Safe farms, safe staff and visitors – a guide to legislation
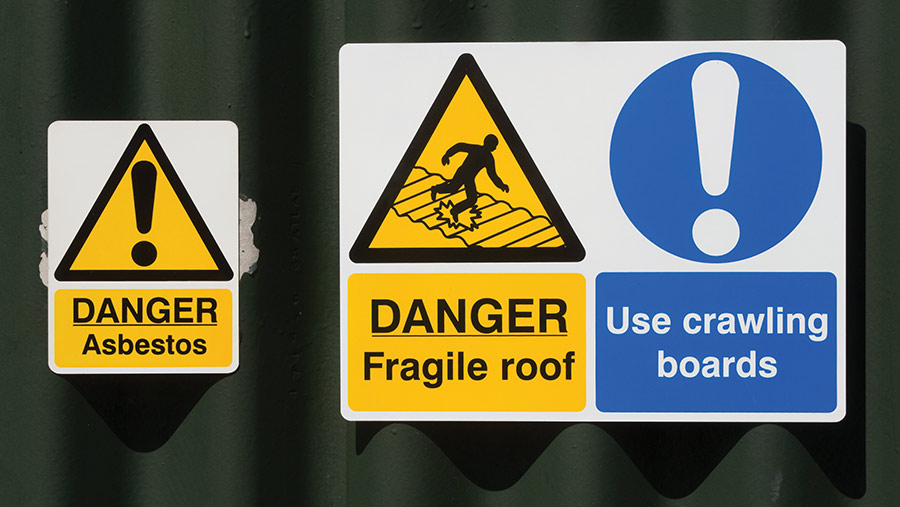
While agriculture employs just 1.5% of the total UK workforce it accounts for almost 20% of all workplace fatalities in Britain.
Aside from the devastating impact on families, friends and co-workers, deaths and injuries cost the industry £200m in fines, lost earnings and remedial work each year.
See also: Farm fatality – what happens next
Yet, according to the Health & Safety Executive (HSE) and safety consultants, most accidents are still caused by unnecessary risk taking and poor planning.
The most common causes of death and injury in UK farming are:
- Struck by moving vehicles
- Struck by moving objects – such as bales and trees
- Falls from height
- Suffocation or drowning
- Contact with machinery
- Injury by an animal
- Trapped by something collapsing or overturning
- Electrocution
- Handling, lifting or carrying
- Trips or falls on the same level
- Ill health due to exposure to zoonoses (diseases from animals), chemicals, dust, machinery noise and vibration.
To tackle the various issues, a plethora of legislative measures and guidelines has been developed. Strutt & Parker farming department director and health and safety consultant Rob Gazely runs through some of the key health and safety advice.
The overarching pieces of legislation are:
- The Health and Safety at Work Act 1974 which places a duty of care on employers to protect the health, safety and welfare of their employees and anyone else who may be affected by their actions.
- The Management of Health and Safety at Work Regulations 1999 which require all employers and employees who share a workplace to co-operate with each other and co-ordinate their work to ensure everyone complies with the law.
These, along with other laws, relate to the main causes of death and injury and also include staff management obligations.
Staff management
In carrying out on-farm audits Mr Gazely says he encounters a range of attitudes towards health and safety, ranging from “sheer complacency to incredibly engaged and astute”.
Farmers must, by law, encourage a positive approach to health and safety across their units and with their employees, he advises.
Safety management plan
Farm businesses should have a safety management plan which the HSE suggests should be formed around a five-step process.
1. Safety policy A written policy – specific to the farm business – should be agreed, signed and dated. This is a legal requirement for farms employing five or more staff although is recommended as good practice for all workplaces. It must identify those responsible for its implementation and should be reviewed regularly and updated if the business changes.
2. Organisation of the workforce The safety management plan should reinforce the importance of health and safety and provide information on hazards, risks and precautions. It should also involve the workforce in developing the plan, provide them with clear direction and meet training needs.
3. Plan tasks Tasks must include a risk assessment and be planned with health and safety at the forefront, including a demonstrated standard of work.
