Downsizing and enterprise stacking makes Kent farm financially resilient
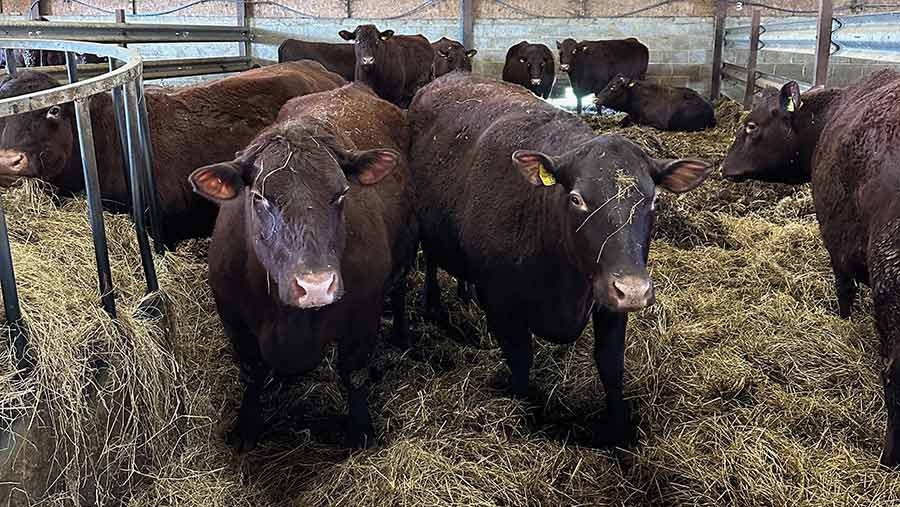
If ideas and enterprise stacking rather than scale and focus make a farming business resilient, then Doug Wanstall is onto a winner.
A business that at its largest was contract-farming 1,900ha of arable and selling eggs from 250,000 free-range chickens has evolved into a 360ha multi-enterprise business based on circular economy principles.
See also: How will price pressures affect fungicide decisions on farm?
A Nuffield scholarship investigating how to build financial resilience provided several “lightbulb moments” to embark on a radical downsizing and change in philosophy, Mr Wanstall says.
“I concluded in my report in 2016 that you can only become truly resilient if you remove as many external forces as you can, and that’s what we’ve done. We’re trying to be masters of our own destiny.”
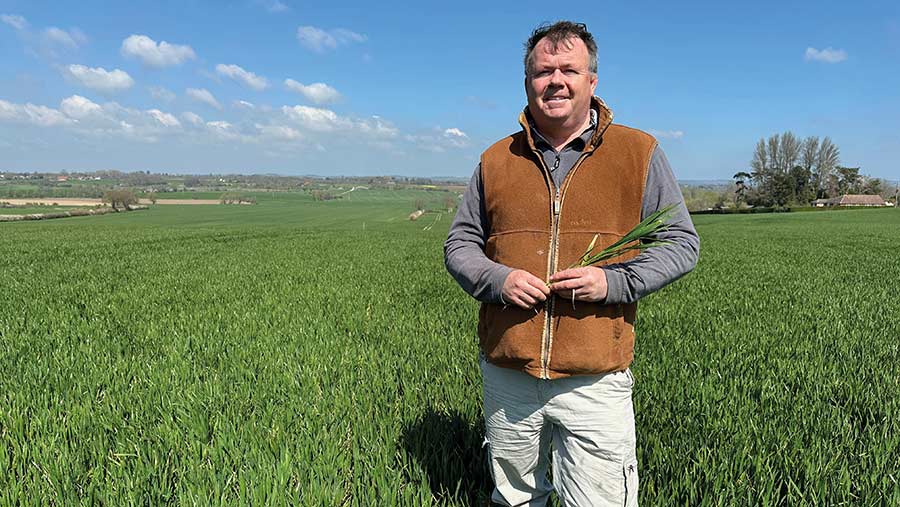
Doug Wanstall © Mike Abram
Vending machine
At the heart of the business lies a large vending machine selling mainly produce from the farm.
