Exclusive: Mass food fraud and safety scandal engulfs sector
British farmers are being ripped off by an industrial-scale country-of-origin fraud in a scandal that has engulfed almost the entire food retail sector, as well as some major food service outlets.
An in-depth investigation by Farmers Weekly has revealed that up until at least the end of 2020, a food manufacturer was passing off huge quantities of foreign pork – sometimes tens of thousands of kilos a week – as British.
See also: Editor’s view: Meat trade duping us daily and that must end
The processor, which cannot be named for legal reasons, has also been accused by former employees of regularly “washing” hams that are visibly off, or mixing rotting pork with fresh product for further processing.
© David Simonds
Other products such as ox tongues were not heat treated properly, and meat was sometimes thawed out on the factory floor, posing a serious food safety risk.
Two former employees also said the paperwork for sampling, which would pick up bacteria such as listeria and E coli, was falsified.
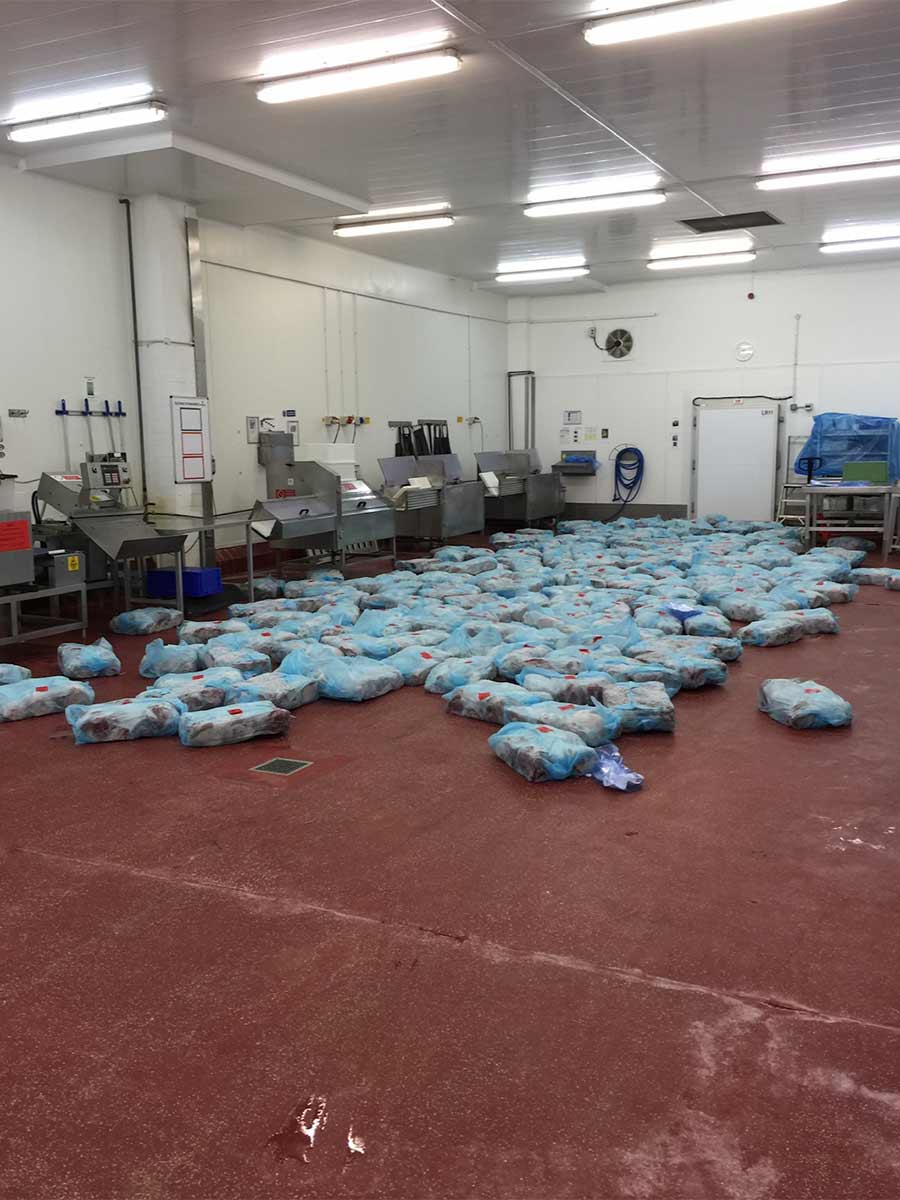
Meat being thawed on the factory floor, posing a serious food safety risk © Picture supplied
Wake-up call
Industry leaders approached for comment have said Farmers Weekly’s investigation should act as a “wake-up call” for the sector and questioned the response of the Food Standards Agency (FSA) and National Food Crime Unit (NFCU).
