How to keep lone workers safe on farm
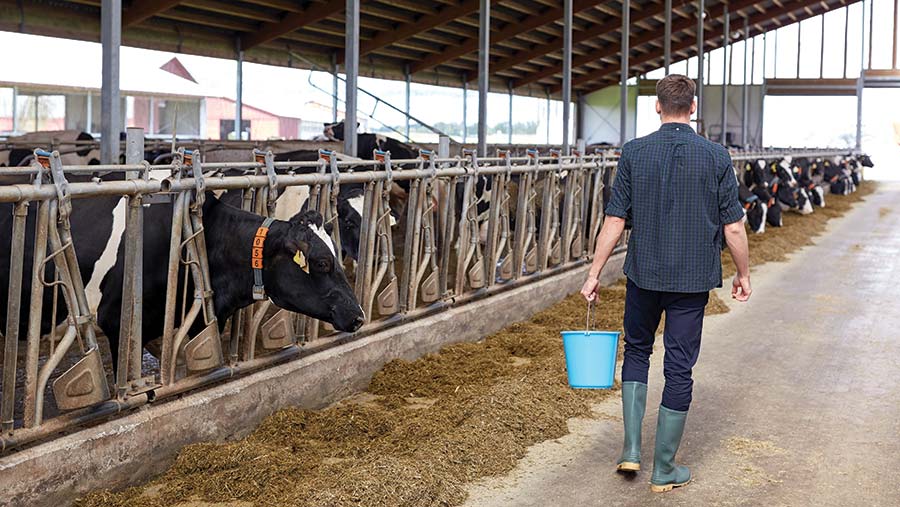
Working alone is taken for granted in farming, and while it is often necessary, a change of attitude could improve not only safety but also the working culture.
Oliver Dale, managing director of safety specialist Safety Revolution, says the most important advice is that farmers should avoid lone working whenever they can.
“This is often overlooked and quite often people’s immediate reaction is that they can’t do so because that is always the way they have done it.
“But if you ask them to think about it, they can often come up with ways of minimising lone working.”
See also: Health and safety policy: What farmers need to include
The law
Under the Management of Health and Safety at Work Regulations, farmers must manage the risk to lone workers by considering health and safety risks and then put in place reasonable measures to ensure tasks can be carried out safely.
This means providing training to ensure the lone worker is competent to perform the task and then deciding on the level of supervision or monitoring appropriate to the level of risk.
The Health and Safety Exexcutive’s (HSE) key questions for deciding on safe working arrangements are:
- Can the risks of the job be adequately controlled by one person?
- Is the person medically fit and suitable to work alone?
- What training is required to ensure the person is competent and can work safely?
- How will the person be supervised?
- What happens if a person becomes ill, is injured or there is an emergency?
- Who will be involved and which hazards could harm those working alone?
Assessing risk
A good-quality safety management system is the foundation for reducing lone working risks.
It is a legal requirement for farming businesses with five employees or more to have a written health and safety policy. Since 2022 it has also been a condition for all farms certified by Red Tractor.
The five employees include partners, directors and casual or part-time labour.
“Risk assessments, if they are to be any good to you, need to be tailored and adapted to the activities you are undertaking, rather than being so generic they could apply to any operation,” says Oliver.
“Your job as a manager is to identify what are the high risks – whether that is working with cows and calves, combining under overhead powerlines or students carting corn in the hours of darkness on a public highway – and really zone in to address these risks.”
However, a written policy does not need to be lengthy to be effective, so long as it is implemented properly, sits within an effective safety management system and is not regarded simply as a tick-box exercise.
“It needs to be really high quality and based on your activities, rather than a generic farmer’s activities.”
Provide training
Employers must ensure that every operative, whether employed or a family member, is trained to operate that equipment.
Where there is a statutory obligation to have a specific qualification – for example, for telehandler operation – that ticket must be in place.
Although there is no legal formal requirement for a tractor-driving licence, it is regarded as best practice for harvest labour to have one.
