The best guidance on controlled traffic farming
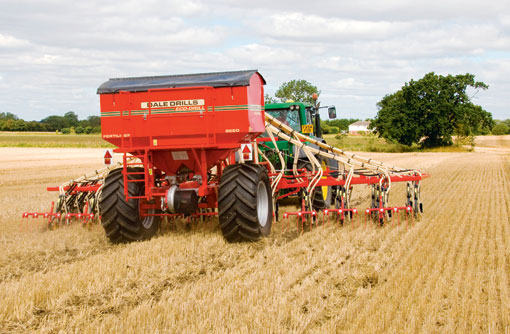
The time is definitely right for guidance, but is it also right for, perhaps, the logical next step: controlled traffic farming?
Many larger arable farms have already invested in a guidance system in some form, whether it is a cheaper light bar control or the more expensive autosteer system.
The advantages of doing so are well chronicled: more accurate driving results in fewer overlaps when using pesticides and fertiliser, less fuel use and fewer headaches for the operator, who can remain alert for longer, and cover more ground in a day.
Importantly, it also pays for itself. For example, trials carried out when James Evans was farm manager at Lowley’s Farm, Great Leighs, Essex in 2009 in conjunction with Strutt and Parker using John Deere’s Greenstar SF2 system found fuel use was cut by 10% per annum and reduced the time spent on field operations by 11%.
The greatest savings were found during combining and cultivations, with payback for the system used in the trial only taking three seasons. Its success is leading to a greater interest in controlled traffic farming. The technique confines all machinery to the smallest possible area of permanent traffic lanes.
Guidance systems make that possible, but only if the positioning is repeatable each time you come to the field.
The best pass-to-pass systems, such as the John Deere one used by Mr Evans, only guarantee repeatability for 15 minutes maximum.
For repeatability over a longer period, a real time kinematic (RTK) system is needed, which can guide the operator to the same spot each time to an accuracy of +/- 2cm.
By using permanent traffic lanes, depending on the system, the percentage area of a field trafficked in a season can be cut to below 30%. In some min-tillage systems, the proportion of the field area trafficked randomly can be as much as 127%, but typically it’s closer to 85%, says Tim Chamen, owner and founder of the UK arm of Controlled Traffic Farming Europe.
Avoiding that unnecessary traffic across a field will help to reduce compaction, he says.
“When you run over soils, you squash a lot of the air out of it, and reduce the pore sizes. That has a lot of implications – if we reduce the pore sizes, there is less air and space for roots to breathe, and you can get reduced rooting.
“The knock-on effect probably means that crops won’t take up all the nutrients you put on in some years, and some of that could be lost through diffuse pollution or to the atmosphere as nitrous oxide.
“Obviously we want crops to root as well as they can to get good crop production and use nutrients as efficiently as it can.”
Reducing pore size also has implications for drainage and how accessible water is to plants, he says. Larger pores are needed for drainage, while the smaller the pores in soils, the tighter water is held. That can be helpful in maintaining soil moisture. “But there comes a point, when it is so tightly held that plants cannot get hold of it or it becomes difficult for it to move into the soil, and causes run-off, erosion or water-logging.”
Research from around the world has shown that crops grown on soil that has not been travelled upon yield better.
Grass forage and oilseed rape are particularly responsive with yield responses of over 25% in some experiments, while wheat, for which there are more comparisons, produces 8% more yield where not compacted with wheelings.
Compacted soil is also more difficult to work.
“The more soils are run on, the stronger they get – you can measure that. At 4in deep, trafficked soils need 60% extra pull, and 20% more at 8in deep,” Mr Chamen says.
That helps explain the results on Lowley’s Farm – the more energy required for tillage, the more fuel and time it takes to create a seed-bed. “And compaction creates clods, which you need to break down to get a seed-bed,” says Mr Chamen.
The trend towards heavier machinery is only exacerbating the situation, he says.
“The big danger is sub-soil compaction. These machines are getting so heavy that sub-soils are getting gradually compromised and you can’t afford to repair them at half a metre deep.”
But it can be avoided, he says. “Compaction doesn’t happen in soils naturally.
“A lot of the energy, time and effort we’re putting in to getting crops established and growing is addressing problems we are creating with random traffic. Using controlled traffic is a way of using clever technology to avoid that problem.”
Of course, putting a controlled traffic farming system into practice isn’t that straightforward. It requires excellent management, which begins with the initial planning.
Having a very accurate steering system doesn’t mean you can necessarily implement a controlled traffic system, points out Clive Blacker, director of precision farming firm, Precision Decisions.
“There is investment you will have to make in your farming system to get it working properly.
