How to cut weed control costs with GPS implement steer
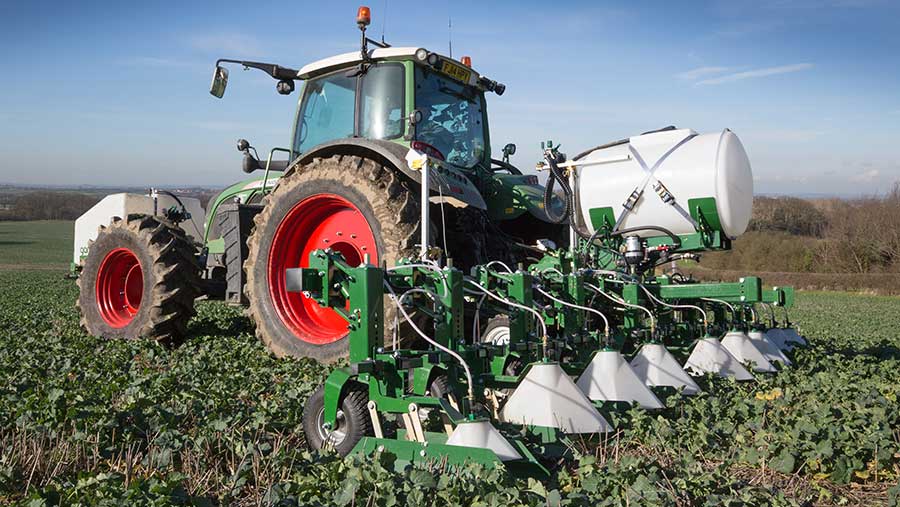
Ultra-precise GPS steering systems can undoubtedly improve the efficiency of field operations but is there room for improvement?
We look at a system that uses the implement’s position to steer the tractor.
When you’re doing fieldwork, it’s the position of the implement that you’re hauling up and down each bout that really counts.
So why do we mount GPS receivers on the roof of the tractor rather than on the bit of kit we’re running?
The answer is of course that it’s convenient. There’s no need to shift kit and cables when you swap jobs, there is plenty of electrical power on tap and up on top of the cab the expensive stuff is kept out of harm’s way.
See also: The robotic technology revolutionising weed control
Accuracy issues
This all makes sense if it’s just the tractor that you want positioned with pinpoint accuracy, but more often than not it’s actually what you’ve got hitched on behind that needs to kept on the straight and narrow.
On ground that’s anything other than billiard-table flat, trailed kit such as sprayers and drills will have a tendency to hang downhill. And, as often comes to light when you scrutinise pass-to-pass accuracy, any implement with soil engaging parts will tend to run at a slight offset to the centerline of the tractor.
The solution
Mount your receiver on the tackle and use that signal to control the tractor’s steering. That way the drill, sprayer or cultivator will remain rooted firmly in the centre of each bout while the tug may end up a few inches off to one side.
That’s the thinking behind Trimble’s TrueGuide system. A second satellite receiver (in addition to the one on the cab roof) is bolted to the implement and this provides a position feed that automatically steers the tractor to keep what’s being pulled on line.
The company reasons that the only way to directly influence the implement is to measure where it is and control it.
Adding the TrueGuide system to the standard Trimble Autopilot set-up costs between £4,000-£5,500 and, according to the firm, typically reduces the uncontrolled drift of the implement by more than 50% when compared with guiding the tractor alone.
Does it work in reality?
Farmers Weekly Farmer Focus regular Keith Challen has been using the TrueGuide system for the last year on Belvoir Fruit Farms’ arable unit.
He has been quickly convinced of its merits and the opportunity it presents for some pretty significant cost savings.
Farm facts: Belvoir Fruit Farms near Grantham, Leicestershire
Farmed area: 1417ha (3500acres)
Cropping: Winter wheat 506ha (1250acres), OSR 162ha (400acres), winter barley 162ha (400acres), let grassland 243ha (600acres), elderflower bushes 40ha (100acres) plus 300ha (740acres) woodland
Soils: Predominantly heavy clays
Machinery:
Tractors – Case IH Quadrac STX 535 and STX 440, JCB Fastrac 3230, Fendt 718, Case IH MXM190 and Fendt 514
Loaders – Manitou MLT 741 and Sanderson TL6
Combine – Case IH 9230 Axial Flow with 12.5m header
Sprayer – 6000-litre Challenger Rogator 655 with 36m booms
Staff: Keith Challen plus two others full-time and another two as required at harvest
However, it took a major change in the oilseed rape crop management policy and a shift to band-spraying to really highlight the necessity of such a set-up.
