VIDEO: Combining and baling – a one-stop operation
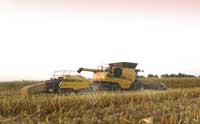
Take a drive through the rolling countryside of Western Australia at harvest and many of the wheat fields will be dotted with the familiar sight of big square bales.
But only the keen eyed will notice the lack of telltale tyre patterns left when a tractor pulls the baler – or that the bales contain more than just straw.
Across the 12,000ha of arable land farmed from the Glenvar property – and several more such properties in the area – combining and baling has become a one-pass operation.
The lack of tractor wheelings result from equipping the combine to tow a modified baler; the bales are different because they contain everything other than quality grain – straw, chaff, cracked grains and weed seeds.
It was largely because of the latter that the Shields family, who farm Glenvar, developed the direct baling system.
Faced with a growing herbicide resistance problem, they concluded that capturing weed seeds rather than allowing them to fall back to the ground, and carting them off in straw bales, would help contain, perhaps begin to reduce, the resistant population.
Subsequent analysis showing a 1% improvement in the protein content of the bales made them a popular choice for stock producers it seems, despite the obvious risk of importing the resistant weed problem.
Watch a video of the harvest
After five years of on-farm development and two years of harvest trials with a production version, the Glenvar Direct Baling System is now being produced under licence for several different combine and baler combinations by engineering company Primary Sales Australia.
According to business development direct Alan Fisher: “Under normal harvesting conditions, baling on the combine does not substantially affect the speed of the harvest nor interfere with the operation of the combine harvester.”
More recently, Agco’s USA harvest machinery R&D team has also worked on the concept of baling while combining.
The motivation in this case is the fast-growing interest in producing ethanol from biomass – as opposed to corn or wheat – which entails packaging threshed cobs and leaf material. And since that is difficult to pick up once deposited on the ground, the easiest way to bale such material is to transfer it direct from the back of the combine into the front of the baler.
The attraction of this approach is that it keeps the material clean, with no soil contamination of a feedstock destined for an ethanol plant nor, in the case of bedding material, any stones or other debris that can be a hazard to livestock.
With the baler’s pick-up assembly surplus to requirements and therefore removed, both development teams needed a means of transferring material from combine to bale chamber.
In Australia, the Glenvar team decided a frame-mounted conveyor with hydraulic motor drive was necessary to bridge the gap between the combine and baler. Together with a curtain hung from the straw hood to contain the chaff and other light material, this ensures all material passes into the bale forming chamber.
![]() |
---|
An MF 187 baler working in cereals behind a New Holland CX880 equipped with the Glenvar conversion. |
Field measurements suggest the system recovers up to 30% more crop residue than is baled from a swath, albeit in very dry conditions with short, brittle straw, while analysis by the University of Western Australia shows that 98% of weed seeds are retained in the bales.
In North America, Agco engineers wanted to avoid the added complexity of installing a conveyor between the two machines.
“The combine’s been modified to tow the baler in terms of the drive system, and also the discharge area has been modified,” says Kevin Cobb, Challenger combine marketing manager. “We wanted to deliver the product to the baler in a simple manner without a conveyor or chains and so on.”
Since there was no concern about retaining light material, Agco engineers devised a modification that in effect simply blasts material into the modified intake throat of the baler.
The Australian and US development teams agree that 120cm x 87cm (4ft x 3ft) cross-section bales best suit transport and storage efficiency and that a combine can handle the size of baler needed to produce them. They also decided that a hydraulic motor would be the best way to power the baler.
The Glenvar installation puts an engine-driven pump, oil reservoir, filter and cooler on the combine and a hydraulic motor on the upper drawbar frame of the baler where it is coupled directly to the flywheel.
Agco has yet to detail its baler drive installation at this pre-production stage but it clearly draws hydraulic power from a source on the combine, absorbing around 90hp of the engine’s output in doing so.
With 8.5t of baler to haul around, it is clear that this technique needs a big, powerful harvester.
The US company’s trials have been carried out with a Challenger 680B full-rotary combine (equivalent to the MF 9895) with up to 459hp on tap and a Challenger LB34B baler – the same as an MF 2170.
Primary Sales Australia recommends at least 400hp and rear axle drive on the Case IH, Claas, Challenger/MF and New Holland combines, for which it has conversion kits.
Apart from the hydraulic power pack, the kits comprise a substantial “A” frame tow bar that bolts in two places on the front axle and then also to the towing plate of the main frame, an extension to the cleaning shoe to carry chaff to the conveyor and the straw hood curtain. The chaff spreader and straw chopper are removed altogether.
With Agco’s conversion, there is just a single rail drawbar in place of the baler’s usual towing assembly while the Glenvar replaces the regular drawbar with the conveyor frame, which positions the machine far enough back that it can trail 90° to the combine.
“If required, two people could convert the baler back to standard operation in approximately four hours,” says Alan Fisher.
Could this approach find favour in Britain?
Apart from any agronomic or bale quality advantages, the one-pass approach eliminates labour and most fuel costs involved in baling and keeps one pass of a tractor’s wheels off the land.
But whether growers will risk a baler problem delaying the combine in the UK’s fickle weather remains to be seen.