Workshop tips: What you need to know to use grinders safely
Having spent more than 35 years teaching the agricultural fraternity to weld, Derbyshire farmer Richard Archer knows a thing or to about joining bits of metal together.
He has taught hundreds of farmers and farm workers to weld through a series of college courses and on-farm courses with the former Agricultural Training Board and now Lantra.
He also acts as an external quality assurer for City &Â Guilds at agricultural training centres and colleges and presents at HSE safety awareness events around the country.
See Richard Archer’s other workshop tips:
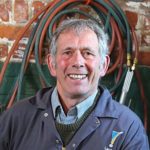
Richard Archer © James Andrews
Archer’s advice – abrasive wheels
Thanks to the Provision and Use of Work Equipment Regulations (PUWER 98), everyone who uses an angle grinder, petrol-driven saw or bench grinder for work needs to be properly trained to do so.
That means there has been a surge in the number of farmers and farm workers booking on to abrasive wheel courses. It’s easy to get lulled into a false sense of security with grinders, but these tools can be some of the most dangerous in the workshop.
Bench grinders, angle grinders and cutting wheels can also burst if treated incorrectly.
See also: Work boots on test – which are the best?
Bench grinders
It sounds obvious, but bench grinders should always be fixed securely to a bench, either with bolts or clamps. I see some that are just stored under a bench and lifted up when needed, running the risk of them falling over or moving around the bench when being used.
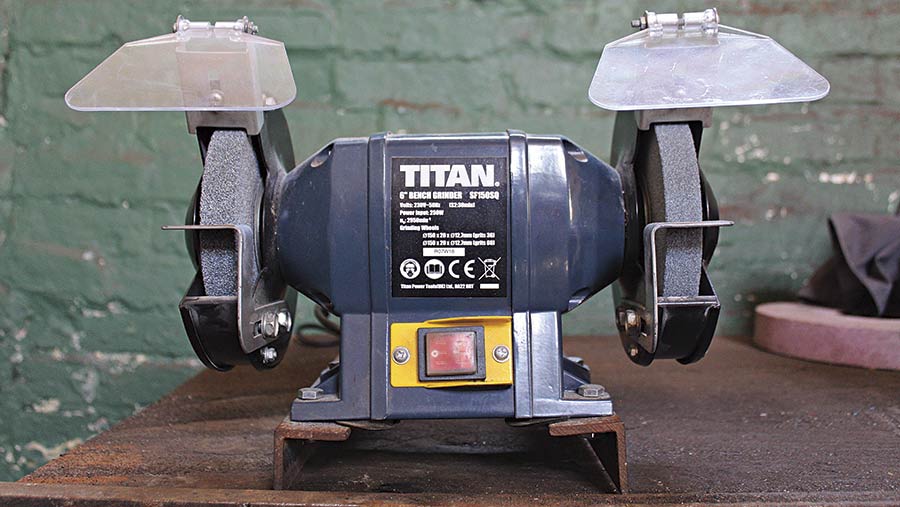
Bench grinders should be fixed securely © James Andrews
A lot of people also fail to adjust the work rest. This should be as close to the wheel as possible to avoid the item you are grinding (or your hand) being dragged into the wheel. The maximum safe gap between wheel and work rest is 3mm.
Bench grinding wheels should also be kept true and clean using a dressing tool (Huntingdon Dresser). If this isn’t done, they can become unbalanced and don’t grind as efficiently. This may encourage the application of too much pressure, which can be a cause of wheels bursting.
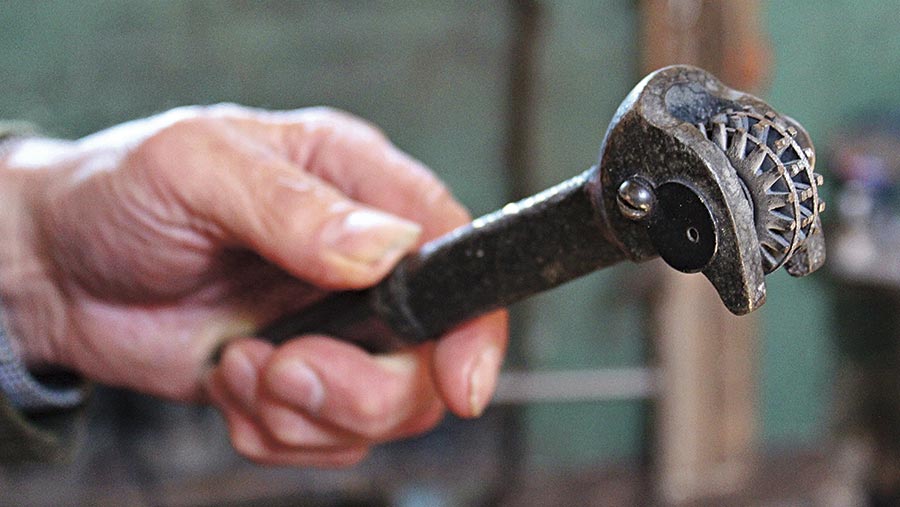
Huntingdon Dresser © James Andrews
Angle grinders
I hear of quite a few safety misdemeanours with hand-held angle grinders – such as people using them without the side handle fitted and cutting materials that aren’t properly secured.
Another common problem is people over-tightening the disc. Discs are self-tightening in use, so you shouldn’t “gorilla them up” with the spanner. This can cause damage to the disc and will make them difficult to remove.