It’s not the first farm retail business Mr Wanstall has run. In 2002, he set up a local food hub selling the farm’s eggs and acting as an outlet for other local producers, which saw him crowned Farmers Weekly Local Food Farmer of the Year in 2008.
As the business grew, he responded to an initiative by Asda for local food hubs to supply local supermarkets.
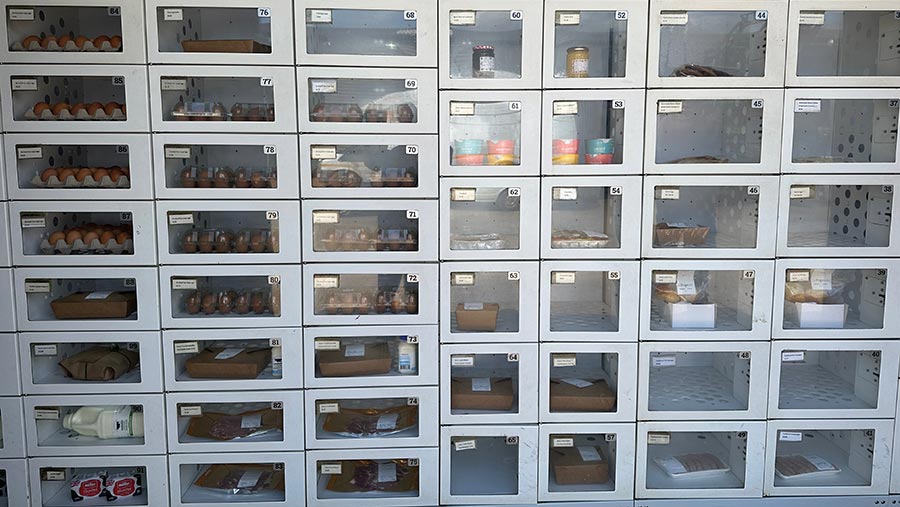
The vending machine makes about £600 a day © Mike Abram
“Unfortunately, that didn’t end well,” he says.
“There were promises about volumes, and we set up an infrastructure to deal with those volumes, but they never came through. In the end we stopped supplying overnight.”
This time the supermarkets are competitors rather than partners or customers.
All eggs from the much smaller flock of 2,500 chickens are now sold through the vending machine, which was bought in January 2019 for £26,000.
Unsurprisingly, the Covid lockdown helped put the machine on the map for the local community.
“Its best day took £3,200,” he says.
A bit like Jeremy Clarkson’s farm shop, customers were queuing out onto the road, and it became a bit of a problem, he admits.
Today the 24/7 machine takes about £600/day selling eggs, sausages and bacon made and cured on farm, dairy products, as well as fudge, jam, brownies and cream teas made by a wedding venue business run by Mr Wanstall’s wife, Stephanie.
It’s the farm’s engine room now, Mr Wanstall stresses. “We’re aiming to create more farm enterprises that we can sell through it.”
Vegetable enterprise
This includes his small-scale market garden, growing vegetables such as French beans, baby carrots, new potatoes, Romanesco cauliflower, squashes, parsnips and Brussels sprouts.
“We tell customers what’s in the machine on Facebook and Instagram.
“There’s this term supermarkets use – choice editing – where they effectively tell their customers what they’re going to buy. We do the same thing on a micro scale.”
While 500sq m might not seem worth bothering with, he says it produces about £70,000/ha. “Show me an arable crop that does that?”
Just across from the market garden underneath two old horse chestnut trees is a small area of composting woodchip, which has been seeded with wine cap mushrooms.
While the mushrooms are also sold via the vending machine, its real purpose is to create fungal colonies to go into his worm farms, along with well-rotted cow and poultry manure, biochar, woodland soil, leaves, grass, lucerne and insect frass.
The composted material will be used to create an extract and then applied in a rip-and-drip system with seed at drilling to stimulate soil biology, with potentially another couple of applications in the spring.
