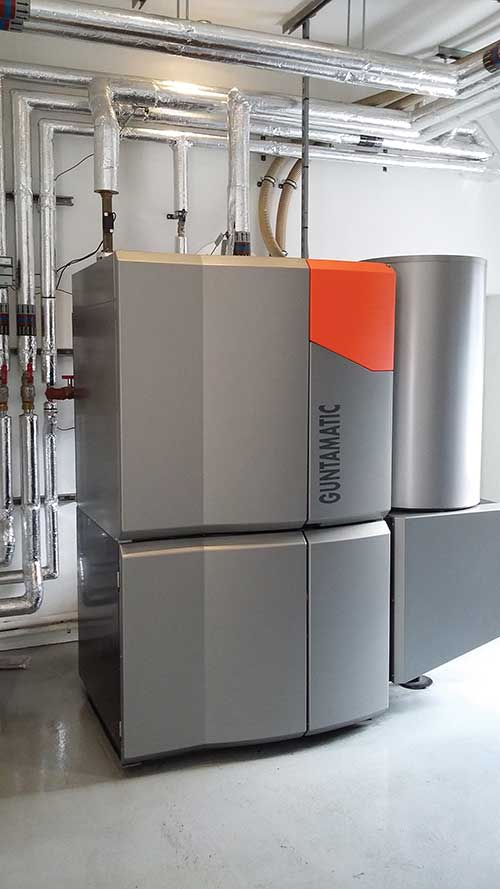
© Mark Campbell
However, if you have to buy in timber, the figures don’t make such great viewing, as prices have become hard to justify in recent times.
Two years ago, roadside cordwood timber cost about £30/t, but it is now closer to £42/t. It’s the same story if you buy in ready-to-burn chip.
You will now be forking out over £100/t for decent stuff – two years previous it was £60/t – which will make any owner question the viability of this heating method, especially if you’re depleting your own woodlands at an unsustainable rate.
See also: Dorset grower’s guide to building a cash-saving DIY grain dryer
So, keeping these boilers efficient and well maintained is key to make the most from the fuel, but also to avoid the wallet-shattering replacement parts.
These high costs are driven by the monopoly of a sole importer and the limited choice for new spares due to the depleted biomass market below 500kW.
We’ve chosen two 99kW Guntamatic boilers for this article – there are plenty of other makes on the market, of course – and guiding us through the dirty work is Mark Campbell, an independent biomass engineer with more than 30 years’ experience looking after boilers.
The boilers are part of a 2010 installation at the 1,000ha Chaldean Estate in Hertfordshire. The system looks after a number of residential houses as well as the estate’s offices and has also been used to dry grain during the summer.
Over the eight years, the two Austrian boilers have clocked up a mammoth 47,000 hours each, which means they are some of the hardest-working biomass boilers in the country.
What is a biomass boiler?
Biomass boilers are large heat generators that warm water by burning renewable fuel. The water is then stored in a buffer tank before flowing around a system providing heat to buildings via heat exchangers or direct connection.
There are a number of working parts within these boilers and due to the exposure to heat and carbon, thorough maintenance is required to prolong efficient and operational life.
Fuelling options for these are varied, with the most common being woodchip – either soft or hardwood – and wood pellets.
However, with the timber price going up, alternative fuels are being explored, including pellets, straw, pallets and even wheat. Other potential fuel sources include willow, miscanthus and landfill timber recovery.
1. Baffles – £15 each
With a minimum of 31 baffles in each boiler, replacing them all every few years will soon eat away at any profit.
These are essential to control the flow of heat from the burning area through the boiler up to the flue, allowing the heat to radiate from the tubes to the boiler in order to maintain its temperature.
These baffles move up and down in vertical holes and also help to keep the channels clear of muck for air to pass through. They are made from mild steel and are spiral in shape to slow heat, but not stop it. Temperatures can hit 1,200C during work, so it’s not a surprise they don’t last forever.
Carbon is the main killer of these baffles (a by-product of burning) and ends up chewing away and distorting the tops until they snap.
Rather than paying for a full new set, Mr Campbell cuts the affected areas back to good steel and then weld sections from donor spirals onto the original, bringing it back up to the full length and strength.
A baffle will usually do about two to three years before it needs replacing, although it depends on use and fuel as wood pellets are harder on wearing parts than woodchip.
