Claas tractors: Common problems and how to fix them
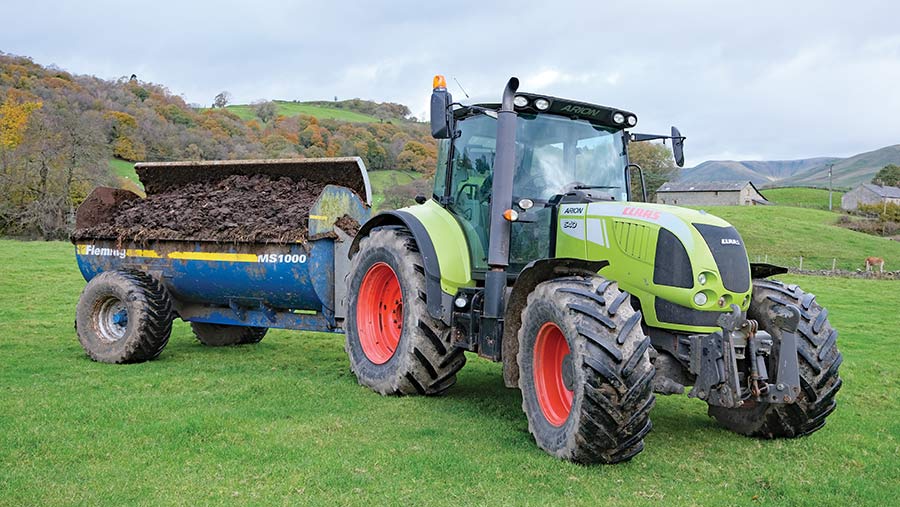
Amassing a sales tally of roughly 600 tractors a year at the last count makes Claas the eighth most popular tractor brand in the UK, just behind Valtra.
And of that figure, its mid-power Arion models are the biggest sellers, most of which come fitted with Gima-built semi-powershift transmissions.
These are shared with Massey Ferguson and, consequently, suffer the same list of gremlins.
See also:Â Case and New Holland tractors: How to fix common problems
Engines have predominantly been sourced from John Deere over the years and therefore have a few Deere-related quirks, but since about 2014, four-cylinder 400 models have been powered by FPT.
Here, we take a look at common problems associated with the Arions and other popular sellers in the Claas range, such as the lower-powered Axos and heavier-duty Axion 800.
Guiding us through the minefield is Cumbria-based mechanic James Rawsthorn, who cut his teeth working for local Claas dealer Rickerby before branching out on his own two years ago.
Arion Carraro axle wear
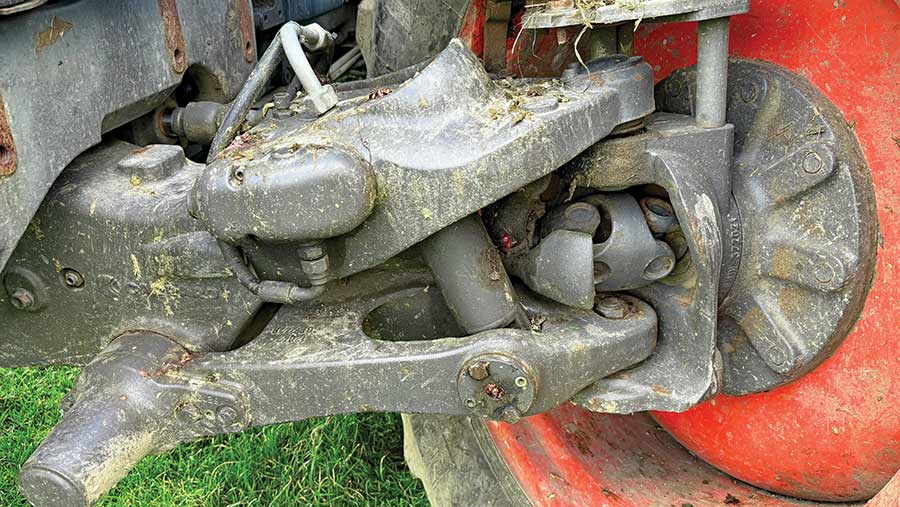
© James Andrews
Though they give a silky-smooth ride, Carraro suspended front axles fitted on Arion tractors can give all sorts of problems if they’re not regularly greased.