Both bodies have been aware of the activities taking place at the processor since 2020, but at least one source claimed to have sent photographs and information about the practices to the FSA several years before that.
Meat processed by the company ended up in products such as ready meals, quiches, sandwiches and other produce sold in Tesco, Asda, Co-op, Morrisons and Marks & Spencer.
Food manufacturer and distributor Oscar Mayer, which supplies Sainsbury’s, Aldi, Ikea, Subway and airline food producer Dnata, was another customer, as were major brands Princes and BidFood.
Bakkavor was a customer until 2019.
Schools, hospitals, care homes and prisons were also indirectly supplied, with one source alleging the most rotten meat would end up there.
“I used to tell them about it,” they said. “I used to [say] ‘you can’t do this’. [The reply was] ‘Do you want the effing job? Get back in there’.”
Audit deception
There is no suggestion that any of the processor’s customers were aware of the criminal practices, which took place for at least two decades and very likely beyond 2020, as auditors who visited the site were deceived.
One former employee said: “They did surprise audits, but they’ve got 15 minutes to be in. I’ve been there before when that’s happened.
© David Simonds
“It was 6am and they’re knocking on the front door to come in. The first thing they do is bring them in, give them a cup of tea.
“By that time, there’s a text message come down to one of the phones [and] everybody is on the job, pushing stuff onto lorries, getting rid of them. So when they walk in, it’s all nice.”
Another source said if the meat was not hidden on lorries, employees would push any suspect product around the top of the circle-shaped factory.
“The auditor would be walking round with the management and they would get employees to push it round at the same time, so they never met it,” they said.
Prior to 2018, some of the meat that wasn’t seen by auditors would be hidden in a secret chiller, but its location was eventually reported to authorities, which forced the processor to put it on the site plan.
This incident led to “a lot of supplier audits”, according to one source.
Ex-workers speak out
Almost all of the former employees Farmers Weekly has spoken to said country-of-origin fraud was embedded in the company’s operating model.
“It was all one big fiddle,” said a source.
The business would buy a relatively small volume of British meat from a retailer-approved supplier, then use the traceability information from this delivery for all the products it made in that week – with the majority coming from elsewhere in the world.
One source said they were 100% confident that all the retailers the company supplied have been victims of country-of-origin fraud.
For pork, the price differential between British and imported product could be as high as a few pounds a kilo.
Another former employee claimed, at one point, EU bacon medallions were being bought at £1/kg and sold on, as British, for about £12/kg.
Farmers Weekly has seen evidence that showed Danish pork, which was only allowed to be sold on the mainland of China, was delivered to the factory.
Other products, such as ox tongue sold direct to Morrisons, were subject to the same fraud.
A source said: “What they are supposed to do is buy it from Woodheads [Brothers Meat Company]. They are basically owned by Morrisons.
“We would then buy that ox tongue to send them, but then also we could buy a small bit from other approved suppliers.
“Obviously, the UK is expensive, but Ireland would be cheaper. So all they would do is buy some from Ireland that is not approved and mix it in with the Woodheads. But then on the traceability again, everything would say Woodheads.”
