Super-efficient potato facility reduces costs and allows longer storage
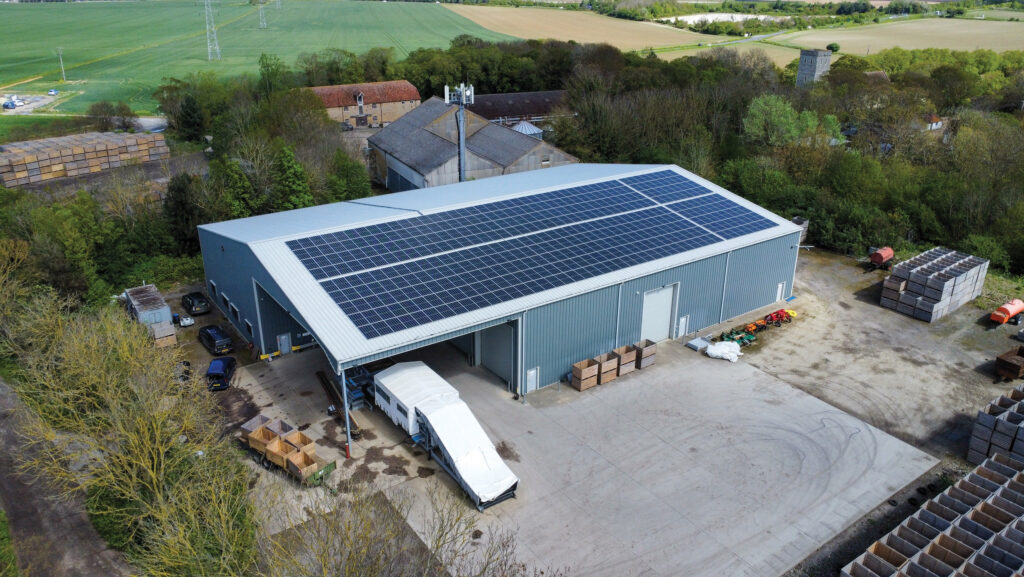
After a store-ravaging fire destroyed his older buildings and boxes in 2016, specialist potato producer Philip Smith invested in a new super-efficient facility that is cheaper to run and maintains crop quality for longer.
The fire at the farm’s base on the Isle of Thanet in east Kent happened just as its first harvest rumbled into gear, with the potato enterprise having been brought back in hand after a local contractor gave up.
Fortunately, potato supplier Greenvale came to the rescue, allowing the use of a redundant store nearby while Philip considered his next steps.
See also: High-tech potato-grading line ups profits for Cornish grower
Farm Facts – Monkton Court Farm
- Total area 350ha of silty loams and silty clay loams
- Cropping 60ha potatoes (30ha owned, 30ha rented) plus winter wheat, peas and AD crops
- Potato varieties Desiree, King Edward, Laura and Lanorma (all pre-pack)
“That got us through the 2016 harvest, but we had to decide immediately whether we were going to rebuild or not, as the lead time on a store was a good 12 months.
“If we wanted a new facility to be ready for 2017, we had to act swiftly,” he says.
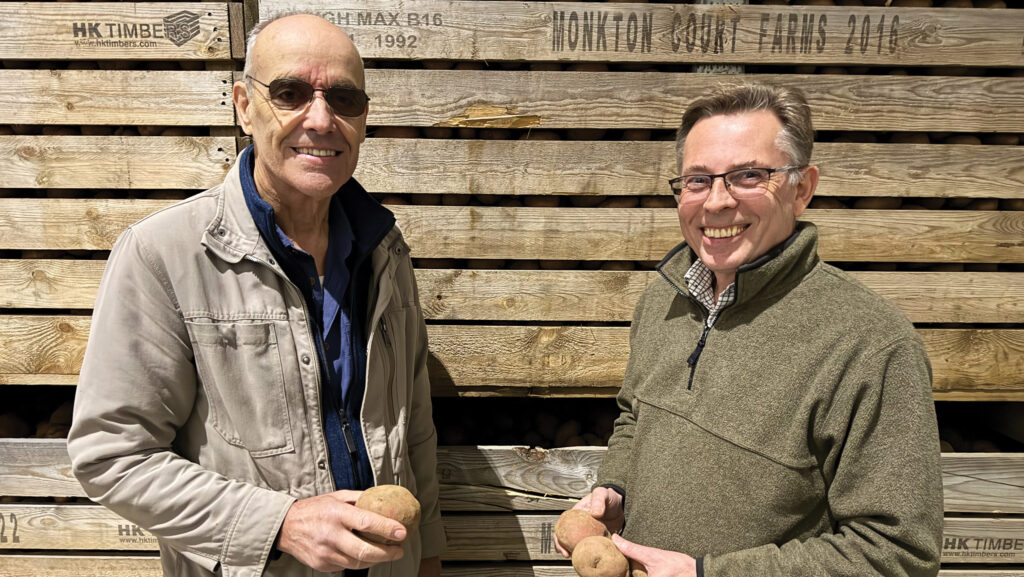
Philip Smith and Graeme Skinner © Adam Clarke
Decent storage is essential for his business, which has the ideal soils to grow pre-pack varieties Desiree, King Edward, Laura and Lanorma with a good skin finish for local supplier Provenance Potatoes.