On hard-worked machines, this needs to be carried out every day to prevent premature wear and, with about 20 of them in total, it’s a laborious job.
For those that start off with a good one and look after it, there shouldn’t be too much cause for concern. But take some time to check the condition before buying second-hand.
Where there has been a lack of grease, play can develop in the driveshaft hangers, which is given away by a knocking sound coming from the axle when driving on full lock.
Minor wear can be taken out by adjusting a couple of nuts, but more serious deterioration requires a new set of bushes. These aren’t that expensive, but it’s a good half-day job for a fitter who knows what they’re doing.
Top and bottom ball joints are another thing to watch out for, as they can wear to the point that they damage the castings.
These are more of a pain to check as they require jacking the front wheels off the ground and listening for squeaking as the steering wheel is turned.
Worn drive shaft needle bearings are a common ailment, and result in the driveshafts wobbling. Again, they’re not too expensive, but they’re a fiddle to replace.
Bigger Axion tractors have a simpler Dana axle that doesn’t require too much attention, other than the odd failed accumulator.
Six-cylinder Arion engine head gaskets
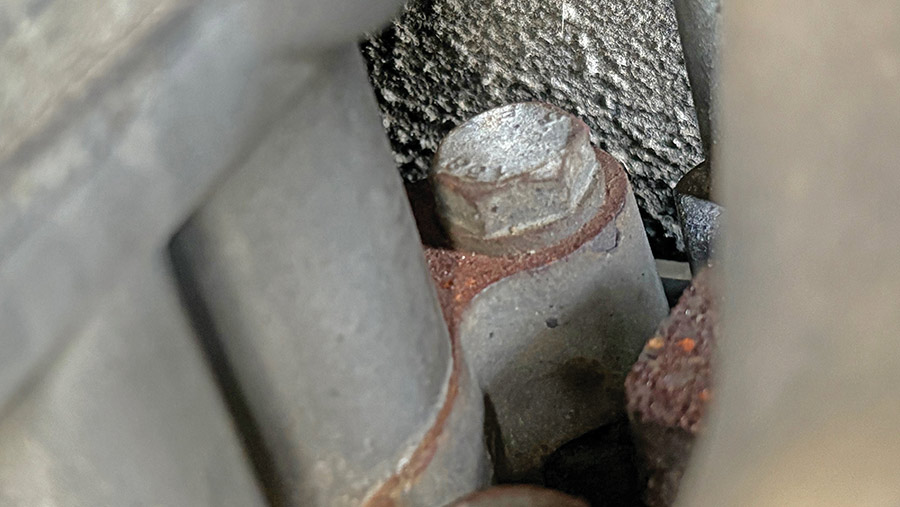
© James Andrews
John Deere’s 6.8-litre six-cylinder engine was renowned for head gasket troubles, but newer shape Arions built from 2012 onwards received an update that largely solved the problem.
This came in the form of a new gasket kit with bolts that had a higher torque setting, thus holding the head down tighter to prevent gasket failure.
Any older tractors that have done more than 6,000 hours will have likely been sorted too, so these days it’s less of a concern for those buying on the used market.
To check whether a tractor has been upgraded, look at the numbering on the top of the head bolts – those with a 5F stamp have received the upgrade and those with a 4F could be on borrowed time.
Even with the upgrade, it’s wise to keep radiator screens clear and coolant topped up to reduce the risk of the engine running too hot.
Arion variable geometry turbo

© James Andrews
Though they help give a smoother power delivery, the vanes in the complex variable geometry turbo will eventually soot up, causing the tractor to throw up error codes and possibly derate the power.Â
The proper fix is to fit a replacement, which costs about £1,000. However, there’s also the unofficial option of fitting a simpler fixed vane version and remapping the ECU.
This is an approach offered by the Derv Doctor that also tends to involve removing the emissions kit.