“I’d been becoming increasingly concerned about weed control in oilseed rape and what it was costing the farm. With resistant blackgrass on the horizon and no new chemistry in the pipeline I could see problems brewing,” explains Mr Challen.
“We were already sowing the rape in rows spaced 720mm apart with our home-built sub-soiler seeder so it made sense to look to band-spraying.”
The kit
After much pondering he settled on a unit built by Garford, with shrouded nozzles to cover the ground between the crop rows and others directly over the plants.
Two separate tanks – front and rear – carry different chemicals. Typically it’ll be a broad spectrum herbicide to deal with anything in the uncropped area and a fungicide or selective herbicide for the in-row mix.
Camera guidance and side-shift on the company’s Robocrop – mounted on the farm’s GPS-steered Fendt 718 – meant, in theory, everything would be kept on line.
“We had been using RTK-corrected GPS steering for a good number of years and we knew that it could genuinely provide sub-20mm accuracy,” explains Mr Challen.
Drift prevention
“But what I hadn’t quite realised was the amount our big 10-leg trailed sub-soiler seeder can drift off path. On decent side-slopes it could be up to 300mm out.
Of course by the time the crop was in the ground last season we could do nothing about it so our sprayer driver had to navigate his way through over 400ha of band-spraying manually. You forget just how draining that can be.”
Having sworn that that would never happen again, Mr Challen contacted Trimble specialist AS Communications to find out what could be done.
They suggested fitting a second receiver to the rape seeder set-up and, with a simple software upgrade to the tractor’s existing FMX controller, the TrueGuide system was up and running.
Pulled by the farm’s 535hp Case Quadtrac, the heavily-modified Simba Solo has the dome fitted just ahead of a liquid fertiliser tank bang in the centre of the frame.
Accuracy
As it works across banks and side-slopes the big tractor can been seen to be travelling on the uphill side of the centre line, ensuring the cannabalised FreeFlow tine-coulters place the seed in exactly the right place so that row spacing is a definite 720mm, pass after pass.
“The minute the band-sprayer got into the crop drilled with the extra receiver on the cultivator we could see how much more accurately it was working,” says Mr Challen.
“With the Fendt’s 420mm wide front tyres running on cotton reel rims and the rears set to match them at 2.88m centres, it might look a bit odd but it perfectly straddles all four rows. And because we know the crop is planted exactly where it should be – to within 20mm – there’s never any danger of the sprayer drifting off course.”
Cost savings
The savings in agrochemical use are impressive. Because the over-row nozzles are only targeting the planted area, they’re only covering 40% of the field.
With blanket autumn fungicide applications generally costing around £12/ha, the band-sprayer has the potential to shave up to £7.20 off that figure.
Add a selective herbicide – such as Kerb – into the mix at around £45/ha and you’re looking at a total saving of over £34/ha.
And then there’s what’s going on between the rows. The shrouded nozzles are generally used to apply a broad-spectrum herbicide, which is a huge amount cheaper (and arguably more effective against problem grass-weeds) than selectives. Also, it’s only going on to the uncropped area so there’s a 40% saving in its use too.
Set up costs
Of course there’s then the £50,000 purchase price of the Garford set-up to justify but given this results in a reduced workload for Belvoir’s new 6000-litre Challenger Rogator, Mr Challen believes it’s an easy case to make.
“The environmental and financial benefits are pretty clear and I’ve got a plan to make the Garford sprayer even more useful in giving the rape a targeted shot of nitrogen in the spring.
“The guards that run alongside each plant row cleverly lift the leaves so that the herbicide gets right up to the root base.
“I’m planning to mount a pencil jet to squirt liquid fert right along under the plants directly into the rooting zone. That way there’s no danger of scorching and we know the product’s being placed exactly where it’s needed. And that could all happen alongside other chemical applications.”
Inch-perfect results
But it’s not just the band-sprayer that’s being found other jobs to do. Last autumn, with all the rape drilled, the Trimble TrueGuide’s second receiver was shifted over to one of the farm’s two 8m Simba FreeFlows.
Running alongside each other, the difference was clear. Pass-to-pass accuracy was much more defined and overlaps were eliminated, doing away with the issues of increased disease pressure in areas where plant populations are too high.
“We need to be placing fertiliser and pesticides in a targeted way exactly where they need to be. By having everything inch-perfect that’s possible,” concludes Mr Challen.
“Having an implement-mounted receiver guiding the tractor makes so much more sense. It’s good for the environment and good for the bank balance – there is no downside.”