Notts Monitor Farm sees benefits of reduced cultivations
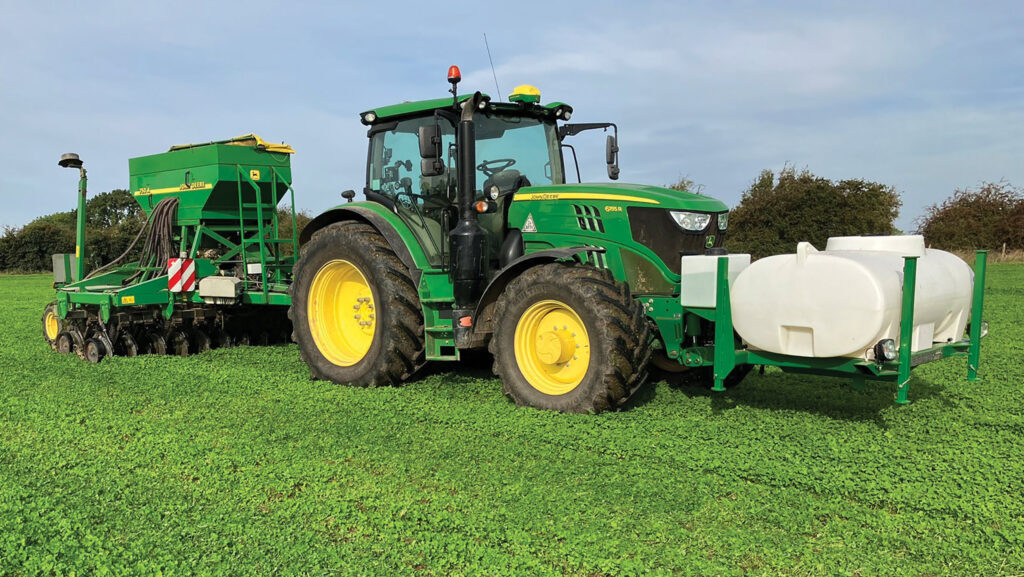
Reduced labour and machinery costs and more resilient soils are some of the benefits being seen since reducing cultivations at Manor Farm, near Bingham in Nottinghamshire.
The Fisher family have been on a journey since 2000 with the aim of moving less soil, and they have built a flexible system based on a direct disc drill for the majority of autumn establishment and a tine drill for spring crops.
See also: How a hybrid regenerative system works on Bucks Monitor Farm
Before 2000, the farm used a plough and combi drill approach on its soils, which range from sandy to clay loams.
Joe Fisher says that while the old system worked, they needed to move less soil as they doubled the size of the farm.
Transition period
They initially moved to a min-till system and then a Simba Trio plus trailed drill which sped up the operation and proved reliable.
Then Joe returned following two years working in fresh produce and the farm took its first direct drilling step. He opted for a Claydon, as he felt the soils needed some movement in the seeding zone.
Farm facts: Manor Farm, Bingham, Nottinghamshire
- 450ha of arable and 25ha of grassland
- Growing combinable crops plus maize and stewardship.
- 100ha contract drilling, spraying and combining for neighbouring farms
- Other enterprises include horse liveries, building lets, asparagus and an enclosed dog field.
Recalling the first season, he says: “We did not get the same amount of mineralisation and crops were slower to get away, but by spring, they had caught up and we did not see any yield drop.”
However, he says it wasn’t all plain sailing. The A-share struggled in heavier parts of fields and was bringing up clay lumps.
So they opted for narrower VOS openers. While this produced better seed placing in the seed-bed, there was too much strain on the tine carrying legs.
Fortunately, as they progressed further, soils regained structure and Joe says they are now making better seed-beds.
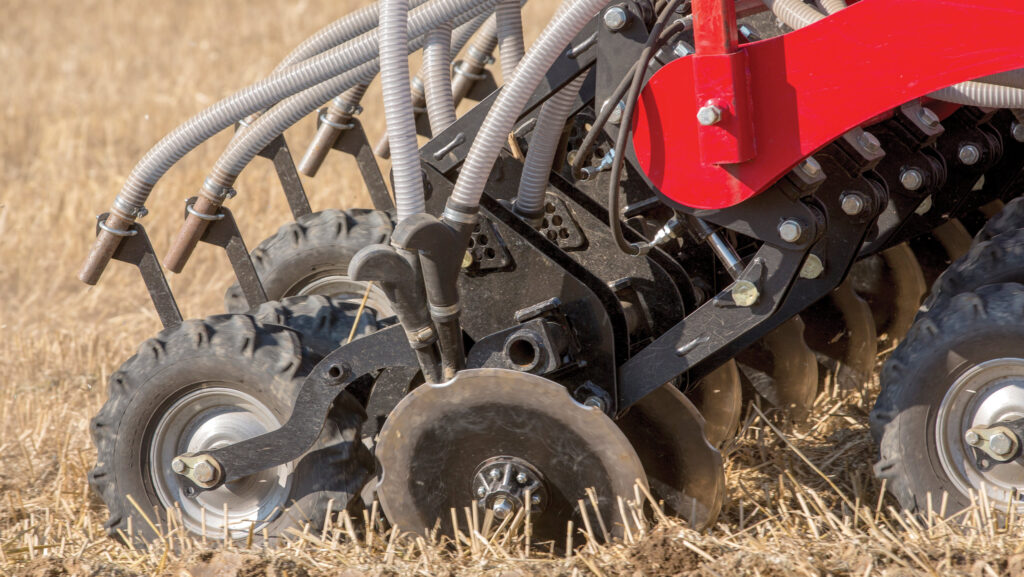
© GNP
Building a system
From 2016 to 2020, he extended the rotation, introduced cover cropping and started adding more organic material to soils.
