How farmers can benefit from growing hemp market
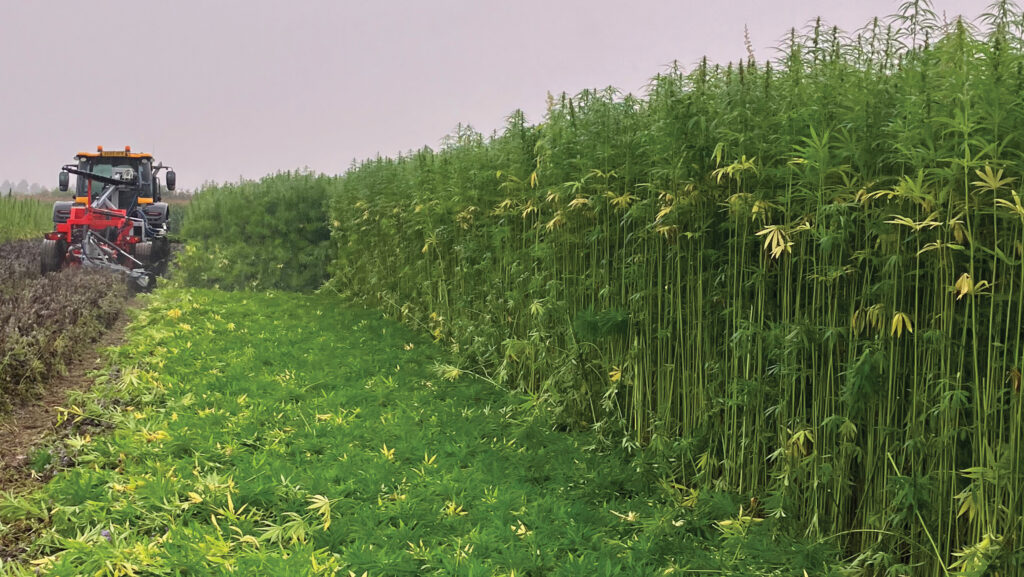
Fast growing with break crop suitability, hemp can produce high-value fibres in a low-input system, with low nitrogen requirement, and minimal chemicals.
But one of industrial hemp’s major downfalls is that farmers must be licensed to grow the crop, alongside a lack of direction for end markets.
However, as demand shifts and there are changes in licensing policy – which includes a proposal for emergency licensing in the face of failed spring crops – the tide could be turning for hemp in the near future.
Hemp has shown impressive potential for carbon sequestration, estimated to fix up to 22t/ha of carbon dioxide, which is significantly more than pasture, wheat or alternative crops like miscanthus at about 4t/ha, 8t/ha and 15t/ha respectively.
Hemp has the capability of outcompeting any other commercial crop when it comes to carbon storage, including woodland.
See also: Why flax for fibre could reappear in arable rotations
Hemp has also been shown to improve soil health and structure; helping to mitigate the effects of erosion, flooding and drought.
Additionally, it can have a net positive effect on biodiversity, and importantly, on the yields of following crops – for example, winter wheat.
Producing a strong, versatile natural fibre, hemp is a solid contender for the domestic market, with export trade potential, too.
More sustainable than other natural fibres such as flax (a sustainable natural fibre crop heavily imported into the UK from Northern Europe) and bamboo, hemp has attracted the attention of businesses looking for UK-supplied options.
Growing hemp
Industrial hemp is grown from EU/UK-approved cannabis sativa seed varieties of less than 0.2% tetrahydrocannabinol (THC) – the naturally occurring medicinal compound found in cannabis plants, of which hemp derives.
Bred for either natural fibre, seed, or oil, hemp is drilled in May, at the same time of year as maize.
It should be drilled no more than 2cm deep into a warm, fine and level seed-bed with a bit of moisture and an application of nitrogen.
Higher seed rates are advised to achieve high plant density for every square metre; this is crucial to outcompete weeds and ensure finger-thick stems, which contain higher levels of the all-important bast fibre.
Thicker, woodier stems have higher processing costs.
“It must be drilled into a fine and level seed-bed,” advises farmer and NFU crops board appointee, Heather Oldfield.
“Hemp has shown to perform best when drilled with a combination drill. Timing of drilling is also important, as is a pre-emergence spray to achieve a clean seed-bed.
Hemp’s first 10cm of growth is delicate, but it quickly develops an expansive, fibrous tap root network – metres long – which is very efficient at capturing carbon.
“At this point it appears to stop growing, but it hasn’t, it’s putting all of its energy into root growth, before continuing above ground development,” she adds.
While hemp can be grown on a range of soils, when produced for natural fibre it should not be grown on stoney soils, as stones pose a fire risk at processing.