Arion EGR coolers
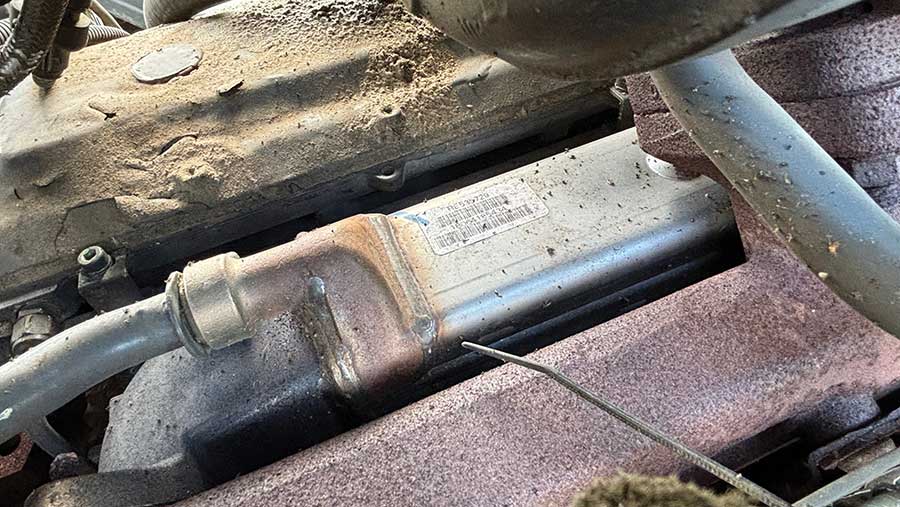
© James Andrews
Recirculated exhaust pass through an EGR cooler first, which is prone to cracking and leaking coolant.
If the tractor’s coolant level keeps dropping and it’s not obvious where it’s going, or you can see steam coming out of the exhaust, this component is probably the culprit.
The proper course of action is to replace it. But with the part costing about £800, some will decide to remove it and the EGR valve altogether.
To avoid the tractor throwing a wobbly, the ECU will need to be remapped in the process.
Arion and Axion flywheel damper plates
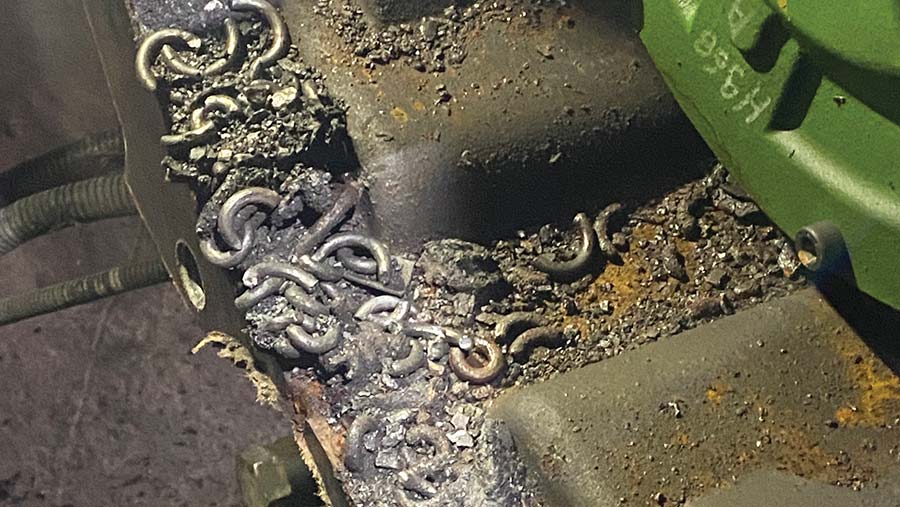
© James Andrews
After about 5,000 hours, the flywheel damper plate between the engine and transmission on six-speed Hexashift and four-speed Quadrishift tractors will likely be on the way out.
You can tell by listening out for a rattle as the tractor is turned off, which is caused by bits of broken spring jiggling.
If the rattle is ignored, the plates can eventually wear through the casing, leading to a complete loss of drive and a banging noise coming from the bell housing.
Replacement takes about a day for an experienced mechanic, with most of the work involving splitting the tractor.
