Switching from floor to bin drying system reduced costs
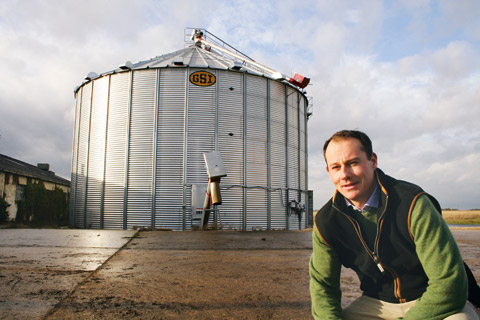
Faced with tight storage capacity and poor on-floor drying performance, an arable unit on the Lincolnshire fens turned to in-bin drying and storage as a solution. Peter Hill reports
It looks like a missile bunker, according to one local wag. But the shiny silo erected in time for this year’s harvest at Dovecote Farm near Boston, Lincolnshire, has a more prosaic role – providing additional grain storage capacity and more cost-efficient drying.
“We’d expanded to the point where our on-floor drying and storage sheds could barely cope,” explains James Pocklington, who farms the 810ha enterprise with his father.
“It all came to a head in 2010 when we really struggled in the wet conditions,” he adds. “The combine didn’t turn a wheel for two weeks while we tried to dry grain coming in at up to 20% moisture; that was the push we needed to improve the system.”
The business has a share of capacity at the Lingrain co-operative and there is storage available 10 miles away on a separate 344ha unit farmed in conjunction with Dovecote.
But added acreage and increased yields meant further capacity, as well as an improvement in drying efficiency, were needed on the home farm, where the focus of attention was firmly on tackling the shortcomings of the 30-year-old bulk stores.
Storage capacity has been pushed to the limits by piling 3,000t of grain into the three sheds, each divided by a central tunnel to push air through the drive-over ventilated floor. Piling grain deeper than the original design allowed for, however, means drying is very slow and costly.
“Even managing the system to use ambient air whenever possible, it was still costing us ÂŁ9/t to dry grain, which is very expensive,” says Mr Pocklington. “And we were getting problems with crusting on the surface because of the lack of airflow and slow drying rate.”
Two options were considered – adding a stirring system to at least one of the existing stores to improve airflow and evenness of drying; and building a new, higher-specification bulk store.
“We didn’t want to invest in the old sheds because we’d still have old sheds,” Mr Pocklington says. “Buying a new bulk store, when it was mainly the drying performance that was the issue, would have been a very expensive choice.”
While a new shed is more versatile, he acknowledges, in that it can be employed for other things such as machinery storage or alternative uses in future, the decision came down in favour of in-bin drying as the most cost-effective option.
“It gives us more options for managing incoming grain at harvest and on-floor drying performance will be improved by cutting back on the depth of grain stored in the sheds,” Mr Pocklington explains. “We also have more storage capacity for future increases in yields and tonnage.”
James Pocklington says of the in-bin drier: “It gives us more options for managing incoming grain at harvest and on-floor drying performance will be improved by cutting back on the depth of grain stored in the sheds.”
At present, a single 14.6m (48ft) diameter GSI FCDL 48-7 in-bin drier sits on an easily accessible concrete pad opposite the yard entrance. But there will be two by next harvest, providing up to 4,580t of storage and the ability to dry or condition up to 950t of grain at a time.
“It’s another advantage of using bins that we can spread the investment over two years,” Mr Pocklington notes. “Using the first unit this harvest worked out very well; we put our oilseed rape through it as a bit of a trial run, which proved that in a very wet year we could operate the bins as batch driers before transferring grain to the floor stores.”
The fan house and ducting were installed by GSI supplier Danagri-3S with that in mind – the 30kW (40hp) low-speed centrifugal fan blows into Y-shaped ducting, with simple lever-operated rubber sealed louvres determining which bins receives the airflow.
Inside, a “small grains” galvanised steel drying floor on 300mm supports distributes air throughout the entire footprint of the bin, which is filled evenly with the aid of a powered spinner with variable speed electric drive to suit different crops.
Maximum bin capacity for drying – to just below the eaves – is 950t, but that can be topped up with dry grain to 1,190t for long-term storage.
A stirring mechanism with three full-depth augers accounts for difference. Mounted on a rail at the eaves, they trace a circular zig-zag pattern to continuously mix moist and dryer grain, and encourage optimum air flow.
“The stirring system allows us to apply heated air at much higher moisture levels because it eliminates the risk of crusting due to excessive wetting in the upper layers of grain,” says Frank Ward of Danagri-3S. “It also has an impact on fan size, energy consumption and noise because we can reduce the volume of air needed from 100cu ft/min to between 30 and 40.”
Temperature-based drying control is incorporated into the panel supplied by Tryac that also handles all other functions; the only exception being the spinner speed dial, which is located next to the eaves hatch where the operator can see the effect of making adjustments.
The hatch also provides access for sampling in addition to the access door sampling facility at ground level so that drying progress can be monitored.
With the 2.5m btu/hr modulating gas burner cutting in and out as ambient conditions allow, Frank Ward calculates the system set at 50C will typically remove 1.5-2.0% moisture from 500t of wheat every 24 hours.
“I was a bit alarmed at the amount of gas it was using at first,” says Mr Pocklington. “But then there was a tremendous saving overall because the grain was dried so much quicker than in our floor system, which also reduced energy consumption.”
So much so, he calculates a figure of around ÂŁ3.50/t getting grain from 19% to 14% moisture – a far cry from the costs incurred in the floor store last year but which should also be reduced by drying a shallower bed of grain more efficiently.
Control unit produced for Danagri-3S by Tryac is used to set the drying temperature and operate all other functions except the filling spinner speed adjustment.
Fan house and ducting with rubber-sealed louvre outlet are installed ready for the second in-bin drier being erected early in 2012.