On-farm renewable energy systems: All you need to know
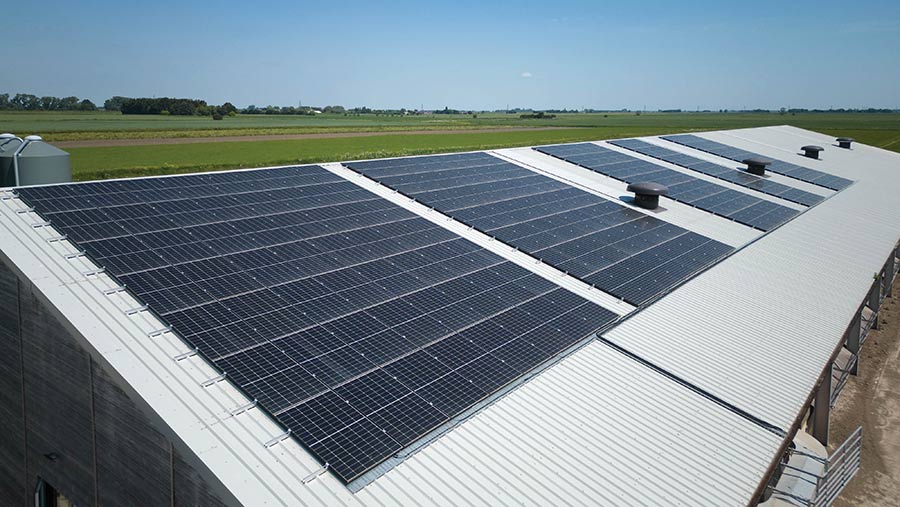
The case for investing in on-farm renewable energy has arguably never been stronger.
Fuel prices soared in the past 18 months, driven by the effect of the conflict in Ukraine, adding to an already difficult economic climate after the Covid pandemic.
See also: Biodiversity net gain detail includes ‘stacking payments’ option
Although fuel costs have now dropped they remain high and are creeping up again, squeezing farm business margins.
We look at the pros and cons of investing in renewables on farm, which source is best suited for your farm and what practical, legal and political challenges might crop up.
Why invest in renewables?
Pressure to hit environmental targets is growing as political and consumer influences demand action in a bid to avert climate change.
At the same time, advances in the renewables sector mean the capital cost for hardware, such as solar panels and heat pumps, is lower, in relative terms, than it was when the technology was in its infancy.
These factors make investing in on-farm renewable energy systems feasible even without government incentives, says Dr Jonathan Scurlock, NFU chief adviser, renewable energy and climate change.
Some renewable energy systems could generate 75% of a farm’s needs, isolating it from volatile fuel markets, Jonathan suggests.
Environmental, social and governance (ESG) standards, which measure a business’s effect on society and the environment, are also a developing challenge.
Renewables could help a business with its ESG targets and commitments.
In addition, the government and industry champions such as the NFU have ambitions to counterbalance greenhouse gas emissions from farming.
Producers want to do their bit because they can see that agriculture is exposed to increasingly frequent periods of extreme weather, Jonathan says.
They can see there is clearly a need to adapt and continue the move from reliance on oil, diesel or LPG-powered machinery towards renewable energy for electrification.
Pros, cons and advice for different renewable energy types
With all renewable energy types, you need to establish the capacity required.
There is no such thing as a typical farm, so take advice and work out the capacity needed to cover peak and residual demand, Jonathan advises.
In the past, government incentives made for a lucrative income, so producing surplus energy was a target.
But now, exporting is less valuable than the potential savings to be made with imported electricity at 25-35p/kWh, so matching demand and supply is critical.
Solar
Photovoltaic (PV) panels are the most common form of renewable power source on farms, converting sunlight into electrical energy. They are simple with no moving parts, so require minimal upkeep.
But it’s not a case of fit and forget with PV panels – they are not maintenance free, Jonathan warns.
An annual service is advisable and the effectiveness of the panels can be limited by dust or corrosive fallout from ventilation outlets on livestock buildings.
When working efficiently they could cut up to 75% from an energy bill.
In most cases, panels are roof-mounted but where this is not possible a ground-mounted array could be set up on spare land.
For roof-mounted panels generating less than 1MW of power, full planning permission is not necessary in England.
Instead, an installation is covered by permitted development rights (PDRs).
Even so, it is advisable to consult local authorities before going ahead. In Scotland a much tighter ceiling of 50kW is applied to PDR ventures.
This is under review with a consultation completed in August and a response from the Scottish government awaited.
For ground-mounted arrays, it is necessary to have full planning permission agreed before going ahead.
