New grain drying technology reduces energy use
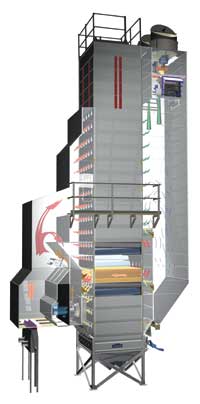
This year’s harvest emphasised the value of having good grain-handling and drying equipment. Peter Hill takes a look at the latest innovations on show at the recent UK Grain event near Peterborough
At the UK Grain event, energy-conscious growers – and who can afford not to be these days – were presented with new technologies designed to reduce the amount of energy required to dry or cool crops in storage.
Most tower dryer manufacturers now included inverter controls for exhaust fans as part of the package. Apart from giving precise control of fan speed to prevent light seed being lifted off, these machines are said to reduced energy costs by around 27% for every 10% reduction in fan speed.
Another technique set to become more commonplace is heat recovery, which re-uses some of the hot air used to reduce grain moisture content that would otherwise disappear into the atmosphere.
Swedish manufacturer Tornum believes heat recovery can cut energy consumption by as much as 30%.
“The extra hardware needed adds about 15% to the cost of the dryer,” said Andrew Buesnel of the firm’s new UK agent M Construction Services, Diss, Norfolk. “But that can be recouped in three-to-five years, according to Tornum’s calculations, depending on how much the system is used.”
Although saturated air from the top of the column is still exhausted as usual, air from the lower part of the drying sections and from the cooling section of Tornum’s heat recovery dryer is drawn by a fan through ducting to join incoming air passing across the burner.
Since this warm air is not saturated, it still has some capacity for removing moisture from grain as it passes back into the upper sections of the dryer.
Optional dust reduction is another novel feature; during discharge, the exhaust fans are slowed briefly, which together with an extended wet air channel, is said to greatly reduce the amount of dust leaving the dryer.
A screw auger in the wet air channel is used periodically to remove this material to a tote bin or similar vessel for disposal.
“Reducing the airflow briefly obviously has some impact on output,” Mr Buesnel accepted. “But it does also reduce the amount of dust blown across the yard and on to buildings.”
Low-energy electric motors are used to reduce the power consumed by Evolution extraction ventilation fans from Evans & Pearce.
Rob White of the Dorset-based company calculated that the brushless motor uses 0.35kW, costing 3.5p/hr, to pull the same amount of air through the crop as a conventional motor using 1.1kW costing 11p/hr to run.
“The fan unit costs more to buy because the technology is more expensive,” he said. “But they cost less to run so there’s a saving in the long run.”
A pair of Evolution fans costing £1398 (£128 more than a pair of conventional units) typically costs around £150 less per year to run for 1000 hours or so, which could easily racked up in a typical season, he suggested.
Lower start-up power demand means standard extension leads can be used and building a temperature differential control unit into each Evolution fan means there is no need for a separate device and associated wiring.
Growers wanting to use the new fan units on existing Evans & Pearce Polycool or similar pedestals will need to fit 20cm (8in) diameter upper tubes in place of the standard 15cm (6in) size on base sections because the fan needs a larger impeller and scroll to achieve its performance.
Mobile grain vac
Grain stores that lack power to operate an conventional auger can be emptied using a tractor-driven, high-capacity grain-handling device being imported from Canada by Ryetec Industrial Equipment.
The Rem Manufacturing GrainVAC differs from traditional grain blowers in using suction to draw grain from the store, but an auger to deliver it into a trailer.
“It has a greater output than a ‘sucker blower’ because the impeller only has to create a vacuum, it doesn’t also have to blow the grain,” explained Robin Sparrow of Ryetec. “Grain sucked into the unit is separated from the air by a large rotating barrel screen, from which it falls to the 10in auger to be carried away.”
There are two GrainVAC models – the 2700 with up to 160t/hr capacity drawing grain through a 10m hose priced £19,500; and the 3700 with up to 270t/hr capacity and priced £27,760.
Takeover
Law-Denis tower dryers are back in production after the manufacturer was placed in administration towards the end of last year.
All intellectual property rights were acquired by British storage and handling equipment manufacturer Brice-Baker and dryer production was restarted earlier this year at the company’s manufacturing facility near Bristol.
Brice-Baker’s sales and administration headquarters remain at Wyboston in Bedfordshire, but production is moving into more modern manufacturing facilities in Yate with more automation on the production lines.
“Acquiring the assets of Law-Denis Engineering has broadened our product line and came at a time when new shareholders have provided significant capital investment to develop the Brice-Baker business,” said chief executive Frazer Newell. “We’ve had a successful first year with dryer sales in Britain, New Zealand and Russia; we’re now improving our silo range and working to further improve quality and delivery.”
The latest dryers built to the Law-Denis design have a new large-scale touch-screen control panel that integrates controls for the whole handling and drying installation – including elevators and conveyors – not just for the dryer itself. Remote viewing, data logging for computer-held records and text alerts are also part of the package.
• Chief Industries has taken over UK and Ireland distribution of the Marot rotary cleaners and spares previously handled by Law-Denis Engineering.
Vision control terminal allows for remote monitoring
The Vision control system introduced on GSI portable and static dryers from Danagri-3S features a 264mm (10.5in), colour, touch-screen terminal that can be mounted on or up to 300m away from the dryer.
It features on an improved range of dryers said to bring together the best features of the Farms Fans, Airstream and DMC equipment lines, which have all been acquired by the GSI group in recent years.
“Until last year, GSI continued to sell grain driers using all four trade names,” noted Mark Unit of Danagri-3S. “But now, the equipment is available solely under the GSI name.”
The dryers feature a low filling height and are available with several lengths of drying chamber – from 2.43m to 7.9m long – and with modules that can be stacked up to three high on top of each other.
Portable versions of the single-stack model are available up to 30t/hr output, while static versions are up to 100t/hr capacity stacked three high.
The Vision software control system touch screen is used to set-up and choose between temperature-based or one of two moisture-based control regimes. It also allows easy switching between batch and continuous flow modes.
Animated grain-flow graphics and large, digital displays are said to help make dryer control and setting up easier. The lack of moving parts (timers, time delays, thermostats, etc) is said to give the system a long and reliable service life.
Drying history and shut-down logs can be transferred by USB memory stick to an office computer for analysis and software updates downloaded from GSI’s website are transferred to the Vision system by the same means.
The optional Watchdog software allows remote monitoring of functions such as moisture, temperature and dryer status using an internet-connected office or hand-held computer.
Portable dryers from Opico boast high capacity
The Magna 3810QF is the smaller of two high-capacity portable dryers added to the Opico range. The recirculating batch-type machines have a larger plenum chamber than usual, a bigger capacity burner and high-output loading and emptying augers to promote high throughputs. The 38t holding capacity Magna 3810QF is rated at 16t/hr drying feed wheat and there are manual and automatic versions. Unlike previous Opico portable dryers, the Magna 3810 and 46t capacity Magna 4610 are built for operation primarily in one location; the top section must be dismantled to move them from one site to another, with re-fitting taking a day or so. Prices are £67,617 and £83,012, respectively.