Business Clinic: What kit checks should we be carrying out?
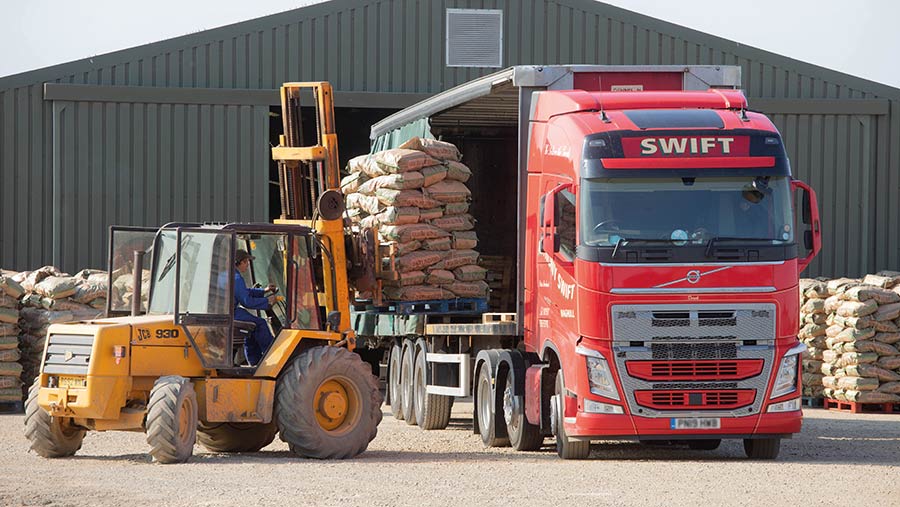
Whether you have a legal, tax, insurance, management or land issue, Farmers Weekly’s Business Clinic experts can help. Here, Will Oakes of A-Plan Rural Insurance, advises on how to ensure your equipment is well maintained and fully insured.
Q: Over the years our business has grown, and we’ve started doing some contracting and storage alongside the main 283ha arable farming operation.
Our range of kit has been expanded and a neighbour recently suggested that there are legal requirements to have certain checks done. What checks are these, how often should they be done and which bits of kit do they cover?
What are the potential implications, both from a legal perspective and in respect of my insurance if they are not carried out? Do you have any general advice about farm vehicle and machinery safety? For example, what are the most common types of claim, and how can we reduce the risk of these?
A: These are common questions when businesses grow or diversify. It’s important to inform your insurance broker when high-value equipment is purchased and when a business diversifies or pivots to include new services.
Even the simplest of changes can affect your exposure to risk.
See also: Business Clinic: how can we prepare for extreme weather?
Contracting
First, ensure your public liability insurance covers you for working on farms that do not belong to you, as cover for contracting is not always included as standard by all providers.
Inspections and breakdown cover
The Health and Safety Executive (HSE) website includes a list of what should be inspected and how often. The purpose of an inspection is to identify whether work equipment can be operated, adjusted and maintained safely.
It is critical to ensure that any deterioration is detected and remedied before it becomes a risk to those operating it, or a financial loss to the business.
Some of the typical machinery claims we see include:
- Breakdown and loss of revenue
- Theft
- Fire
- Injury (liability).
Whether your equipment requires inspection, and how often, is normally determined by legislation and what category of equipment it falls under (see “Equipment categories and regulations”).
Equipment categories and regulations |
|
Boiler/pressure systems |
Pressure System Safety Regulations 2000 |
Lifting equipment |
Lifting Operations and Lifting Equipment Regulations 1998 |
Electrical/mechanical – covers any equipment that is used in a workplace and could pose a risk to people’s health and safety |
Provision and Use of Work Equipment Regulations 1998 |
Local exhaust ventilation |
The Control of Substances Hazardous to Health Regulations 2002 |
Power presses and associated machinery |
Provision and Use of Work Equipment Regulations 1998 |
Fixed wiring (electrical) |
Electricity at Work Regulations 1989 |
The inspection itself can be undertaken by anyone who has enough knowledge and experience of the equipment to know what to look at. HSE defines a “competent person” as “someone who has the necessary skills, experience and knowledge to manage health and safety”.
However, you can also purchase inspection services from your insurer or broker for a reasonable annual cost.
Equipment should be inspected after purchase and before first use, and at suitable intervals after that. It is also important to recheck when modifications are made.
Failure to do so can leave you uninsured and in breach of government regulations. Moreover, if anyone is injured as a result of faulty or unsafe machinery there are also severe legal implications and a threat of litigation.
Is your equipment suitably insured?
It’s important to know for certain if kit is insured under your current policy, especially when new equipment is purchased, so always check.
Some motor policies, for instance, include cover for attachments automatically – others don’t. Could you afford to replace the kit if it was lost or broke down? Would your business suffer?
Other questions to ask include:
- Do your staff have training for using the kit?
- Does the farm have a risk assessment and plan that staff and employers can follow?