4. Review The plan must be reviewed and adjusted to meet any changes in the business.
5. Learn from experience Any mistakes, accidents or near-misses should be analysed and the policy and plan updated.
Risk Assessments
The Management of Health & Safety at Work Regulations 1999 require all employers to assess the risks to employees and others who may be affected by their work.
Objectives of the risk assessment are to identify the activity, who might potentially be harmed, and the hazard itself. Then evaluate the risk and decide on precautions, record and implement the findings of the assessment, and review and update the risk assessment regularly to take account of any changes on site.
While it might not be possible to produce task-specific risk assessments for every activity undertaken, areas associated with the highest levels of perceived risk should be prioritised.
The extent of the risk should also take account of all people exposed to the harm – employees, other workers, visitors, tenants or members of the public.
Risk assessments should be signed and dated once they have been reviewed, even if no changes are made, to demonstrate that they remain valid.
Training
Employers are required to provide information, instruction, training and supervision that meets the needs of the tasks undertaken by staff. It is also important to identify:
- Intervals where retraining is needed to maintain certification for a task
- When changes require a different way of working
- When people start work on the farm or are reassigned to another area of work.
Refresher intervals are frequently recommended rather than an absolute requirement, but they are also not uniform, says Mr Gazely.
He advises setting up a training matrix to record, track and identify staff training requirements.
Emergencies
Legally, businesses must provide first aid equipment and facilities that are adequate and appropriate according to the hazards involved. A competent person must be appointed to take charge of first-aid arrangements and to ensure the kit is maintained.
Deaths, specified injuries or over-seven-day injuries, occupational diseases, incidents or dangerous occurrences must all be reported under the Reporting of Injuries, Diseases and Dangerous Occurrences Regulations 2013.
Further details of reportable injuries and diseases are available at: hse.gov.uk/riddor
Staff must also know what to do in an emergency including the locations of first aid kits, fire extinguishers and alarms, exits and assembly points.
The emergency services should be provided with the OS map reference, postcode or WhatThreeWords app location of the premises, Mr Gazely advises.
Common accident areas
Transport
Accidents involving moving and overturning vehicles are the most common causes of serious and fatal injuries on Britain’s farms.
All too frequently these occur in yards or buildings where vehicles reverse into unseen pedestrians.
It sounds simple, but where possible operators should not use reverse in areas where people may be on foot, says Mr Gazely.
Often telehandlers, quadbikes and forklifts are involved in accidents when they are operated incorrectly. For example, overloaded telehandlers or forklifts, and quadbikes on steep terrain and with riders not wearing helmets, he says.
Legislation for transport issues come under the Workplace (Health, Safety and Welfare) Regulations 1992 and the Provision and Use of Work Equipment Regulations 1998 (Puwer). Basically these require that vehicles should:
- Move around safely to protect operators and pedestrians
- Be properly maintained
- Have appropriately trained operators.
Tragically, a staggering 30% of injuries involving vehicles could have been prevented if operators practised the Safe Stop procedure (see box). This ensures a vehicle is switched off and immobilised whenever the operator leaves the cab or controls.
Safe Stop procedure
The Farm Safety Partnership’s Safe Stop campaign promotes a procedure that all machinery operators should use before exiting their vehicle or leaving equipment. If followed rigorously, it is estimated the simple measure could cut farm deaths by almost a third.
- Engage handbrake
- Controls in neutral
- Switch off engine
- Remove key
Falls
Falls are the second biggest cause of death in agriculture and this area is covered by the Work at Height Regulations 2005. Employers must ensure work at height is properly planned, supervised and carried out by competent people.
Rules must be applied in this order, according to the HSE:
- Avoid working at height
- Ensure those working at height are trained and supervised
- Use safety equipment to prevent falls
- Use work equipment that minimises the distance and potential consequences of a fall.
Any task carried out above ground level is inherently dangerous and this is often overlooked, Mr Gazely says.
The combination of a farm being both workplace and home, alongside a “can-do-will-do” attitude, means it is often not seen as a place of industry. A blocked gutter on a building or a broken roof panel may be viewed as a minor task, and the farmer will fetch a ladder to fix it without even considering the risk involved.