Hexashift C-range bearing failure
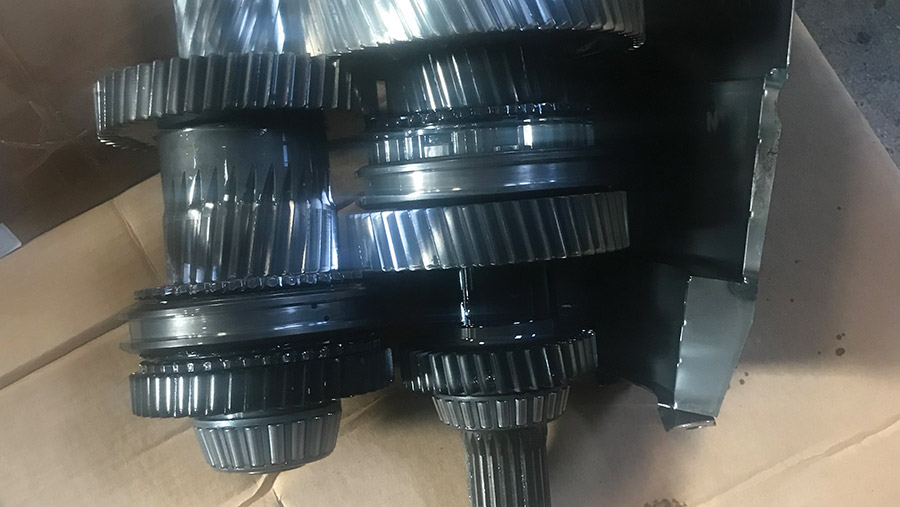
© James Andrews
Both Axion and larger Arion tractors fitted with Gima-built six-speed Hexashift transmissions can have trouble with the bearing on C range wearing and developing play.
Not all tractors are affected and it’s not purely a Claas problem either, as Massey Ferguson Dyna-6 models can suffer in the same way.
The first sign of this is a little crunch when shifting down from D to C range on the road which, if left too long, will file away the synchro teeth on the gear.
At this point, an error code will pop up saying that the range can’t shift.
Regardless of the point you intervene, it’s an involved week-long job for a qualified mechanic.
However, if it’s caught early, you only need to shell out for a couple of bearings, rather than a replacement shaft and gear.
Part of the problem is the oil gallery feeding the bearing not being sufficient to keep it properly lubricated when working very hard.
This was improved in later tractors, but they still aren’t immune to the issue.
The best preventative measure is to keep the back-end oil clean and make sure the brakes are changed promptly – after no more than 5,000 hours – to avoid the risk of contaminants blocking the oilflow.
Belville springs
Both Hexashift and Quadrishift tractors can suffer from failed Belville springs in the forward and reverse packs.
If they’re on the way out, the tractor will creep, even when the shuttle is in neutral.
Although the parts are cheap, there’s a fair bit of labour involved as the tractor has to be split to gain access to the transmission.
The rear one is a particularly tricky and time-consuming job as the powershift portion of the gearbox needs to be removed in order to access it.
Arion Quadrishift pto bearings
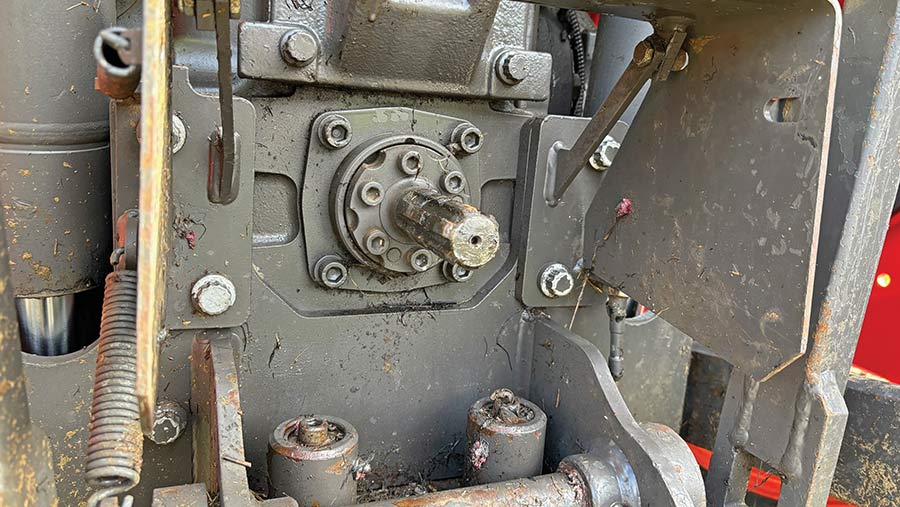
© James Andrews
Some tractors with the lighter Quadrishift back end have a splash lubrication arrangement for the pto bearings, rather than a dedicated oil feed.
