How a potato farm is leading the way on lower CIPC rates
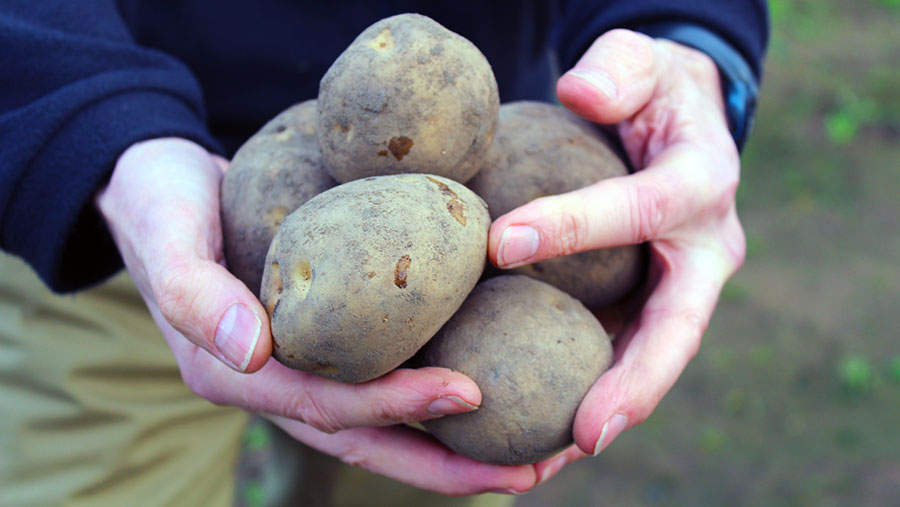
A North Yorkshire business is leading the way in being ready for life on new lower maximum doses of chlorpropham (CIPC), a key spud sprout suppressant, by developing a new application system for box stores.
Based just outside the village of Dunnington, some five miles east of York, RS Cockerill is a family-owned farming, packing and potato supply business.
The farm grows winter wheat, winter and spring barley, oilseed rape, spring beans, maize and sugar beet plus 200ha of potatoes on a combination of owned and rented land.
See also: Tips on establishing a high-yielding sugar beet crop
RS Cockerill, North Yorkshire
- Area: 545ha, split between owned and rented land. 200ha of potatoes, about two-thirds irrigated and one-third non-irrigated.
- Soil type: Mainly sand over clay, with significant levels of potato cyst nematode and free living nematodes.
- Supplying 100,000t of potatoes a year to processors, with crops coming from a network of more than 40 growers.
- Packing 80,000t of potatoes a year for the retail and food service industry.
- Storing in excess of 15,000t of both growers’ crops and own crops.
Potatoes are mainly grown for crisps, with the balance going to the packhouse.
The business is also involved in a trials programme to develop new varieties for the crisping sector and produces seed potatoes.
The farm has been working closely with AHDB Potatoes and the CIPC (chlorpropham) stewardship group to investigate new, more efficient ways of box store application.
CIPC is a vital tool to control sprouting and is applied to about 3.5m tonnes of potatoes stored each year in the UK.
Since 2012 the potato industry has gradually reduced the amount of the chemical that is applied to stored crops, following concerns over residue levels.
From July this year, total doses applied to processing potatoes must fall below a new 36g/t limit, while fresh market spuds can be treated with only up to 24g/t of the fumigant, which must be applied using an “active recirculation” method.
What is “active recirculation”?
The potato industry has agreed on the term “active recirculation” to describe the recirculation of air containing CIPC gas using fans.
Research shows that correct use of fans can dramatically improve the uniformity of CIPC dispersal within a store, leading to a reduced risk of exceeding maximum residue levels – a particular problem in box stores.
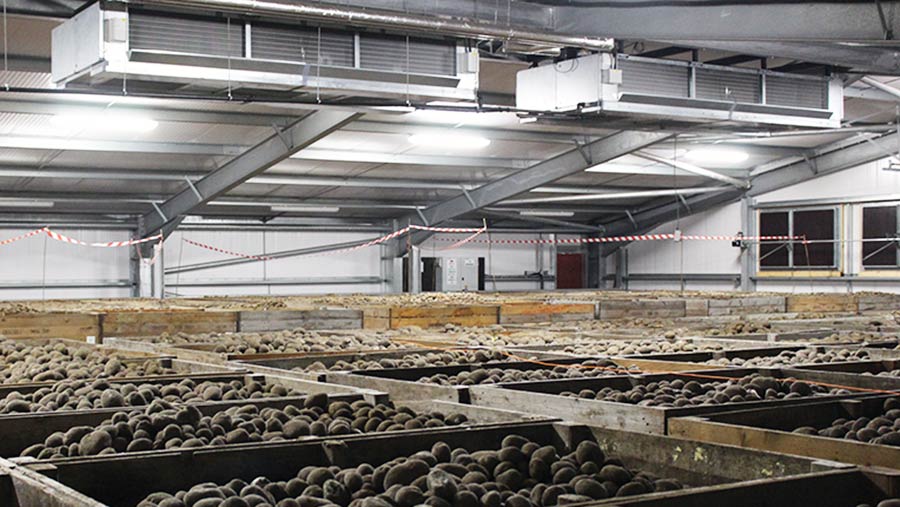
RS Cockerill’s new box store holds up to 3,300t of potatoes © Oli Hill
Adrian Briddon of AHDB Potatoes explains that, in most cases, “active recirculation” can be achieved using variable speed control to slow fans down to give a steady circulation of fog throughout the store.
“Everything we do in a store is carried out by air, so handling the air is critical,” says Mr Briddon. “Fans need to run at slow speeds so we have to fit an inverter to control speed.
