A guide to reducing tuber bruising losses this potato harvest
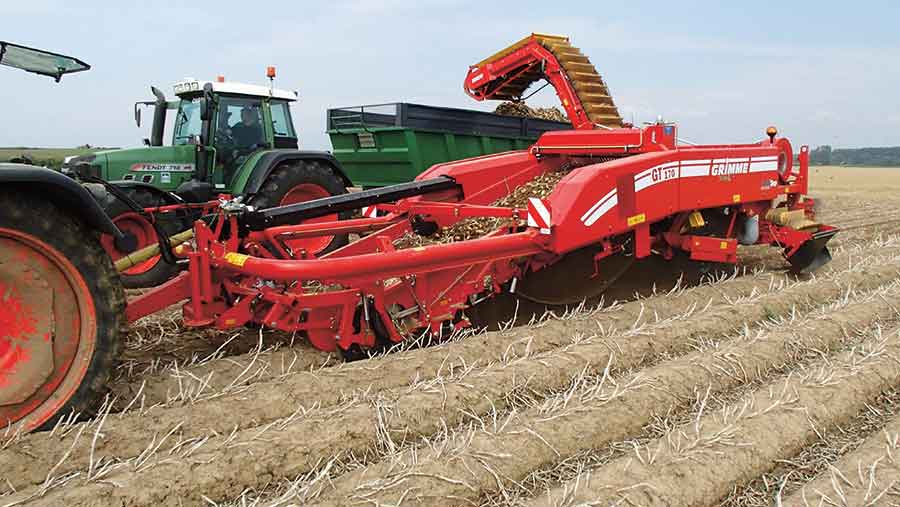
Thorough preparation and setting up, and adjustments with changing conditions once under way, are fundamental to minimising levels of bruising damage as potato crops are harvested
Taking the time and focus required to prepare and set up a potato harvester correctly for a new season is fundamental to lifting a crop with the least possible tuber bruising.
While soil conditions, crop maturity and dry matter and various other management factors influence susceptibility to impact damage, the lifting process exposes tubers to some of greatest damage risks as they are sifted, cleaned and elevated.
These risks are most effectively mitigated by ensuring harvesters are thoroughly prepared, with conveying and other elements returned to tip-top condition, with all cushioning materials in place.
See also: Invest in potato storage now to secure bright future
Thereafter, everything rests on the ability of the operator to set up each section and device on the harvester to lift the crop cleanly and efficiently, but with the least risk of bruising damage.
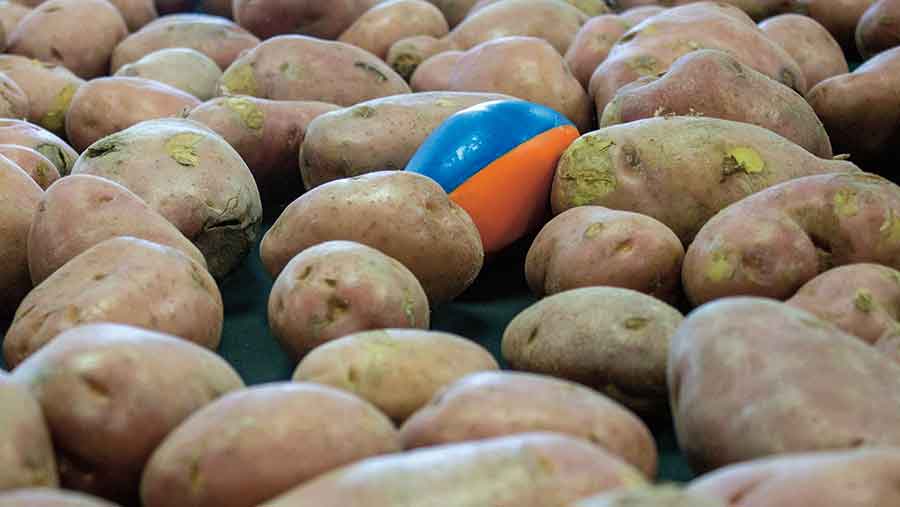
Using an ‘electronic potato’ to record impacts experienced by tubers on harvester, handling, grading and packing equipment can help identify where improvements need to be made
“An ‘electronic potato’ like our TuberLog makes a valuable training tool for operators working throughout the harvesting process,” suggests Gavin Lishman of electronic monitoring and control specialist company Martin Lishman.