Generally, this is adequate, but if a tractor is left stationary for long periods doing a job like slurry pumping it can run a little dry, particularly if it’s parked with the front end lower than the rear.
For anyone that is doing this sort of work, it’s worth filling the back-end oil to max and adding an extra jug for good measure.
If the bearings are run too dry, you’ll first hear a rattle and eventually the speed selector will get stuck. What this generally means is the selector fork has welded itself to the shaft.
Parts aren’t that expensive, but it’s a day’s labour to sort it.
Twisted top shafts on Quadrishift back-end
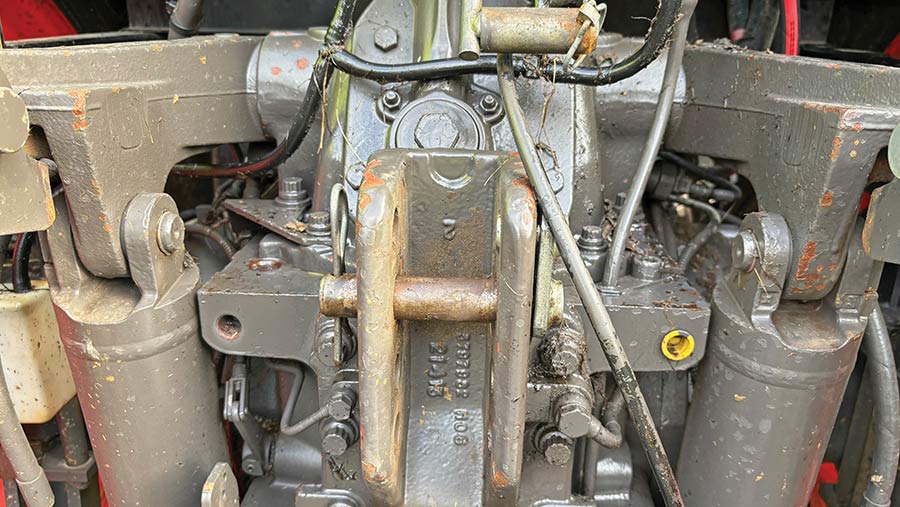
© James Andrews
If used within its limit, the Quadrishift back-end gives little in the way of problems. But if it gets overloaded, carrying a heavy 3m offset mower, for example, it is possible for the linkage top shaft to twist.
After doing this, the first thing people tend to notice is that they can’t release the pick-up hitch. They’ll then adjust the lift rods and invariably end up breaking the pins.
To confirm that the shaft has been damaged, lower the lift cylinders until they are in line with the shoulders of the back-end casting.
If one ram is higher or lower than the other, this is your problem.
Canbus connectors
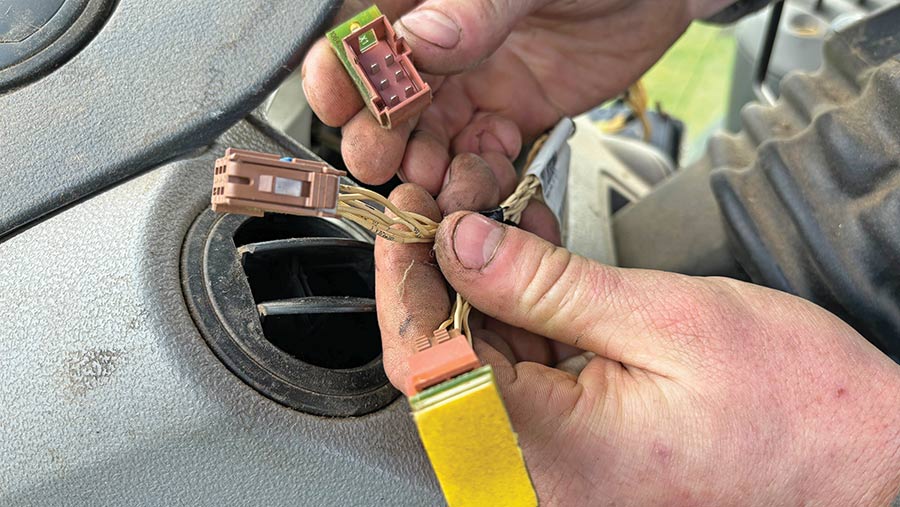
© James Andrews
Most, if not all, modern Claas tractors run on a canbus electrical system, and if moisture gets into the connectors, it can wreak havoc with the electrics.