“We realised that we had to build a system rather than just change the drill.”
The rotation was lengthened by adding in quinoa, beans and maize. He also pushed forward with soil organic matter by using green compost, biosolids and farmyard manure/digestate – as and when available.
He also aims to have more living roots in soils with overwintered cover crops ahead of the new spring crops.
Disc drill
The eureka moment came in 2019 when Joe was drilling wheat into a thick catch crop and realised they needed a disc drill to complement the Claydon.
He acknowledges that he has grown some good alternative crops, such as maize and sunflowers, with the Claydon.
“Last year we had a 52t/ha maize crop and it was the crop of 2023,” he says.
“But the downside is that on the areas where we didn’t need be moving soil at all, it moved more than you needed.”
So in 2021 he bought a 20-year-old John Deere 750A from Lincolnshire. He says it was a kind autumn that allowed less disturbance, and the soils that were ready coped well.
Soil improvements seen
Over the years, he has seen seen visual improvements in soils while trafficability has improved, such as combines and spreaders being able to travel in wetter conditions.
“It wasn’t a bad system before, but we wanted to move on and move less soil and reduce costs,” he says.
“Looking at finances, while we don’t grow as higher yielding crops as we have in the past, we have reined in overheads and variable input costs. The business is more resilient and with better margins.”
This is backed up with benchmarking figures. He points to his machinery and labour costs being £56/ha lower than the average of the top 25% of growers in AHDB’s Farmbench, at £223.4/ha and £280/ha, respectively.
Soil movement options
The system at Manor farm is based on having both tine and disc direct drills, which complement each other with their differing levels of soil movement.
Joe Fisher explains that they have more success with the 4m John Deere 750A in the autumn, as soils are warmer and there is greater biological activity.
In spring when soils are colder and nutrient mineralisation is required, he opts for cleaner seed-beds and that is where the Claydon comes in.
The Claydon is also used for establishing maize, beans, sunflowers and cover crops.
However, this autumn has shown the value of having both. The Claydon will still run in wetter conditions when the John Deere 750A would not.
In addition, the 750A’s capability for minimal surface disturbance complements the tine drill when managing grassweeds.
Minimising the cost of compaction
Reducing tyre pressures and sticking to the correct tractor ballast levels are some ways that farmers can minimise soil compaction with direct drilling systems.
Trafficking is a key cause of soil compaction and there are a number of actions farmers can take to reduce the risk. These are:
- Avoid high-risk fields in wet conditions
- Avoid high tyre pressures
- Minimise axle loads and optimise ballasting
- Take care with trailers/chaser bins at harvest
- Take particular care on headlands.
Focusing on tyre pressures, independent soils expert Philip Wright points to research showing how running tractors with high pressures can prove costly in terms of lost yield.
The work was carried out over four years across two farms.
He compared winter and spring cereals yields and found that areas trafficked with high-pressure tyres (1 bar) yielded only 60% of what the untrafficked areas achieved.
The yield increased to 70% with medium-pressure tyres (0.7 bar) and then 94% with low-pressure tyres (0.5 bar).
For a set of 710 tyres on a tractor pulling a 3m tine drill, farmers can be affecting 50% of the farmed area when allowing for tramlines and turning headlands.
Therefore, the 40% yield penalty with high-pressure tyres can apply to half the farmed area, effectively taking 20% off the bottom line.
So how can farmers minimise this? One way is to opt for tyres that enable drilling to be carried out at ground pressures of 0.7 bar or less.
Philip explains that conventional tyres run at low pressures can overheat with the excessive flexing, which can result in failure of the rubber.
However, VF (Very High-Flexion) tyres are built to enable tractors to carry out work like drilling at lower pressures.