The production and marketing group sells its spuds to large retailers, local wholesale and catering businesses, and export markets.
Philip’s potatoes are typically sold between February and July when values peak, so a proportion of the crop can spend up to 10 months in store before being moved on.
Under the guidance of Provenance Potatoes’ independent agronomist and store manager Graeme Skinner, he made the decision to construct a new facility on the existing site, which came from Norfolk-based installation specialist Crop Systems.
Monkton Court Farm potato store spec
- Four box stores within building, totalling 3,400t
- Includes 346t seed store, plus three crop stores
- Steel and timber suction chambers in each store
- Glycol cooling system
- Humidification system including adiabatic cooling function
- Automatic inverter controlled multi-speed fans
- PosiStor ambient cooling system
- Fully automatic fogging program
- Carbon dioxide sensors and automatic purging
- Galvanised steel stairs and handrails for safe access to all stores
- SmartStor and SmartSola control systems
- Total investment about £1m or £300/t (£70k planning and groundworks, £930k building and equipment)
Reduced operational and maintenance costs
The new setup represented a real step change for the business relative to its previous infrastructure, which featured refrigerated “overhead throw” stores built and added to over time. Each building had only basic controls.
The overhead throw stores forced air around boxes to dry and cool the crop and were often inefficient. This sometimes resulted in uneven temperature profiles through the stacked boxes due to inconsistent airflow.
Instead, Graeme recommended open plenums – which help reduce short circuiting of air to improve the flow – along with a glycol-based refrigeration unit and a humidification system with adiabatic cooling function.
Crop Systems claims glycol refrigerant setups are more efficient than alternatives, as they use one quarter of the volume of gas.
Coils with a large surface area and high airflow result in improved performance and little defrosting.
These factors combined result in greatly reduced operational and maintenance costs.
The store is managed through Crop Systems’ SmartStor kit, which allows complete control of the site remotely via a smartphone, tablet or laptop, making an in-store console almost obsolete.
SmartStor automatically adjusts temperature and relative humidity, and triggers automatic carbon dioxide flushing when a set threshold is reached.
All data is logged and easily accessible, and alerts can be sent to store managers when certain set parameters are exceeded and if plant faults occur.
“There is always a budget, but it is about prioritising the features that are going to maximise value for the business. In this store, I think we achieved that,” says Graeme.
One of the features that has provided the greatest value is the humidification system, with weight loss through dehydration – caused by ventilating the crop with dry air – having the potential to significantly reduce yield at the end of a long storage period.
During the first operational year of 2017, national oversupply meant that some of the crop was held on site until October 2018, coming out of store in very good condition with a noticeable reduction in weight loss relative to previous years.
“We tried to specify the best store we could, and then find a way to pay for it,” says Philip.
“Humidification was a sizeable extra, but it’s clearly very important to achieve reliable long-term storage whilst maintaining quality, so we went for it.
“When potatoes are at reasonable contract values and very high free-buy values, just a small percentage of yield loss from dehydration starts to add up to a significant financial hit,” he adds.
