Video: Hands-Free Farm turns to drilling after good harvest
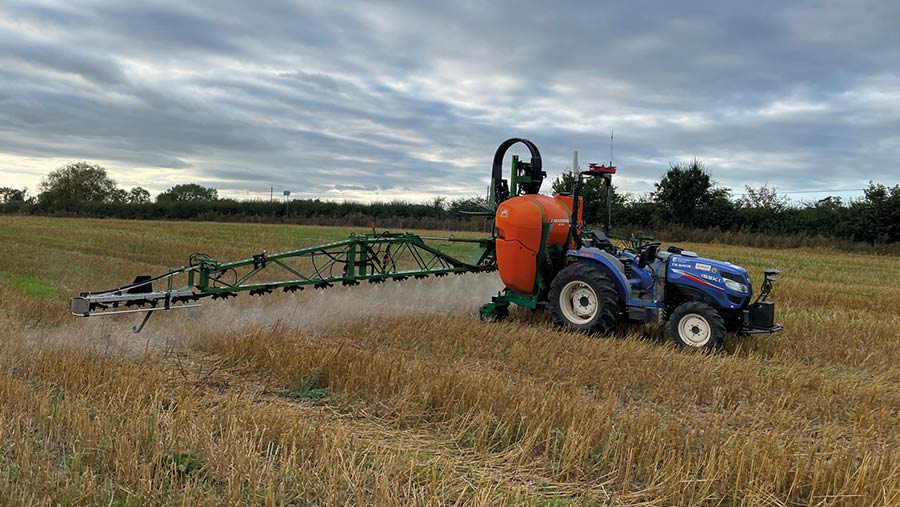
The research team behind the Hands-Free Farm, which aimed to autonomously drill, manage and harvest arable crops without operators in driving seats or agronomists on the ground, has successfully delivered above average yields in a challenging season.
After the success of this year’s harvest, which saw wheat yield nearly 9.3t/ha, drilling is now under way for its ultimate season.
Run by Harper Adams University, in conjunction with Precision Decisions and Farmscan Ag, based at the Agri Epicentre, the project is the successor to the initial Hands-Free Hectare initiative.
This was the first of its kind to remotely grow and harvest a crop across its 1ha site and highlights how automated machines can shape the future of farming.
Watch the video of harvest in action read the rest of the report below.
See also: Video: Electronic robot weed zapper cuts inputs and carbon
Simple, lightweight tractors kitted out with GPS technology help reduce compaction risks, thereby improving soil health.
In addition, the research team are now using variable-rate applications, drone technology and flower margins to work more precisely and in an environmentally friendly way across the project.
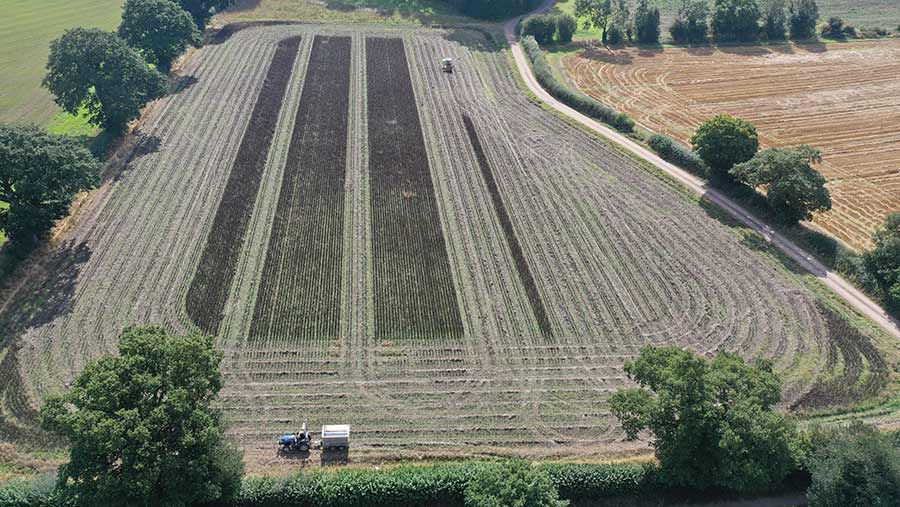
© Harper Adams University
How the machines work
Machinery operation and control has evolved considerably since the start of the project in 2016, explains the university’s mechatronics researcher and unmanned aerial vehicle pilot, Jonathan Gill.
What started off with open-source drone technology to automatically drive the range of Iseki tractors and a combine has progressed to custom-built hardware control systems which precisely plan and communicate routes.
