VIDEO: Make the most of good spraying conditions
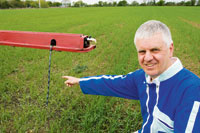
Reduced water volume, low-drift nozzles and increased speed are some of the simple measures operators can take to speed up T2 fungicide applications and increase the number of spray days, says Syngenta application specialist Tom Robinson.
Dropping from 200 to 100 litres/ha means a larger area can be treated with each fill, reducing the number of fill-ups needed a day, he says. “It means you can spray an additional 34ha a day (see table, below) which, at a contracting rate of ÂŁ10/ha, adds up to a saving of ÂŁ340 a day.”
There is no drop in efficacy from using 100 litres/ha and it is the optimum water volume for most Syngenta fungicides, he notes.
Choosing a low-drift nozzle allows faster operating speeds and opens up more opportunities, as operators can spray safely at higher wind speeds. Nozzle choice can also improve efficacy by depositing more product on the target.
See Tom Robinson in action
“A three-star LERAP nozzle has 75% less drift than a 110-03 fan-jet, which means it is less drifty in a Force 3 wind than the fan-jet is in a Force 2 wind,” says Mr Robinson. “If you can spray at Force 3 rather than Force 2, it gives you four more spraying days in May and June.”
Applying T2 fungicides a week late can mean a yield penalty of 0.5t/ha, or about ÂŁ5000 on a 100ha plot with a crop worth ÂŁ100/t, he says. So using nozzles that perform at faster forward speeds can increase work rates and reduce the likelihood of late fungicide application. Nozzles that are angled backwards allow faster forward speeds, he says. “Our 16kph Amistar nozzle is angled at 13° to counteract the forward speed.”
![]() |
---|
Correct nozzle choice allows safe spraying in higher winds and at faster forward speeds. |
This increase from 12kph to 16kph gives an extra load per day (see table, opposite), which means a saving of ÂŁ300 a day, he notes.
Switching to co-formulated products and using modern packaging is another measure that can significantly cut the time taken to fill the sprayer, he says.
A Syngenta survey carried out earlier this season showed one-third of growers were not using co-formulated products.
“Co-formulated mixes mean fewer cans are used, there is less mixing, sprayer turnaround is faster and they are good value for money,” he stresses.
Cutting down the number of cans needed to fill the sprayer means there is less time spent pouring product into the sprayer and washing out empty cans, he says. “Using cans without foil seals can save yet more time and make the filling process safer by reducing the chance of a spillage.”
Trials with a 1800-litre tank showed formulated products could save 10 minutes a load over the alternative mix and not having to deal with foil seals saved a further five minutes. This means operators can squeeze an additional load into their working day, he notes.
Using a bowser to ferry product to and from the sprayer considerably speeds up filling and can make economic sense for some operators, he says. “It takes roughly 11 minutes to fill the sprayer with a bowser in the field opposed to 19 minutes in the yard.” It also removes the travelling time from the field to the yard, he notes. Using bigger pack sizes improves filling efficiency.
A good-quality washer nozzle in the intake hopper can slash the time taken to wash out cans. “If they have multiple jets that also target the neck of the container washing is faster and more complete.”
Good filling technique can save time and improve the quality of the mix, he says. “If the sprayer is too full when the chemical is added the chemical doesn’t mix and if it is too empty the product starts to foam.”
Best practice is to fill a third of the tank with water, add the chemical and rinse the containers with the re-circulating spray mix. The circulated chemical removes deposited chemical more effectively than water alone, he says. The remaining water should then be added and packs rinsed with clean water before being left to drain.
A well-managed filling site is crucial for safe product handling, but also offers considerable time saving, he concludes.
Sprayer work rate comparison
Tank size (litres) | 3000 | 3000 | 3000 | 3000 | 3000 |
Speed km/h | 12 | 12 | 16 | 12 | 16 |
Boom width (m) | 24 | 24 | 24 | 30 | 24 |
Water volume (litres/ha) | 200 | 100 | 100 | 100 | 100 |
Area covered per load (ha) | 15 | 30 | 30 | 30 | 30 |
Time to spray 1ha (mins) | 2.1 | 2.1 | 1.6 | 1.7 | 1.6 |
Spray time per load (mins) | 31.3 | 62.5 | 46.9 | 50.0 | 46.9 |
Filling time (mins) | 30 | 40 | 40 | 40 | 25 |
Travel time (mins) | 10 | 10 | 10 | 10 | 10 |
Time per load (mins) | 71.3 | 112.5 | 96.9 | 100.0 | 81.9 |
Actual work rate (ha/hr) | 12.6 | 16 | 18.6 | 18 | 22 |
Ha sprayed per 10hr day | 126 | 160 | 186 | 180 | 220 |