Low-cost system converts remote sheds into grain drying system
A low-cost grain drying option for locations where there are no built-in facilities is promised by the “horizontal drying system” conceived by a seed and cereal engineering company in north Lincolnshire.
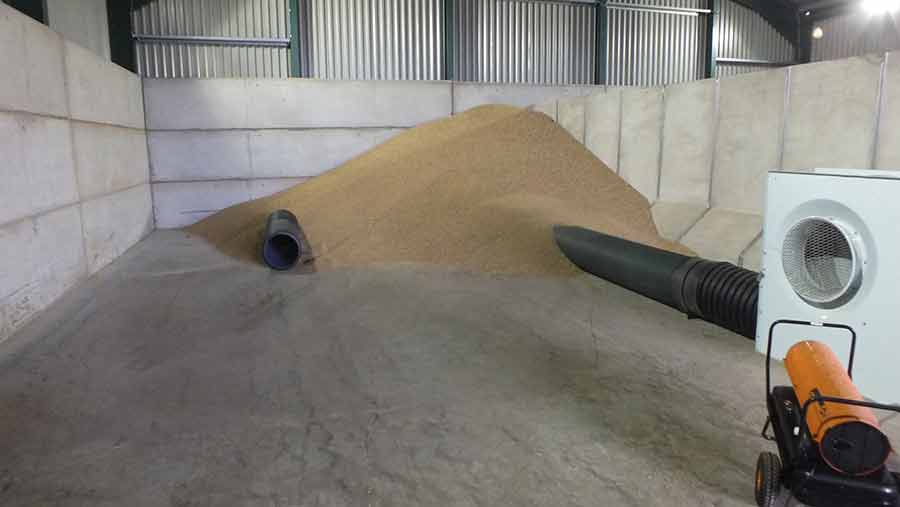
Perforated laterals with the correct density and size of holes for the required airflow and a semi-portable fan provide on-floor drying at relatively low cost
According to Robin Mumby of Plot Feeds, the system enables drying of bulk grain at an acceptable rate and cost in a floor store without fixed installations by delivering warm air through lateral plastic tubing via a portable fan and heater.
See also: Grain storage clubs offer cheaper alternative to on-farm options
“It’s not something that can replace a large bulk store with a fully installed drying system,” he points out, “but with capacities from 30t to 194t per lateral, we can get up to about 770t in total with different configurations.”
How it works
The idea is to lay the plastic tubes – which have a perforation size and density chosen to give correct airflow – 3m apart, leaving space between for a standard telehandler bucket to gain access for out-loading.
A coupling is used to connect a semi-portable Kongskilde axial fan to each lateral in turn, with a portable heater, such as one of the company’s oil burning units, positioned to provide a source of heat.
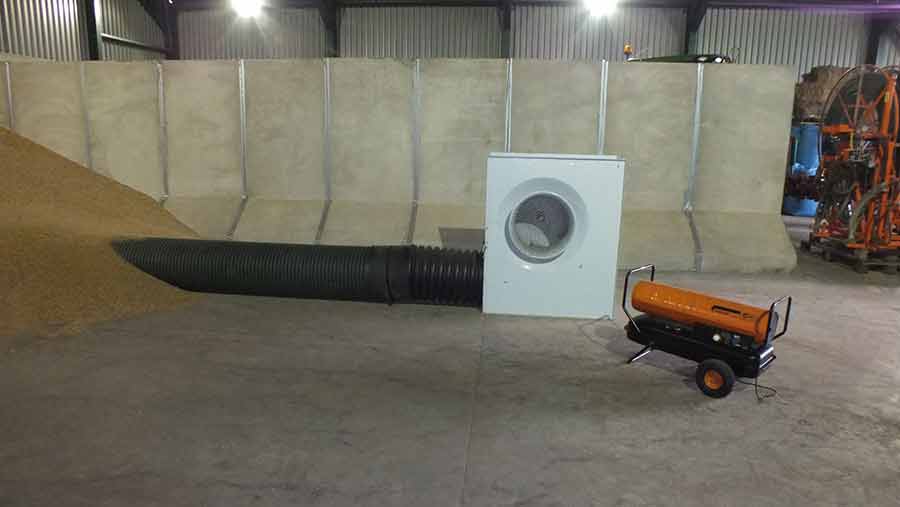
An oil-burning heater provides hot air when ambient conditions are inadequate for drying
“The fan would be run on each lateral for two to three days at a time, blowing air through the bulk heap levelled off 3m deep,” explains Robin. “That means each fan can service four to five laterals in rotation during the course of a week.”
This approach has been trialled at I&J Mason Farming in Lincolnshire to check that the calculated fan size and lateral specification works in practice. In this instance, the laterals were spaced 3.5m apart and covered in a 2.5m depth of grain.
“The farm’s winter barley came off the combine almost dry so it needed only ambient air to condition it,” recalls Mr Mumby. “But the spring barley came in at 17.5% moisture and the 218t pile needed drying down to 14%, which the system achieved over a 30-day period.”
Fuel use
Fuel consumed by the heater amounted to 750 litres – so about 1 litre/% [check this] of moisture removed.
Grower Ian Mason says the system was easy to use and adds he plans to equip more stores for drying in this way.
Mr Mumby adds: “This low-cost approach is attractive to growers who want to retain the flexibility of a solid-floor building.
“People have tried drying using vertical pedestals, but it’s not successful from high moisture levels and you can’t add heat because they work on the principle of sucking air through the grain.”
Plot Feeds has put together several packages of perforated and plain ducting, and a choice of five fans to suit different run lengths, from 9m to 27m. Average capital cost works out at £13/t for a 400t installation.