The worms will be harvested to multiply the system, and could help create starter packs for others to use in future, he says.
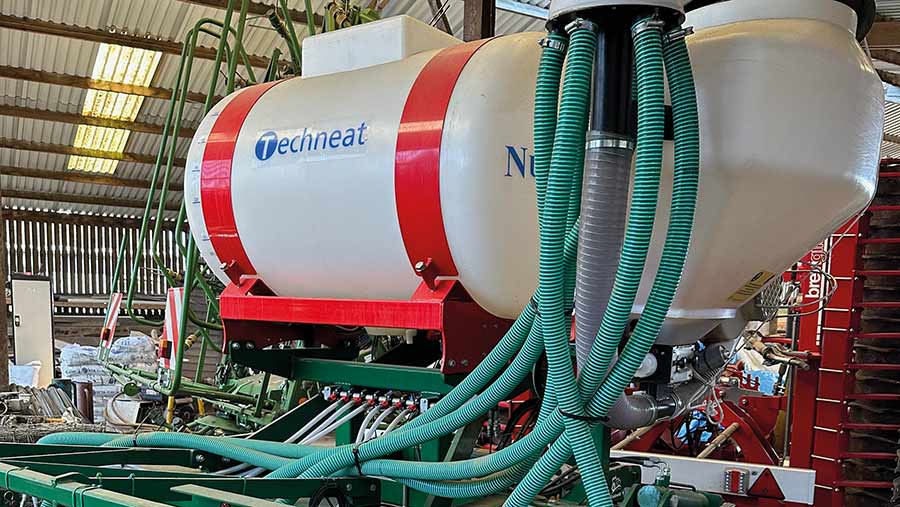
An extract is applied in a rip-and-drip system with seed at drilling to stimulate soil biology © Mike Abram
Reducing arable inputs
It’s just one of several projects on farm to either create alternative forms of fertiliser or improve soil biology to reduce the need for synthetic inputs – a key aim for his regenerative arable system.
“We’re predominantly trying to produce the same with a lot fewer resources. We’ve reached the stage where we are now applying less than one-third of the synthetic nitrogen we used to, for the same yields.”
Reaching milling specification with his blend of Crusoe, Extase and Zyatt has proven difficult, as has, so far, finding a local baker to work with him on producing artisan products to sell via the vending machine.
As a result, he’s moving away from aiming for milling spec, although he will trial whether using foliar urea at the milky ripe stage can boost the low-N regime by the 1-1.5% in grain protein required to meet spec this season.
Instead, his wheat will either feed his chickens, go to local feed wheat homes or be used to supply a distillery business on the farm.
As well as using wheat from the farm, the distillery sources other agricultural products, such as Jersey Royal potatoes, apples and berries, and turns waste products into a high-value spirit.
While alcohol won’t be sold in the vending machine, which is self-service, Mr Wanstall is considering a pop-up takeaway for another of his fledgling projects – selling chickenmeat, where there could also be an opportunity to sell the distillery’s output.
The farm is also home to 42 Sussex breeding cows and followers and some relatively rare-breed Oxford Sandy and Black pigs, which will be fed a combination of fruit and vegetable waste, and distillers’ and brewers’ grains.
“The aim is to have a continual programme of pork products we can sell through the vending machine or through pop-ups, all butchered on the farm.”
Agroforestry
On the other side of the farmyard is a 5.5ha agroforestry field, which forms part of a Growing Kent & Medway project, funded by UKRI, investigating the microbiological effect of regenerative agriculture.
“The field has been completely DNA-mapped by the University of Kent to give a soil microbiome baseline, with the plan to see how various interventions, including the use of biochar and different crop rotations, affect the microbiome.”
The biochar will be made from materials such as hedge-trimmings, tree prunings, grubbed-out orchards and manures using a retort, and then activated by mixing it with composts, insect frass and other products.
