Minimising stress during piglet vaccinations
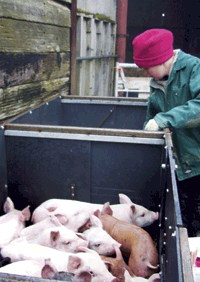
Injecting 1000 piglets in one day is back breaking-work but, for the Fawley Farms business, which has 10 breeding units spread out between Oxfordshire and Devon, the process was made even more challenging following a change in vaccination policy.
Previously they had been injecting for enzootic pneumonia at four-to-five days old, says Justin Willoughby, manager of New Manor Farm’s 750 sow unit, Wiltshire. “Although this was easy, vaccine cover was dwindling at the end of the pig’s life.”
Consequently, Fawley Farms decided to move the vaccine 21 days on, to prevent pneumonia flaring up in the growing sheds.
The farms were then faced with the challenge of vaccinating for pneumonia and wasting disease on the same day at weaning.
The question was, how could this be done at a practical level? says Fawley Farm’s technical manager, Duncan Stanford.
“Previously, because we had only been administering one vaccine, every piglet was picked up and jabbed. However, if you consider the fact each piglet weighs about seven kilos, you are essentially shifting 7t of pig in one day or 14 tonnes/day if you move to jabbing twice.”
We used to use a stock trailer to vaccinate, with one person holding a board and moving up and down the trailer and two people jabbing, says Mr Willoughby.
“The whole process was extremely stressful for piglets. They were continually trying to escape and consequently we had a few casualties from over-heating.”
In response, Mr Stanford began designing a vaccinating box for piglets with the view of minimising piglet handling to reduce both piglet and staff stress.
“The new vaccinating box is made up of a ramp that goes up to two partitioned boxes. Piglets are unloaded from the trailer and move up into the first box in batches of 18.
“The first handler injects this batch with the first vaccine and then opens a sliding door to move this group into the next box to be vaccinated for a second time.” Because the boxes are at waist height, staff do not have to bend down to reach piglets.
The new system may not be any quicker, but the whole process is a lot less stressful for all involved, says Mr Willoughby. “I no longer finish the day with a bad back and the experience is a lot safer.”
Because one of the vaccines is oil-based, it is essential the vaccination procedure is as safe as possible. “When we were picking up piglets and injecting, there was more room for mistakes.
“Before we were also injecting in the ham on the back leg, which is not ideal considering this is one of the most useful bits of meat on the pig,” he explains. However, because pigs are not being picked up, they can now be jabbed in the neck.
The whole process is also better for the piglets. “Previously we were vaccinating piglets as they went into the shed using the trailer, now because we have the vaccinating box in the shed, we move the piglets inside the day before. They then have 24 hours to ‘chill out’ before we vaccinate them.”
The system has been modified several times to improve the process and make specific designs to suit individual farms, says Mr Stanford. “To start with I tried to get the piglets to follow each other in single file, but they simply wouldn’t go in. Now I have designed a 2ft wide box so animals can move in groups,” explains Mr Stanford.
The box is made out of steel and stockboard so it can be easily washed and disinfected when needed.
Each farm has their own requirements depending on their set up, so some of the boxes are static where as others are on wheels. But whatever the set up, most of the farms agree the new system is an improvement.
“The key is to make life as easy as possible for the staff.” And at a cost of £330-400, it is well worth the investment.”