Silage pit turns into grainstore
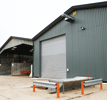
It’s not often that companies are asked to quote for converting a silage pit into a grain store. But that was the brief Perry of Oakley was given by a Cotswold farming operation that had abandoned dairying and needed to upgrade storage facilities for its organic beans and milling wheat and oats.
“The farm’s existing 600t storage capacity was marginal for the cropping acreage some years but more important was the lack of drying capability,” explains Mike Callaghan, UK agricultural sales manager. “With only a noisy diesel-engined Lister fan available for ambient drying and cooling, a significant proportion of the crop was in danger of being lost in a bad year.”
Erecting a new, purpose-built store was considered but when it became clear that half of a two-span, four-bay covered silage pit could be converted at lower cost and with few compromises, it became the obvious solution.
“The building was located near the old grain store, so it was in the right place, and it was very sound, being only a few years old,” adds Mr Callaghan. “At 43m long, it was also a very generous size, so it could house a modern handling and drying package while still providing more than enough capacity for the farm’s current and likely future requirements.”
Besides which, the adjoining span could also be converted in future if more capacity is needed, something that was taken into account when installing the store-filling conveyor. It projects from the front of the new store so that a lateral elevator could be installed to feed the additional storage space.
As it is, the conveyor positioned high in the roof space and running the full length of the new store provides efficient automated filling and under-cover truck loading of grain being dispatched off the field.
The handling system transformed store filling when it was used for the first time last year. Previously, this involved backing a trailer in, tipping it and pushing up grain with a telescopic handler.
“With the new store, trailers back up to a free-standing intake hopper located outside to minimise dust contamination,” notes Mike Callaghan of Perrys. “It feeds a 60t/hour chain-and-flight conveyor and double-lift belt and bucket elevator, which had to be set into a shallow trench so that the installation would squeeze in under the roof.”
An aspirator pre-cleaner between the intake conveyor and elevator removes the worst of any debris, discharging it to a cyclone outside the building.
Grain can be directed straight into the store via a short elevator feeding the roof conveyor or along a flow-and-return conveyor, which fills the drier and takes any excess grain to the two 27t capacity holding bins.
The drier has continuous roller discharge rather than pulsed or batch emptying of dried grain to an integral conveyor hopper that minimises the overall height of the drying installation.
This set-up, together with sensor-triggered auto shut-off controls, means the facility can be operated much of the time without constant supervision.
The only clue to the steel-framed building’s former role as a silage bunker is the 600mm fall in the concrete floor, which for its new role was given a fresh skin with a smoother finish so that grain can be scooped out cleanly with the telehandler bucket.
Alterations to the cement fibre roofing were limited to filling in ventilation slots to make the building as bird-proof as possible. The vertical timber slats along the side and rear aspects above the concrete retaining walls were retained to match the appearance of the adjoining span.
Marine ply boarding on the inside allows grain to be piled a little above the outside walls, with stainless steel flashing installed to bridge the gap and eliminate a wall-top ledge.
The front of the building has been enclosed with profiled steel sheeting, a large electric drive roller shutter door and a single door giving access to the control room and drying area, which occupies the front-right corner of the building.
“The drier and wet bins could have been located outside to maximise storage capacity,” notes David Perry, managing director, Perry of Oakley. “But it was important to the client that the conversion should be as unobtrusive as possible.”
Portable concrete sections divide bunkers according to the proportions of winter wheat, spring wheat, oats and beans grown each year.
With the drying facility enclosed by the building’s central silage wall and steel profile cladding to the roof, the only other internal modification needed was to take out a section of the centre wall to give out-loading access to the right-hand bunker. Moveable concrete sections are used to divide the bunkers according to storage requirements.
“As a result of this project, the farm now has around one-and-a-half times the storage capacity it had before, with holding, pre-cleaning and drying facilities that will greatly improve harvest management and crop marketing opportunities,” says Mr Perry. “I’m told last year’s wet harvest would have been a disaster without the new facilities, which came in at substantially lower cost than would have been the case with an all-new store.”
If you’re thinking of putting up a new building or refurbishing an existing one, make sure you come to the Agricultural Buildings Show at the Bath and West Showground on 2 April 2008. Tickets cost ÂŁ10 on the door or ÂŁ5 in advance. Tickets and further info from 08454-900142 or click on the official ABS website
If you specifically need a steel building, then get quotes for Steel Buildings here from up to 6 suppliers.