Yielding 5.5-7t/ha in total fibre – comprising high-value bast fibre on the outer layers of the stem and a lower value woody core – hemp has a low appetite of about 70kg/ha of nitrogen (N), up to a maximum of 120kg/ha.
“Don’t cut corners; while it is a low-input crop, seed is expensive, so make sure you soil test, and if you are using manures, test them too,” says Heather.
Hemp’s natural chemical compounds (cannabinoids) have a pesticide-like effect and disease risk, at present, is negligible, so there’s no need for tramlines in the crop.
Hemp is ready to cut in as little as 100-120 days (August). The crop is mown without a conditioner or with a specifically designed three-bar cutter and then left to dew ret – a natural process where the cut crop lies on the field for four to six weeks, allowing its fibre bonds to be broken down by soil microbes and moisture.
Once complete (October), it is then baled as retted straw, and stored ready for processing.
Hemp draws in moisture so requires dry storage where it can hold its quality.
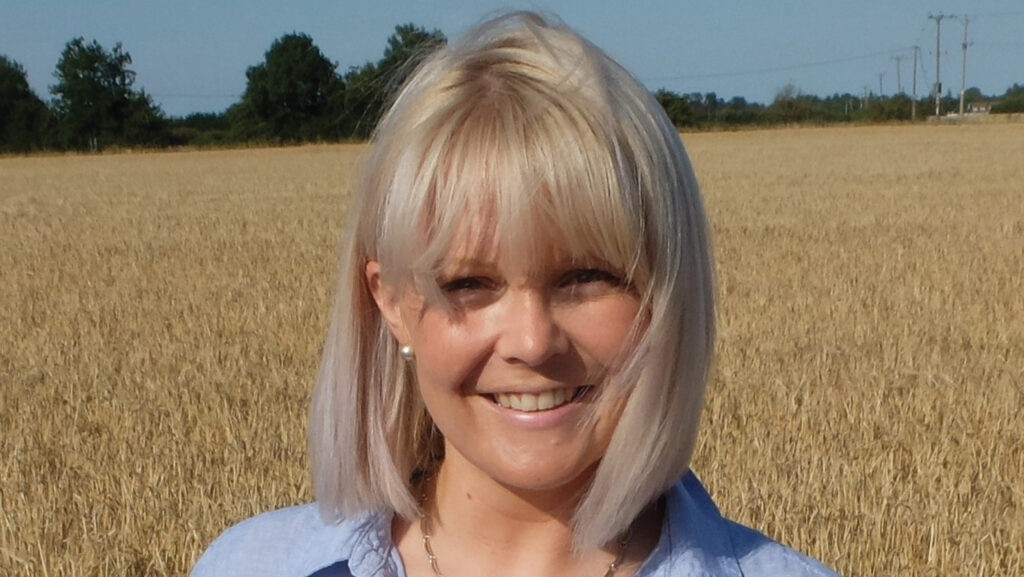
Heather Oldfield © NFU
Potential
Conversations around natural fibre use have seen a step-change in the past 18 months, says Heather.
“Demand for natural UK fibres is building; people are wanting to make climate-positive changes, and companies are looking at their environmental credentials.”
Hemp-based insulation can be used in buildings, and there are also opportunities in motorsport.
For example, in GT4, new regulations require some additional aerodynamic surfaces to be manufactured using completely natural fibres and/or natural cores.
Formula One is exploring co-weaving natural fibres with carbon fibre to produce components, like wheel arches, that flex or break into large pieces on impact instead of shattering.
“From a health and safety and operations perspective, natural fibre is hugely advantageous,” says Heather.
Lighter weight, natural fibre and hybrid components could also prove valuable to commercial vehicles and transport.
“When processed you will get a percentage of long fibre, medium/short fibre, shiv and dust,” explains Heather.
“To make the crop financially viable, from a farm perspective, you have to have a market for all parts of the processed plant.”
Hemp in the Centre for High Carbon Capture Cropping (CHCx3) project
CHCx3, a 19-partner, four-year collaborative project led by Niab, aims to build robust carbon market frameworks and agronomic knowledge for a selection of crops.
It focuses on crop species which may have significant importance to agriculture in future, says Heather Oldfield, who leads hemp and flax crop improvements within the project.
The consortium represents the whole supply chain; researchers, breeders, processors and end users.
With six large, replicated trial sites, it is collecting carbon, agronomic and commercial data. “On one farm we are using flux monitors to monitor both above and below ground emissions,” she says.
“The sites produce enough fibre to send to businesses along the supply chain, that can test for differences between hemp varieties that are relevant to specific end uses. For example, strength testing for automotive composites, or drying potential for fabrics.
