What to look for when buying a used telehandler
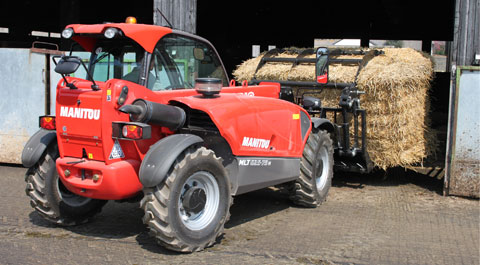
Whether a livestock farm, an arable unit or a contracting business, a materials handler of some kind is the core of many farming fleets, and for most the telescopic handler has become the tool of choice for everything from grain, silage, muck and straw shifting to loading seed and fertiliser, with many machines in service daily.
Whether a livestock farm, an arable unit or a contracting business, a materials handler of some kind is the core of many farming fleets, and for most the telescopic handler has become the tool of choice for everything from grain, silage, muck and straw shifting to loading seed and fertiliser, with many machines in service daily.
Because they play such an important role in so many businesses, it pays to be particularly careful if buying this type of telehandler secondhand.
Not only can the wrong machine leave you with a hefty repair bill or something that won’t squeeze under your shed doorway, but telehandlers are a common factor in farm accidents, so it’s essential to ensure you select an example that has been treated well, operated carefully and looked after properly, and doesn’t put its next owner at risk.
It pays, therefore, to spend more than a little time examining potential purchases if buying secondhand.
Most dealers are likely to be offering machines that have undergone at least basic checks and servicing if not a thorough overhaul, and should be supplied with a current LOLER (Lifting Operations and Lifting Equipment Regulations) certificate, but machines being sold through private vendors may cover a far wider range of conditions.
Farmers Weekly and its FWi website both offer good sources for those seeking used machinery, but it’s hard to split the good and the bad from a few words and a photo.
Here, with the help of Steve Day of Kent JCB dealer Agwood, we provide a few pointers to not only help the uninitiated, but also remind experienced buyers of the little things that can be overlooked when assessing a potential purchase. We’ve used two JCB Loadalls, a rear-engined 526S and a side-engined 536-70, as our examples, but most of these points would apply generally to most makes of rigid telehandler.
As with any secondhand machine purchase, handler appearances are rarely deceptive. There are, of course, exceptions, but generally speaking, if a machine looks rough from the outside, the chances are that there may be ‘issues’ within.
Any seller worth his salt will have given his machine a good hosing, so one that’s covered in crud should raise alarm bells.
Machines which have worked on livestock units are, obviously, more likely to have worked deep in mud and manure, but owners who care should have still ensured that the bulk of such muck was washed off at regular intervals.
A machine that’s clean underneath is a good sign. Look also for general cab cleanliness, damage to mudguards, dents and scrapes, broken mirrors, torn seats etc.
Machines from arable units may have been just as badly abused, especially if they’ve been used to load lorries in a hurry, with consequences for brakes, transmission and tyres.
Beware also of buying a construction-spec machine, as these often won’t have the features many farms require, such as a limited slip diff, air conditioning and 40km/hr top road speed. They are also likely to have fewer transmission speeds in total and less power, as well as a different joystick.
Tyre condition is up at the top of any self-propelled machine checklist, and on a telehandler, it’s importance is at least doubled.
Not only will worn tyres provide little grip – particularly if the machine will be expected to work on straw yards or silage clamps – but serious splits and cracks can be dangerous on a loaded machine. Ensure that you budget for replacements or negotiate a better deal if tyres are severely worn or damaged, unless the buyer has made their condition clear from the outset.
When visiting a potential purchase, it’s a good idea to go armed with an examination tool kit – torch, screwdrivers, adjustable spanner – for unfastening panels and examining concealed areas.
Undo the air cleaner and see that the filter is as clean as can be expected, and check the condition of the radiator and its water/antifreeze level.
After making initial checks and once the machine has been running for a while to get the oils warm, check the engine, transmission and hydraulic oil levels. A well-cared for machine can often be identified by the filter change dates/engine hours written onto them or a cab window label.
On a handler, regardless of transmission type, the transmission oil check is particularly important. The scent of burnt oil can indicate a serious transmission issue, or at the very least be a sign of machine abuse which could lead to a problem.
Working deep in mud, muck and silage can take its toll on telehandler propshafts.
Release the torque wind-up in the shaft and look for any evidence of oil leaks.
Check all universal joints for play and ensure all is as tight as it should be right along the shaft. When test-driving the machine, listen out for knocking noises from the shaft or whining from the transmission.
Telehandlers are now, almost universally, equal-wheeled machines with four-wheel steering and selectable front/rear/four-wheel/crab steering modes, and the nature of their work means they spend a lot of time manoeuvring.
Examine carefully the knuckle joints on each ‘corner’ and ensure that they are free from damage, as repair/replacement can be costly.
Check the condition of the battery – located behind a cover and tucked under the cab steps on most JCB machines, as shown here – for both the amount of gunk around the terminals and the level of de-ionised water in the cells.
If the machine is a poor-starter, the problem may lie here, in which case addressing it will be – relatively – cheap.
If the issue is elsewhere, the starter motor is more likely the culprit.
The rear-engined format has, in recent years, fallen out of favour with telehandler designers, with general consensus being that side-mounted engines offer more advantages in terms of manoeuvrability, efficiency and visibility.