An interesting development in England is a current government consultation on the siting of solar canopies.
These could be constructed over hard standing vehicle parking which is particularly useful for charging points for electric vehicles, for example, Jonathan points out.
Considerations
Even a modest PV installation may be constrained by approvals from the power distribution network.
Operators do not want overloads that can shut down a network or see frequency variations associated with solar- or wind-powered setups.
An engineer will, therefore, scrutinise the project and decide whether it could trigger “faults” in the local grid.
To overcome this likelihood power diverters can be fitted to limit exported electricity.
For example, power can be diverted to an ice builder or other equipment with a switchable high demand.
Alternatively a gate, known as a reverse power relay, can be installed to block the surplus energy from moving into the network.
NFU energy consultant Thomas Ovenden says battery banks are often associated with solar PV installations to store surplus power and mete out energy in periods when generation dips below demand.
For example, a dairy farm may have a high demand early in the morning before solar generation kicks in.
But battery systems are expensive and it may be better to store excess energy as hot water or an ice bank.
Wind
The options for wind energy on farms are more limited than solar.
While almost one-third of farms have solar panels, and the number is increasing, just 5% have wind power and that figure has been almost static since 2015, says Jonathan.
The stagnation began when planning restrictions were tightened early in the Conservatives’ administration under David Cameron.
There was parliamentary opposition to the visual impact of turbines which, by necessity, must be sited on exposed land to exploit wind flow, he says.
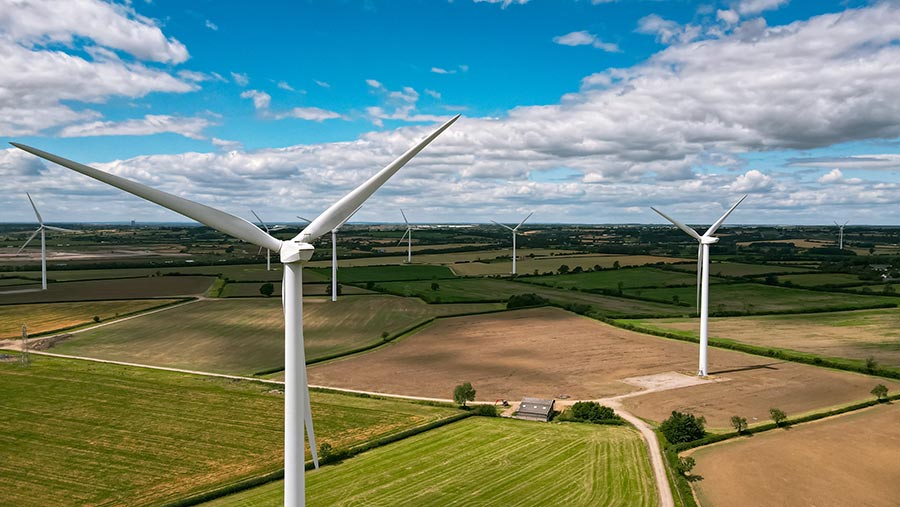
© WD Stockphotos/Adobe Stock
This is a big and almost insurmountable barrier because the tighter rules apply equally to smaller, single wind turbines as well as large farms.
In practical terms the PDR limit, before full planning permission is required, is hopelessly too small at present. The maximum permitted size is a single 10m tower with a 2m-diameter rotor.
This will only produce 1-2kW of power, possibly enough for a house, but not a farm business.
A turbine large enough for a farm business would need to be about 25m tall to produce about 30-40kW. Currently, that would require planning permission which is difficult to obtain, Jonathan says.
A wind project will need local community support. It must also fit in with a local authority plan or it will be rejected by the planning committee.
Considerations
The growing expectation is that an incoming government may look again at the situation which has all but shut down Britain’s small wind power industry.
The UK has relatively high average wind speeds and many small businesses and communities could benefit particularly in the winter when solar is less effective.
A campaign is building to get height restrictions under PDRs raised.
The premise is that mobile phone masts are permitted up to 30m, outside areas of outstanding natural beauty and National Parks and 25m within them, he adds.
Average wind speed is critical. Under 5m/sec is insufficient, Thomas explains.
However, many sites are in excess of 6m/sec or even 8m/sec and large areas of the UK are suitable.
The contradiction is an open, hilly landscape might not meet stringent planning controls. But positioning a turbine out of sight is likely to mean it is too sheltered to be effective.
Biomass
About 8% of UK farms use or supply biomass fuel in the form of tree trimmings, an energy crop, crop residues or by-products.
Woodchip- or pellet-fed boilers are generally the most convenient option for on-site heating.

