How even heavy machinery can ease soil compaction
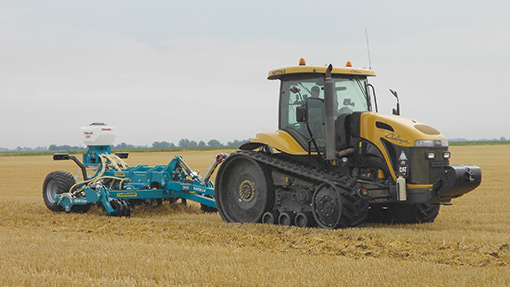
Tyres, tracks, tines and tramlines. Those are the principle tools available to growers keen to tackle the conundrum of how to maintain favourable soil structures as field machinery gets bigger and heavier.
It’s certainly one that needs to be tackled, says Prof Dick Godwin, who highlights a Cranfield University report for Defra that estimates the national cost of soil degradation at £0.9-£1.2bn/year, with compaction accounting for 40% of that figure.
Compaction is expensive in terms of the energy expended putting it right by soil-engaging implements, he points out, while its negative impact on water infiltration after rainfall adversely affects field work schedules and timeliness, and can cause soil erosion through water run-off.
The use of tracks, large tyres and appropriate inflation pressure management can reduce the impact of machinery on soils and the cost of putting right the damage it causes. And crop establishment techniques requiring fewer fields passes clearly have a role to play.
But ultimately, the ideal solution is to organise field traffic in a way that leaves as much as possible of the cropped area unsullied by wheelings.
Trials compare traffic and tillage
The Soil & Water Management Centre at Harper Adams University has set up a long-term trial to investigate the effect of farm traffic and tillage on crop yields, soil structure and energy requirements.
The trial, funded by the Douglas Bomford Trust and the university with the support of industry contacts, is based on plots where three traffic systems – random, low ground pressure and controlled traffic – are being compared along with deep tillage, shallow tillage and zero tillage.
Appropriate traffic control and tillage systems that reduce soil degradation and increase efficiency are essential for future sustainability in crop production, believes research leader Prof Dick Godwin. “The trial is designed to gather data that will help inform farmers about they can better manage their soils.”
The Soil & Water Management Centre was established by Harper Adams University in conjunction with industry partners Agrii, Basis, Agco Challenger, The Co-op Farms, GrowHow, Interagro, Michelin, NRM, and Väderstad, with support from The Rothschild Foundation.
Tyres and tracks
Tractor tyres have never had it so bad – they are expected to cope with heavier loads and faster speeds while still providing excellent traction and good ride comfort.
Little wonder, then, that tyre manufacturers have had to pull out all the stops to find ways of meeting such demanding expectations – and to combat competition from tracks for harvester applications and the highest powered tractors.
They have certainly risen to the challenge: tractors that once had to run on tyres inflated to 1.6 bar (23psi) to support a load of just over 3,300kg and sustain a 50kph road speed can now do so at half that pressure with a corresponding reduction in the vehicle’s impact on the soil.
“Carcass construction and dimensions are the key elements here,” notes Gordon Brookes of Michelin. “This defines a level of deflection or ‘squashiness’ under load from a carcass structure that can still carry a lot of weight.”
Michelin applied Ultraflex technology adapted from run-flat car tyres to create the first tyre classified “VF” some 10 years ago and only now is the XeoBib facing competition; first examples of the Bridgestone VF-Tractor design should be available this autumn.
While the XeoBib caters for 80-220hp tractors with tyre sizes up to VF 710/60 R 42, there is a greater choice of tyres classified “increased flexion” (IF) for bigger, heavier and more powerful units.
At the top end of this category, manufacturers are also pushing the boundaries in terms of tyre height to increase air volume and create as long a footprint as possible.
While the mainstream tyres with IF classification go to 42in rims, the biggest fit 46in rims and go to nominal widths of up to 900mm to cater for the latest generation of 400hp-plus tractors. So far, they have appeared in the Trelleborg TM1000 High Power and Michelin AxioBib ranges – an AxioBib IF 900/65 R46 stands 2.32m tall so the tractor really has to be designed around the tyre if it is to fit.
