Searching for the best fertiliser spreader
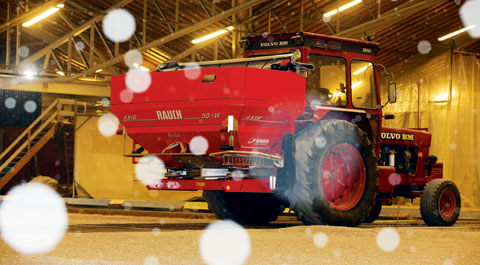
Wondering how good your fertiliser spreader really is? Emily Padfield joined European colleagues in Denmark to test the accuracy of some of the most advanced spreaders on the market
Click on the links below for more detail on each spreader:
Our last in-depth spreader test was nearly 15 years ago, when 24m working widths were becoming more commonplace. Now many spreaders cover a colossal 42m width and on-board weighing systems are becoming the norm. The weighing system constantly monitors the amount of fertiliser in the hopper and automatically adapts forward speed to the weight in the hopper.
It was clearly time to conduct a new test – one that looks at up-to-date spreaders equipped with weigh-cells and with a minimum working width of 36m. The norm in the UK may still be 24m, but it won’t be long until these wider working widths creep in.
Who took part?
The test involved four magazines – Boerderij in The Netherlands, Top Agrar in Germany, La France Agricole in France and Farmers Weekly in the UK. We asked all western European fertiliser manufacturers to participate. Amazone, Bogballe, Bredal, Rauch, Sulky and Vicon/Kverneland took the challenge. Tulip, who took over Lely spreader production in 2002, decided not to take part.
The spreaders were tested at Bygholm Research Centre, part of the University of Aarhus in northern Denmark. This is the only independent spreader test hall in Europe.
Even spread pattern
To ensure the test was done properly, it was conducted to the official European EN13739 test protocol. So each spreader was tested four times to flatten out any anomalies in the spreading performance figures.
The test was also designed to be a practical one, so each machine was adjusted purely using the instruction manual and spreading tables, as any farmer in the field would do.
Spreader adjustments were made by Boerderij staff, after which manufacturers monitored whether these adjustments were done correctly. However, manufacturers were not allowed to see any of the test results throughout the week.
Fertiliser
Supplied and produced by Yara from the Sluiskil plant in The Netherlands, the fertiliser was CAN – 27% N ±4% MgO. This is a standard Extran with a uniformly round shape, however transport and handling can cause some granules to be damaged. The fertiliser in the test was finer than usual.
Spreader manufacturers were not given a prior sample of the fertiliser used to avoid influencing the settings recommended in the spreading tables. Why? Because a farmer does not know the exact quality of the fertiliser he buys and uses only the spreading tables as a guide. Many manufacturers now offer websites with up-to-date spreader tables too.
Coefficient of variation
After each test, the coefficient of variation (CV) was established. This is the key indicator of accuracy and measures the range of widths of granules and shows how much a spreader’s average spread pattern differs from the ideal.
According to the EN protocol, a CV lower than 15% is acceptable and one below 10% is good. Anything between 15% and 30% is poor and although the farmer won’t be able to see a visible difference in the crop, yields will be affected. A CV of over 30% will result in striping and even crop damage.
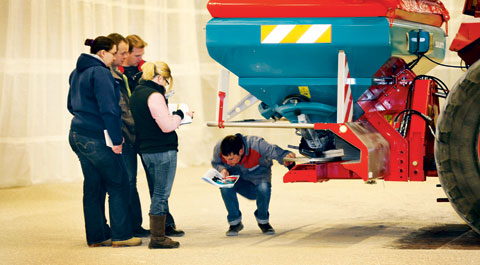
One spreader was tested each day and the test consisted of five steps. The accuracy of the weighing system wasn’t tested (see box: No weigh cell test).
1. Starting measurement
The spreader was adjusted according to the manual and manufacturer’s spreading table. The distribution of granules when the spreaders was stationary was measured based on the spreading table settings. Although weigh-cell spreaders automatically adjust the shutter opening width based on driving speed, weight and rate/ha settings, manufacturers advise the operator to put specific settings into the computer to take account of factors like flow characteristics.
At the same hopper setting, finer fertiliser granules flow faster than coarse ones. You need to compensate for this in the first few metres if the spreader is to achieve the correct application rate, as when spreading starts no weight measurement has been established. Adjusting the hopper according to the recommended settings means the rate/ha is accurate enough to commence spreading.
Because the Yara fertiliser was finer than usual, the actual amount spread was higher than the advised 260kg/ha for the Amazone, Rauch and Sulky spreaders at the start of the run. However this had no negative effect on the spread pattern.
2. Field measurement
In the field test, the spreader’s own computer was left to adjust the hopper opening, resulting in an application rate approaching 260kg/ha at a forward speed of 8km/hour. The spreader computer does this automatically as soon as the operator starts spreading. Each field test involved four runs.
In an ideal world the spread pattern would be accurate enough without having to run a tray test. In practice, most growers don’t perform one regularly due to the amount of work involved and complexity.
3. Getting the best spread pattern
Manufacturer’s manuals give operators the chance to adjust the spread pattern based on the results of the tray test. This involves putting between four and 14 trays (depending on the make) in the field to collect the granules. Once the tray contents have been weighed, the instruction manual consulted and, possibly, the dealer rung up, the operator can check whether the spread pattern is good enough and if not, how to improve it.
According to the EN standard used in our test, each manufacturer had two attempts to correct the spreader pattern, using the instructions in the manual.
4. Border spreading
We also adjusted the spreader for border spreading using the instruction manual. We worked to the EU regulations on this; they stipulate that only 0.3% of fertiliser can cross the boundary. In addition, the spreading value (CT) needed to be below 25%.
5. Optimising border spreading
In their manuals, Amazone, Bogballe, Bredal, Sulky and Vicon indicate how to adjust the spreader both for full-width spreading and border spreading. Rauch doesn’t have a protocol in its manual for adjusting border spreading.
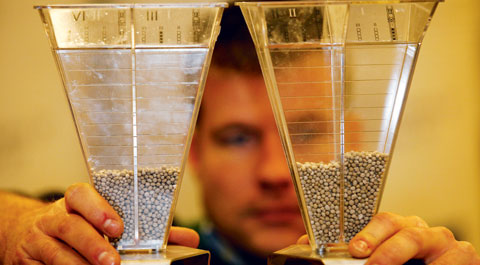
All spreaders achieved a CV below 15%. In the field, the difference between the measured CVs seemed big, but in practice it was slim. However, the machines’ performances fell into the acceptable, good and very good categories, and all spreaders tested provided a good spread pattern.
After spreading, we used the instruction manual to work out whether a better spreading pattern was possible.
For Bogballe, Vicon and Rauch the initial tray test meant there was no need to adjust the spreader, as the deviation was already within the guidelines.
For Amazone, Sulky and Bredal the test showed there was little improvement after adjustment. Readjusting the Sulky spreader didn’t result in a better spread pattern and after two attempts the spreader was set to the original settings. The instructions in the manual turned out to be wrong and the manufacturer has now changed this.
Eventually, all spreaders scored a CV of below 10%, which is very good. Border spreading wasn’t a problem for any manufacturer. No spreader broke the 0.3% rule and all have a border spreading value (CT) of under 25%.
Conclusion? There is no real winner in this test as the differences were too small, particularly if the grower takes time to perform a tray test regularly.