Tips and advice for planning and building a new silage clamp
Tucked away in a corner of the yard and inherited from a previous generation, silage clamps are often at the bottom of the priority list. But given how important forage stocks are in the grand scheme of things, should we pay them more attention?
Recent research has revealed at least one-fifth of UK silage clamps are more than 30 years old. While that figure might not be staggering, many of them are in need of some fairly major repair work or replacement.
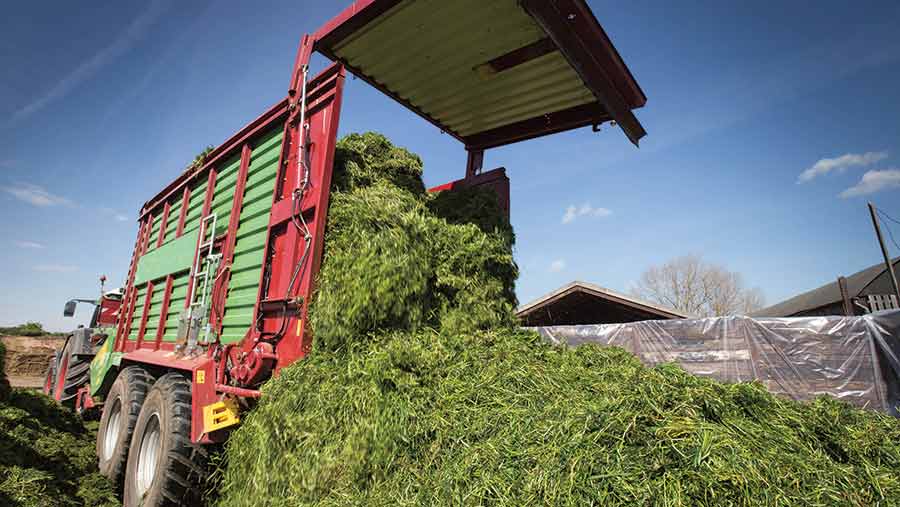
© Tim Scrivener
The study also identified that more than 60% of all silage pits were more than 10 years old and many of them don’t comply with the latest rules and regulations.
That’s increasingly important with the Environment Agency keeping a closer eye on the pollution risks on farms. And it is equally important having forage storage facilities that minimise waste and make the most of the crops you have spent all year growing.
See also: Guide to assessing your silage clamp for costly losses
What are the options?
Clamp design has moved on in the past few years, partly due to the introduction of bigger-capacity storage facilities for anaerobic digestion plants from Europe.
In the UK, most pits employ pre-cast concrete panels or cast-in-situ vertical walls, but there is an increasing move towards sloping-walled clamps.
“Standard panels are still a great option for farms with limited space. They are relatively simple to build and are widely available,” says Mr Wilson.
“However, pay close attention to ensure they meet the current British Standards regulations and are rated to accommodate enough silage, even in a bumper year, plus the weight of the machinery that will work on the clamps.”
While earth-banked pits with angled walls might be commonplace on many farms, they tend to present certain challenges with regards to contamination and sheet damage.
Due to the requirements for an impermeable base and leak-proof drains, current regulations don’t allow for the construction of this type of wall any longer. It means that panels and a concrete or tarmac floor are now the only realistic options for new clamps.
Sloping v vertical walls
Sloping walls
- Improved consolidation – allows compaction right up to panel, reducing potential shoulder wastage
- Machinery operation – buck-rakes can run right to the edge of the clamp without the risk of walls giving way
- Safety – earth banks between walls provide a safe platform for staff sheeting down as well as storage for sheets and gravel bags
Vertical walls
- Space – upright panels take up less room
- Availability – plenty of companies supplying and erecting vertical walls
What are the rules?
Defra’s silage, slurry and agricultural fuel oil (SSAFO) regulations govern how silage clamps should be designed and built. They outline where storage can be sited, how it should be built and how much effluent capacity you will need.
“When you look at your wall options you should consult an engineer to gauge whether the walls will satisfy the relevant British Standards and that they will be strong enough to handle the weight of your compacting machinery,” warns Mr Wilson.
“It is also very important that you understand the ground conditions you are working with, as you may have to put in significant foundations if you are working on unstable land.”
There are minor differences between English and Welsh rules.The Environment Agency (EA) specifies it must be notified 14 days in advance of any building work taking place, while Natural Resources Wales wants notification 14 days before the clamp is put to use.
Construction Industry Research and Information Association (CIRIA) C759 guidelines outline the best ways of coming up with an appropriate design for the requirements of the particular farm. They are free to use, but you have to register to get access to the website.
What about extending/improving an existing clamp?
Clamps built before 1991 are exempt from current legislation providing they are not presenting an unacceptable pollution risk.