© Tim Scrivener
These can be automated, self-feeding, adding further convenience. Uses typically include heating livestock sheds or farmhouses.
For example, in poultry sheds a 100-200kW boiler can produce hot water to circulate, radiating heat and, less commonly, hot air, says Jonathan.
Considerations
Sizing a boiler appropriately is imperative. Too large, and the boiler will need high feed-source inputs to run at optimum temperatures; too small, and the output won’t be sufficient, says Thomas.
But, depending on considerations, a biomass boiler can still make sense, whether it’s as a replacement for an existing heating unit or to provide supplementary heat.
Hydro
This is a minority area for renewable energy because of the particular geography requirements and stringent permitting controls, Jonathan says.
Generally, on-farm hydropower units are classified as micro when they are below 100kW, and mini from 100kW to 1MW.
Capacity is, to an extent, dictated by the geography, says Jonathan. The ideal is for a high-head system with up to a 30m water drop and good flows in both summer and winter.
A low-head unit, suited to lower water drops, on a wider river or weir, may channel off water through a slow-rotating Archimedes screw before returning it downstream.
Considerations
The Environment Agency’s requirements, which include a permit to abstract water upstream of the unit and another to return it downstream, along with planning permission, can push up the time and cost of a hydro-energy unit, he warns.
Costs also vary hugely, but whichever system, it is likely to be bespoke to meet the nature of the water supply and the outlay can be high, adds Thomas.
To ensure flows are maintained and regulated, extensive construction work may be needed to create channels, pipework, reservoirs and pen stocks.
Heat pumps
Heat pumps work by extracting heat from the ground or air using temperature differentials.
The relatively cool fluid in piping draws heat from the ground passing through a heat exchanger and into the pump to heat water.
Similarly, air-source heat pumps extract heat from air flowing through the unit.
Typical applications are in protected horticulture or poultry or in housed livestock sheds. Some producers run sheds entirely on an all-electric system.
Considerations
A potential downside is that the system relies on a constant electrical energy source to power the pump, says Jonathan.
In remote areas where the grid supply may be interrupted, a backup diesel generator for the pump or fossil- fuel powered heating system may still be required.
Heat pumps can be installed under PDRs, but larger set-ups will need full planning permission.
Ground-source pumps take up large areas of land – about 700sq m. This is needed to bury long runs of coils at depths of about 1m to draw sufficient heat from the earth around them.
Heat pumps are three times more efficient at producing energy than a gas-fired system.
But because a unit of gas is cheaper than a unit of electricity, some of the economic benefit is lost in running the air or heat pump system, according to Thomas.
Anaerobic digestion
There are significant opportunities for AD energy production, whether it is slurry-fed on livestock farms or a crop/food-waste system.
By capturing and storing carbon dioxide from the slurry or feedstock, it is possible to run a carbon-negative AD plant.
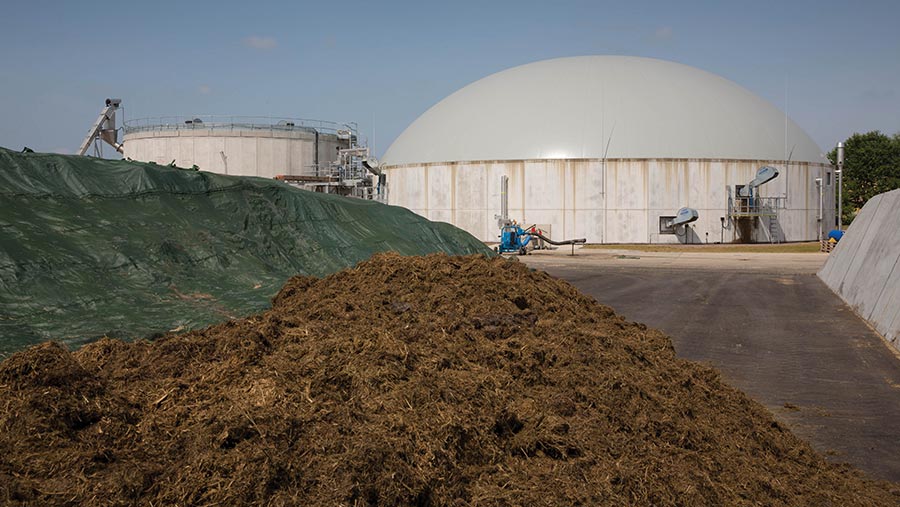
© Tim Scrivener
But while there is a long-term need to displace gas from fossil fuels with green gas, the government is not particularly supportive of AD.
This has led to the category being dubbed the Cinderella of renewables, says Jonathan.
