Potato growers warned over sensible CIPC use
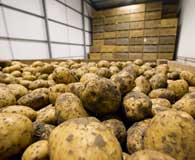
One of a potato grower’s most important tools, the sprout suppressant CIPC, could be withdrawn, dealing a hefty blow to the potato industry.
CIPC (chlorpropham) is vital to the potato industry, with no viable alternative to control sprouting in stored potatoes currently registered.
Residues of CIPC above the maximum residue levels (MRL) have continued to be detected in potatoes coming out of store and industry experts warn growers need to do more to reduce these levels and so safeguard CIPC’s future.
The Potato Council is currently waiting for a report from the Advisory Committee on Pesticides (ACP) which will dictate the future of CIPC.
Potato Council technologist Adrian Briddon admits there is a reliance on CIPC, but he does not know how the report will fully unfold.
“We won’t know the practical outcomes until the ACP reports, so our interim recommendation is not to commit any major investment. However, that’s not to say there aren’t things growers can do in the meantime,” he says.
“There is a reasonable chance that the report will require people to make some investments eventually, and in the long term it will be beneficial to growers,” he adds.
One thing that has been implemented as a result of the stewardship scheme is that no more than 36g/t of CIPC can be applied during a season to potatoes destined for the fresh market. The maximum dose for processed potatoes, including those used for peeling, is 63.75g/t.
Head of Sutton Bridge crop storage research Adrian Cunnington believes structural and management changes will be key.
“If best practice is not followed, in terms of both store management and application, the MRL can be exceeded and this is unacceptable,” he warns.
Mr Cunnington says positive ventilation gives the most uniform use of CIPC in trials and while this isn’t a viable option for many growers, there is still a need to change how potatoes are stored in order to lower the risk of residual problems.
With overhead throw systems being some of the most common storage systems, Mr Cunnington says even relatively simple measures such as an “air divider” curtain will significantly increase the efficiency of air use and CIPC distribution.
“In a season like this, drying crops as quickly as possible, preserving quality and discouraging sprouting will be a big help,” he says.
Meanwhile, Mr Briddon highlights that applying CIPC to achieve a predictable even residue is technically fairly easy.
“We have got a system for bulk stores and that does not present any major issues,” he says.
“The difficulty we have in the UK is the majority of our box stores are of the overhead throw design that does not have positive ventilation, making it difficult to get an even distribution of CIPC,” Mr Briddon adds.
“Some situations are more difficult than others. For processing in particular it is difficult to see how we are going to adopt change without significant investment.”
Mr Briddon says he knows where upper limits have been exceeded and considers box stores and low temperature stores to be at a relatively high risk of poor CIPC distribution.
“The bottom line is we know how to apply CIPC predictably and reliably – we just need to get our storage stock up to date,” he says.
Alternatives
Mr Briddon says that although a fairly significant amount of investment will be needed, there are also options on the horizon that may ease worries of any possible restrictions on CIPC.
“Ethylene is a possible option that can be used with modest amounts of CIPC and indeed we can use spearmint oil on them. However, this has only been tried in pre-packed stores”, he adds.
Mr Briddon feels dimethylnapthalene (DMN) is one of the most promising alternatives, as is SmartBlock, but they may be a few years away.
Mr Briddon admits it will be a waiting game to see whether they can get the right range of compounds that will suit UK requirements and relieve the pressure on CIPC.
CIPC best practice |
---|
|
Seven checks to avoid CIPC residues in your spuds