Pits that are substantially enlarged or modified lose their exemption from the SSAFO regulations. There’s no hard-and-fast definition of substantial enlargement, but as a rule of thumb, a 10% increase shouldn’t be a problem. If it is 25% or more, exemption is lost, so you need to notify the EA and it will tell you which parts need to be brought up to the standards of the regulations.
What forms must I fill in?
There’s a simple three-page form called a WQE3 that you can get from the EA or download from its website.
There’s not much to fill in other than the farm address and the grid reference of the clamp. However, there is a box which an engineer must sign to confirm the effluent tank is fit for purpose.
What are the key things to keep in mind for new clamps/alterations?
- It must have an impermeable floor slab
- It must have a perimeter effluent drain channel outside any walls
- It must have a suitably sized effluent containment tank
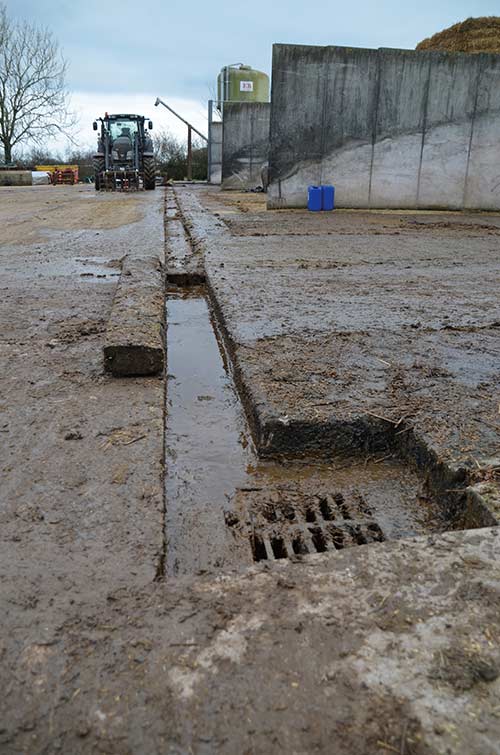
An unobstructed channel across the clamp face can reliably capture any run-off © Nick Fone
What about drainage?
One of the key regulations is that all clamps must have a drain at base level around the outside of the panels. It is there to intercept any liquid that leaves the clamp through the walls.
Floating sleeper drains are a good, simple option across the open ends provided they can handle large amounts of water in a short period of time.
The best drains are straightforward – all the effluent flowing to one channel following the contours of the base and not running along the bottom of the panels.
Not all liquid need necessarily be considered effluent, but keeping clean water out of the effluent tank is key because the legal minimum tank size is rarely enough to cope with heavy rainfall.
“If it’s possible to separate sheet and clean concrete rainwater run-off from effluent, that needn’t necessarily be considered as dirty water,” explains Adas’ Charles Bentley.
“If not contaminated with effluent or silage, it can be considered ‘other fouled water’ and can be channeled directly into a constructed wetland [reed-bed] system.”
What size effluent tank do I need?
The rules say you should have at least two days’ storage at peak flow. However, it’s up to you to ensure you have enough capacity to avoid the risk of pollution.
Clamp capacity |
Minimum effluent tank capacity |
Up to 1,500cu m |
20 litres for each cubic metre |
More than 1,500cu m |
30cu m minimum plus 6.7 litres for each cubic metre of clamp capacity over 1,500cu m |
What else should you consider?
Having a clamp with no back wall cuts out the corners where compaction can be harder to achieve.
The most important factor is face width relative to feed-out rate. The length and the breadth of the clamp should be based on the speed at which it will be emptied, because the longer the silage face is exposed to oxygen, the greater the wastage.
Be aware that new clamps should have a loading plate issued by the design engineer that states the maximum weight of any buck-raking or rolling machine on top of the static load of the stored material.
“Traditionally the weight of the tractor has been assumed to be about 6t, which is clearly significantly out of date,” says Mr Bentley.
“To keep it future-proofed, owners should ensure the structure is rated for clamping kit in excess of 15t.”
