Yield is king when cutting wheat costs
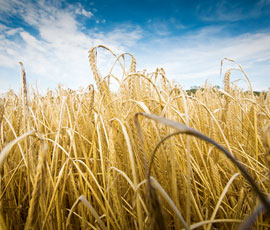
UK growers face some of the highest production costs in the world and finding ways to reduce them isn’t always easy. Here, Will Gemmill, head of farming at Strutt & Parker, gives an expert view on how to get a better handle on costs across the main cropping enterprises – cereals, oilseed rape and root crops.
The cost of crop production should, by definition, be the sum of variable costs (seeds, fertilisers, sprays), fixed costs (labour, power, depreciation, property and administration) and rent and finance divided by the yield. This gives you a cost of production per tonne.
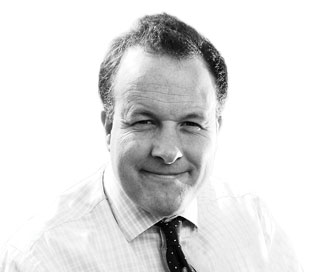
However, there can be significant variability in rent and finance depending on whether the farmer is an owner-occupier or tenant and the cost of borrowed capital.
In order to give more meaningful figures it is probably sensible to use a standard benchmarking figure for rent and finance which, if we average Strutt & Parker data, works out as £100/ha.
The major variability in cost of production per tonne comes from actual yields, and there is significant variance between the top 25% and bottom 25% yield performers.
There is also considerable seasonal variability. Therefore, a five-year rolling average of a particular crop yield is needed for a truer understanding of the trends in cost of production and how they relate to sale prices.
Most farmers have pretty accurate figures for variable costs between different crops, particularly with the computerised field recording systems.
It is often much harder to accurately allocate fixed costs – particularly labour and power – between crops. Greater variability comes where an arable farmer is growing a significant amount of root crops or is an arable/livestock producer which can further complicate the allocation of fixed costs to the different crops.
Strutt & Parker benchmarks yields and costs; trend lines show that many cereal and pulse yields have remained static, while oilseed rape and sugar beet have seen general increases in yield.
Not surprisingly, cost of production per tonne in cereals continues to rise year on year, particularly with increases in fertiliser and fuel prices.
Focusing on wheat, a typical cost of production per tonne for last year’s harvest was £120. This breaks down as shown in the graph.
If you take the typical DEFRA eastern regional five-year average yield of 7.8t/ha, then the cost of production goes up to £131/t. The variances in cost of production per tonne can be significant based on yield alone.
Looking at the Strutt & Parker top 25% (10.57t/ha) and bottom 25% (6.61t/ha) wheat yielding farms for 2011, where there were significant yield variations due to drought on lighter land, the cost of production varies from £95/t to £160/t.
In practice, on some of these higher yielding farms where there are owner/occupiers running with labour and power costs below the £300/ha, the cost of production can be as little as £75/t.
However, where a farmer is renting on a Farm Business Tenancy and has inherently high fixed costs coupled with a low yield, perhaps due to drought, the cost of production could be up to nearly £200/t.
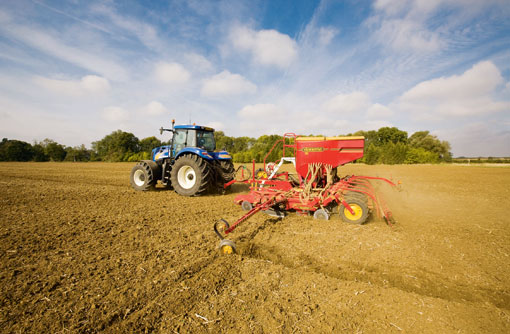
Looking at 2012, we know that variable costs are up significantly due to higher fertiliser prices and increased spend on fungicides and herbicides, particularly for blackgrass control.
Although fuel prices have dropped slightly on last year, it is likely that overall costs will be up by somewhere between £50/ha and £100/ha. The five-year average yield for Strutt & Parker in East Anglia and Kent – 8.95t/ha – puts the total cost production alone up by £3/t. However, using the DEFRA eastern regional average yield, the cost of production is up £141/t.
Looking forward to 2013, we see seed costs continuing to rise in line with commodity prices.
Nitrogen fertiliser prices are slightly down on 2012, but pesticides are predicted to rise by 5%. Fixed costs are set to increase by around 5%, so if yields remain static we can probably expect the average cost to go up by £6/t.
As this can vary significantly depending on rent reviews, outcomes look set to increase at a much higher percentage. One consolation is that the Single Payment and Entry Level Stewardship schemes are not built in to the cost of production per tonne, so you could argue they are an added bonus.
So what can farmers do to get low-cost production per tonne? First and foremost, they must ensure yield potential is optimised. With yield the most significant factor for cost of production per tonne, inputs, particularly good establishment, must be tailored to push yield potential.
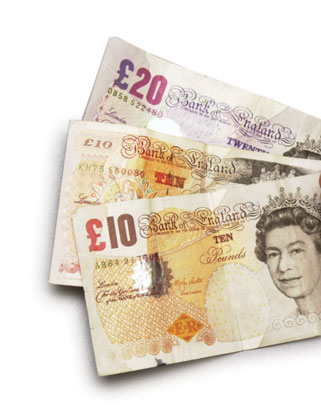
Ignoring the variability of rent and finance, the next most important factors are the variances of labour, power and depreciation. Where farmers can achieve economies of scale – either by reducing the number of cultivation passes or by utilising the best possible labour resources – healthy savings can be made.
Looking to contract or short-term hire, rather than ownership, may reduce machinery costs. Fuel efficiency, too, is key as fuel prices continue to rise.
Do not underestimate the importance of buying the right brand – a good-quality machine with high brand value will depreciate at a much slower rate than a cheaper alternative.
The fundamentals – soil structure and drainage through properly maintained ditches – are vitally important, yet often overlooked. Clear drainage outfalls and appropriate mole ploughing are key to good establishment and rooting and timeliness of operations.
Do you agree with the costs and have any other suggestions on reducing production costs? Share your thoughts on our Cutting Costs forum