“The crop improvement aspect of the project is looking at disease susceptibility, maturity and rotation suitability, as well as farm and soil type.
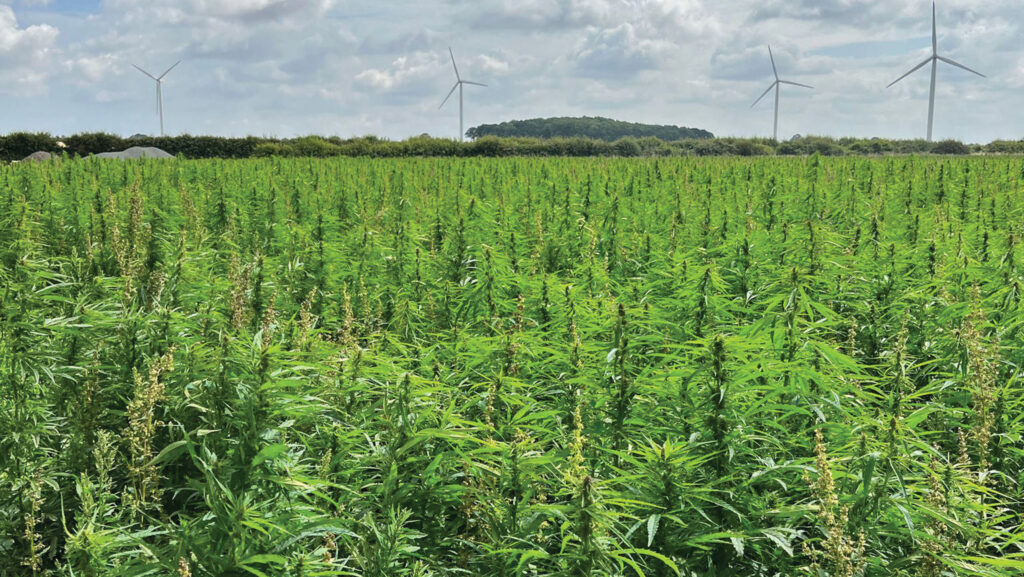
© Heather Oldfield
“Importantly, the project’s end-use insights will help to foster new, sustainable multistreamed revenues for farmers – it’s something to get excited about.”
A year into the project and preliminary trial results are filtering back.
“The results will help us build detail around which varieties produce the most quality fibre and which produce more shiv – something we’ve not had from the UK before.”
An interesting development is the regular presence of high-profile businesses and organisations at meetings.
“I never thought I’d be talking to key stakeholders for the automotive, transport and aerospace sectors,” says Heather.
“That level of interest from those stakeholders is very exciting, not just for the project but the opportunity it could create for farmers.”
Case study: Nick Voase, Inn Carr Farm, East Yorkshire
Nick Voase has been growing hemp in East Yorkshire since 2002 and processing it since 2007, which makes him a pioneer of sorts.
Starting with 16ha of hemp on his 240ha arable and potato farm, he was already growing niche crops like borage, lupins and evening primrose, so was familiar with incorporating alternative crops into his rotation compared to second wheat, barley, and oilseed rape, which have never done well on his farm.
By 2009, Nick stopped potato production after disastrous flooding, a severe farm fire and closure of the contract processor.
He then upscaled his hemp acreage, invested the insurance money into on-site processing facilities, and developed his own markets.
Today, his farm grows about 115ha of hemp, with contracted farms growing an additional 100ha. He also buys in around 40ha of baled straw, and processes it all on-site.
The crop is sown in early May into a good tilth at 40kg/ha (2cm deep) using a Vaderstad Rapid seed drill, followed by 90kg/ha of nitrogen.
Nick tried direct drilling, but it firmed the seed in too much, leading to thinner and more sporadic germination. This allowed weeds to get the upper hand, resulting in fewer but thicker stems, which are more expensive to process.
“There are no chemicals approved for use in hemp in the UK,” says Nick. “So we have to do all our weed control before the seed goes in. We must get establishment right to get the plant density and the fibre yield.”
Pest control and diseases are not major issues as cannabinoids act as a natural repellent.
“Sclerotia can mildly affect the crop – but we have usually mown before that disease would typically become a problem in any of our crops.”
Retting and harvest
The crop is typically ready to be mown in August using the farm’s self-built cutting machine, which has three staggered cutting bars; one at ground level and then at 1m and 2m heights.
It cuts and chops the hemp into five shorter sections which improves the mowing efficiency and the retting process. Retting is very much about observation.
“The straw becomes darker as the process goes on – starting off bright golden, deepening in colour,” says Nick. “We will harvest once it starts to lose that golden colour, which is around four to six weeks after mowing.”