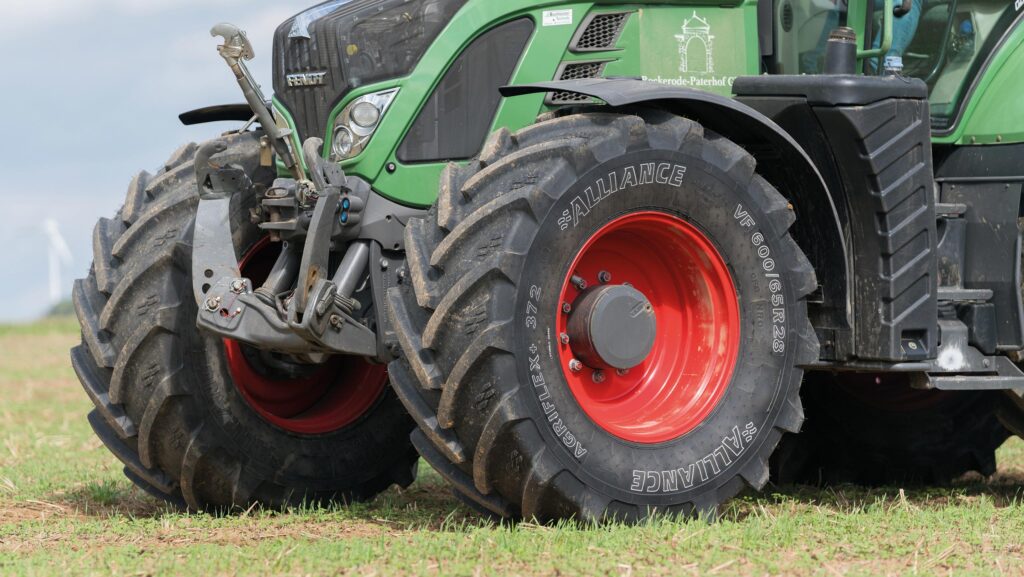
Low-pressure VF tyres can have a marked effect on crop yields © Agriflex
At Manor Farm, both of the John Deeres (6155R and 6215R) were conventionally shod and tyres were due for replacement.
Following Philip’s visit last summer, Joe has now opted for Bridgestone VF tyres that can run at 0.5-0.6 bar when drilling, instead of the 1 bar+ previously.
It’s not just pressure: getting the weight balance right is important when running lower pressures. Philip says the ideal balance is 40% of the weight on the front and 60% on the back tractor axle.
He recalls a contractor who came with a tractor and drill to set up a trial and the front tyres didn’t have enough downforce, with only 22% of the weight on the front.
Consequently, the front tyres were scratching up the surface which was then being compacted by the back tyres.
The solution was to put a 1t weight on the front. While this might be counterintuitive, in this case adding weight to the tractor improved performance and minimised soil damage.
Critical depth
Philip’s other piece of advice relates to tine drills and ensuring they don’t go below the critical depth.
“When above the critical depth, you get lifting and loosening of soil. But if you go below this, soil is compacted by moving sideways or downwards around the tine.
“If it’s dry, soil will crack apart below, but the problem is if it is wet. Then you get compaction/compression, which will form a smeared slot.”
With narrow tines, he says the rule of thumb is that the critical depth is six times the width. “So for a 1in wide tine, the critical depth is 6in.”
However, he warns that care is needed as tines are worn narrower, as the critical depth will become shallower and there is a risk of compaction and smear if farmers stick with the original depth setting.
Instead, he suggests taking off worn tines for a dryer season and putting unworn ones on.
For disc drills, it’s all about the cutting angle, he says.
“If discs are too deep, then you don’t get cutting of the straw trash, and risk stalling. If too shallow, the “scissors are nearly shut” and you get hairpinning.”
Hairpinning is where the disc does not cut through the residue, and instead pushes the residue into the seed slot. The seed is then left without good soil contact, resulting in poor germination and establishment.
Philip warns that you can get “a heck of a lot of hairpinning” going shallow with drills with inappropriately large discs in high residue levels.
“If nothing else, this might determine when worn discs are renewed – ideally before drilling deeper sown crops, for example,” he says.
Overcultivation danger
Philip’s final tip is for when farmers carry out some soil lifting to crack compaction: first check if it’s needed.
That is because soil loosening where it isn’t needed can have the opposite effect on crop yields.
He points to ongoing work at Agrovista’s Lamport AgX site in Northamptonshire, which recently looked at soil loosening in areas of simulated soil compaction.
There were four treatments:
- Untreated
- Compacted with no loosening
- Compacted with appropriate loosening
- No compaction with similar levels of loosening.
The compacted area had a significant yield reduction compared with untreated, showing the impact of this compaction.
Loosening brought the yield back up but, more importantly, the area that did not need any loosening had a yield loss.
This was of lesser magnitude than the compacted area, but still a loss compared with leaving it alone.
This shows the yield cost of loosening where it’s not needed.
“If you don’t need to fix it, loosening will make it worse, as it breaks up the natural blocks, and de-stabilises the soil,” Philip says.
“The cost of this unnecessary loosening also impacts negatively on the bottom line.
“So you need to be out with a spade, as it could cost you in lost yield.”