“Think about the ultimate working widths you want to get to and your machinery replacement policy, because if you want to go to a 12m controlled traffic system, and your combine header width is 11.5m, then that isn’t going to work.
“You need to think about your whole system, and have an idea at the start where you want to be at the end of it. It is very easy to have one component of the system, which prevents you from achieving your goals.”
The likelihood is that the system will feature reduced tillage, Mr Chamen says.
“Otherwise you’re not going to see all the benefits. The chances are that subsoiling will become very infrequent once you have got into it.
It shouldn’t be necessary, other than in these very targeted areas.
“You’ve also got to analyse what is going to work, what is going to fall apart.
“For example, with straw management, is your combine going to spread it evenly, or will you need a rake to spread it that won’t fit in with the traffic lanes?
“You’ve got to take a pragmatic approach that if you have a problem, you have to deal with it.”
Drill performance in a reduced tillage system also needs to be considered, he says.
“You’re going to be dealing with more residue on the surface, so is your drill going to perform?”
The first step to designing the system is to draw up an inventory of the machinery that would be used. This involves measuring the width of each machine and the wheel track gauge of the wheeled equipment, and gives an idea of the compatibility of the different elements of the system, and identifies what modifications would be necessary or worth considering.
The aim is to match all the working widths of the equipment in unit widths. Ideally the combine’s cutting width will form the base unit width, although it is possible to have a module width less than the width of the cutting table in the short term, Mr Chamen says. “For example, a 9m cutting table could operate with an 8m unit width of drill and cultivators.”
But for most growers, combining at less than full capacity is to be avoided, so a machinery replacement plan to match everything on a multiple of the unit base width would be an urgent priority.
You also need to consider whether the grain auger is long enough to get the grain into the trailers, and how they are going to fit into the system, Mr Blacker says.
The next decision relates to the maximum overall acceptable width of the main tractors to be used. In Australia and USA, growers tend to match the wheel track widths up to that of the combine.
But in the UK and Europe having all tractors over 3m wide is not a practical option, not least because any vehicle with a width wider than 3m requires special dispensation from the local police force to use public roads.
“It means we have to be clever in the way we implement the system,” says Mr Chamen.
The most common system being used in the UK is known as “OutTrac” because the harvester tracks outside the main tractor wheelings. “Everything is centred, and you try to get as much overlap between the two tracks as possible.”
An alternative is “TwinTrac”. The harvester puts in the main tracks, and then everything else straddles adjacent passes of the harvester.
“It just works. The implement width is the addition of the two track widths, so, if the combine is 3m and the tractors 1.8m, you would have a 4.8m wide cultivator and drill. It is not that common a width, but there are drills out there, and it fits into a 24m tramline.”
The limitation is you cannot get bigger than the addition of the two track widths, he says. “So about 6m is the limit.”
Another system being used commercially is “AdTrac”, which adds an extra track for the narrower vehicle, but still using the same implement widths. “It means you have two different track centres, which might provide a challenge for your AB lines, but it is doable.”
To help identify how much area is currently tracked with that equipment, and to test different scenarios, CTF Europe members have access to a calculator that uses implement, track gauge and tyre widths, along with % overlap, to calculate the tracked area for different systems.
Once a plan for the system has been formed, it is probably worth introducing the system on a trial basis in one or two fields. Ideally, any major soil problems will have been rectified before embarking on a CTF system, Mr Chamen says.
“The best entry is in a year following a dry season when the maximum amount of repair has been possible.” Testing the system will help provide confidence that it will work, and, most importantly, yields will not be affected, he says.
“We all know ploughing is a reliable, if expensive, operation – we have to have equal confidence in a CTF system. We cannot afford to have any loss of yield or lack of reliability in establishing crops.”
- Lower energy for cultivation – soils not squashed by wheels lifts more easily. On average, 50% saving in fuel/tonne of crop harvested
- Lower energy for driving over soil – wheels run on compact traffic lanes minimising rolling resistance
- Lower machinery investment – shallower, less intensive and less energy demanding tillage operations means smaller tractors and machines can be used
- Better seed-beds – with no compaction damage, less cloddy seed-beds can be produced with little loss of moisture
- Improved crop yields – research suggests yields on average from non-trafficked soils are 9-16% higher
- Improved soil structure – helps with water infiltration and availability, but also reduces erosion and water-logging
- Improved field efficiency – less overlap with inputs and machinery, and opportunity to cut seed rates and slug pellet use
Source: CTF Europe
Managing cropped wheelings is one of the areas where more research and practical experience is needed. “It is up for grabs,” Mr Chamen admits.Growers on CTF systems are managing them in very different ways, from deep cultivations to leaving them alone.
