Calculating the cost of growing spuds
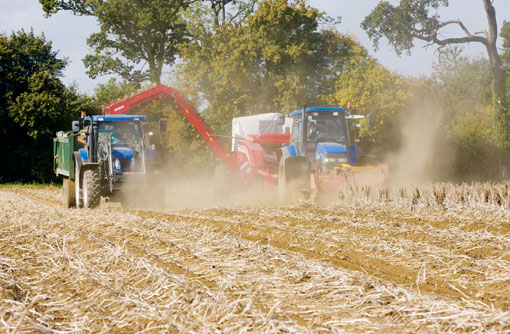
How do you estimate the cost of production of a potato crop? The input (direct) costs are straightforward as you know what you have spent on the crop, but overheads are more difficult to quantify – unless potatoes are your only enterprise or you use contractors for every operation.
In most cases, potatoes are just one enterprise in a bigger arable farming or mixed farming business, so inevitably there has to be an element of informed estimation as to the allocation of labour, power/machinery and other overheads between enterprises.
That said, the Potato Council has commissioned work to estimate the cost of production of potato crops for a range of situations including ware and processing potato crops. Total cost of production for 2012 including rent and finance (ÂŁ24/t) is estimated as ÂŁ157/t for ware crops and ÂŁ132/t for processing crops.
This immediately highlights one major anomaly, which is that every grower’s rent and finance costs will be different – all of the crop may be grown on owned land with no debt, but where land is rented the range in rents is wide from less than £495/ha to about £1240/ha. Debt may also be a significant factor.
Based on analysis of client budgets for 2012, typically the cost ranges from ÂŁ105-110/t for green crop through to ÂŁ155-160/t for stored crops to April/May.
The differential between green crop and stored crops highlights the real cost of storage based on the grower data storage costs of between ÂŁ50-55/t through till April/May.
This is a significant figure and takes into account in-store losses and the additional inherent risk of storage. How many years does the price between harvest and the following May rise by less than this figure?
With recent renewable energy incentives, a number of producers have looked at ways to cut store running costs. Simple options include additional insulation and checking the electricity tariff is the cheapest possible.
The cold store roof or the land adjoining it may be suitable for solar photovoltaic panels which, as well as significantly reducing running costs, will bring additional income from the Feed-in Tariffs (FiTs) and electricity sales. For ageing stores the real cost of storage only becomes apparent at the point of reinvestment.
The range in cost of production between the most and least efficient growers is another area that could improve the overall profitability of the sector.
At the risk of making the same mistake as former farm minister, Jim Paice – who told dairy farmers that one of the ways they could counter a fall in milk prices was to be more efficient producers – the use of benchmarking data, such as ADHB/Potato Council cost of production, can help growers highlight areas of weakness in their own potato enterprise with a view to making future improvements. The key, as always, is to take the necessary action once you have analysed the information.
In common with every other crop, the focus in terms of cost of production per tonne is on the saleable yield per acre. This comes down to field selection, appropriate variety selection, management in and out of store and access to irrigation.
What we are reminded of, particularly in a year like 2012, is that weather is key in determining yield – and hence cost of production. The grower has only limited influence in many circumstances, resulting in compromised planting and seasonal growing conditions.
There is a trend, particularly in the processing sector, to place potato contract prices on a “cost-plus” basis. Calculating the cost part has its challenges; the more difficult question is: what should the “plus” part be?
What does the typical grower need to cover reinvestment and his management input? Should there be something to cover the additional risk and working capital compared with growing, say, a wheat crop?
The concern is such contracts are paying enough in the short term, but may not be enough to cover long-term reinvestment, particularly where the switch into combinable cropping is straightforward for those farmers who are already “kitted up” and wheat and oilseed rape prices are at historic highs.
As an example, the cost of putting up a new 800t bulk store has increased by about ÂŁ30,000 (20%) in the past 10 years and a new potato harvester has increased by around ÂŁ25,000 (35%) over the same period, according to the Agricultural Budgeting & Costing Book.
Couple this with the removal in 2011 of tax allowances on new buildings (previously 4% per annum) and the reduction in the Annual Investment Allowance threshold from ÂŁ100,000 to ÂŁ25,000 per annum for capital allowances for machinery and fixed equipment, and tax breaks are less of a stimulus for major capital investment on arable farms. This is particularly the case for higher rate taxpayers, which many arable farmers will now be as a result of higher cereal and OSR prices.
Looking to the 2013 crop, cost inflation for potato crops will no doubt continue. Tentative budgets for the coming crop year see costs of production increasing modestly based on current input prices, but not dissimilar to the figures expected for 2012.
Anglia Farmers’ “Aginflation” index for the 12 months to August 2012 estimates that the cost of growing a potato crop increased by almost 5% during that period. Although input costs are set to remain relatively stable, rent and finance costs are likely to continue on a steady upward trend.
Potato growers can assess the profitability of their enterprises online using the latest version of the Potato Council’s benchmarking model.
The software allows growers in each key sector – ware, processing, salads and seed – to compare their business’s production costs confidentially with similar enterprises.
Funding may also be available to help growers set up business improvement groups. Click here for more information or call Phil Bradshaw on 07776 492 274.
Do you agree with these figures or have any other tips for reducing costs? Share your thoughts on our costs of production forum and read the wheat and OSR articles in this series