There are still plenty of such machines on the used market, though, and if the format fits your requirements, they can be a good purchase.
There are relatively few issues specific to rear-engined handlers, but do check for rear end knocks and scrapes, and related radiator damage, as well as weak exhaust pipe mountings.
Check the boom wear pads at both the front and the rear (not so easy to see) of the boom, and look for evidence of scoring by debris ingress.
They should be chamfered on their upper facing edges; when the chamfer has worn away, the pads are worn out and need replacing.
Look over all of the boom pins and bushes for evidence of play and wear. Also look carefully at the hydraulic pipework routed under the boom.
Pipes that have been pushed out of place and pinched are likely to result in a hefty replacement bill.
Check that the boom nose guard is fitted and is in good condition. If it’s not, then debris ingress will have incurred, and grease plus grit is not a good combination where metal is concerned.
Extend the boom, and look for evidence of scoring along its surfaces. Light scoring should not be too much of an issue, but budget to replace the guard if it’s missing.
It’s time to turn the key, but before firing up the machine, see that the hours clock looks untampered with and that the instrumentation works as it should. Check that the dash lights illuminate as they should when the ignition is turned on, and all go out when the machine is started. At the same time, check the test button on the safe load indicator to see that it works correctly.
Don’t be too concerned if the machine takes a second or two to fire up – most Tier 2/3 engines take more cranking as the electronic fuelling system has to ‘see’ that the camshaft and crankshaft sensors are turning in time.
Allow the engine a few minutes to warm up, and use the time to check all levers, the handbrake and the brakes for play. Listen to the sound of the engine for any unusual noises, and then do the same with both engine and transmission when putting the machine through a test drive, also assessing power, general performance and any signs of overheating.
After a road run, work through all the boom functions and look around the machine for any signs of leaks and drips.
Check the brake fluid reservoir – sited at the front of the cab on our example JCB machine.
Some machines are hydraulically-braked and incorporate a charge system. If the machine you are looking at is so-equipped, test the system by stepping sharply on the brakes when the machine is at tickover, listening for evidence that the hydraulic accumulator is working.
Ensure that the shuttle operates solidly and run through all of the transmission’s speeds.
Listen for noises when changing gear and direction. A clunk when shuttling might mean a universal joint problem.
Check that, when applied, the brake holds the machine and pulls engine rpm down. If the machine is hydrostatic, ensure that it stops still when the driver’s foot is taken off the throttle. If any aspect of the transmission sounds poorly, either call in an expert to view the machine with you and give an estimate of how much the problem might cost to put right, or walk away.
Unless you’re looking at an elderly machine, the chances are that if it has been built in the past couple of decades it will have equal-sized wheels and selectable steering modes – rear-wheel, front-wheel, four-wheel and crab.
Check that they all work as they should, and that when switching between modes that the wheels align correctly, and that the in-cab guide/lights for this work as they should.
A four-wheel drive machine on which the four-wheel drive doesn’t work isn’t a lot of good, so check that engagement and disengagement works as it should.
JCB machines drive through the front wheels when in two-wheel drive, so check that drive is being transferred as it should to the rear axle.
The best way of doing this is when on the move on a road or track. This way, the sound of the rear axle drive engaging should be immediately apparent.
On most modern machines, it should also engage with braking.
After a road run, put a hand to the brakes and axles. If they are too hot to touch, then a transmission or brake problem is the likely cause.
Any self-propelled machine seller worth his salt should have at least ensured that vehicle basics such as lights are all working correctly.
A bulb or fuse change doesn’t take a minute or two, and if something so simple hasn’t been sorted, it doesn’t bode well for the general care that’s been taken of the machine. If it’s apparent that neither brake light is working, the issue may be connected to the 4wd not engaging.
Look over the headstock, and check that the hydraulic locking pins, if fitted, work properly. Ensure that all boom functions and services work as they should, ideally by coupling an attachment. Even if it isn’t one that requires a third service, listen out for unlikely noises from the external oil supply by engaging its lever/joystick function.
Check the boom suspension works correctly – it will take a moment to engage – by placing a load on the attachment and taking a short journey with it on board.
Check the headstock for play by putting the attachment through all its cycles.
If you are buying a machine without its attachments and plan to use your own from another type of telehandler, factor in around £1500 to change the headstock. Be sure that the machine’s boom geometry will suit the new headstock, and bear in mind that an adaptor will push forward the load centre of any attachment, reducing its capacity.
If buying a machine with attachments including a set of pallet forks, check the two forks to ensure they are stamped with the same serial number. It’s not possible to buy single forks, and they must be bought/replaced in pairs, so if the numbers are different, something is wrong.
Check the capacity/weight rating of the forks, which should also be stamped on them – 1500kg at 500mm load centres in this case.
Remember that this will be affected if using an adaptor plate as this will push the load centre forwards.
Check that the pick-up hitch works correctly, fully extending through its travel and securing firmly back into place when raised. See also that the trailer light socket works, as well as the trailer brake and trailer tipping pipes.
Telehandlers are a commonly stolen item of farm/construction equipment, so it’s essential to be confident that what you are buying is genuine and completely above board. Look for the machine’s serial plates, and ensure that they look legitimate. An HPI check is well worth the relatively small investment.
Whether they are being offered by a dealer or a private seller, machines must also have a current Lifting Operations and Lifting Equipment Regulations (LOLER) certificate, which identifies them as being safe and fit for purpose.