“Everyone from tractor drivers to those manually handling bagged potatoes soon alter their methods if they can see the effects of any bad practices.”
More typically, such devices are used to monitor harvesting machines and handling lines already in use and help set up new installations with carefully managed crop flows to minimise bruising.
The usual the usual “rules” apply when using the TuberLog to make assessments, explains Dr Lishman.
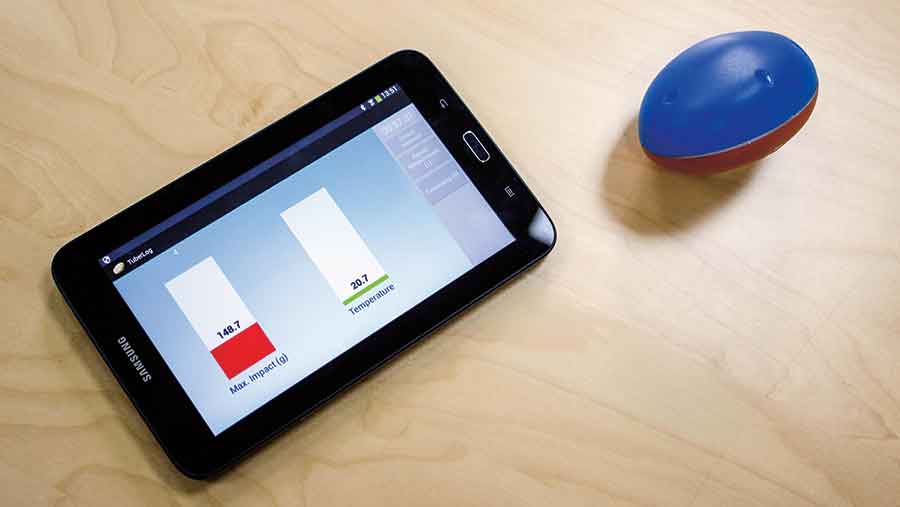
Latest version of the TuberLog has upgraded waterproofing and easier service access
“Take several readings from each place where a bruise is detected, so that the average is used to provide an accurate picture rather than a solitary high reading.
“Ensure that comparative readings are taken from a machine, so divide it into sections and always use the same sections to get results,” he adds.
Dr Lishman recommends using a hot box to “calibrate” results, as high levels are obviously going to be an indication of bruising, but medium levels can indicate bruising in some varieties and not in others.
“Knowing which is which is important in terms of whether or not it is safe to continue working with the machine or it needs immediate maintenance,” he adds.
Potato harvesting – anti-bruising checklist
Preparation
- Defoliator flails should be sharp and match the ridge profile
- Check harvester webs and star rollers for damage, exposed rivets, web and elevator guide roller condition and adjustment
- Measure diablo roller width and side disc dimensions to ensure they are correct for the ridge profile
- Inspect for missing rubber coverings, foam padding etc and for damage and excessive wear
Crop condition
- Ensure haulm is effectively desiccated for easy separation from tubers
- Wait if necessary for tuber and soil temperatures – not just ambient – to rise above 10C
- Soil moisture is a significant factor – too wet increases clods, too dry lacks cushioning
Harvester set-up
- Set defoliator to leave 180mm stems – short haulm is more difficult to remove on the harvester
- Adjust harvester share depth and pitch to undercut the crop without excessive soil
- Set diablo roller pressure to avoid squashing the ridge but sufficient to get soil flowing up the share
- Set web and roller speed to provide a soil cushion for as long as possible
- Avoid settings that result in tuber roll-back – a significant source of bruising
- Minimise use of any web agitation device – don’t use it at all if possible
- Avoid using haulm fingers if possible – but check rubber protection and set pre-loading tension as light as possible
- Aim to remove around two-thirds of haulm – tuber damage will likely result from trying to take out more
- Adjust cleaning module to remove small clods and stones without excessive tuber bouncing (speed too fast) or pinching (speed too slow)
- Incline adjustment helps regulate tuber flow across cleaning systems
- Be prepared to adjust haulm extractor and crop cleaning settings with varying soil type and conditions
- Adjust cart elevator speed so that pockets are three-quarters full to minimise movement