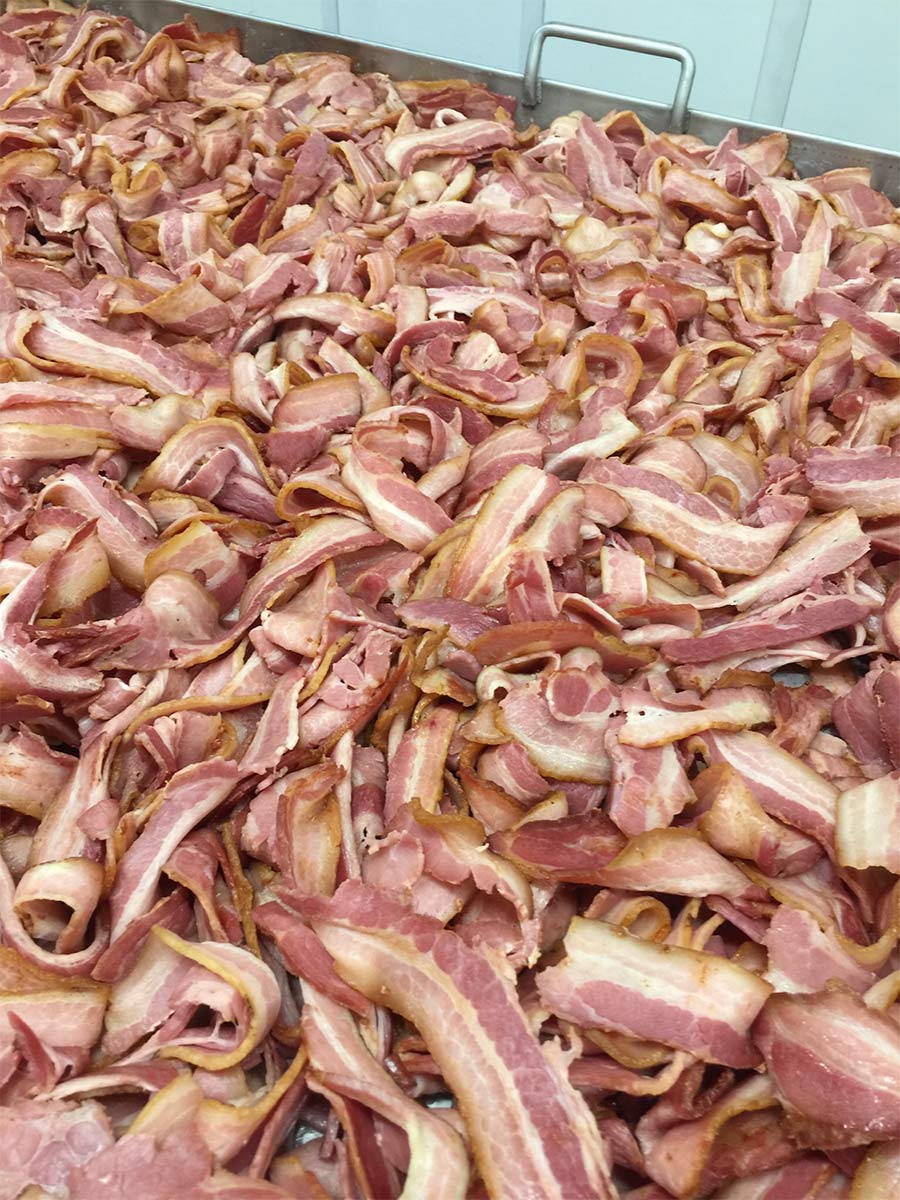
How bacon should look © Picture supplied
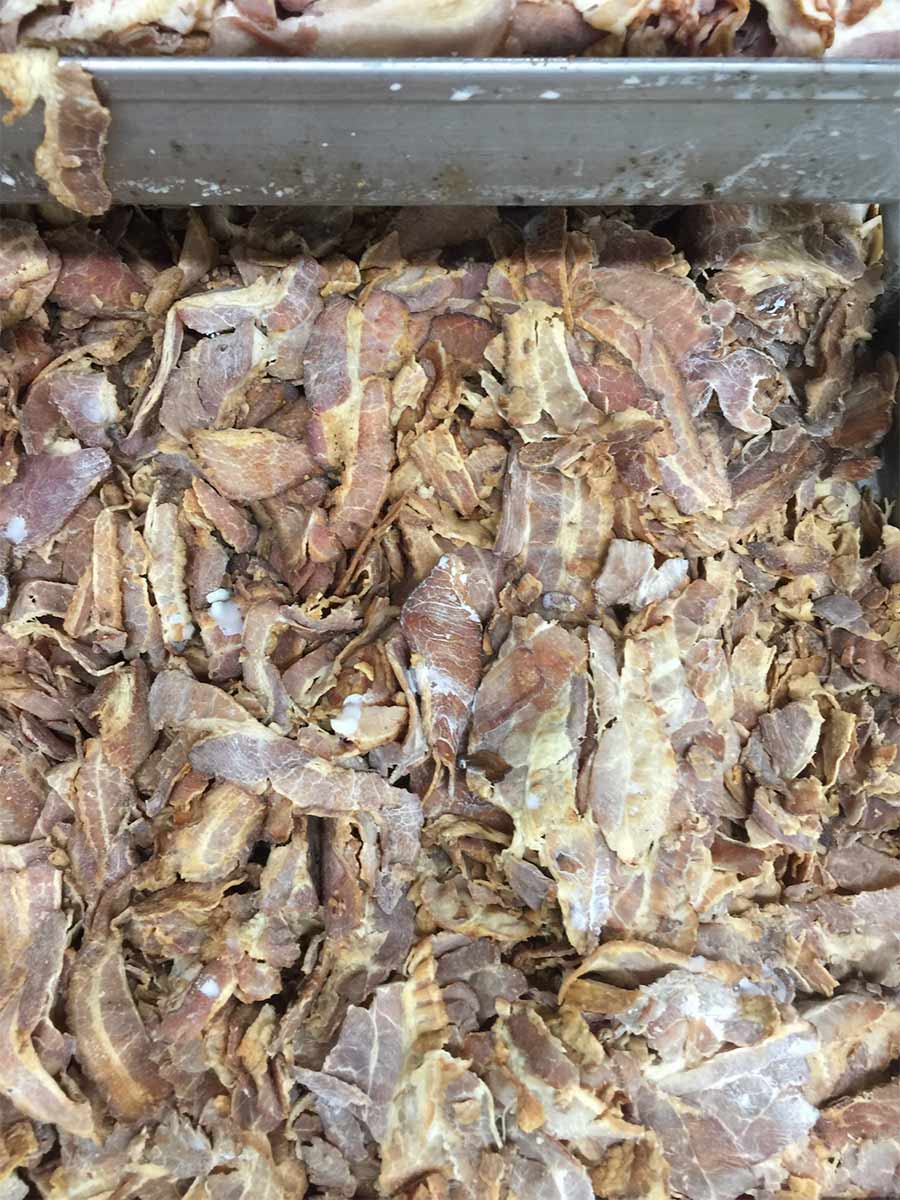
Former employees accuse the processor of mixing rotting pork with fresh product for further processing © Picture supplied
Falsified records
According to one source, the processor kept two separate sets of records – a fraudulent set and the originals, which were hidden in the factory and could be used to trace product in case of a food poisoning outbreak.
All of Farmers Weekly’s sources say employees knew about the widescale criminality taking place, but most were kept silent with threats of job losses, as there were few other work opportunities in the local area.
“If you did anything wrong, you were given the s******t job they could find you, like cleaning the drains, or you were bullied and bullied and bullied until you left,” said one source.
“There aren’t many places around here. It was either shut up, carry on or get out.”