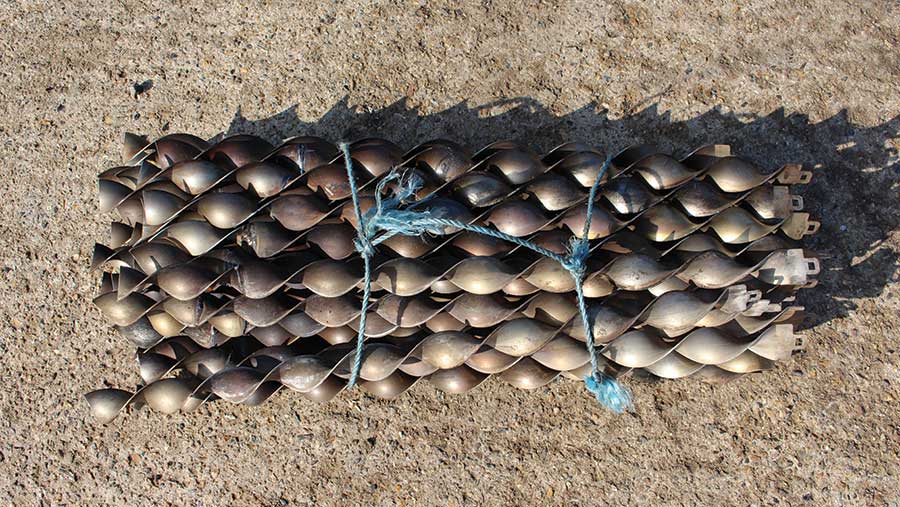
A full set of refurbished baffles © Edd Mowbray/RBI
2. Augers – £144-£600
On a Guntamatic boiler, there are two main augers keeping material moving. The main fuel auger transfers woodchip from the hopper into the boiler, while the stoker auger keeps the fire lit. There’s also a smaller ash auger that prevents an ash blockage.
These are driven by high-torque, low-ratio ABM gearboxes that work in bursts rather than a continual pull and Mr Campbell has seen all three break during his time working on boilers.
It’s surprising how tough woodchip can be on the steel augers, but most should last about 20,000 hours before any remedial work is needed to the flights.
Softwood will be easier on the metal and you may get 30,000 hours from a set of flights. Eventually, the leading edge becomes worn and rounded from the constant battering against the chip, so a bead of weld up to 6mm thick is run along the edge and then ground back flat to bring it back to life.
Heat and carbon have a large effect on the stoker auger as it it sits next to the burning area. Over the years, it will wear away the steel to a point where the auger is too short to keep the woodchip supply at the correct ratio.

Worn auger flights © Edd Mowbray/RBI
3. Gearboxes – £550
These components should last the life of the boiler. They are rarely under any stress unless there is excessively large material in the hopper or the fuel is too wet.
A small dab of copper grease is required to keep the sprockets from nattering and seizing up. These are a good gauge to alert you to a problem with the fuel as the gearbox note will change from its usual tone.
If they have been under serious stress, gearbox oil can start dripping from the housing. Most commonly, the cause is an oil seal leak from the auger and gearbox connection, solved by a simple £7 part and a bit of patience to strip it down – this can save a hefty bill.
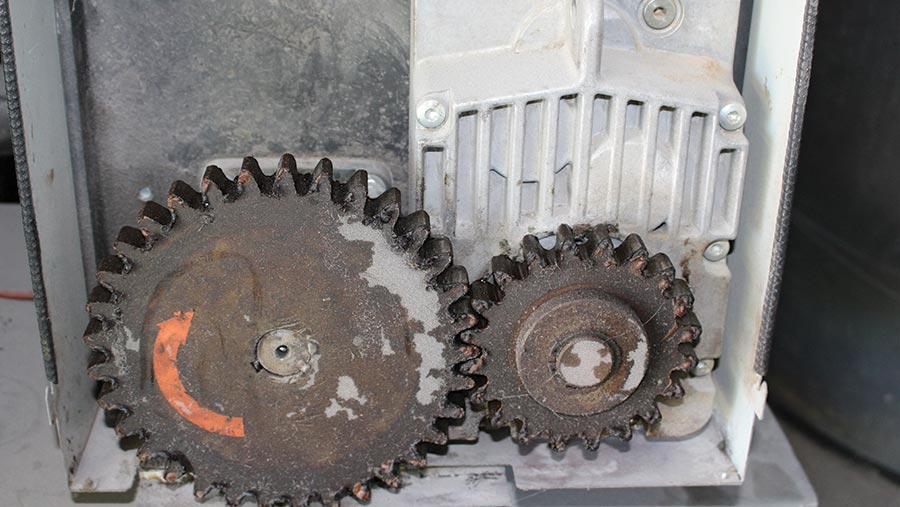
Gearbox and cogs requiring copper grease © Edd Mowbray/RBI
4. Meters – £350
Early installs mainly had battery-powered metering units that had sealed batteries good for about seven years. Unfortunately, they provided no warning when the battery started to lose power and the gradual decline meant a slowdown in actual recording or complete failure.