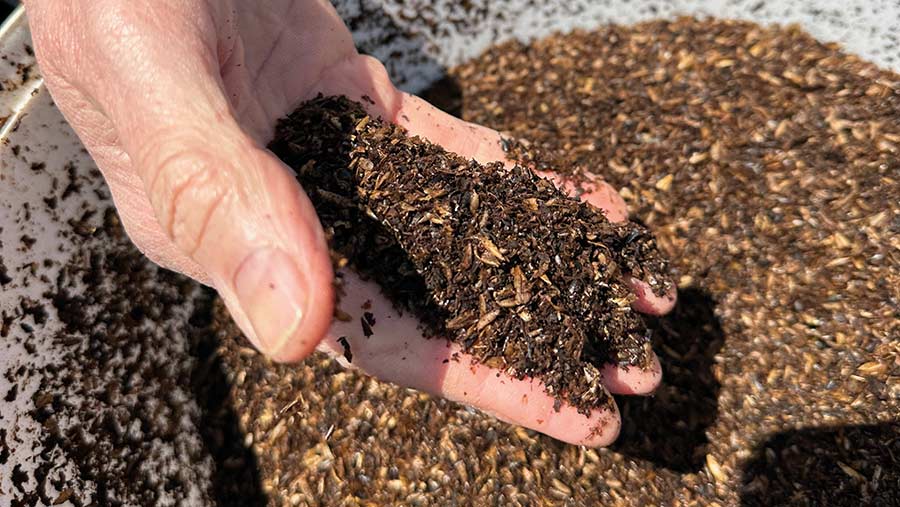
Frass is used as part of the biochar © Mike Abram
One tonne of activated biochar will effectively capture nearly 3t of carbon dioxide in the soil, Mr Wanstall says.
“It’s not only the physical act of adding the carbon, which is derived from carbon dioxide, but once in the ground it accelerates increases in soil organic matter.
“We’re interested in interventions that increase soil carbon sequestration so farmers end up with more fertile soils and can benefit from carbon credits.”
Carbon
Carbon is yet another of Mr Wanstall’s interests – alongside fellow farmer and co-founder Richard Bowe, he started Re-Generation Earth, which works with landowners to help them benefit from carbon offset and biodiversity net gain sales.
He’s also been instrumental in the development of the UK Carbon Code of Conduct – not to be confused with the UK Soil Carbon Code.
The code has established a set of standards to give buyers and sellers confidence that its carbon credits are robust and meet additionality, permanence and leakage criteria and avoid any other negative outcomes.
“Farmers are the secret to short-term, immediate carbon sequestration,” Mr Wanstall says.
“The quicker we can scale regenerative agriculture adoption, the sooner we can move the dial on climate change and change the agenda away from agriculture being seen as this nasty, polluting, emitting industry.”
Turning waste into valuable feed and fertiliser
Recycling farm and food waste into useable materials is a key part of the farm and ancillary businesses.
From composting farmyard manure from the cattle and chickens to worm farms and use of fruit and veg waste in the distillery, little is thrown away at Bank Farm, Doug Wanstall says.
“We’ve just set up a deal with Curious Brewery in Ashford to take their waste distillers’ and brewers’ grains and yeast to feed to the pigs and chickens, and then sell produce to them.”
That waste is also the feedstock for another UKRI-funded project with Inspro and the University of Kent.
Here, it is processed by black soldier fly larvae to produce an insect protein source for the chickens and a fertiliser, frass (the solid excreta of insects).
