Cereals 2022: Silo drying cheaper for grain storage upgrades
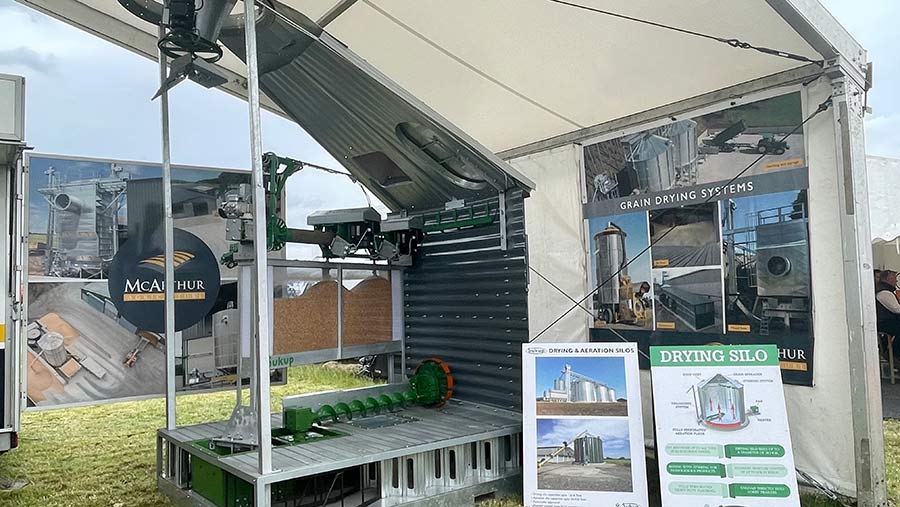
Growers looking to upgrade their grain-drying and storage facilities could save money by opting for a silo-based system that is proving popular in northern Europe and Scandinavia.
UK growers have traditionally opted for sheds with drying floors, while their northern European counterparts have favoured silo-based systems.
See also: Tips to achieve successful long-term grain storage
John McArthur, managing director at grain storage and handling company McArthur Agriculture, believes part of this is due to historic experience with silos, with older bins that were not up to the job.
In addition, farmers like the idea of multiple-use sheds. “Therefore, silo systems have never caught on in the UK,” he says.
But he reports increasing UK interest in recent months, as growers see the benefits of silo systems like that from US manufacturer Sukup.
The main benefit is that it is the cheapest way to deliver new storage with drying and cooling. “It’s the most cost-effective system to deliver all three,” he says.
Depending on the situation, he estimates that the silo system has a 10-20% lower capital expenditure than a grain store with drying floor, heaters and stirrers.
In terms of running costs, they are similar, but the silo delivers extra control of heated air, he says.
This gives growers the certainty of drying as seen with hot air dryers, along with the convenience of a floor drying system.
Another benefit is the more homogenous heap of grain, being loaded vertically and the fact it is much easier to mix the whole heap.
The silo system can cope with grain at 25% moisture and has proven itself in challenging harvest areas like Finland and Sweden.
Finally, Mr McArthur points out that as it’s classed as equipment, the system is tax efficient under the Annual Investment Allowance and qualifies for the super deduction.
How does it work?
At harvest, grain is put in the top of the silo and is distributed using a spreader. Once grain reaches get 0.5-1m depth, farmers start the fan and heater to start the drying process.
Air is heated to 40-45C and enters from the perforated base and exits the silo via the roof vent. The stirrers mix the whole area.
Once dry, it then switches to the cooling stage and he says it offers good cooling control.
When it comes to unloading, one advantage is that it happens at the push of a button and there is no need for a telehandler.