Workshop legends: We visit 94-year-old war veteran Harold Gilbert
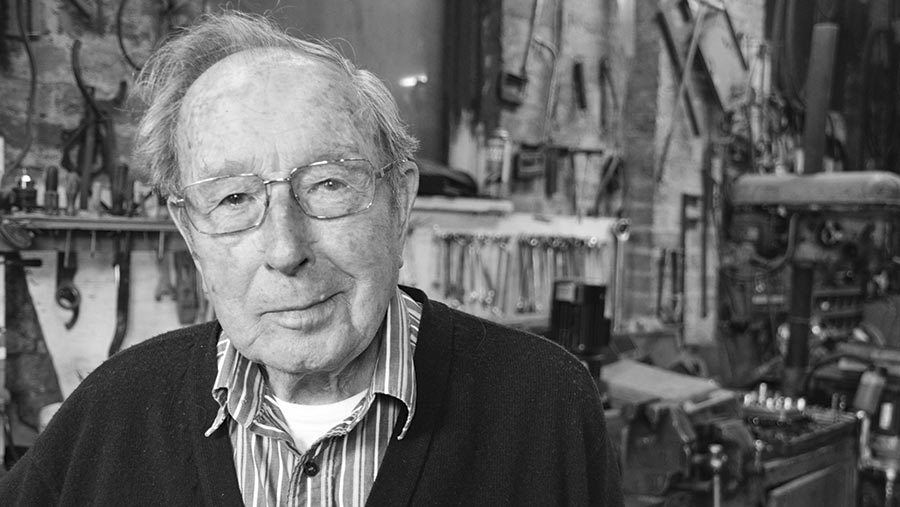
Across the country there are welders, mechanics, fitters and fabricators beavering away in sheds and out of the back of vans to keep the nation’s farm machinery fleet in running order. Often geniuses in their own right, we’re visiting 94-year-old Kent superstar, Harold Gilbert.
Mr Gilbert’s distinguished career has seen him adapt First World War howitzers, undergo training to defuse bombs and seas mines, and finally settle in a job engineering kit for use on fruit farms in the south east of England.
Where did you learn your trade?
I’m 94 so it’s a bit of a long story. When I was 14 I went to work as an apprentice at Wingates Engineering in Rochester. I started out making wheelbarrows and that’s how I learned all the basic skills of measuring and drilling.
I moved up through the ranks and got the job of welder. By then, war had started so some pretty interesting jobs came in.
See also: In pictures: Simple category highlights from the 2016 Farm Inventions Competition
What sort of jobs did you have?
We had to adapt First World War howitzers and build turntables to mount them on warships, then we were on to making winches for barrage balloons and arrester hooks to catch Spitfires landing on aircraft carriers.
To do that I had to take aeronautical engineering qualifications – that’s where I learned about the value of precision.
I had to take more tests to prove the quality of my welding when we were given a contract to make tank armour. Gluing 3/8in or 1/2in plate, there could be no failures or people would die.
In 1942 I was called up and got assigned to 937 port construction and repair company and ended up doing a lot of underwater salvage work.
We got trained to defuse bombs and sea mines, but we never actually put that into practice. Generally, we just stuck a stick of explosive in and got out of the way as quick as we could.
How did it work?
I had to wear a 240lb rubberised deep sea diver’s suit and helmet – moving around was horrendous.
You crawled about like a crab in silt and were fed air from the surface by a hand-cranked pump.
One day I almost died. I was dealing with a bomb dropped in soft mud and a tug collided with our dive boat. It snapped off the ladder and nearly severed my air line.
In 1943 I got the chance to do my underwater welding course and learned some pretty useful tricks.
Things got interesting in 1944. I was sent into to Normandy on the day after D-Day. We had to secure the lock gates at Ouistreham near Caen. We went in on a big American landing craft under HMS Warspike’s 16in guns – there were shells dropping all around us.
Luckily, the British 2nd Airborne had got there first and surprised the Germans – there was still breakfast on the table in the officers’ mess.
With the demolition charges on the lock gates defused we moved eastwards to Boulogne where the Germans had scuttled one vessel after another on top of each other.