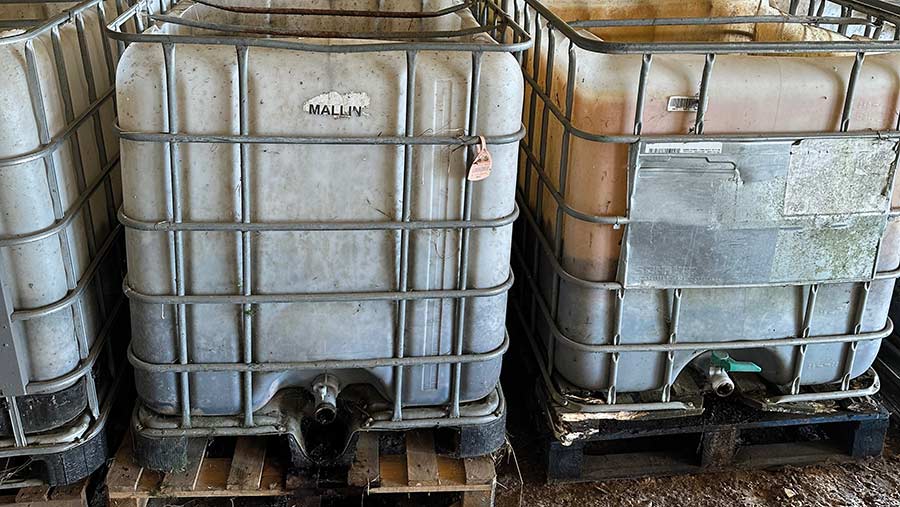
Mushrooms are used to create fungal colonies to go into the worm farm © Mike Abram
The process happens in a bioconversion unit on farm in two seven-day cycles, Richard Small, managing director of Inspro explains.
The first seven-day cycle hatches the black soldier fly eggs, with the second cycle growing the larvae as they eat through the waste substrate of brewers’ grains, waste veg and fruit, and yeast.
After 14 days the mix is sieved to get two outputs – the larvae, which are fed to chickens on the farm as an alternative source of protein, and frass, the digested substrate and insect casings, which can be used as a fertiliser source.
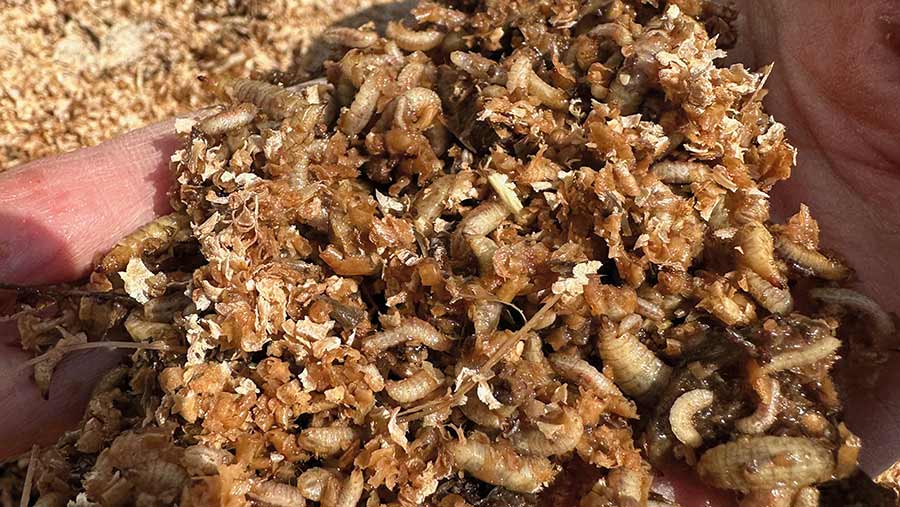
Black soldier fly larvae © Mike Abram
“With Kent University we are experimenting with what works well as a substrate,” Mr Small says. “We know a certain moisture and protein content is needed for the larvae to grow well.”
That’s more important for other markets, such as exotic pet food, where size matters, while microwaving them into meal worms for wild bird feed is another outlet.
Chicken feed
“We concentrate on feeding them to chickens. Our business plan is to develop dispersed hubs on farm, rather than a centralised factory which is not carbon efficient – we’re aiming for 12 hubs, with this being the first.”
For Mr Wanstall the benefit is a potentially low-carbon feed for the chickens, with the aim to produce a carbon-neutral egg, which will be certified by the UK Carbon Code.
The frass could be used as fertiliser on the farm, but more likely it will be sold externally as a high-value compost, after being composted with biochar and other substrates on farm.
Initial tests show for every tonne of substrate, about 100kg of frass is produced, with NPK values of 5:2:3, although that varies depending on initial substrate mix.