It makes sense to make the first pass in dry conditions, if possible, and preferably not on soil that has just been deep loosened or ploughed.
If wheelings become rutted after the first few passes, it could be necessary to “sweep” soil into the wheelings from as great a width as possible, using discs or a shallow pass with a rotary harrow, he suggests.
But understanding how to manage those wheelings for best gain in the longer term will be crucial to maximising output from the system, he says.
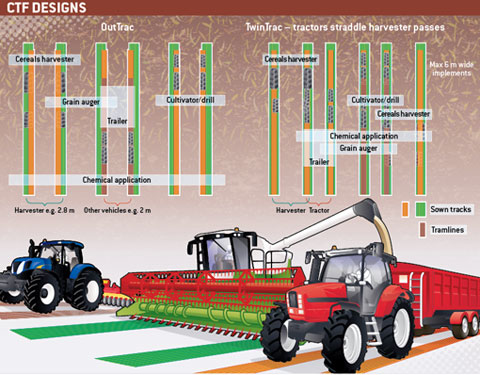
Andrew Ward, Leadenham
Andrew Ward is already part of the way towards a controlled traffic system, after investing in RTK guidance in 2009.
With a firm grip on his costs, Mr Ward recognised moving to an autosteer system could help improve work rates, fuel use and reduce establishment costs and his overall cost of production.
He chose the Trimble RTK system to run on a new Quadtrac 535, rather than a cheaper guidance system as he has a policy to invest in the best system. “I wanted to do everything as accurately as possible, and to be able to drill without markers.”
While he hasn’t been able to measure fuel savings directly as the Quadtrac 535 was replacing his previous Quadtrac STX450, he is confident it has made a significant difference, as he is using less fuel/hectare than with the previous machine. He has also noticed a difference in work rate, and the ease of working at night, as well as less operator fatigue.
But he was aware using the system on just the Quadtrac was not fully utilising its potential, so he has bought a new Trimble FMX750 box and EZ steer units to fit to three machines – combine, John Deere 200hp tractor and the Fastrac tractor used for fertiliser spreading.
But he is unsure of whether the next step of implementing a controlled traffic system is economically justifiable.
Financial return
To help, Crops asked Mr Chamen to put Mr Ward’s operation details and costs through one of his calculators to give some guidance on what return on investment (RoI) a controlled traffic farming system could bring.
Using Mr Ward’s costs for machinery, pesticides, seed, fertiliser and fuel, the Excel spreadsheet was able to calculate machinery and total system costs for the current random traffic RTK system, and what they would be for the same system without guidance.
That required some assumptions to be made on the overlaps for various operations with and without guidance, and the knock-on effect for productivity.
In Mr Ward’s system overlaps were assumed to be reduced by 1-4%, depending on operation, by switching to guidance.
The results showed, using the information inputted, that moving to RTK guidance saved around ÂŁ5/ha in operating costs, or nearly ÂŁ7,500 across the farm in a year.
With an investment of around ÂŁ28,000 for all the RTK kit used that translates to a 9.5% annual return on investment, or ÂŁ4.80/ha.
However, Mr Ward has reduced some of his initial investment by collaborating with four neighbours to share his base station signal.
That has a marked impact on the annual return on investment, doubling it in percentage terms.
Mr Chamen then turned his attention to two possible controlled traffic systems, the first (CTF 1) is switching to a no-till system, except for oilseed rape which incorporates deep loosening directly in front of sowing, while the second system (CTF 2) is a no-till system for all crops. Both systems were based on a 100% combinable crop rotation and 20% of each field being tracked, but neither considered sugar beet in the rotation.
Fewer passes
The spreadsheet primarily accounts for the return on investment associated with a reduction in overlap from guidance, so where no yield increase is attributed to the CTF system, the return on investment in guidance remains broadly similar to that of a RTK system as a controlled traffic system will require fewer passes.
But if a net 5.7% yield benefit is attributed to CTF – 8% higher yield on non-trafficked parts of the field and a 5% loss in yield in cropped traffic lanes – then CTF system shows a huge return on investment of over £70/ha.
The calculations do not represent an accurate assessment of the change in profitability of whole farm systems, Mr Chamen stresses. “For example, it doesn’t take into account any changes in machinery that could be made. Mr Ward currently uses a 600hp Quadtrac to pull a 6m cultivator.
“If he switched to a CTF no-till system, you could probably slash that power investment to maybe a 250hp tractor pulling an 8m drill.”
And while Mr Ward would have to make machinery changes to implement a CTF system, such as investing in a new drill, and a new sprayer to fit either a 9 or 12m base unit width, the net cost of converting to CTF should always be neutral or negative, Mr Chamen reckons.