We had to clear the harbour so, together with a team of naval divers, we spliced together a load of depth charges and positioned them in the holds of the ships.
We set the fuse on a piece of wood floating on the surface and retired to a safe distance. It wasn’t really far enough.
That was a big bang but afterwards all our shipping could get through.
At one stage a tug had hit a scuttled dock crane and so I had to weld a patch on the hull to make it watertight enough to limp back to Dover.
Unfortunately, my work set light to the inside of the skipper’s cabin.
After Normandy we followed the retreating Nazis all the way across France, Belgium and through Germany, repairing bridges, fixing up lock gates and clearing scuttled vessels.
At one junction where five canals met in Holland we spent days fixing up holes in a scuttled pleasure cruiser, pumping in air and refloating it only for the Germans to drop mortars on it and sink it the following day.
What happened after the war?
I went back to engineering, building cement-batching plants and big drag-line buckets for civil engineering projects such as dam building in Africa and India.
They obviously valued my opinions because I was asked to go on an evaluation panel for a new type of welder being developed by a firm called Lindon. It was a wire-feed machine that used a shroud of carbon dioxide gas to make a clean weld – basically the forerunner to today’s modern metal inert gas wielding.
It was interesting work but there was a big call for men to go and work on farms. I took a job with the Worley family at Oakleigh Farm as mechanic and fabricator building equipment for their fruit and veg growing business.
What sort of things were you building?
There was lots of bodging done in a hurry. Some of the stuff I’ve made over the years has been pretty unusual.
Probably the most complex was a plastic laying attachment for a rotavator.
It had discs to open a trench either side, discs to scuff soil back in over the top of the sheet and then a hot rotating drum to burn holes in the right place for the plants to grow through. It took months to get it right and it was so long that our Massey 185 couldn’t really handle it.
Sundays were my day off but I ended up in the workshop building sledges out of one-quarter inch square bar for the strawberry pickers to drag their trays along on.
I could churn about 20 out in a morning.
We grew a lot of hops at the time so I had to build special tapered-body harvest trailers that needed to be lightweight.
I think I did too good a job as a local engineering firm then started to copy them.
What was your best invention?
I designed a fruit bin dipper that treated the fruit with a preservative before it went into the cold store.
Everything ran on rollers and it really sped the job up.
Favourite workshop tool?
The 2lb hammer – you can’t do anything without it.
That said there are many clever bits of kit that have come along in my time that make the job so much easier.
To cut steel I tend to use an oxy-acetylene torch for but we’ve now got a plasma cutter on the farm.
It’s fantastic – it’s quick, accurate and there’s no slag.
Favourite farm welder?
The DC stick generator/welder.
You’ve got your own power and so you can work anywhere.
Once you get to grips with a good DC welder you can get it running like syrup.
I still rate my 30-year-old Oxford – it has got heaps of power and there’s nothing to go wrong.
I should change the oil but that rarely happens.
How to choose the right rod for the job?
It’s difficult because there are so many different types of steel on farms.
You’ve got to have a decent range of sticks to suit every eventuality.
Spark colour is a good guide to indicate what you’re welding.
If it’s a dull spark then it’s generally hard and if it’s bright then it’s likely to be softer.
Dissimilar steel rods were a massive step forward when they first came in – they’re much more forgiving and because they’ve generally got chrome in them the weld doesn’t tend to rust.
What about welding cast?
You can’t rush it. You need to pre-heat it with an oxy torch.
If it’s thick, chamfer the edges to get the heat into the full thickness.
Once it’s glowing, weld it and then cool it in dry sand.
You’ve also got to choose the right rods.
There are three types of cast – black is soft, white is hard and mottled tends to be somewhere in the middle.
How difficult was it welding underwater?
It’s completely the opposite way round to welding on the surface.
You still use a DC stick welder but uphand and overhead welds are easier than horizontal because you don’t have the bubbles and gases coming up into your face.
Get in touch
We’re looking for workshop wizards to feature in our new series, so if you know someone that has spent decades grafting as a fabricator or fitter then send some brief details to oliver.mark@rbi.co.uk or call 020 8652 4951.