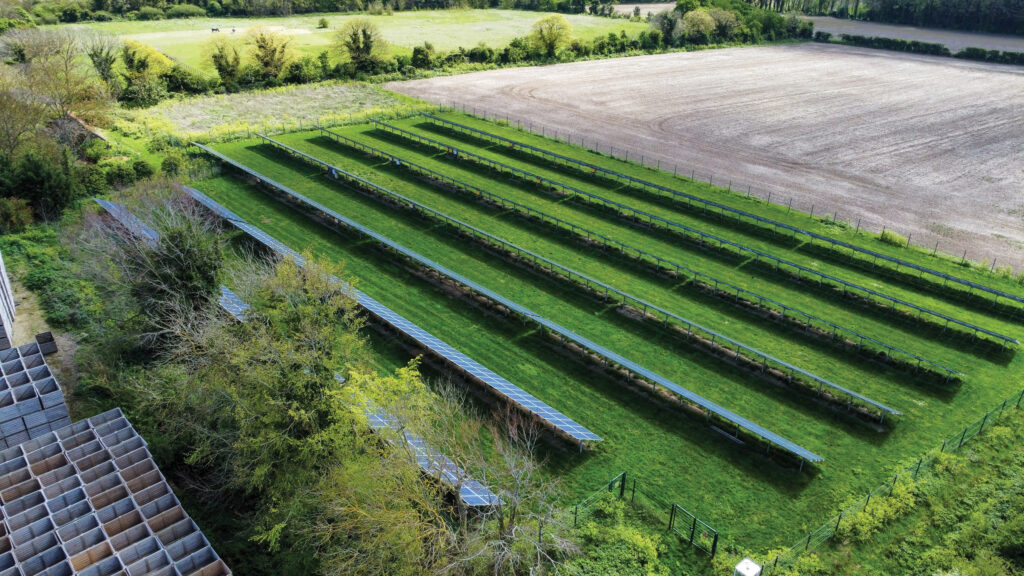
© Adam Clarke
Energy use
Energy consumption for potato storage, particularly in refrigerated cold stores that keep fresh potatoes at about 3C for long periods, can be high.
Many modern installations are now making use of solar panels to meet demand.
Philip had an existing ground-based 50kW solar installation adjacent to the storage site.
This was commissioned when the government Feed-in Tariffs – which pay households and businesses for excess electricity generated from renewable sources and feeds it into the grid – were attractive.
Two years ago, the decision was made to add another 150kW installation on the roof of the store, which he felt was a no-brainer given he would be storing potatoes for long periods.
“Solar is such a good fit, as most of the energy is produced through the warmer summer months when you need it most.
“And, with the way the energy prices have gone, it’s a lot more attractive now than it was just before we installed it,” he adds.
The upgrade of the farm’s solar capacity coincided with Crop Systems releasing additional store control software, and this was added to optimise use of the renewable energy.
SmartSola, which costs upwards of £1,100, is coupled with SmartStor to constantly monitor the energy requirement of the store, or cluster of stores, and prioritise use of the cheapest energy source at any given moment.
In any refrigerated store setup, when the ambient air outside is cold enough store managers will take advantage and use it to cool the crop and put in a slight offset, say 0.2C on a 3C store.
The control system will then ventilate the crop with the cold ambient air down to 2.8C, essentially using the crop as a heat sink by bringing the temperature slightly lower that the target 3C, delaying use of the fridge and saving electricity.
In a similar way, Graeme says a neat benefit of SmartSola is that when there is enough solar energy to run the cooling equipment, it kicks in and bring the crop down to an offset – essentially uses the crop as a battery.
“It’s saying if we have the energy today, lets store it in the crop, as we don’t know what tomorrow might bring.
“You can’t do that every day if it’s bright and sunny, but using cheaper cold ambient air when we have it, or maximising use of solar energy when we get it, can really help optimise energy use,” he explains.
As the system was retrofitted to the store around the same time as the roof-mounted solar panels, Philip does not have a before and after comparison of financial savings with and without SmartSola.
However, he does stress that achieving the 80-90% coverage of spring and summer energy needs since it was installed would not be possible with a standard control system alone.
“I’m confident that the reasonable cost of SmartSola represents a very good investment and is recovered in a short period of time,” he says.