Now, sources are speaking out to clear their conscience.
“It used to get me to a point where I’d be thinking ‘we’re going to kill someone, we’re going to kill someone, we’re going to kill someone’,” said one.
Another said: “There were days I’d sit outside in my car crying because I didn’t want to go in. It was that bad.”
There is also a fear among some sources, which Farmers Weekly believes is rooted in fact, that other businesses may be acting in the same way.
“You wonder if there’s anyone else,” said one. “They’ve learned it from somewhere haven’t they.”
Regulator response
Darren Davies, head of the Food Standards Agency’s (FSA) National Food Crime Unit, said: “The FSA’s National Food Crime Unit is carrying out a criminal investigation into how a supplier was allegedly providing products labelled as British when they were in fact sourced from elsewhere.
“This is a complex and live investigation and we are looking into all new lines of enquiry with our partner organisations, including any potential food hygiene breaches at the premises. If any evidence of a food safety risk is found, then necessary action will be taken.
“The FSA advised retailers last year to check their cooked meat supply chain and to apply extra due diligence in their checks. We don’t give out these alerts without a reason.
“We will not name the supplier while we painstakingly gather evidence to support our investigation so as not to prejudice any possible future action by the courts.
“As a national regulator, we are the last line of defence. At a time when cost pressures and other challenges mean the risks of food fraud might be increasing, it is vital that everyone involved in the food system remains extra vigilant to ensure that food is safe and what it says it is.”
Retailer responses
The British Retail Consortium (BRC) issued a statement on behalf of all the affected supermarkets.
It said: “The role of the FSA [Food Standards Agency] is to work with retailers to prevent fraud. While we cannot comment on an ongoing investigation, retailers will support the FSA with its investigation into the individual supplier in question.”
An Ikea spokesperson said: “The safety and quality of our food is an absolute priority and we take claims of this nature very seriously. In addition to necessary legal requirements, we require all food suppliers to be Global Food Safety Initiative certified.
“We also have additional, mandatory requirements, processes and systems in place for every Ikea supplier, and are therefore concerned by these allegations.
“An investigation by Ikea has now been established to look further into them, and we will support the FSA and relevant authorities as part of their ongoing investigation.”
Brand responses
A Princes spokesperson said: “We take food safety and authenticity extremely seriously and do not accept any violation of the policies or standards outlined in our Supplier Code of Conduct or agreed specifications for raw materials.
“Princes has zero tolerance for unethical behaviour and all of our suppliers are held to high expectations of honesty, integrity and compliance, undergoing regular audits as part of our ongoing due diligence and risk assessment processes.
“Following the recent launch of a National Food Crime Unit [NFCU] investigation into a meat processor, we immediately ceased purchases and have moved to an alternative supplier.”
Jim Gouldie, supply chain and technical services director at Bidfood, said: “We have been alarmed to hear of the allegations regarding this particular meat processor. At Bidfood, we operate on a zero-tolerance policy to any form of food fraud within our supply chain, and take the accuracy of food origin claims, as well as quality assurance of the products we buy, extremely seriously.
“We have a dedicated technical services team who work alongside our buying teams to ensure we properly vet all of our branded suppliers through a formal supplier approval process, ensuring they hold appropriate third-party food safety certification.
“All suppliers are monitored regularly to ensure they maintain the food safety certification, we hold up-to-date product information on all products, which includes country of origin. We also have a robust customer complaint process in place, and if there is cause for concern with a supplier or product supplied, appropriate action is immediately taken.
“While the processor in question has reassured us that the investigation does not impact products supplied to Bidfood, we have made the decision to cease trading with them pending the review.”
An Oscar Mayer spokesperson said: “All our meat sourcing is from suppliers with whom we have held long-established relationships, are retailer-approved and hold appropriate certification.
“We undertake regular, unannounced auditing visits at all of our suppliers, reviewing the traceability of random batches of product supplied to us as well as inspecting the relevant mass balance records.