Generally, this manifests as a flurry of bizarre error codes popping up on the screen, even when those functions are working fine.
Canbus connectors can be found in several places such as behind the dash and under the floor, but it’s the latter location that tends to be the most vulnerable, particularly when drivers leave the rear window open so the rain comes in.
Sometimes, cleaning up the connectors and coating them with Vaseline does the trick but, if not, they’ll need to be replaced.
Headlights
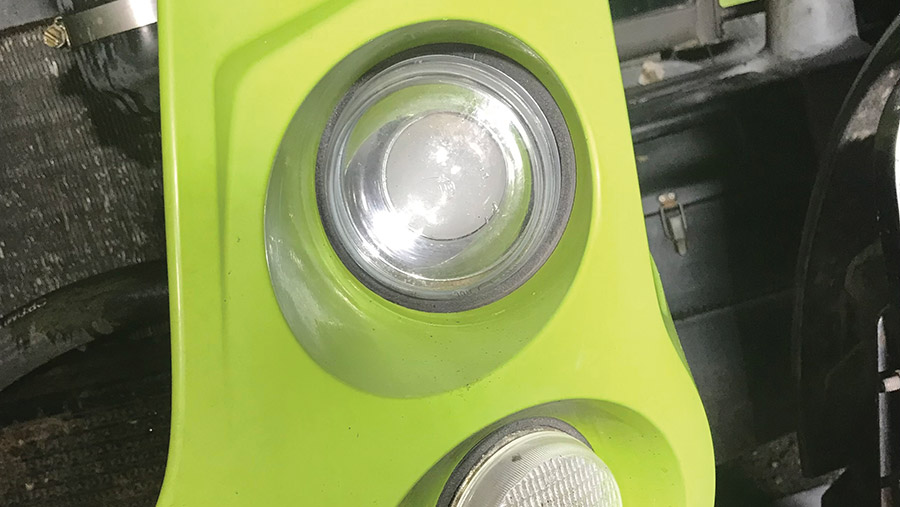
© James Andrews
On several Claas models, the reflective material in the headlights fails and genuine Hella halogen replacements cost a small fortune.
Cheaper, and brighter, LED alternatives can be found from companies such as LED Global, which come in at about £70 each.
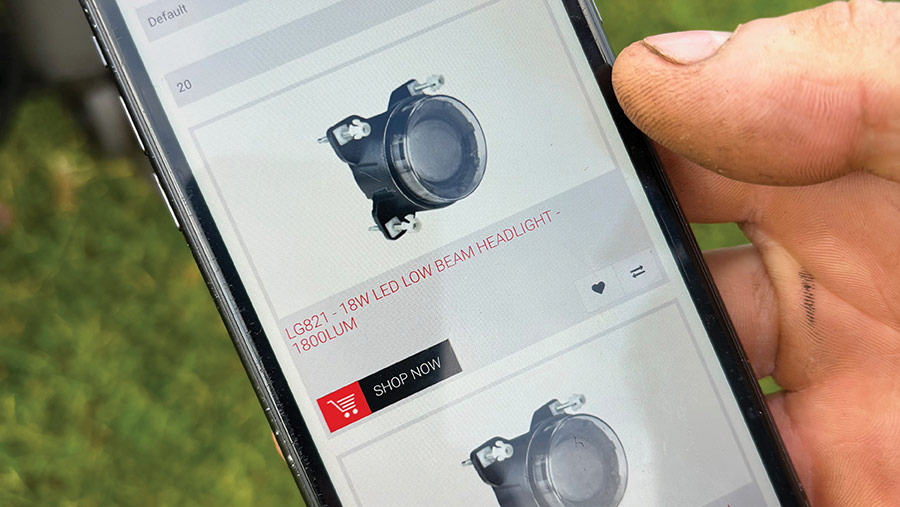
© James Andrews
Axos high-low splitter unit
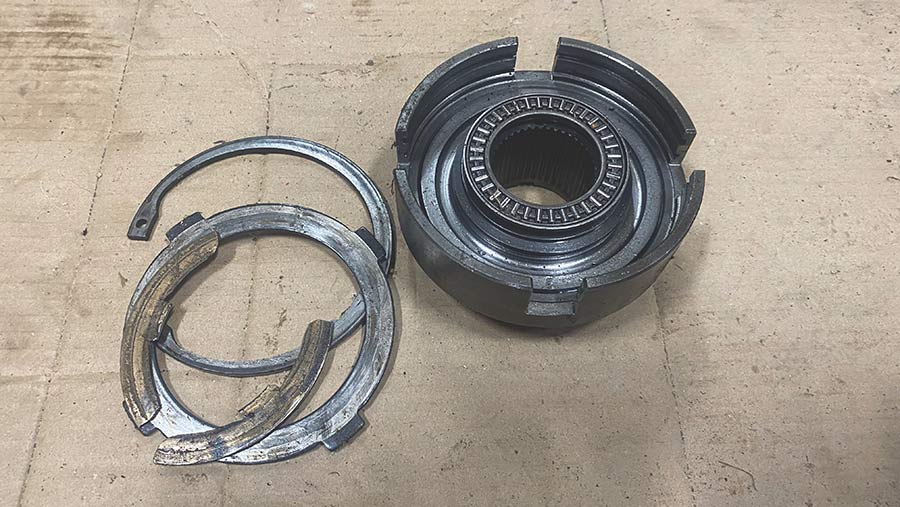
© James Andrews
If Claas’ small Axos tractors are run low on transmission oil, the clutch packs in the high-low splitter can start to break up.