Harvest takes place around mid-September, with the retted straw collected and square-baled.
Yields average 5.5t/ha (dry, retted) and 25% fibre, increasing up to 28% in Nick’s best performing crops.
“We want to bring it in at below 17% dry matter, customers want it at 15%, but when the weather’s been dry we have brought it in as low as 8%.”
He then stores the bales in a shed with passive ventilation.
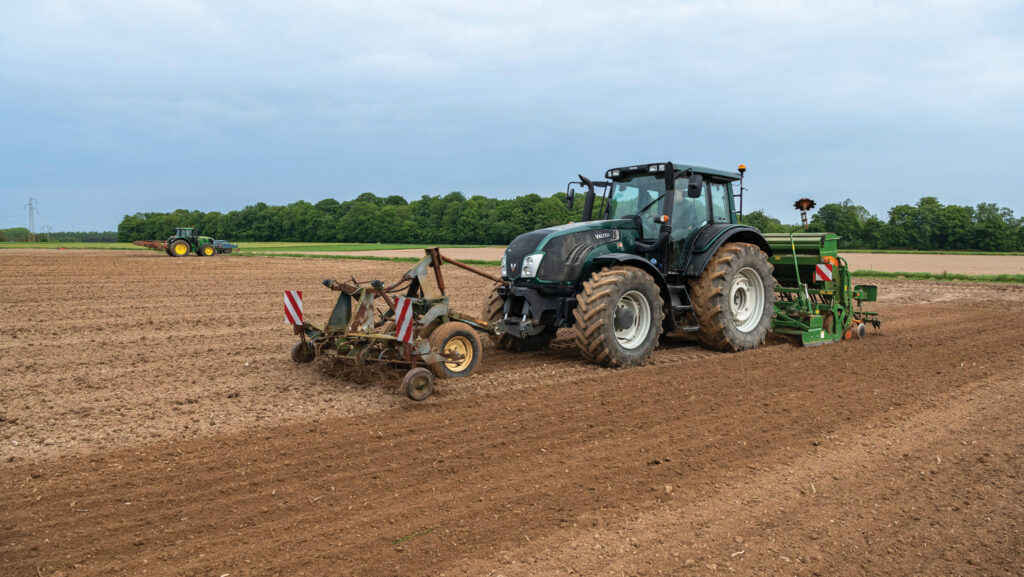
© Andia/Alamy Stock Photo
Processing and markets
Nick’s company, East Yorkshire Hemp, undertakes the mowing and harvest before he processes it into fibre at his on-site facility.
The retted bales are fed into a decortication machine, which crushes the stems, mechanically separating the fibrous material from the woody core.
It then refines the fibre through a cleaning process – removing shiv and dust – before baling it into 400kg bales. The separated shiv is graded, which determines its end use.
Nick sells high-value clean hemp fibre to several businesses, which make various sustainable products including bed mattresses, upholstery fabric, and building insulation.
He has also created his own-branded products, using the shiv to make animal bedding and briquettes, he also supplies hemp as a straight material for hempcrete.
He is now working with more advanced composite material companies considering hemp for high-performance products like automotive parts.
“Hemp offers a renewable and sustainable alternative to materials which have a poor environmental profile and/or are hazardous to health,” says Nick.
Licensing
Although Nick has been licensed to grow hemp for many years, it can be a time-consuming and frustrating task for new growers.
“Be prepared to repeat yourself,” he advises. “The Home Office does not recognise Rural Payment Agency field numbers – you will need to map your farm using grid references.”
For those reasons alone, he advises starting early. “Know what you need to provide, gather the information you need and map your farm before the application window opens, then apply for your licence as soon as the window opens.”
He says the last thing growers want is to miss the window for ordering seed.
Lessons
Hemp has paid off as a valuable break crop on the home farm, lifting average wheat yields and contributing to the soil’s 6% organic matter content, but Nick doesn’t shy away from the challenges that a homogenous rotation creates.
“We grow most of the hemp in a rotation with wheat, but I’d like to have a more diverse rotation because we are starting to see problems like blackgrass reappear.”.
His aim is to have a six-year rotation of peas, hemp, rye, flax and wheat, with suitable cover crops over the winter period.
This will not only improve soils but also assist in combating weather, disease and pest challenge across the board, while improving biodiversity.
Nick is also a CHCx3 (Centre for High Carbon Capture Cropping) trial farm, growing 10ha for the project.
“It’s great to be involved in the CHCx3 trials, which are improving the industry’s knowledge of the crop and its potential for carbon capture, soil improvement and biodiversity gains.”