Follow the biomass route to lower farm heating costs
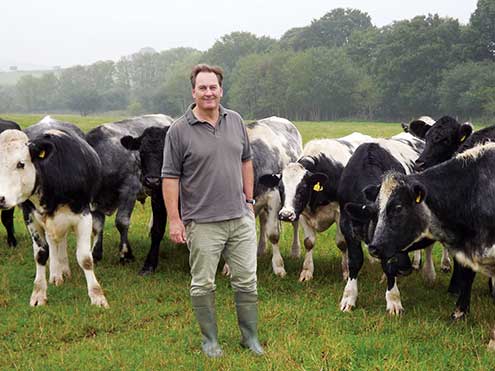
Gordon Traill (pictured above) is a third-generation tenant farmer on the National Trust’s Killerton Estate in Devon.
In 2005 grain prices were so low that Mr Traill bought a biomass boiler to burn Yarde Farm’s grain because it was more cost effective than burning heating oil. The grain burning system reliably heated the farmhouse, saving Mr Traill up to 50% compared with the cost of oil.
Shortly after this investment he established a diversification business called Treco to import and install biomass boilers to burn grain or wood pellets as fuel.
Following the introduction of the Renewable Heat Incentive (RHI) in 2011, it made financial sense to replace the original biomass boiler, the new one being fuelled with woodchip, which reduced costs still further. This system also heats other buildings on the farm, including offices, workshops and a pie factory.
The new system qualifies for an £11,000-plus annual RHI income and now saves about 80% on fuel costs compared with oil. This means the capital costs will be paid back in about four years, says Mr Traill.
His switch to biomass heat and his diversification into supplying and installing biomass boilers have accompanied large-scale changes in the farm business.
In 2004, when the first biomass boiler was being considered, Yarde Farm had 70ha of flood-prone grazing, 40ha of maize and cereals, 180 dairy cows managed as a flying herd and calves reared for beef.
By 2009 the introduction of Nitrate Vulnerable Zones was imminent and the farm had insufficient slurry storage for the dairy herd.
In response, a switch from intensive to extensive farming was planned and a successful application was made to enter a Higher Level Stewardship scheme. Milk production ceased in August 2010 and was replaced by extensive beef production.
The current farming business generates relatively low levels of profit, says Mr Traill. “However, the farming system meets the requirements of the various stakeholders, including the National Trust, DEFRA (NVZs) and the public. Income from Treco has more than replaced the reduction in income from farming.”
His experience of installing and running farm heating systems has led to him learning several lessons. These include:
- Design the system carefully and think about whether other commercial or domestic buildings could be heated
- Think about total system cost and beware boiler-only prices
- Design the system with RHI’s eligibility requirements in mind
- Think about fuel options and storage early in the project – getting the practical aspect of this right is very important
- Ask your supplier to help with your RHI application
- Be aware of deadlines and the fact incentives will reduce in the future
“Above all, be sure to buy good quality fuel from a quality-assured supplier,” says Mr Traill.
Yarde Farm biomass – an overview |
---|
|