Two fully automated Iseki tractors are currently in operation for this year’s drilling campaign, with one manning the drill and the other discing and rolling.
“When drilling a field, the user must select the drilling file in an app on a tablet, which is used as the communication medium between the machine and the field.
“When loading route plans, the tractor is then positioned into the initial starting block, where it begins its programmed operation,” says Mr Gill.
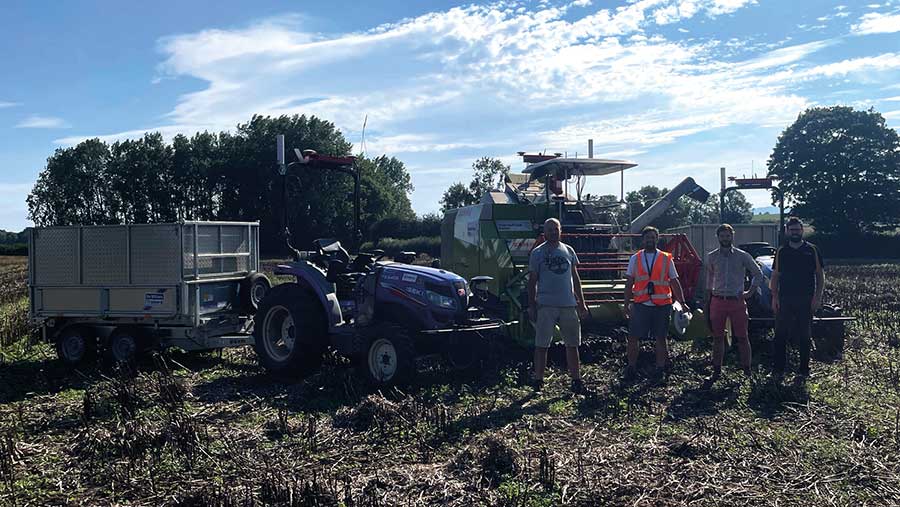
© Harper Adams University
Variable-rate drilling
A smarter, more precise approach is being employed to plant this year’s crops, with the combined use of soil conductivity data and agronomist mapping to variable-rate drill.
A 1.87m Simtech direct drill will be used to variably drill 6ha of Extase winter wheat and 5ha of winter beans, with the remaining area planted to a new spring barley variety from KWS (yet to be announced).
“It’s not about large machines, high horsepower and fast speeds, but working smaller, smarter and at a speed that conditions allow,” says Mr Gill.
The smallest of the tractors weigh just 1.3t with 37hp, while the largest weighs 1.8t and has 49hp.
“Lighter machines will allow farmers to improve soils without large-scale kit exerting huge weight and pressure on land. This will ultimately improve farm economics by reducing the requirements of labour and fossil fuels,” he explains.
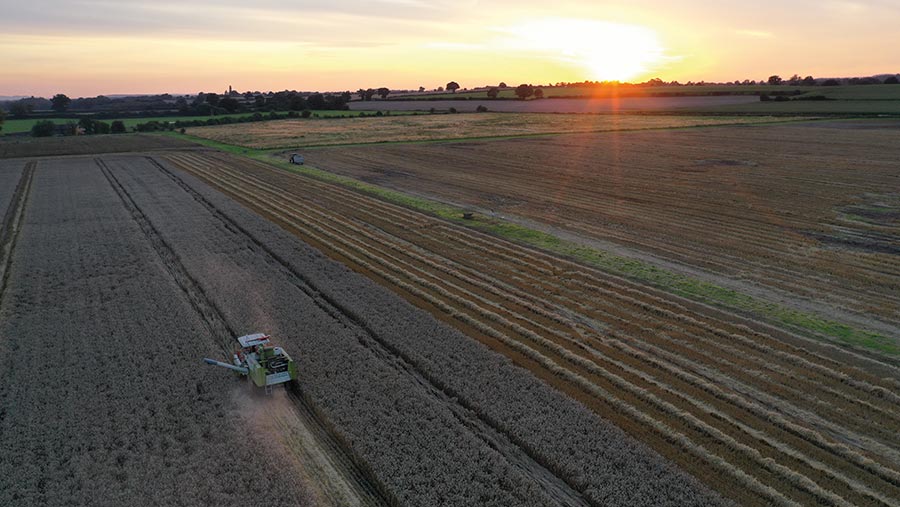
© Harper Adams University
Controlled-traffic farming (CTF) is also being used, but the awkwardly sized drill width makes this somewhat of a challenge. With such lightweight tractors being used, Mr Gill questions whether the known convention of CTF is required.