“The key thing is to make sure you have assessed people’s competence and that you are confident they are capable of doing that job, particularly if you are going to send them out alone,” says Oliver.
Supervision
Good communication systems, which make a point of having regular contact with people, can dramatically reduce the risks of lone working.
The amount of monitoring or supervision required should be based on the level of risk of the activity people are being asked to carry out.
If tractor driving is something someone does every day and they are competent operators, then checking in with them every four hours should be fine, says Oliver.
Similarly, if someone is going to feed livestock, and it is a routine activity for them which usually takes a couple of hours, then checking in with them after that time has elapsed would be appropriate.
For riskier lone working jobs, different arrangements might be needed.
For example, if someone is going to be dealing with an animal that is perceived to be difficult, they should avoid lone working, or at least ensure a co-worker is readily accessible to call on for help if needed.
Top tips for lone worker safety
- Risk assess lone working tasks
- Regular communication and monitoring is key
- Technology helps but should not be relied upon exclusively
- Consider using What3words or similar for precise location information, or a list of key grid references to help when calling emergency services
- Ensure staff know who to contact in an emergency
- List phone numbers in vehicles as well as on phones
Before starting any potentially hazardous job, workers should inform someone – a spouse, neighbour or relative – what they are going to do and how long they think it will take.
If they fail to confirm that the job has been completed after that time, then the other person can go to check up on them.
“It is often not the incident that kills people, it is the amount of time it takes before they get help,” says Oliver. “Time is of the essence.”
Technology can also be harnessed to make sure there is regular contact between staff and their supervisors.
Some farms use a WhatsApp group where employees are encouraged to post regular progress updates, which keeps everyone up to date with what is happening and where people are.
For this to be effective, there needs to be a culture of regular communication and monitoring so people don’t start jobs alone without telling anyone they are doing it, says Oliver.
“We want to avoid those stories of people getting hurt but the penny only dropping hours later when their partner goes out to have a look for them because they haven’t seen them for hours.”
Two-way radios can help but can be unreliable, says Oliver, who warns against using them on the move if they are hand-held.
Trackers can alert a manager to a machine’s activity, or lack of it, but old-school methods such as regular communication and checks are the cornerstone, he says.
What3words
Being able to pinpoint locations in the event of an accident is also crucial, says Jane Rheinheimer, policy adviser for the HSE.
She suggests downloading an app, such as What3words or similar, or having a list of key grid references that will help when calling the emergency services. In addition:
- Everyone should also be aware of first-aid arrangements – who to contact and where to find the first-aid kit
- Regular breaks – tiredness and fatigue will make anyone lone working more vulnerable
- Good machinery maintenance should also reduce the risk of problems occurring while people are out in the field
- Follow the “safe stop” routine when leaving the vehicle to carry out any adjustments or deal with a blockage – apply handbrake, put controls in neutral, switch off engine (or turn off power), and remove key.
Safety tips from FW Awards winners
Paul Temple, Wold Farm, East Yorkshire – Mixed Farmer of the Year 2021
“As an industry, we aren’t always very good at analysing levels of risk.
“A good way of getting workers more focused on this is to discuss how people perceive the risks associated with different tasks by assigning them a mark out of 10.
“For example, the risk factor for someone Cambridge rolling might be 1/10, but it might be 9/10 if walking around a field with a stock bull.
“Encouraging people to start thinking about levels of risk will help them to manage risk.
“I would also recommend having a smartphone policy that covers how they should be used in an emergency.
“There is now a whole generation of young people who rarely use their phone to speak to people.
“But if someone was to send me a message or text in an emergency, I would be unlikely to notice.
“Therefore, it is important to be clear as to the best methods of communication.”
Peter Eccles, Carlaverock Farm, East Lothian – Farm Manager of the Year 2020
“We have a chain of communication with everyone’s mobile numbers, which includes and goes out to the families and emergency contacts of staff, so that if someone doesn’t appear home at the expected time or arrive at work when they are supposed to, they know who to call in the first instance.
“Staff are also asked to send a text when they leave their place of work or finish up for the day.
“Protocols are in place for how to approach different tasks.”