Exotic and unusual harvesters – peas, beans and spinach
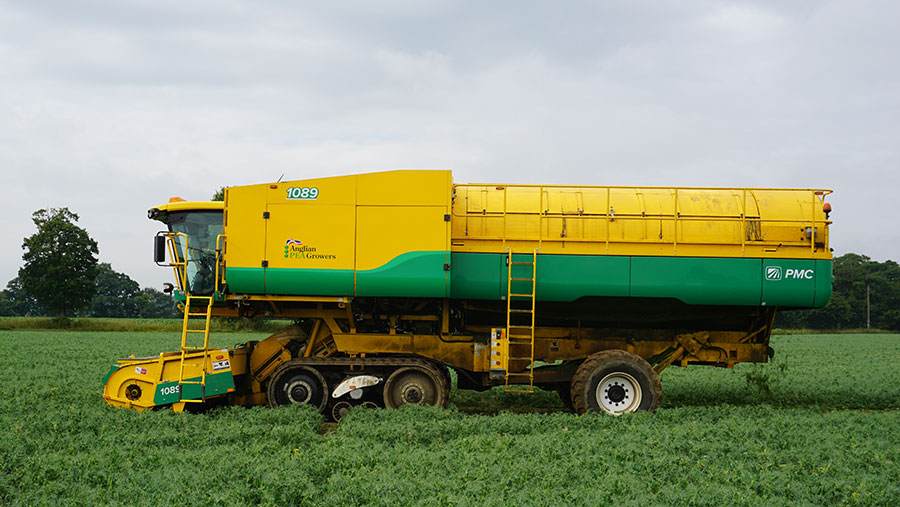
The popularity of frozen food , particularly frozen peas, in the late 1950s and 1960s led to a design rethink in harvesters.
An increase in the machines’ capacity meant the market could keep pace with demand.
Peas were first harvested by swathing them, then bunching the vines into heaps and finally bringing them to the farmyard, where static viners operated.
However, the huge inefficiency of carting large volumes of material led to the development of trailed machines built by the likes of Mather & Platt.
These needed to be hauled by the highest horsepower tractors of the day, such as Muir-Hill, County and Roadless.
See also: Exotic and unusual harvesters – rice
In 1976, FMC (now PMC) introduced its trailed H-2 harvester, which rapidly became the model for today’s range of self-propelled harvesters. The H-2 included the five beater planetary threshing system that is still used by the company.
Peas
A reel with tines strips the pods from the stems and an elevator takes them up to the threshing mechanism. This involves a long drum with riddles and four or five beaters inside the drum that press the peas against the riddle and push them through the length of the drum. The trick was to rub the vines in small portions so that none escaped unopened.
As machines get bigger, modern-day viners are increasingly running up against EU regulations on widths and lengths. Separation drums already take up most of the space available and it’s difficult to increase output without making the machines longer or higher.
PMC’s current 1089 viner on tracks weighs 27t unladen, is 12m long and 4m high. Power comes from a 444hp Scania engine, a 1,000-litre fuel tank is fitted and the machine can self level by up to 15% (giving a tilt of 8.5deg) from front to rear and 18% (10.2deg) from side to side.
Tracks are becoming more common on these machines. At Driffield, East Yorkshire, Swaythorpe Growers’ director Matthew Hayward points out that as cultivators have become wider, seed-beds have become less level.
This is crucial since viners need to be stable, otherwise peas are lost over the side of the aprons that collect them as they fall from the drum. There is also the inevitable issue of soil compaction from machines that weigh up to 27t.
Manufacturers consolidate
In the past 10 years there has been considerable consolidation among pea growers and machinery makers. In the UK there are now 20 or so groups producing 130,000t of peas from 35,000ha and feeding them to eight factories.
The level of investment involved is huge. New machines cost about £450,000 and vining groups such as FenPeas or Holbeach Marsh Cooperative will run three or four machines.
Consolidation among the manufacturers has been even more marked. Pea viners are made by Bourgoin, Ploeger and PMC, but all three companies are owned by Oxboro Corporation of the US, which also makes its own version. Oxboro has quietly been buying up makers of specialised harvesters and its portfolio includes everything from citrus fruit harvesters to coffee harvesters.
Beans
Early bean harvesters were wrapped around the more powerful tractors of the time, such as Ford 7000s. Now, however, beans for the processing trade are harvested mainly by self-propelled machines.
Similar to the pea viner, a bean harvester reel uses tines to pick up the beans and puts them on to an elevator. A series of blowers take away the leaves and residue. Meanwhile, a debuncher separates out the bunches that would otherwise cause problems in the processing plant.
Ploeger’s B2140 is a good example of a modern harvester, with a 300hp engine and a 3m pick-up. Significantly, this full-width flow carries on through the machine, giving it a high capacity. Output is a steady 0.7ha/hour. The limiting factor here is the need to present a clean sample, which limits forward speeds to 5-7kph.
Trailed machines are typically used on beans for fresh presentation. Here, Oxboro faces competition from Asa, which is a subsidiary of Grimme. Larger trailed machines are used in the US for dried beans.
Spinach
Nowhere has the transition from hand picking to machine picking been more dramatic than in spinach harvesting. Ploeger’s enormous MKC 4TC has two sets of tracks, a demountable box and a 400hp Scania engine.
The harvester’s dimensions are in inverse proportion to the delicacy of the crop. A length of 14m, height of 4m and width of 3.8m means the machine hardly squeezes under the EU regulations.
Empty weight is 22t and the hook lift box has a capacity of 17t. These outsized proportions are driven by the need not to compress the crop.
At the other end of the scale is Tumoba’s harvester for baby leaf spinach. This covers between one and three rows and after the spinach is cut it is blown up to the packing area.
Strainer belts remove small objects such as beetles and stones. Similar to lettuce harvesters, the spinach is packed, labelled and even priced on the machine.