Many falls occur in situations like this, where the incorrect equipment is used to scale heights, he adds.
Construction
Various aspects of work on farms are likely to come within the scope of the Construction (Design & Management) Regulations 2015.
These widen the scope of projects covered to include any construction, building or civil engineering work such as site preparation, assembly, demolition, repairs, alterations, conversions, fitting out and maintenance.
The requirements of the regulations vary according to whether the work is a single-contractor project, multi-contractor project or HSE-notifiable project, with duties being assigned to the client, designer, contractor, principal designer and principal contractor.
Equipment
The Puwer 1998 laws regulate all equipment and machinery including mills, slurry handling equipment and grain augers.
Accidents typically occur:
- During maintenance or unblocking while the equipment is running
- Because the equipment is unsuitable for the task
- As a result of missing safety guards on moving parts
- When staff have not been properly trained.
The regulations attempt to prevent these situations occurring by requiring that moving parts are guarded, while emergency stop controls must be working and obvious.
Staff must be trained to use the equipment and relevant information on its operation must be provided.
Any new machinery should, by law, be CE-marked and supplied with a certificate of conformity.
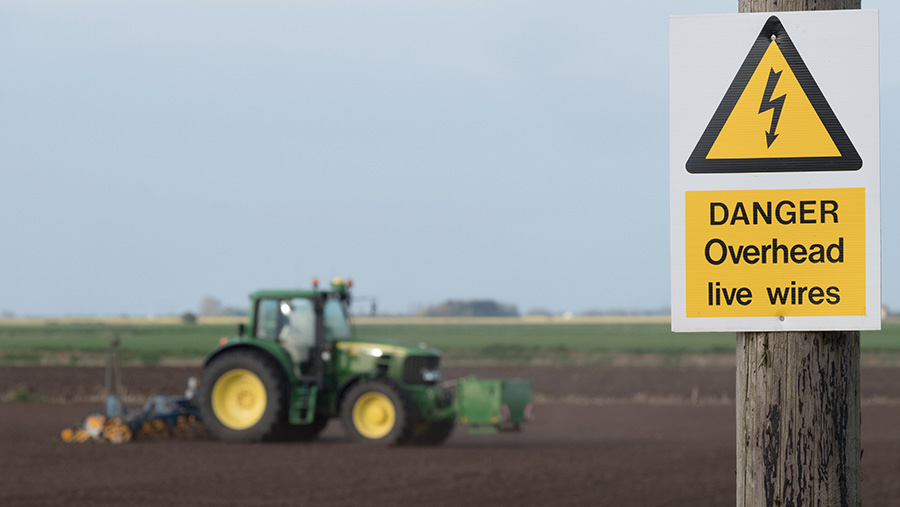
© Tim Scrivener
Electricity
Each year accidents involving electricity cause fatalities, serious injuries and fires. The HSE suggests that the number of serious accidents masks a huge number of near-misses with live electrical systems that could have proved fatal.
Typically workers and their vehicles come into contact with overhead power lines or are sufficiently close to the power source that the current jumps across the gap.
Aside from power line incidents, accidents include maintenance or repair work undertaken without first isolating the electrical supply.
Electrical supplies and equipment used on farms comes under the Electricity at Work Regulations 1989, which state that electrical equipment must be safe and properly maintained.
To reduce risks from electrical equipment:
- Always isolate the supply to equipment before maintenance or repairs
- Ensure electrical installations are carried out by a qualified electrician
- Use tested power cables and extensions.
Overhead power lines
Operations including unfolding and folding sprayer booms, unloading the combine and stacking bales should not be carried out within a horizontal distance of 10m of a power line because electricity can jump across gaps, Mr Gazely says.
Plan and mark safe routes and areas for high-risk operations or, ideally, have power lines buried or raised by the electricity supply company.
[in a circle]
In the event of contact with an overhead powerline operators should dial 105
Children
Every year children are killed on farms. Accidents occur because adults become complacent about risks, mistakenly believing that children have an innate sense of danger, or because children who live on farms appear unexpectedly in work areas.
Tragically, in most cases minor precautions and proper supervision of children could have prevented these deaths.