See also: Biomass boilers: Do wood pellets stack up?
These meters are used to provide quarterly figures to the government for Renewable Heat Incentive (RHI) payments and there have been a few cases where consumption outweighed generation and payments were withheld until the issues were resolved.
If installs have been based purely on this income, it needs to be carefully monitored.
Newer installs have meters hardwired into the electric circuit and Mr Campbell has found a way of fixing older units to run from the same power source as newer set-ups.
5. Step grates – £36-£64 (approx)
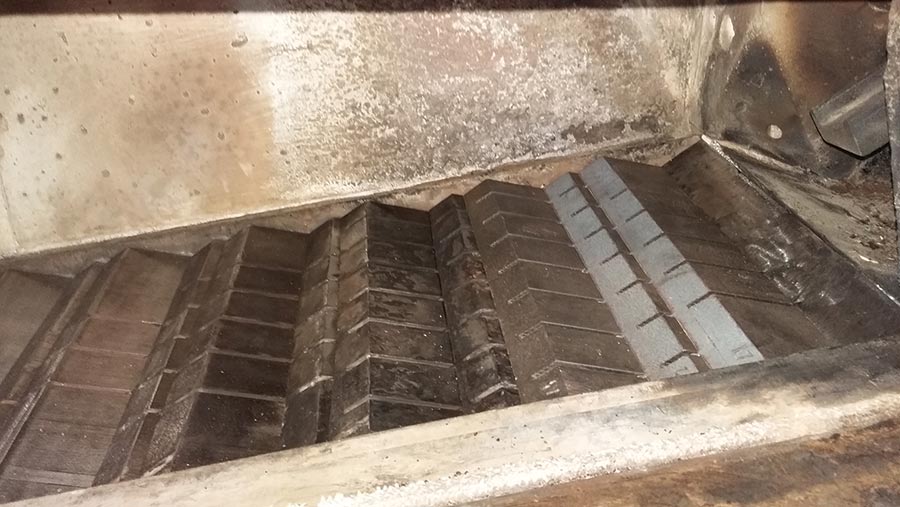
Step grates © Mark Campbell
Due to their proximity to the fire, the carbon builds up quickly and can become quite severe if not regularly cleaned away. If it’s really bad, a hammer and chisel will be needed to clear the carbon build-up to allow the grates to move freely.
Once the burn has finished, the ash is walked down to the ash bins via an arrangement of step grates. These are positioned on an angle and slide up and down to ferry the ash away from the burning area.
6. Buffer tank – £1,100-£2,800 (depending on size)
Most installs will have the buffer tank raised off the floor to allow air underneath to prevent the steel from rotting away.
However, the insulating jacket around the tank drops down to sit on the floor. This limits any air movement underneath and condensation, along with shoddy water quality, can rust the bottom of the tank.
To prevent this from happening, lifting the jacket by 200mm should allow air in and limit the heat escaping, making rust a thing of the past.
7. Other issues
Ropes – £38/m
There are small- and large-diameter ropes around the ash bins and burn chambers to keep the boiler airtight. These have metal braided through them and are alarmingly expensive to replace.
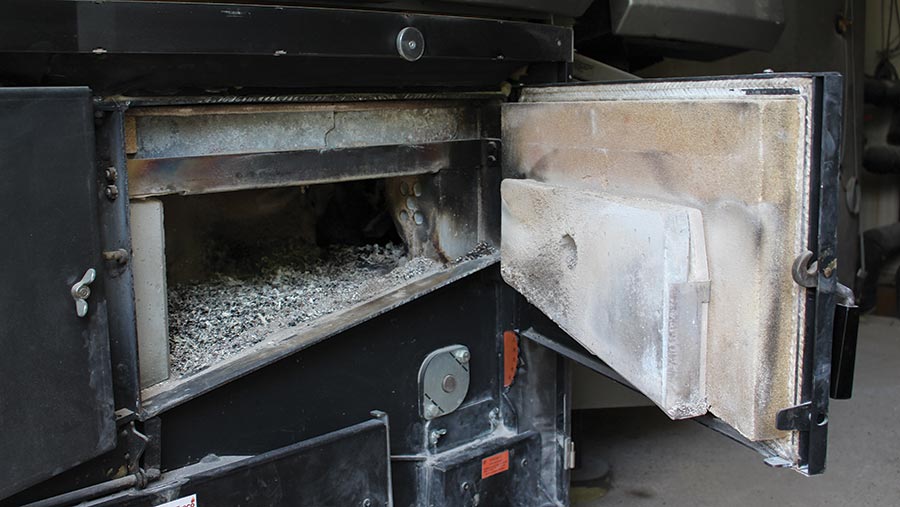
© Edd Mowbray/RBI
Heat exchanger – £6,000
This is the heart of the boiler. Failure requires a full strip-down, taking it out of the boiler house by a forklift after disconnecting the flue and electrics.