“Success does very much depend on following all of the best practice and, with this, I don’t think that the new 2017 limits should be a problem.”
For more information on active recirculation and how it can be achieved, visit the CIPC Stewardship website.
Bulk vs box stores
Research efforts have been concentrated on improving the flow of gas through spuds in boxed stores as 100% coverage in bulk stores is relatively straightforward, explains CIPC stewardship group chair Mike Storey.
“We know very well now how to use positive ventilation in bulk stores, but box stores are more challenging and we need to maintain best practice.
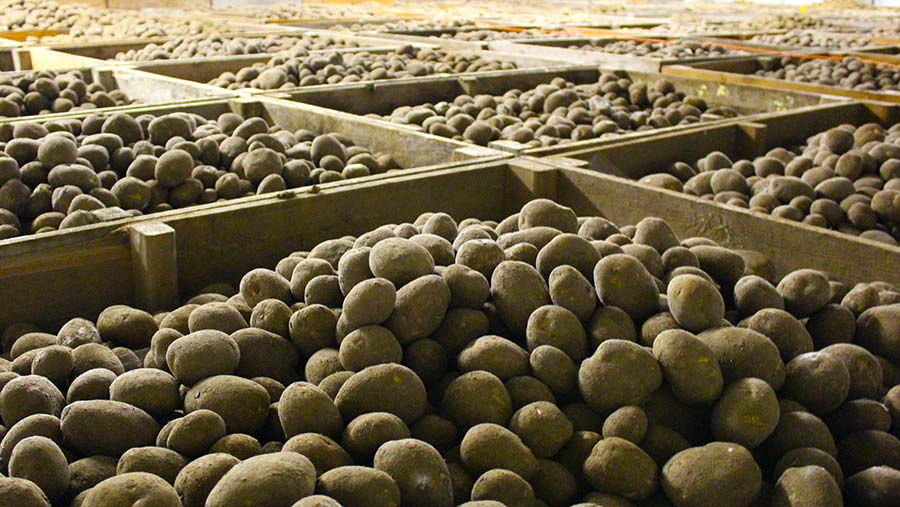
Inside the new box store at RS Cockerill’s central washing and storage site © Oli Hill
“The majority of exceedances have occurred in boxed stores for fresh markets, but we haven’t had any exceedances as an industry since February 2014. We have got to keep this up,” he says.
“Research carried out by AHDB at Sutton Bridge Crop Storage Research in collaboration with the industry has clearly demonstrated that the correct use of fans can systematically improve the uniformity of CIPC distribution and reduce the risk of maximum residue exceedance.”
Total CIPC use across the industry has declined by 50%, as more potatoes are treated with less of the fumigant, but Mr Storey acknowledges that it has taken a lot of investment in stores to get to this stage.
He also makes the point that, as uniformity of coverage improves, inevitably sprouting control improves too.
Horrocks system
Trial work was carried out using an existing box store on the RS Cockerill farm, with the aim of developing a system that achieved good CIPC coverage and sprout control at the lower rates for 2017, but that was cost-effective and simple to replicate in other stores.
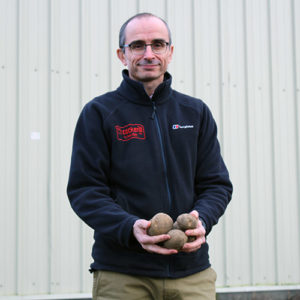
Mike Dangerfield, RS Cockerill commercial director © Oli Hill
“We thought it was important to develop a better way of applying CIPC,” explains commercial director Mike Dangerfield. “In 2015 we converted one of our existing box stores to work out a good way of distributing the gas more effectively.”
Having experimented with four different systems to find a practical way of adapting the stores of RS Cockerill’s grower network, this store is where the Horrocks system for applying the fog was developed, in tandem with Sutton Bridge Crop Storage Research and funded by the AHDB.
Mr Dangerfield says that the Horrocks system is a cost-effective way of adapting current potato stores and adds that the principle can be applied to most box stores that are already up and running.
“We found that this system is not just better for CIPC application, it also means that we can dry the potatoes out more to avoid rot and disease. Temperatures are also held more consistently, so there is less risk of condensation.”
How it works
The system works by forcing air into the two lowest base slots of the boxes using inverter-driven fans to create positive ventilation.
Foam pieces are wedged into the opposite ends of the stacked boxes, meaning the only way for the air to go is up through the stack (see diagram).
Positive ventilation systems such as this one have given the best results in trials, achieving the most uniform distribution of CIPC gas in box stores.
However, it is worth noting that positive ventilation creates back pressure, so there needs to be enough pressure generated in the “active recirculation” system to overcome this resistance and make sure distribution is even.
The Horrocks system of applying CIPC gas achieves good spout control when low rates are applied
“We then used what we learned and applied this to our new, purpose-built store, which needed to be built anyway for extra capacity,” adds Mr Dangerfield.
Finished in time for the 2016 potato crop, the new store can hold up to 3,300t and has seen good sprouting control since holding its first crop. It is located at the company’s central washing and storage site, some 10 miles down the road from the main farm site.
“We have been working with our base of 40 growers, sharing our learning and helping to develop better ventilation systems in box storage.”
It is estimated that so far about half of the UK’s 2,000-2,500 potato stores have been updated to help meet the requirements for lower CIPC rates, but some of these can be modified relatively easily at low cost, explains Adrian Cunnington, chair of the CIPC technical working group.
But Mr Cunnington says more research work is needed to perfect airflow in potato stores.
“We have not done the job completely yet,” he says. “We need to understand how to optimise air distribution further, using predictive airflow computer models.”