This jams the transmission in high and low range simultaneously, effectively locking the engine solid so that it won’t start.
Owners won’t do it twice as it’s a pricey two-to-three-day job to split the tractor and rebuild the gearbox.
Axos 4×4 drop box
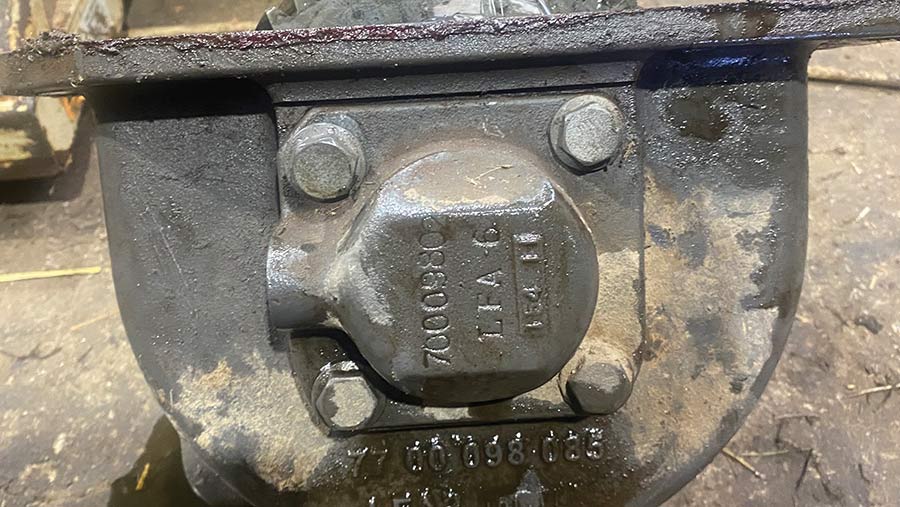
© James Andrews
Another Axos transmission foible is the four-wheel-drive drop box occasionally taking to chewing up the metal drive shaft sealing rings.
The result is that the tractor will get stuck partly in four-wheel drive, which will cause some tyre scrabbling on hard surfaces. It’s a one-day job to replace them.
Axos oil-starved rocker cover
Hydraulic pumps on Axos tractors are driven off the timing gears and, when they first came out, these would put excess pressure on the camshaft bushes, causing them to spin and block the oil galleries feeding the rocker.
Excessive wear would eventually write off the head. Claas fixed the problem a few years ago and almost all older models will have been sorted under warranty.