Exploiting the potential of any farm tyre requires some commitment on the part of users to actively manage ballast and inflation pressures. Removing the 2-3t of ballast needed for heavy cultivations and dropping tyre pressure accordingly will ensure the tractor treads as delicately as possible for less demanding work.
Tine designs
The prospect of cultivating a field to different depths is a measure of the attention being given to ways of improving the efficiency of soil restructuring for root development and drainage.
“After variable-rate fertiliser and seeding, increasing the precision of deep soil cultivations is a logical step,” comments Richard Scholes of implement firm Cultivating Solutions. “Low disturbance soil loosening legs cut fuel costs compared with regular designs and this will be further improved by only working as deep as necessary.”
The company is trialling a variable depth control system for its RapidLift soil loosening implement carried on the tractor linkage or a Väderstad Rapid drill, and for the same low disturbance tines on the Titan Power Drive cultivator, which has a powered rear packer roller to reduce the size and weight of tractor needed to pull it.
The NG system from JJ Metcalfe & Son has been adopted by tillage equipment maker Plowman Agriculture for its Omni-Til cultivator and Omni-Lift subsoiler. Replaceable shin fittings and wings available in different widths adapt the leg to different soil types and working depths.
“Soil around the point is not compressed to the sides or underneath, while the steep angle of the tungsten carbide tile gives powerful shattering in hard, dry conditions,” explains Mike Metcalfe.
At Simba Great Plains, David Holmes emphasises that soil restructuring no longer occurs if the tine is worked beyond the critical depth of soil conditions on the day.
“Beyond the critical depth, soil is compressed instead of lifted,” he points out. “To avoid wasting time and energy, growers planning deep soil working need to establish how deep they need to go and check that the tine can do its job.
“Every year you can see unresolved compaction where soil loosening has not been effective,” Mr Holmes adds. “Take a spade and look at the soil structure both before and after the tines have passed through.”
Controlled traffic farming
Development of more accurate and consistent vehicle guidance systems; wider cultivators and seeders; and wider cutting tables and longer grain augers for combines have made controlled traffic farming (CTF) a realistic means of minimising compaction across the growing area.
It’s not easy piecing together a controlled traffic system to get tractors and other farm vehicles sharing temporary wheelings and permanent tramlines that fall in the same place year after year. But the area of soil “trafficked” can be cut from 80% to as little as 20% in a cereals rotation.
“Controlled traffic farming turns our present production systems on their head – by leaving 80-90% of fields permanently without compaction, rather than the other way around,” says CTF champion Tim Chamen.
Field trials and practical experience comparing controlled and random trafficking show that relieving soils of wheelings stress can recover yield losses of more than 6% in wheat and 20% in barley. Potato yield losses attributable to wheelings can as much as 20%.
Confining wheelings compaction to defined locations so that soils restructure beneficially over time reduces power requirement for cultivations and drilling, raising the prospect of stalling the trend towards, bigger, heavier and more powerful tractors.
Work at Thurlow Estate Farms
Cleaning out ditches and culverts, and replacing damaged or silted pipe drains, should have a helpful impact on timeliness of cultivations, drilling and crop protection treatments across 4,700ha of arable crops grown by Thurlow Estate Farms.
“The fundamentals have to be right,” says Andrew Crossley, farms director. “You can spend a lot of time analysing the best cultivations or drilling approach but if your drainage isn’t up to scratch no system is going to work at its best.”
Ploughing has dropped from about 60% to nearer 30% with a move to more economical cultivations, and any ploughing that is carried out is done out of the furrow to minimise compaction. Subsoiling has become a routine rotational operation in areas identified as having a problem.
Tractor choice also plays a part: the estate runs six modern tracklayers – three Case IH Quadtracs and three John Deere 8RTs – and wheeled tractors hauling triple-axle chaser bins at harvest run on generous tyres and are confined to the tramlines as much as possible.
A more thorough controlled traffic regime is in the pipeline but the estate already subscribes to RTK Farming’s network to keep tramlines in one place year on year and at exactly 40m.
Drainage performance is also under scrutiny to optimise field mobility and help return the infrastructure to good shape. It mostly involves replacement drains for sections of damaged or blocked clay and plastic pipe systems laid 20-30 years ago.
With water seeping in through the better-structured soil and from long-buried pipe drain outlets now exposed, the ditches have an important role to play in regulating the water table and keeping the land workable.