Guide to preventing fire in poultry sheds
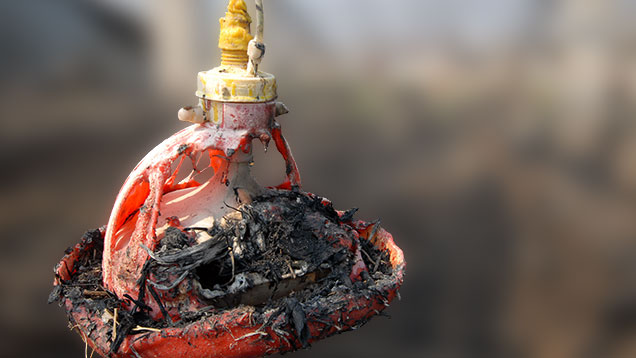
A fire can unravel a poultry business that has taken years to build up in a matter of hours. Poultry World looks at the key areas to consider to cut the risk.
It has been suggested that 80% of businesses that experience a major incident such as a fire never recover.
By its nature, poultry farming is at high risk of devastation; sheds are often lightly constructed, feathers, dust and wood bedding abound. That’s before one considers the myriad electrics required to run a modern shed, and propane heaters that keep birds warm.
See also:Â Top tips for clean water in poultry production
So the danger of combustion is a very real one. This is coupled with the fact that livestock is contained under one roof, compounding the dangers to animals in a farmer’s care and the profitability of a business.
Thermographic imaging to highlight hotspots
A new service is offering to highlight the areas in which heat is concentrated – and could point out the source of a fire before it happens.
Vulcan Inspection Services, a safety and compliance business that works with NFU Mutual, has recently employed the use of thermal imaging technology to identify hotspots in poultry sheds.
The devices visually highlight temperature differences, and faulty wiring that is overheating can be quickly identified.
A trained inspector can survey a shed with birds in situ, meaning checks can be undertaken when equipment is in normal use.
Poultry sheds are a high fire risk due to their highly combustible environment, with extensive use of wood, litter on the floor and the likelihood that everything will be coated with feathers and dust, says Melissa Boyes of Vulcan Inspection Services.
“If a fire does occur, the cost is typically high, with a total loss of birds and severe damage to buildings. The main cause is most frequently a fault in the electrical wiring system, or electrical equipment connected to it.”
The service costs about £400 (excluding VAT) a half-day, and can identify additional dangers that a standard periodic wiring inspection will not.
Thermographic surveys concentrate on control panels for heating, lighting, feeder motors, extraction fans, electrical distribution equipment and general power supplies.Â
Once the survey is complete, a full report is produced for the farm. It includes identified defects which are colour-coded depending on their severity. An executive summary gives guidance on defect priorities with suggested corrective timescales.
In addition to preventing fires, the camera can also be used to improve the energy efficiency of sheds by scanning roofs to identify areas of excessive heat loss.