Furthermore, in a bid to increase beneficial insect populations, the outside margin of every field will be planted to a cover crop and wildflower pollinator mix.
“We are planning to plant one drill width to an environmental mix to promote beneficials and reduce reliance on chemical pesticides,” he says.
Drone technology
When it comes to crop management, the team are also using sophisticated drone camera technology to quickly provide real-time crop data to reduce chemical inputs and tailor their use.
Drone imagery is used to remotely monitor any potential weed, nutrition or disease threats by identifying zones of particular interest to ensure smarter applications are used, where required.
For Kieran Walsh, crop adviser for the project and this year’s Farmers Weekly Arable Adviser of the Year, the use of drones makes monitoring crops much more efficient, as he is able to select key areas that require closer examination.
Before every spray timing, a drone is flown over the crops to identify what is happening in the field so a more targeted chemical programme can be deployed.
One important advancement is the speed at which information is received, with images processed in just a few minutes instead of several hours.
A 15m Amazone UF 901 variable-rate precision sprayer with individual nozzle control, featuring a 900-litre tank hitched to the back of the automated tractors using three-point linkage, then passes through the crop.
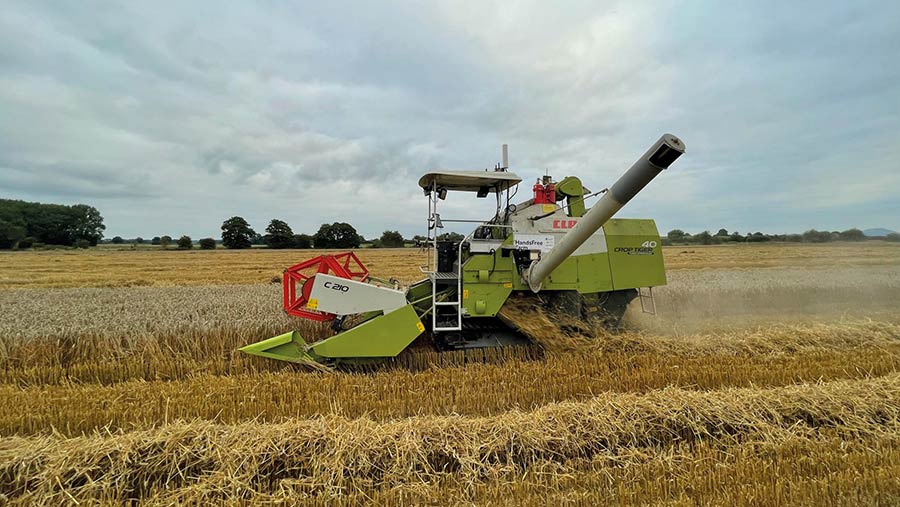
© Harper Adams University
Weather data
In addition to this, a range of software programmes such as weather- and soil-monitoring systems are in place to help track crops.
This is because monitoring disease is significantly harder than weeds due to the long latent periods associated with disease infection.
Weather that favours damaging diseases such as septoria and rust can, therefore, be flagged up, while the use of rapid disease-detection technology provides a more detailed analysis.
New for this year will be an investigation into variable-rate liquid fertiliser applications with in-kind sponsor Omex, which the team hope will improve crop efficiency.
Plans for the future
Looking forward, the research team plan to demonstrate their automated machines at various agricultural shows, including Agritechnica, to showcase their technology and inspire the next generation.
The university is also integrating enhanced 4G and 5G networks to provide a base to test upcoming automated farming technologies.
“When the Hands-Free Hectare first started there were no autonomous agricultural vehicles. Now, just five years on, there are more than a handful of companies and vehicles capable of achieving this,” says Mr Gill.
This delivers many opportunities for the project to work with other companies to trial and test new technologies.
Harvest 2021
A total of five successful autonomous harvests have now been completed, but this year’s harvest was pleasantly surprising, with higher-than-average yields.
Extase winter wheat yielded 9.27t/ha, Wizard winter beans achieved 4.6t/ha, and Elyann spring oats averaged 5.7t/ha.
The start to the growing season was challenging, with yet another wet winter where some areas of land were flooded, causing 3ha of crop to be lost as plants stood in pooled water.
Despite delays obtaining specific machinery parts, harvest kicked off on 11 August and lasted until 8 September, with a stop-start approach due to unsettled weather.
The combine and tractor worked autonomously side by side, unloading grain into small Ifor Williams tipping trailers on the go.