It’s also important to remember that resinoid (angle grinder) discs have a use-by date as they can become brittle over time. If this date has passed, they should not be used. Also make sure that you buy discs with fibreglass reinforcement when used in a hand-held machine. They can be identified by the coding “BF” on the disc.
The most common causes of abrasive wheel accidents include:
- Fitting the wrong type or size of wheel
- Removing guards
- Poor wheel mounting
- Damaged wheels
- Overspeeding
- Side grinding on bench grinder wheels
- Grinding with cutting discs or cutting with grinding discs
It’s hard to believe, but people still use grinders without goggles – even with the risk of a piece of wheel going in their eye at 80m/sec (180mph).
Avoiding accidents – not just the boring stuff
Welding masks
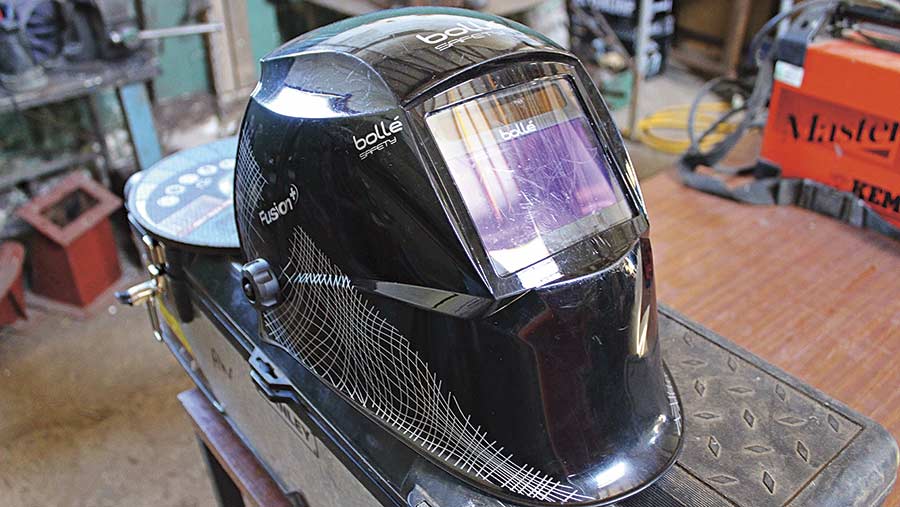
A good-quality welding mask © James Andrews
Clearly, a welding mask is an essential bit of kit to protect you from the searingly bright light and radiation emitted by a welding arc.
Getting a decent light-sensitive model helps improve your welding, as well as reducing the chance of getting arc eye. Don’t forget that uncovered skin will also be burned by the radiation from the arc.
Safety goggles
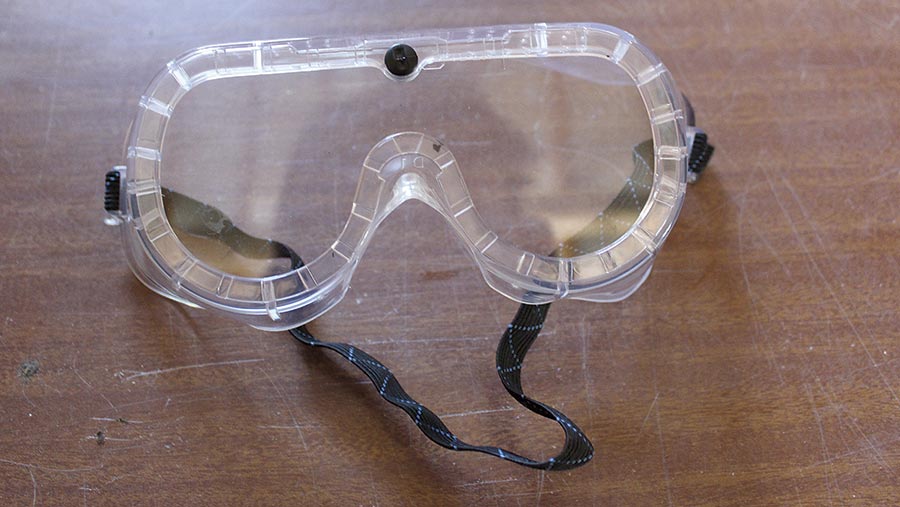
Correct workshop goggles © James Andrews
A lot of people think safety glasses are all that’s required for grinding duties, but they don’t really cut the mustard. First, debris can flick up underneath them; second, most aren’t tough enough to withstand the debris from a burst wheel.
Therefore, go for proper workshop goggles that are rated 166 B (grade 1 impact). Anything with an F is best left to strimming duties.
Gauntlet gloves
Gauntlet gloves might seem overkill for a bit of casual welding, but they serve a couple of very important purposes.
Most importantly, they stop your hands from getting burnt from sparks or radiation – welding arcs operate at temperatures of 6,000C – but they also stop blobs of molten metal shooting up your overall sleeves. Similarly, rigger boots are bad news for welding, unless you wear your overalls over the top.
Lantra course prices
Across the country there are plenty of training providers that offer Lantra-approved courses for welding and abrasive wheels. As a rough guide, a one-day course is likely to cost between ÂŁ100 and ÂŁ150 per person.
However, for more accurate prices and group deals it’s worth speaking with your local training provider.
Get your workshop questions answered
If you have any burning workshop-related questions that you are struggling to get answered, email them to fwmachinery@rbi.co.uk. If we get enough, we will publish an article including the best answers.