There are benefits aside from efficient renewable energy creation, which include the yield of nutrient-rich digestate, carbon capture, food-grade carbon dioxide production and reduced diffuse pollution risks.
Considerations
Even without government support larger plants may be viable, particularly when gas prices are high.
And markets are emerging for food-grade carbon dioxide and carbon offsetting, through geological carbon capture and storage.
However, there is a world of difference between the big 1-5MW commercial units designed to exploit these markets and on-farm 50-200kW systems.
The economics of a small-scale AD plant are difficult to stack up without government support, but they can operate efficiently on big dairy units to manage slurry handling.
Renewable energy, costs and outputs |
|||||||||
|
Solar |
Battery |
Wind |
Hydro |
Heat pumps |
Anaerobic digester (AD) |
Biomass |
||
Air-source |
Ground-source |
Micro AD |
Large AD |
||||||
Cost |
£1,000-£1,400/kW |
4kWh: £3,500 |
5kW: £24,000 |
Smaller not 25kW: £169,000 (£6,800/kW) |
5kW: £7,000 |
4kW: £17,000 |
Micro AD – AD with combined heat and power (CHP) |
AD with CHP and gas to grid injection 250t/day £10m |
100kW: £50,000 200 kW £80,000 |
Maintenance |
£200/year cleaning |
Minimal – possible annual service or clean |
100kW: £9,000/year Exponentially higher at smaller scale |
5kW: £2,200 25kW: £4,000 50kW: £6,300 100kW: £11,000 250kW: £25,000 500kW: £48,300 |
Average house: £1,200/year on electricity bill (assuming 4,000kWh and 30p/kWh) £150 service two to three years |
Lower than air-source heat pump, as ground temperature is more stable than |
AD plants require skilled operators to maximise efficiency |
Large AD plants require skilled management and a high labour input to maximise efficiency |
£1,000/year |
Lifespan |
25 years (inverter |
15 years |
25 years |
25 years as precaution, likely 50+ years |
15-25 years |
15-25 years |
25 years |
25 years |
15-25 years |
Generation |
850-1,000 kWh/year per kW installed |
n/a |
5kW: 8,900kWh 15kW: 36,000kWh |
5kW: 22MWh 25kW: 110MWh 50kW: 219MWh 100kW: 438MWh 250kW: 500kW: |
300% efficiency Produces 3kW heat per 1kW electricity |
300-400% efficiency Produces 3-4kW heat per 1kW electricity |
Can be fitted with CHP for outputs of 24kW, 30kW, 40kW, 60kW |
Typically fitted with CHP ranging from 250kW to 500kW |
n/a |
Grants |
None |
None |
None |
None |
Boiler Upgrade Scheme £7,500 for ASH |
Boiler Upgrade Scheme £6,000 for GSHP |
None |
None |
Boiler Upgrade Scheme £5,000 for biomass |
Source: NFU Energy |
Transition Farmer Eddie Andrew
Transition Farmer Eddie Andrew has embraced renewable energy systems with solar panels already in place and plans to install an anaerobic digester under way.
Photovoltaic panels sited on the Sheffield farm dairy roof provide 15kW of energy to power the refrigeration unit and most of the dairy’s needs.
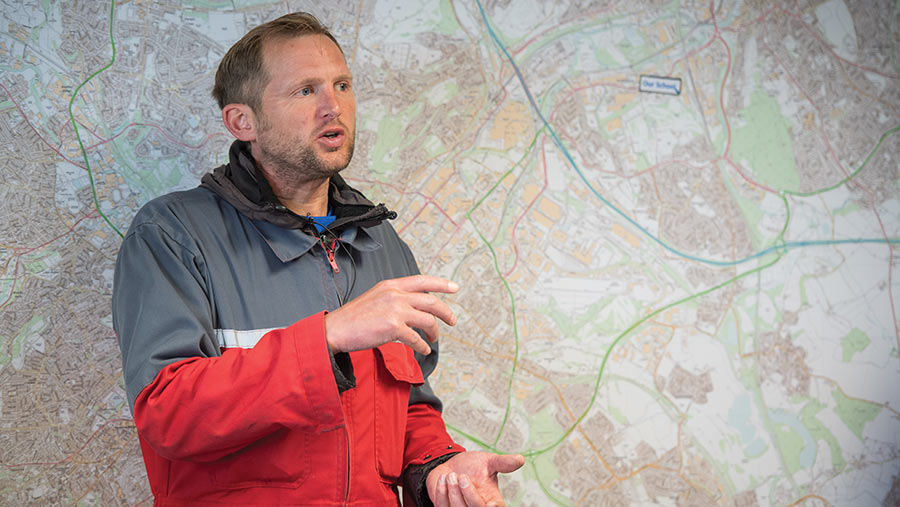
Eddie Andrew © Jon Parker Lee
A 3kW panel on the farm cottage is used to charge a Mitsubishi Ecodan air-source heat pump supplying the house with hot water.