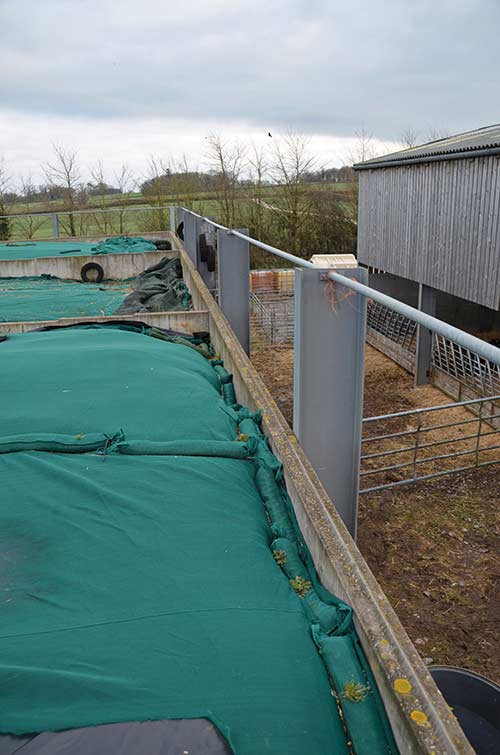
A handrail can help avoid falls from height © Nick Fone
Silage pit tips
- Design clamps to fit the feedstock and the feed-out rate
- Consult the EA early to get feedback and understand the regulations
- Make the clamp apron 50mm thicker than the rest of the base – the combination of trailers turning to tip, corrosive effluent and feeder wagons parked while mixing can do a lot of long-term damage
- Safety is paramount, do everything you can to avoid falls from height – handrails are a must
- Consider how you will be emptying the clamp – most handlers won’t reach more than 5m high, so do not overfill
- Consider the size of machinery that will be working on the clamps when you fill them – are the walls going to be strong enough?
- If silage goes into the clamp wet, consider running lengths of permeable drain pipe along the base of each wall to channel effluent in the right direction and to alleviate the hydraulic loading on the integrated drains
- Talk to specialists who can guide you through the process
What do I need to think about when positioning a new clamp?
Any new pit must be positioned at least 10m away from the nearest watercourse and a minimum of 50m from any spring, well or borehole.
Think about access for increasingly big silage-making kit and the potential for further development around the clamp.
Aim to position it alongside or above buildings so that surface water can be channeled into existing drains (providing they have the capacity to handle it).
Always avoid building load-bearing structures such as silage clamps and slurry stores on built-up ground. Dig in rather than bank up.
Who can I talk to for advice/guidance?
The first port of call should be your local EA office when planning any clamp alterations or a complete new build. They are generally quite helpful as they are keen to see improvements being made.
Adas and other consultants will aid in the planning process and AHDB’s dairy department can provide useful planning guidance free of charge.
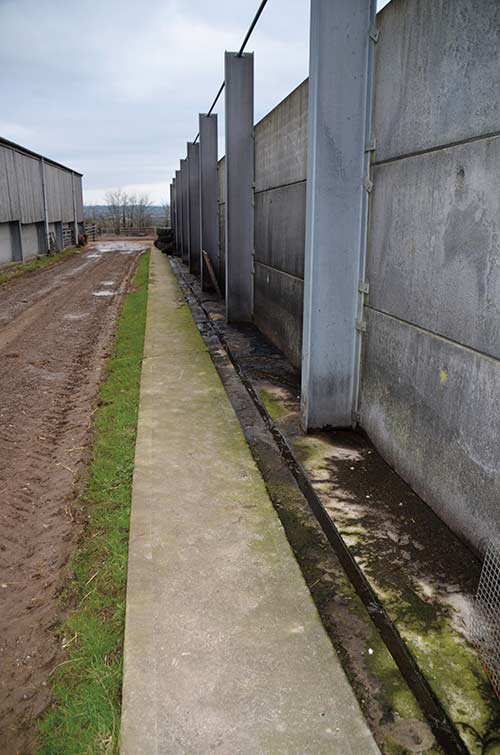
Effluent channels must run around the outside of clamps to capture leachate © Nick Fone
Of course, clamp suppliers, engineers and builders will be able to help with a lot of the construction regulations, but ensure they are CE accredited.
If you are planning a DIY job, be aware of all the rules for health and safety and construction design and management.
What are the likely changes in silage clamp legislation?
The SSAFO rules are expected to change in 2017, with more of a focus on avoiding pollution. One particular area that’s been identified for change is the 20-year design life assumed in the current guidelines. Industry experts are also hoping for more common-sense rules for drainage.
“I would like to see us follow the Irish rules by dropping the requirement for external perimeter drains where there is an impermeable joint between the wall and floor,” says Mr Bentley.
“So often where walls are cast in-situ, the external channel is just decorative because nothing can escape. An internal drain ensures everything is captured and channeled in the right direction.”
What base layer is best?
Asphalt is an increasingly common material, though being a fairly specialist product, Mr Wilson suggests it’s worth doing some careful research and to use a reputable company.
“Asphalt works well, but it might not be the best choice for everyone. The worst thing you can do with it is leave heavy machinery parked on it for long periods of time, as it will slowly dip and puncture.
“Also consider what you are going to be storing, as the potent leachate from sugar beet can cause big issues with tarmac.”
The whole clamp should fall at least 3% front to back to drain rainwater and silage leachate away from the open face. Bock also recommends putting a fall into the middle of the clamps away from the bottom of the panels so leachate doesn’t attack the joint between the base and the walls.