Due to its integral nature, these don’t need replacing very often, but lifespan is affected by most factors including fuel, running time, system flow rates and water quality.
PCB failure – £600-£900
This is usually down to higher incoming voltage powering the boiler house, most commonly when the system has been connected to solar panels that can have fluctuations in voltage delivery.
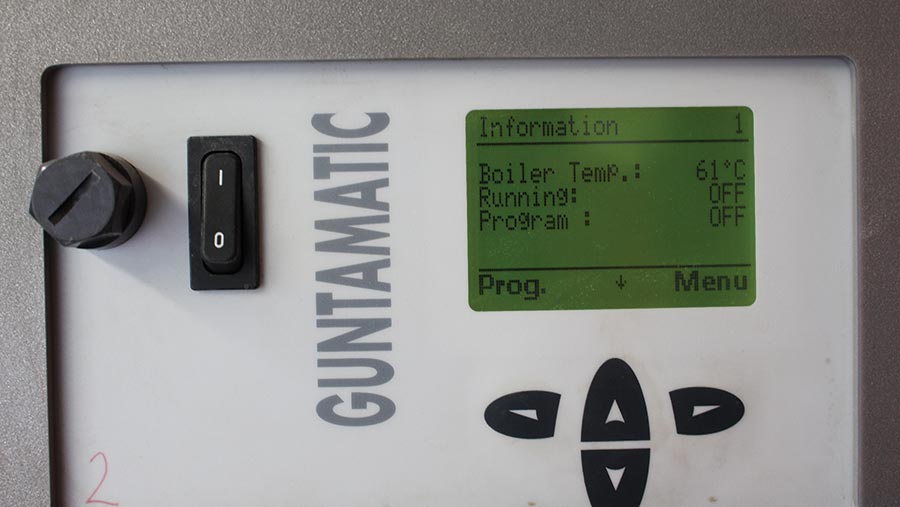
Old-style screen on a Guntamic boiler © Edd Mowbray/RBI
Mice and rats – decent pest control
Boiler houses are usually warm areas and make ideal winter homes for rodents. Keeping them out will not only keep the wires in check, but prevent any nasty smells developing.
MC Independent biomass
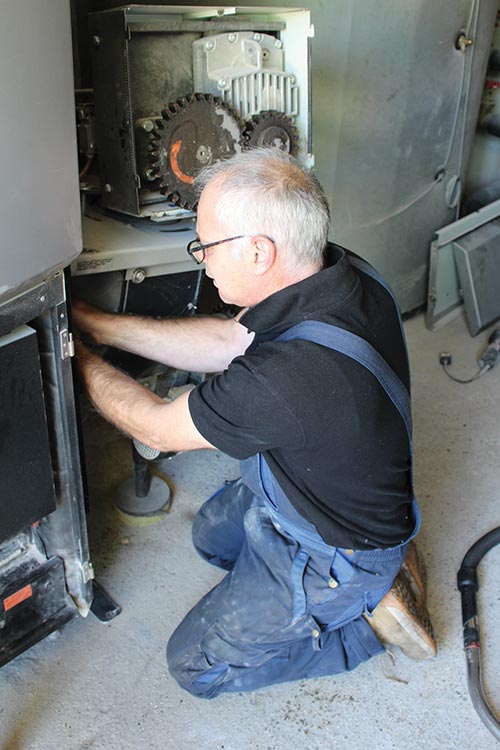
Mark Campbell © Edd Mowbray/RBI
With more than 30 years’ experience as an engineer, three years ago Mark Campbell left Treco, the Devon-based importer of Guntamatic boilers, and set up a business providing service agreements to owners of biomass systems.
Operating countrywide, he now has about 120 yearly contracts, with more than 40 of these in Hertfordshire.
These contracts offer no hidden fees, with labour costs for breakdowns and repairs all included in the price and only spare parts charged to the customer at cost price.
Not only this, Mr Campbell is always looking for modifications and repairs to save his customers money by not shelling out for expensive parts, preferring repair to replacement.
On the newer installs, he can have remote access to boiler systems in case there are issues.