“The allegations against this particular meat processor are shocking. However, in fairness, we have not found any issues relating to country of origin nor any other discrepancies relating to our supplies from this or any other company.
“All our meat suppliers are certified to the BRCGS [Brand Reputation Compliance Global Standards] or GFSI [Global Food Safety Initiative] standard. There is nothing more important to us than the quality of the products we manufacture and our supplier quality assurance tracking is vital to upholding these standards.”
A Bakkavor spokesperson said: “All suppliers into Bakkavor UK meet BRCGS or GFSI accreditation as a minimum standard. Furthermore, as part of Bakkavor’s approach to responsible sourcing we operate a supplier code of conduct that promotes transparency and traceability within the supply chain as well as maintaining a regular audit programme.”
A Subway spokesperson said: “Subway has become aware of a meat processor which has allegedly been involved in food fraud and we are investigating this as a matter of high importance.
“All suppliers and distributors for Subway are required to meet legal requirements on traceability and must demonstrate compliance through third party GFSI certification.
“The suppliers of Subway products have also confirmed they have not utilised the meat processor in question to manufacture products for Subway.”
Meat processor response
The Association of Independent Meat Suppliers’ (Aims) membership includes processors of all sizes.
Norman Bagley, the group’s head of operations, said: “Reading the response from Darren Davies, head of the Food Standard Agency’s NFCU [National Food Crime Unit], we note that they alerted retailers, possibly via the secure Food Industry Intelligence Network [FIIN] members area in May 2022, some five months after first advising the FSA board about there being a live high-level food fraud investigation.
“The FIIN has, according to its website, just 58 members from a supply chain of thousands of food business operators.
“It is inexcusable that food manufacturers and food service businesses, some of whom supply some of society’s most vulnerable consumers, were not alerted at any time to date by the NFCU as to there either being a possibility of labelling fraud or of a risk to public health.”
Recommendations to stamp out future criminality
1. Make digital record-keeping mandatory
Paper records, such as those used by the company at the heart of Farmers Weekly’s investigation, are easily manipulated.
Nick Allen, chief executive of the British Meat Processors Association, said: “The trouble with paper is evidence can be destroyed in a way it cannot with a digital trace.
“A lot of the smaller companies can’t afford to put that infrastructure in, but I think there comes a point where you just have to make people do it.
“If you want to supply the food chain, that’s probably what you’ve got to do.”
2. Address the 15-minute gap between auditors signing into a premises and entering the factory floor
This time was used by the processor in question to hide anything they did not want auditors to see.
If 15 minutes is needed for auditors to put on PPE, consideration could be given to other options, such as stopping production at the moment of arrival and accounting for all staff until entry.
“This is going to have to be looked at,” said Mr Allen.
“You tend to assume when you know these plants that 15 minutes shouldn’t be long enough to be able to do this, unless you’ve got a bunch of employees that are all tuned into it as well.
“This needs to be a wake-up call for the industry to try to root out other people like this. It raises question after question about operations.”
3. Establish an independent, short number whistleblowing line and make it a requirement for this to be clearly displayed in factories, alongside information in multiple languages
Several sources told Farmers Weekly they were not aware of who they should blow the whistle to, with the employee handbook at the factory in question encouraging them to report any issues to the internal HR department.
“Undoubtedly, people need to be aware of who they should go to if they’ve got concerns and are being asked to do things that are illegal,” said Mr Allen.
“We need to give some thought as to how we communicate with people in the industry about what they should do.
“It is all very well saying it’s the employer’s duty to let people know, but if you’ve got people like this, they’re not going to do that.”
4. Ensure an independent body is requesting the total mass balance at processors, to see how much British meat is going in and how much is going out
The manufacturer at the heart of Farmers Weekly’s investigation was able to exploit the fact that its customers operated independently and only audited their own supply chains.
A request for total mass balance would have picked up the fraud much sooner.
If you know anything about illegal practices anywhere else, call Abi Kay on 07399 726 451