How a Lincs farm dries grain cheaply without fossil fuels
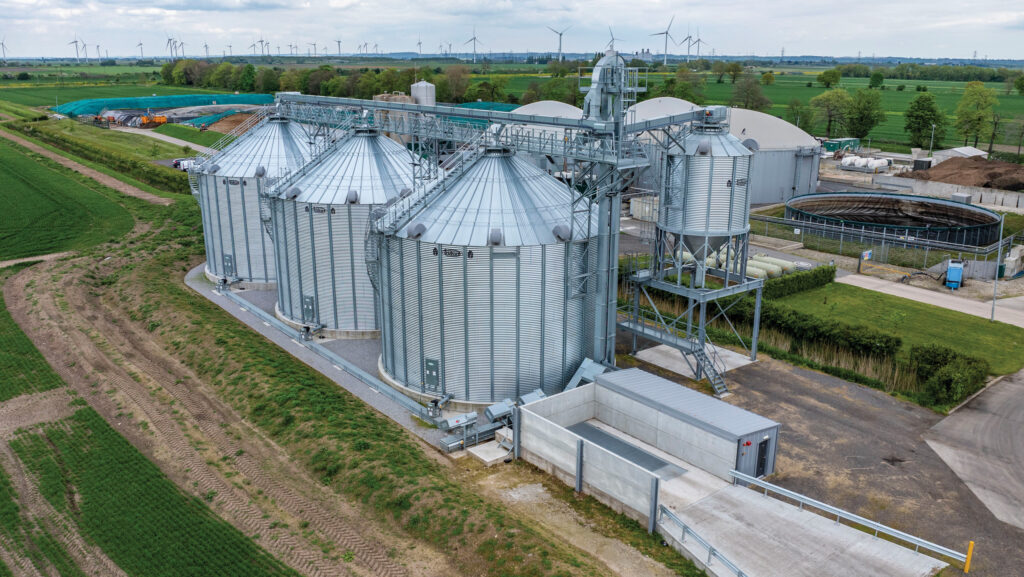
An expanding cropping area meant Rockscape Farms needed to invest in extra grain storage.
By opting for drying silos, the farm is using surplus heat from electricity generated by an anaerobic digestion plant to dry grain.
In addition, the highly automated system has reduced labour and machinery requirements throughout the year, freeing up staff for other tasks like cultivating ground and drilling cover crops after the combine.
See also: Why Lincs grower opted for US-style grain storage system
Storage
Farm business manager Aaron Kew recalls that storage was getting tight and then the company purchased extra land, which meant more capacity was needed for the various crops grown across the 2,424ha of land.
In addition, the farm had storage on four off lying sites of varying quality. They were basically sheds with concrete floors and no drying capacity.
Therefore, their use relied on combining crops when fully dry, which is a challenge in a catchy year like last summer.
There were also the logistics, and Aaron points to one site taking an hour round trip in the telehandler.
“We could be doing 38 trips a year with a telehandler loading and unloading, which adds up to quite a lot of time.”
So the company took the opportunity to bring grain drying and storage to one location and increase it to nearly 10,000t consisting of:
- 5,000t across four drying floors
- 1,000t flat concrete floor
- 960t across eight x 120t bins for minority crops and home-saved seed.
New storage came in the form of 3,000t Sukup drying silos.
Sukup drying silos – how they work with renewable heat
Grain is loaded into the silo from the top, and a spreader ensures that grain is spread evenly, rather than forming a cone.
Once grain reaches a depth of 0.5-1m farmers start the fan and heater to begin the drying process.
Air is heated 12-15C above ambient and enters the silo through the perforated floor and exits through the roof vent.
The stirrers mix the whole area. This runs until grain reaches the target moisture content.
This is a slower process compared with batch and continuous dryers that use higher temperatures for shorter periods. Consequently, grain remains at lower temperatures.
John McArthur, managing director at McArthur BDC, says it typically dries grain at 0.5% per day.