Farmers must comply with the Prevention of Accidents to Children in Agriculture Regulations 1998 (Pacar) and the Management of Health and Safety at Work Regulations 1999.
Risk assessments must also take full account of inexperience, immaturity and a lack of awareness of hazards in people under 18.
Under these rules it is illegal for under-13s to be a passenger in, or to drive, self-propelled machines including tractors.
Children under 16 must not drive, operate or help to operate:
- Towed or self-propelled harvesters and processing machine
- Trailers or feed equipment with conveyors or spreading mechanisms
- Power-driven machines
- Chemical applicators such as mounted, trailed or knapsack sprayers
- Handling equipment such as lift trucks, skid steer loaders or certain ATVs.
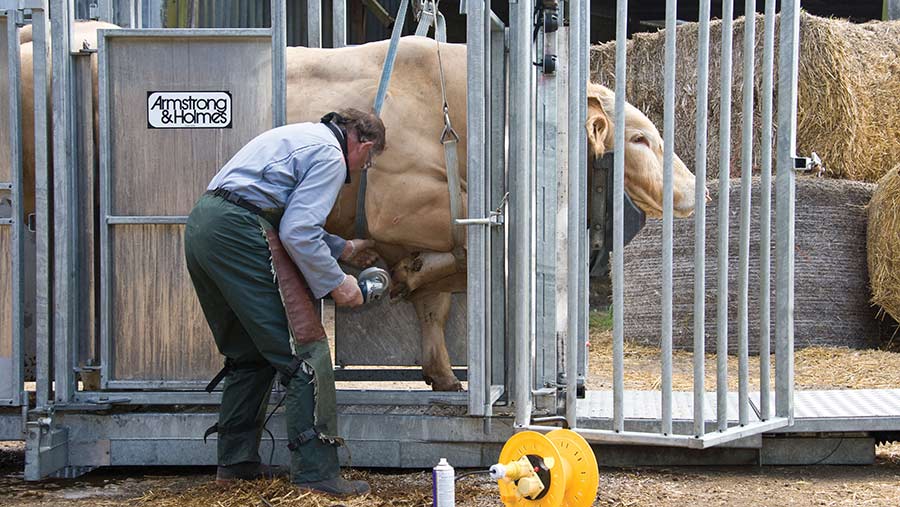
© Tim Scrivener
Livestock handling
Injuries and deaths involving livestock are caused by crushing, kicking, butting or goring. Often this happens when moving animals in confined spaces or treating cattle using makeshift equipment or without restraint.
Employers are duty bound under the Health and Safety at Work Act 1974 to reduce the risk of injury to themselves, their employees, visitors, vets and inspectors. Among others this requires:
- Appropriate and well-maintained handling systems for specific types of animal
- Trained, competent workers
- A rigorous culling policy for temperamental animals.
Costs
As well as the impact that an accident has on the victim’s loved ones and colleagues, the farm business’s future could be undermined by significant costs.
Mr Gazely says that for every £1 in insured costs relating to health and safety, there are £10 of uninsured costs that must be covered by the business. These include:
- Lost time
- Extra wages and overtime
- Sick pay
- Fines
- Legal costs
- Damage to product, plant, buildings, tools and equipment
- Site clearance
- Investigation time
- Excess on insurance claims
- Loss of business reputation
A recent change in the law means fines for health and safety transgressions are no longer capped by the courts.
Instead, where the farm business is proved to be at fault, fines are now linked to turnover.
The crucial word is turnover. Mr Gazely points out that many farms operate at modest profit levels but turnover may still be large. This means a business could easily be rendered insolvent if an accident occurs.
The farm may also face costs if it is subject to an HSE inspection.
These HSE visits may be entirely random or may be the result of a complaint or an accident.
If the inspector finds any material breach, a charge is levied on the business from that moment.
The current rate is £157/hour and this continues while the inspector conducts an investigation and writes up a report, Mr Gazely says.
Costs to the business can quickly run into thousands of pounds.
Instead Mr Gazely is an advocate of independent farm audits. These provide a fresh pair of eyes that are trained to spot a hazard which would otherwise be overlooked as part of the farm’s day-to-day routine, he says.