Why Lincs grower opted for US-style grain storage system
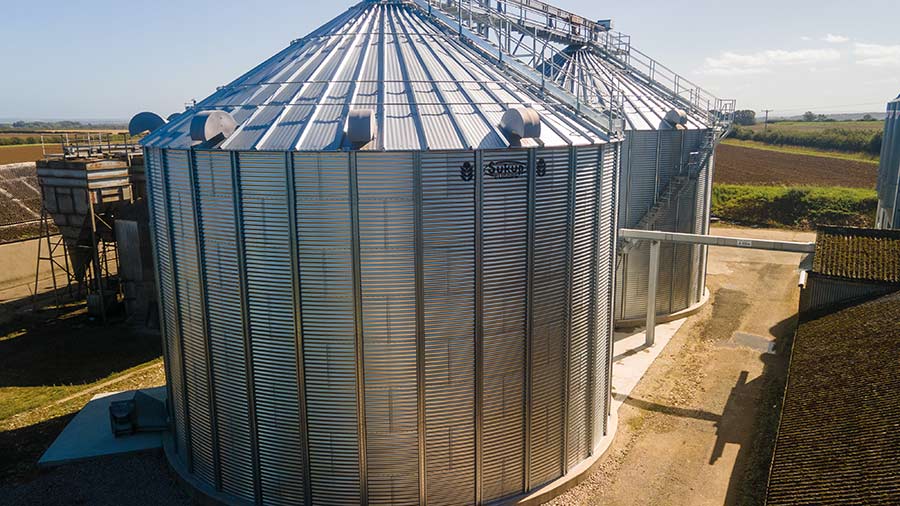
Grain storage and handling facilities installed in the 1970s and 1980s are reaching the end of their working life, and the latest generation of drying silos offer several advantages over new sheds.
Farmers looking to upgrade their grain handling facilities have two options, they can invest in a new shed or opt for silos as preferred by US and European farmers.
In recent years, bins and silos have fallen out of favour in the UK and Scott McArthur, sales director at grain storage and processing company McArthur Agriculture, believes part of this is down to historic experience with older bins that were not up to the job.
However, the next-generation US systems, designed for the European market, are far more labour efficient and offer several other advantages over multi-use sheds, such as ease of emptying and being vermin-proof.
See also: How home-made compost improves soil health for two farms
Farm facts
Limestone Farming
- Cropped area: 1,900ha
- Cropping: wheat (feed and milling), winter barley (feed), spring malting barley, oilseed rape, linseed, vining peas, sugar beet, and forage maize
- Soils: Limestone plus silty, clay loam
- Using about 2,500t of home-grown cereals for pig feed
One farmer who opted for the US-made drying silos is Stuart Meeson, farm manager at Limestone Farming Co, who oversees 1,900ha of cropping at Willoughton, near Gainsborough.
Crops include milling wheat, feed wheat, feed barley, oilseed rape and malting barley.
Quality crops such as milling wheat and malting barley are stored at the local co-op Woldgrain, while the feed wheat and barley is stored back on farm.
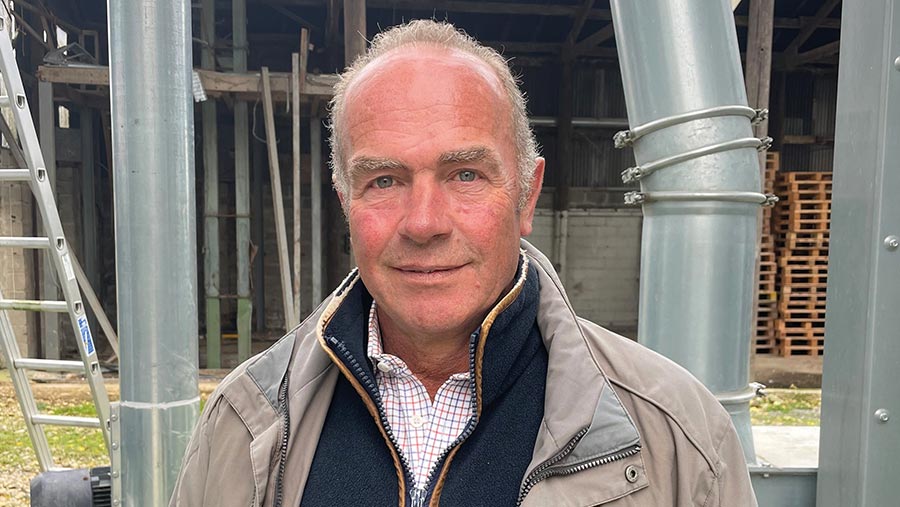
Stuart Meeson © MAG/Richard Allison
Home-grown cereals
These home-grown cereals are used by the Estate’s 750-sow pig enterprise, which takes most of the piglets through to finishing.
About 70t of feed is mixed each week using a mobile mixer, blending cereal with soya bean meal and rapeseed meal. About three years ago, the estate upgraded part of its cereal storage.
Mr Meeson explains that the previous setup consisted of an old Condor bin system comprising 40 individual 50t bins with difficult-to-clean drying floors.
“But they were not efficient and we were starting to see metal fatigue. They were installed in the early 1970s and were getting to the end of their life, so needed replacing,” he says.
Putting up a shed was ruled out, as there wasn’t space without having to knock down and move pig buildings.
Mr Meeson was also looking for a vermin-proof system that was quick and easy to unload for the weekly pig feed mixing.
He opted for two 1,000t Sukup silos that at more than 12m height have a much smaller footprint and comfortably fit the site.