However, Eddie’s belief is that an anaerobic digester (AD) plant is the way forward for the farm.
“Although the panels are easy to use and require little maintenance, they don’t provide the constant level of power we need 24/7,” he says.
“And with robot milkers being installed as part of a new building development, that demand for constant power will increase.
“That’s one of the reasons we are progressing with plans to install a slurry-fed AD plant to meet the power need from the new building while supplying the farmhouse and cottage.”
The plant will also reduce methane emissions, help isolate the business from the fluctuating prices of bought-in energy and produce a valuable fertiliser in the form of digestate.
The chosen system is a slurry-to-electric unit supplied by Biolectric.
Slurry passes into a manure pit to an automated system that pumps a fixed quantity of slurry into the reactor where biogas is formed.
The gas is drawn off and purified to supply a generator that creates electrical power and hot water. Digestate is pumped out into external storage tanks.
Eddie has also looked at two other systems for the future, including Bennamann and Nomad units, which recover methane from slurry lagoons.
The lagoon is covered and, as methane is produced, the cover inflates to store gas.
The methane is cleaned and siphoned off under pressure and can be used as biogas or converted into biomethane to power vehicles.
Transition Farmer Irwel Jones
Transition Farmer Irwel Jones set up a small hydropower system on his Welsh sheep and beef unit in 2015 to provide electricity for the farmhouse and buildings.
The steep-sided hill farm has the ideal geography to power a high-head system from a narrow watercourse.
Water drops 115m down the hillside through a pipe just 120mm in diameter.
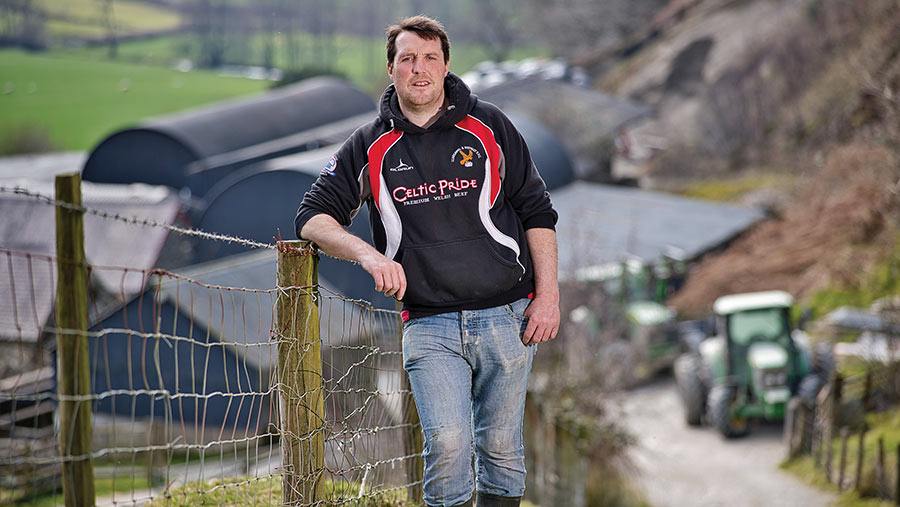
Irwel Jones © Richard Stanton
For every 10m fall the water produces 1bar of pressure so, by the time it reaches the outlet, it has created 11.5bar sufficient to run a 7kW turbine.
This creates roughly four times as much energy as the farm uses with the surplus sold to the grid under a contract agreed in 2015.
The government Feed-in-Tariffs (Fits) system, which was still operating in 2015, paid enough to make the venture viable, says Irwel.
The 25-year agreement is based on a notional amount of electricity generation and pays out even during drier months when the waterflow is slower.
“Generally, we are overproducing for three months of the year, six months somewhere in between and three months with the turbine idling,” Irwel reckons.
To even out the supply and make better use of overproduction in the peak months, Irwel is considering a battery bank installation.
It would also store energy generated during power cuts, which occur at the farm from time to time, preventing the export of power to the grid.
The total initial outlay of £70,000 has almost been recovered, and return on investment is expected in 2024, thanks to the Fits contract.
Maintenance is low with everything on the turbine automated. An annual service which includes cleaning the 115m pipe is required and costs about £200.
A potential looming cost is the turbine itself which may need replacing after 10 years at a cost of about £4,000-£5,000.
But Irwel warns permitting and planning took five years due to the Environment Agency’s rigorous process.