2 Sisters on building efficiency drive
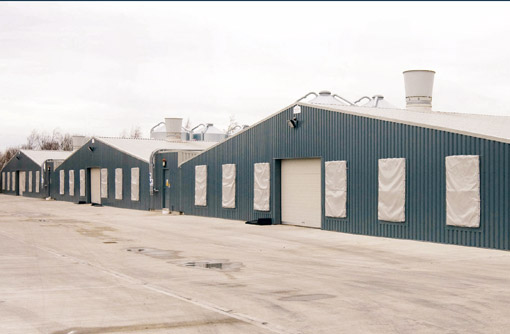
The 2 Sisters Food Group has embarked on a major investment programme, building new state-of-the-art poultry buildings closer to its factories. Rhian Price finds out more
Lowering carbon emissions is a valuable business strategy for any player within the poultry industry.
Having greener credentials can improve efficiency, which in turn can drive profits and elevate a company’s image in the marketplace.
See a video of Rob Rafferty talking about the building project
While becoming carbon neutral may seem a long way off for many producers, the 2 Sisters Food Group is pioneering new technologies and investing millions of pounds into new projects to transform its agricultural portfolio into a so-called green haven.
“What we are doing isn’t particularly ground-breaking; it’s really simple stuff,” explains Rob Rafferty, managing director of property. “Effectively we are just taking logical steps to create the most energy efficient farms.”
The move fits in with the government’s policy, announced in its budget four years ago, to make all new non-domestic buildings “zero carbon” by 2019.
“We are not waiting to be told by the government what to do. We have taken the lead in the industry to be energy efficient and lower our carbon footprint,” says Mr Rafferty.
The business has already started to replace old stock and to build new farms close to its factories. So far it has completed over 500,000sq ft of new buildings, with a further one million sq ft ready to move into the construction phase, while an additional two million sq ft of space is still in the planning phase.
The company is also aiming to generate 100% of the electricity it uses across its whole agricultural portfolio by the end of this year.
“We want the project to be as far-reaching as possible, so we decided to invest resources into as many of our farms as we could to make a real difference,” explains Mr Rafferty.
Building solutions
Ferry Farm, near Lincoln, is a testament to 2 Sister’s commitment to its new building project.
Comprising of six new sheds, which each house approximately 40,000 birds, it is just one of a number of farms in the company’s portfolio which boasts a lower carbon footprint through a succession of new and innovative technologies.
Each shed is built with energy efficiency in mind, from the foundations to the finishing touches.
Additional insulation in the roof and side walls provides a thermal conductivity of between 0.26 and 0.38 W/m2 – more than the recommended performance for poultry buildings.
“We are providing extra insulation to provide better U-values than the industry norm, which is great,” says Mr Rafferty. “For us it is a balance between cost and efficiency – creating the most efficient building while working within the cost constraints of the industry.”
Every effort is made to cut the energy bill at Ferry Farm, including solar panels (above) and sealed windows (below)
A new Big Dutchman heat exchanger (above and below) manages the heating, lighting and ventilation systems.
Optimising efficiency is a priority for each building designer and the team has made simple structural improvements to reduce heat loss.
“An example of this is that we have extended the insulated external wall to ground level covering the concrete dwarf wall, thereby adding an additional construction layer at a very vulnerable point of the building,” explains Mr Rafferty.
“The trouble with concrete is it loses heat, so by the simple step of adding an extra construction layer, thermal efficiency is improved.” The windows reflect this philosophy, too. Made from five layers of polycarbonate, they are designed to minimise heat loss and perform better than conventional glass. Smoke tests conducted after the building’s completion are able to uncover the tiniest of gaps – invisible to the human eye – where air can escape. Builders are then brought back in to seal the unwanted cracks prior to the house being stocked.
The provision of windows also minimises the amount of artificial light required, so saving electricity, while providing the birds with a natural light resource.
The new building utilises a mixture of tunnel ventilation and roof extraction to improve the flow of air, while reducing the overall power requirements.
“It all boils down to the quality of the building and we are constantly looking at ways to improve that.”
As one of many ongoing trials, the company is also looking at replacing concrete walls and steel lining sheets with recycled plastic components.
“We are currently conducting trials at a site with dense recycled plastic to ensure it’s hard enough to take the impact of machinery when we are cleaning out sheds after depletion,” explains Mr Rafferty.
If the trial is successful, the company will be rolling it out on a number of its farms, in an attempt to reduce costs and the impact on the environment.
“It is a brilliant material to use and, because the surface is clinical, it will make cleaning much easier.”
When it comes to equipping the sheds, the focus is also on efficiency. Thousands of broilers can be seen feeding from an automatic system, which reacts to sensors, so reducing wastage. Similarly, automatic sensors detect the presence of birds’ beaks at drinkers, which then release droplets of water in a hygienic, waste-free way.
The pressure put on man-power has been eased significantly through a fully-computerised Big Dutchman control system, which manages the heating, lighting and ventilation systems.
“At first managers were reluctant to use them and it has taken a while for them to get used to them. But we believe computer systems can significantly improve performance. They have in other industries, so it shouldn’t be any different for the poultry sector,” says Mr Rafferty.
Energy solutions
Solar PV
Visible only from a birds-eye view, solar panels are already in use at Ferry Farm – one of many of the 2 Sisters farms benefiting from the technology.
So far the company has installed solar panels on 32% of its portfolio, investing a total of ÂŁ1.5m into the project. The farms are using 99.7% of the electricity generated by the solar installations, saving the equivalent of 504t of carbon a year.
Wind power
As well as solar power, another way 2 Sisters is generating electricity is by using wind turbines.
The installation of a wind turbine at Baulker Farm, near Newark, is already well under way, while Ferry Farm is expected to get one this spring. A site for the 75m turbine is already mapped out.
Providing consent is granted for all 28 of its wind projects, the company has predicted it will help the company reduce carbon emissions by over 21,000t a year and generate 49m/kWh of electricity annually.
Heating
Another project which is still in the development stage, but promises to be one of the most exciting yet, is the company’s research into alternative heat sources.
After installing a heat exchanger at Ferry Farm last year, 2 Sisters has seen considerable benefits – most notably in the reduction of LPG (liquid propane gas) used to heat the units and from drier litter, which reduces the need for top-up bales by 41%.
The company is also investigating using three different types of heating solutions, including a high moisture burner, a dry wood pellet burner and a gasification system, which all aim to lower carbon emissions by replacing Kerosene and LPG.
All systems burn waste – either produced on or off-site – and all are proven to reduce humidity, helping to generate a better food conversion rate.
“The results from our investigations will determine which one we roll out to farms,” says Mr Rafferty.
Water recycling
Among the many projects taking place on 2 Sisters farms, there is one which isn’t carbon-related, and that is water recycling.
The first installation is expected to be fully-functional at Ferry Farm this month (March) and will recycle over 10,000cu m of water annually.
Once the project is up and running, water will be harvested off roofs and from an attenuation pound, before being collected and stored in an on-site treatment room, where it will be treated on demand to provide birds with potable water.