The farm’s existing intake pit and 60t/hour elevator feeds the bins – the elevators also unload grain into an existing holding bin ready for the mixer.
He stuck with the existing intake, as it matches combine capacity with the farm’s Claas 8700 with 10.8m header.
One of the silos has stirrers and drying using an LPG burner and 37kW fan, and the second is for storage only with just an ambient 7.5kW fan blowing air through to condition grain.
During harvest, he has the option of loading wet barley into the drying stirrer silo which will take out 5% over about 10 days. This is then moved over to the other bin, leaving the drying silo ready for the wheat harvest.
He says with the old batch dryer, he would not dare exceed 18% grain moisture, but the in-silo Sukup system means he can cut up to 20% moisture.
Mr McArthur adds that in Scandinavia, they can take grain at 25% moisture, by opting for a few upgrades such as having extra stirrers and bigger fan capacity.
Less labour
One advantage that Mr Meeson has found is the lower labour requirements – cleaning takes two hours a bin which is much less than the smaller ones they replaced and drying is automated, so does not require staffing during harvest.
It is also labour efficient when unloading, farmers simply push a button. There is no need for a telehandler and it avoids double-handling grain.
The good airflow proved valuable this summer. “Grain was going in at 32C and its now below 10C,” says Mr Meeson.
One potential downside is that it reduces flexibility, although that isn’t a problem for Limestone Farming with just four varieties (Skyscraper, Dawsum, Champion and Typhoon) grown across 600ha, so Mr Meeson can easily fill the 1,000t silos.
Mr McArthur adds that the silo system is less suited for those farmers growing a lot of different grains and segregating varieties. “This is where a batch dryer comes into its own.”
Finally, he points out that as it’s classed as equipment, the system is tax efficient under the annual investment allowance and qualifies for the super deduction.
Drying Silo benefits
- Vermin proof
- Grain stirrers lower risk of hot spots
- Easy to unload – doesn’t need a telehandler
- Highly automated with reduced labour requirement
- Tax efficient – classed as machinery
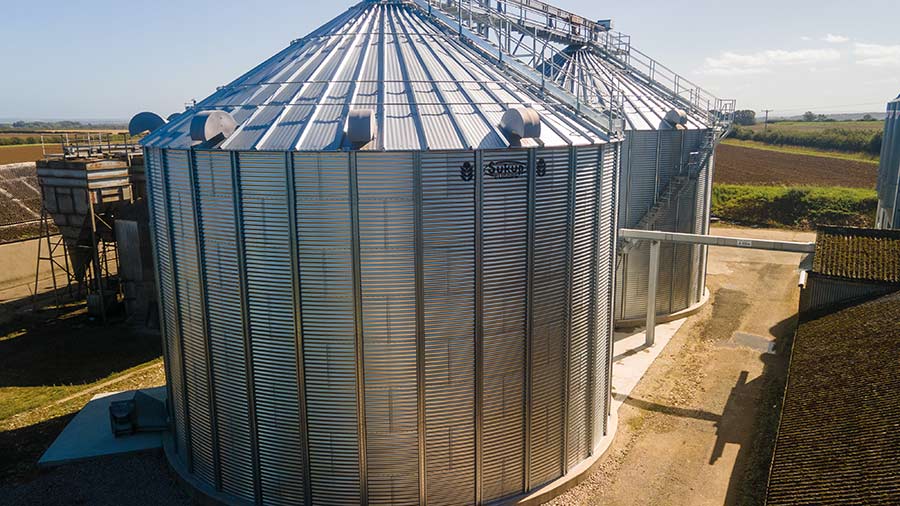
© Limestone Farming Co
Sukup Drying Silos – how they work
Grain is loaded into the silo from the top, and a spreader ensures that grain is spread evenly, rather than forming a cone. Once grain reaches 0.5-1m depth, farmers start the fan and heater to begin the drying process.
Air is heated 12-15C above ambient and enters the silo through the perforated floor and exits via the roof vent. The stirrers mix the whole area. This runs until grain reaches the target moisture content.
This is a slower process compared with batch and continuous dryers that use higher temperatures for shorter periods. Consequently, grain remains at lower temperatures.
“The grain temperature is lower and it is constantly stirred, so eliminating the risk of hotspots in the silo,” says Scott McArthur.
The silo system typically uses air heated to 35-40C, compared with 120C for hot air drying systems.
Malting barley
Mr McArthur sees these silos having a role for Scottish malting barley growers, as they can be filled rapidly, so avoiding any bottleneck at harvest.
The low temperature method is ideal in helping farmers maintain germination, as UK maltsters have a minimum standard of 98% germination.
“Many Scandinavian malting barley growers use the system to dry and store their crops,” he says.
Furthermore, the silo system can cope with grain at 25% moisture and has proven itself in challenging harvest areas such as Finland and Sweden, which are similar to Scotland.
Once dry, it then switches to the cooling stage. Farmers can run fans to keep grain conditioned and stirrers will avoid compaction. Silos without stirrers may only cool and condition grain.
When it comes to unloading, one advantage is that it happens at the push of a button using an auger, and there is no need for a telehandler.
For Mr Meeson, his silos are filled and emptied using 60t/hour Skandia Elevator grain handling equipment connected to the existing shed, which houses the pit and holding bins.
Renewable energy
While Mr Meeson uses LPG burners, Mr McArthur says soaring energy prices mean there is increasing interest from farmers looking to use renewable energy.
“The 1,000t silo only needs a 217KW heater and it can be coupled with a 300KW hot water radiator, so could fit in with renewables. This reduces energy bills and breaks grain drying’s dependence on fossil fuels,” he says.