Biomass boiler maintenance for poultry producers
As any farmer will know, water quality varies across the country – and the poultry industry is increasingly focused on giving birds the best water possible.
But another consideration for water quality should be its potential impact on the efficient operation of biomass boilers.
Improper maintenance can in some cases damage these expensive – and vital – installations, according to Alan Marshall, consultant with Combined Chemical Services.
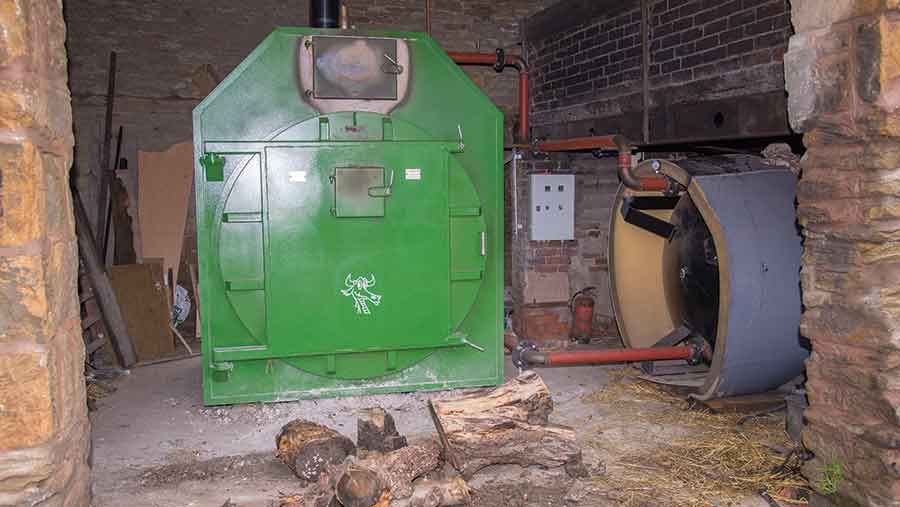
Biomass boilers’ need careful maintenance if they are to live out their intended lifespan © John Eveson/FLPSA/Rex Shutterstock
Dr Marshall says manufacturer’s instructions should be closely followed when it comes to the water used in heat exchangers, and some recommend the use of softener or demineralised water to fill the system.
See also: Surprise policy changes threaten new CHP biomass projects
No treatment
A poultry farm he recently visited had a Weiss 995kW biomass boiler providing heat to eight poultry sheds that had operated for 18 months with no treatment.
The farmer was finding it difficult to achieve the intended shed temperature, and the cause was found to be corrosion and fouling with corrosion deposits.
Upon inspection, overhead heaters in the poultry sheds were blocked with black deposits.
These were restricting water flow and reducing heat transfer – the reason why the required temperatures and control of temperatures could not be achieved.
Analysis showed the deposit to be predominately 85% iron oxide (See table).
Analytical parameter | Before treatment |
After treatment |
Total iron | 125.0 | 4.5 |
Soluble iron | 14.5 | 2.3 |
Soluble copper | 1.2 | 0.2 |
Water was sampled at various parts of the system and analysis showed found the soluble and suspended iron levels in the system water to be very high, says Dr Marshall, particularly the samples taken from the boiler itself.
The solution
Under guidance, the farm adopted a three-phase approach: cleaning to remove blockages; applying passivation and dosing the system with a corrosion inhibitor.
Each individual overhead heater was physically cleaned to remove the majority of the black deposit before they were flushed individually using a small flushing rig.
The heaters were flushed using a cleaner effective against iron oxide dosed at 1% in the recirculating water.
When all the overhead heaters had been individually flushed, the whole system was cleaned using a 1% solution of the cleaner.
“After the cleaning of the system, selected overhead heaters were then inspected to make sure they were still clean and had not trapped any of the debris liberated during the full system cleaning process,” explains Dr Marshall.
Protection
The next stage was treatment to prevent the problem reoccurring. A passivator is a corrosion inhibitor designed to quickly promote the formation of a protective film. In this case, the system was treated with a dose at 0.5% – half a litre for every 100.
The system was then treated with a corrosion inhibitor dosed at 0.5%. The corrosion inhibitor is a multipurpose treatment to inhibit metal corrosion and scale in all types of waters.
The concentration of inhibitor in the system was monitored to establish that the correct dose was being applied.
The result
Cleaning the system re-established the correct waterflow rates and restored heat transfer. This resolved the problem of control over the temperatures and the correct temperatures could be achieved in the poultry sheds.
“The passivation treatment and use of an effective corrosion inhibitor provided control over the corrosion of the system.
Total iron rates fell from 125.0mg/litre before treatment to just 4.5mg/litre afterwards. Soluble iron fell from 14.5mg/litre to 2.3mg/litre and soluble copper declined from 1.2mg/litre to just 0.2mg/litre.
Instantaneous corrosion rates for mild steel measured with a corrater probe also showed a dramatic reduction in corrosion rates from 0.218mm/year with no treatment to 0.012mm/year with treatment.
If no action had been taken, the lifespan of the boiler could have been dramatically reduced.
Dr Marshall says the black iron oxide was generated from corrosion of the boiler and the system pipework.
The majority of this corrosion had taken place in the boiler itself.
“Biomass boilers are an expensive piece of equipment and the water systems must be treated to prevent scale and corrosion,” concludes Dr Marshall.
“The systems need to be monitored quarterly for treatment levels and performance to ensure trouble-free operation and to achieve the expected lifetime of the boiler.”
What sort of water should I use?
The quality of water used can vary from softened or naturally soft water through to hard water depending on the local water source or the instructions of the boiler manufacturer.
However, in many cases the need to treat the boiler water to prevent the problems of scale and corrosion is either over-looked or thought not to be necessary.
What should farmers do when they get a new biomass boiler?
It needs to be treated with an effective multipurpose corrosion inhibitor from the first time the boiler is filled with water.
When operational, water samples should be taken on a quarterly basis and analysis carried out. The level of inhibitor needs to be checked and should be topped up if below the recommended level. Iron and copper levels should also be measured to check corrosion is under control.
Biomass rescue job
There are three stages to reinvigorating a boiler that has built up corrosive components to its water system
- Clean the system to remove the blockages and restore heat transfer using an effective cleaner. This can also be combined with a side-stream filter to remove suspended matter, reduce flushing times and reduce the amount of water required during flushing.
- Apply a passivation treatment to rapidly generate a protect film and reduce the corrosion in the system.
- Dose a multi-purpose corrosion inhibitor to maintain corrosion at acceptable low levels.