Surplus heat
Another key reason for centralising storage at North Moor Farm is to utilise surplus heat from the anaerobic digestion plant, run by the farm’s sister company, Rockscape Energy.
The plant produces biogas which is supplied into the main grid.
However, to supply gas 24/7 means having a backup 1.2mW combined heat and power plant, effectively an engine that runs off the biogas.
Aaron explains that this is because electricity is constantly needed to power the systems that allow gas to be injected into the grid.
The heat is also used to pre-warm the feedstock being fed into the digester to kick-start the process.
But in summer much less heat is needed, so there is plenty for drying.
John McArthur, managing director at McArthur BDC which supplied the grain equipment says the Sukup silos are ideal for using this heat.
They use air heated to 12-15C above ambient temperature rather than the much hotter approach, with batch and continuous dryers.
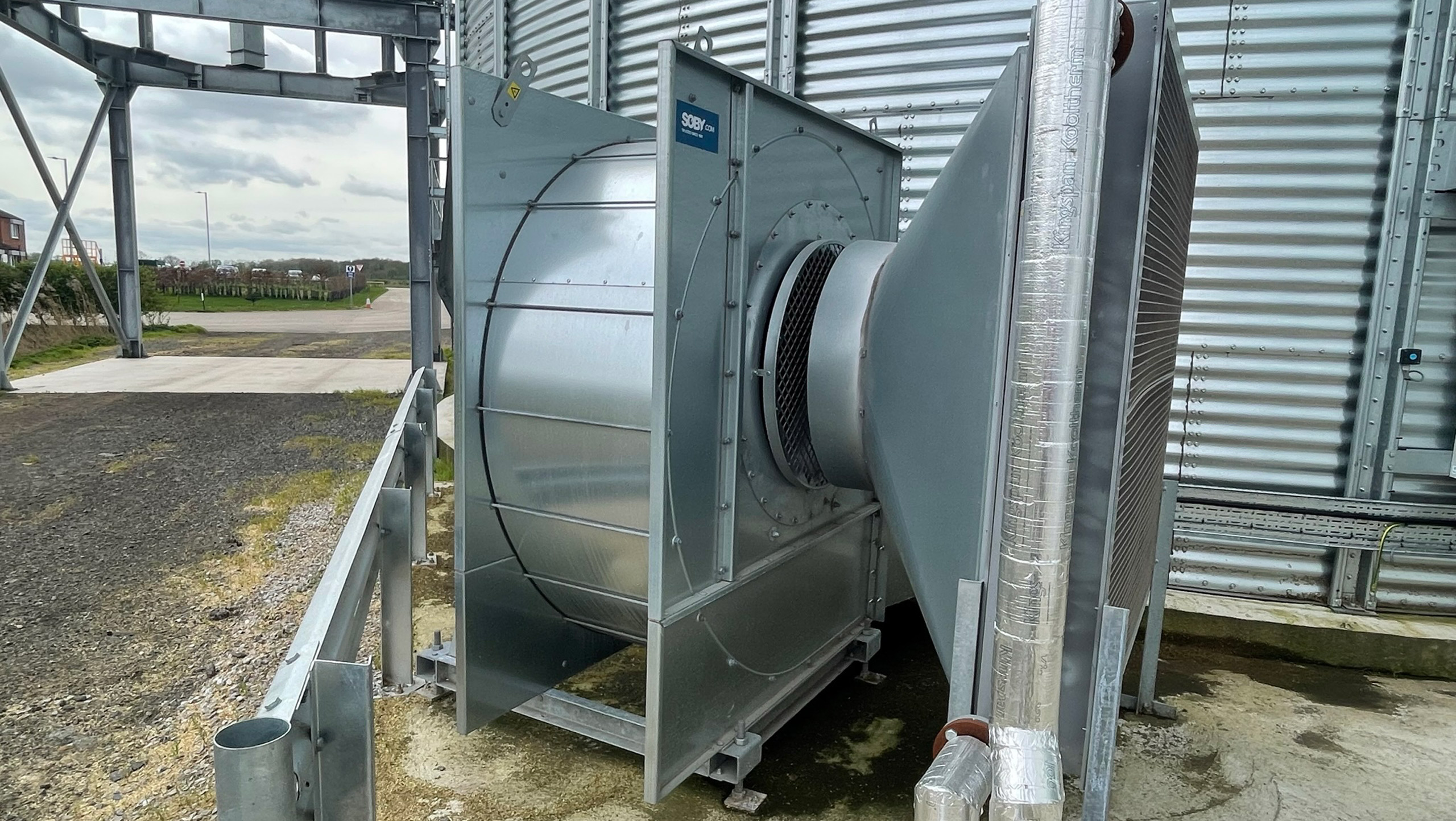
Hot water radiator at fan intake © MAG/Richard Allison
Benefits
Using the green heat and power, drying grain from 19% to 15% moisture costs about £2.87/t.
