Earn and learn as an apprentice
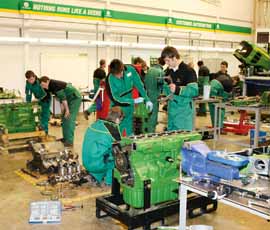
Tractors and farm machinery have changed beyond recognition in recent years, so the servicing industry has had to shift up a gear to keep pace. No longer can general mechanics fix all the farm’s machinery with an adjustable spanner and a screwdriver. Nowadays they virtually need a degree in computing, mechatronics, transmission systems, and, of course, a good old-fashioned understanding of engines.
So to keep up with the rapid rate of change, manufacturers and independent dealerships are providing tailored apprenticeship schemes to produce a workforce capable of meeting their increasingly technical requirements.
What is an apprenticeship?
Apprenticeships combine practical and theoretical training in colleges with a full-time job in a dealership. Not only do they provide youngsters with an income and free training, they should produce a dedicated workforce to meet the requirements of the industry. “However, until about 18 months ago the manufacturers were finding that, even after they were qualified, some apprentices were unable to read and write, and didn’t have the necessary skills,” says John Godden, industry partnership manager at Lantra. So in conjunction with the industry and colleges, Lantra revised agricultural engineering qualifications to better fit the needs of manufacturers.
What qualifications do you need?
Following a comprehensive overhaul, there are now two routes open for apprentices – those with a minimum of five GCSEs at grade C and above (or equivalent) can do an extended diploma – an option used by Claas, JCB and Case New Holland. The alternative route, which does not have such demanding entry levels, is the National Apprenticeship Framework, preferred by Agco and John Deere. Both offer the same course content, with additional modules for basic reading, writing and IT skills if needed.
The three or four-year part-time diplomas combine a mixture of practical and theoretical work, assessed by college or independent assessors both in the place of work and through evidence-based coursework.
What do you get paid?
Apprentices should expect to be paid a minimum of ÂŁ95 a week, but on average the industry pays ÂŁ170 net, as well as training fees (which can be government-funded), accommodation and meals while at college.
“Once qualified, a technician can earn ÂŁ25,000 to ÂŁ30,000 – and we get a lot of people moving in from the motor industry because it’s a lot more interesting,” says Mr Godden.
To obtain an apprenticeship, youngsters can either approach a dealership or manufacturer direct, or contact Connexions or Lantra. “The problem is that the careers advisers in school don’t understand our sector. If a young person is interested in agricultural engineering, enthusiastic and willing to learn, then we always have businesses who are willing to invest in them.
Most apprentices tend to come straight from school at 16-19 years of age, having perhaps done work experience to get a flavour of the industry. They are then likely to be enrolled in an apprentice programme and start college in the new academic year.
Case-New Holland
“It is up to the dealers how much experience fresh employees require – usually aptitude is more important than experience,” says James Fermor, training manager at Case New Holland, which enrols about 25-30 apprentices at Reaseheath College, Cheshire, every year.
“We provide Reaseheath with as much equipment as we can, but also provide on-the-job training and specialist top-up training at our factory in Basildon.” The in-house courses focus on brand-specific diagnostics, engines, transmissions, hydraulics and electrics, as well as new technology like GPS.
So while the college offers relatively general agricultural engineering training, CNH provides the more specific information required by its own technicians. “That way we can ensure our apprentices are fit for purpose and obtain the right skills for the future.
JCB
JCB takes a similar approach, using Reaseheath College for general training and its own headquarters at Rocester, Staffordshire, for specialist tuition. “We also encourage continued learning, and many of the apprentices go on to higher education and foundation degrees,” says human resources manager Ken Stepney.
Claas
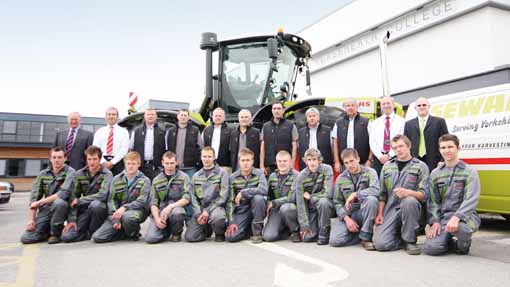
Claas is another Reaseheath patron, along with Barony College in Scotland. “We prefer the extended diploma because it recognises each candidate for their personal performance – instead of just pass or fail, they get a pass, merit or distinction,” says training manager John Palmer. “We usually take on 20-30 apprentices a year, and have spent a lot of time streamlining the college programme for the best outcome for our dealerships.”
The apprentices spend 36 weeks at the college over three years, split into four-week blocks – and in the fourth year they get additional training from Claas experts, either at the Bury St Edmunds training centre or within the college. “The college training is very broad and provides an excellent foundation, but we have to also bring in the brand elements that we want to see,” says Mr Palmer.
John Deere
John Deere decided to take its apprenticeship programme in-house in 2010, via private training provider Babcock. “Our Ag-Tech programme was the first in the UK – we started working with Brooksby College, Leicestershire, in 1992, and it was very successful,” says Peter Leech, training delivery manager at Deere & Co.
The students are now based at Babcock’s training centre in Ruddington, Nottinghamshire.
The first year of the part-time course covers basic engineering; health and safety, engines, hydraulics, electrics, brakes, steering and welding. Split into two-week blocks over eight weeks a year, the course becomes more brand-specific and technical in the second and third years, including JD diagnostic software, combines, Isobus and Cambus systems.
About 40 students complete the course each year, graduating with a diploma and a level two certificate in the Land-based Technician Accreditation (LTA) scheme, which benchmarks professional standards in the industry.
Agco
But what happens when such specialised engineers need to work on a different brand of machinery? Tony Linfield, training development manager at Agco, which encompasses Massey Ferguson, Fendt, Valtra and Challenger, prefers students to have expertise in a wide range of equipment to cover this very scenario.
“We work in partnership with Warwickshire College, and I like to encourage them to encompass other brands that may have different designs and techniques that technicians will find in the big wide world,” he says.
“The agriculture industry is very diverse, so there can be an incredible range of jobs coming into a dealer’s workshop.”