John says this is much cheaper than using a mobile/conventional dryer, which costs about £5-£6/t using oil and mains power.
Aaron says one key benefit of the cheaper drying is that it enables them to get the most from their combine and avoid having to invest in a second one.
Their own New Holland CR9090 with 40ft header does 80% of the area, with the rest done by contractors.
The cheaper drying capacity means Aaron can extend the combining window with more hours a day.
So by cutting crops at a higher percentage moisture, they can avoid the cost of buying a second combine.
“All the wet stuff went into the silos last harvest. Effectively, areas cut in the mornings and evenings went into the silos, with the rest tipped onto the drying floor and dried using LPG.”
Labour-saving benefits
The highly automated system has improved labour efficiency, as it needs one man less to keep pushing grain up with a telehandler.
“You just press a button, tip and then you are away. It means we have an extra person free to do mowing or cultivating ground after the combine.”
Aaron estimates that the automation enables three times the tonnage to be managed for the same man hours.
The drying silos are being used to dry feed and milling wheat, malting barley, and oats.
Last year, Aaron used the system to successfully dry grain maize and this year, they have increased the area to 300ha.
The cheaper drying means grain maize is now a viable break crop, as drying costs can be substantial.
Aaron’s aim is to fill the silos twice this harvest. They will be used for the cereal harvest, and the dry grain will be sold and moved before the grain maize harvest begins.
He then plans to fill the silos again with grain maize which is harvested in October, so using cheap drying twice.
New handling system setup
The new handling system starts with two Skandia Elevator 100t/hour intake conveyors, which can cope with two combines running flat out, thereby future-proofing the installation.
The conveyors automatically switch on when grain is tipped and switch off when it’s all in the chosen silo.
The high level of automation means tractor drivers don’t need to leave their cab and the pit is emptied well in time for the next load.
In fact, farm business manager Aaron Kew can monitor the whole system remotely using the app on his phone. He can also remotely load lorries.
Rockscape Farms has three 1,000t Sukup silos, which are filled at 200t/hour by the intake conveyors and emptied at 100t/hour with an overhead hopper bottom silo which allows a 29t wagon to be filled in four minutes.
The modular system means more storage can be easily added.
Aaron says they are looking at adding two more in this bank of silos then perhaps another five on the other side.
When it comes to unloading, one advantage of the highly automated system is that it happens at the push of a button, and there is no need for a telehandler.
There is also no need to spend 10 mins sweeping up, because once the sweep auger has been round, it leaves about 1cm of grain across the silo bottom, which can be quickly swept to the out-take chutes.
Ideal for heat plant
The silo system uses air heated to 35-40C, compared with 120C for hot air drying systems.
This is achieved by having radiators fitted in front of the intake fans.
This makes these silos ideal for harnessing the surplus heat from the combined heat and power plant.
Once dry, it then switches to the cooling stage.
Farmers can run fans to keep grain conditioned and stirrers will avoid compaction. Silos without stirrers may only cool and condition grain.